[caption id="attachment_1003731118" align="alignnone" width="550"]
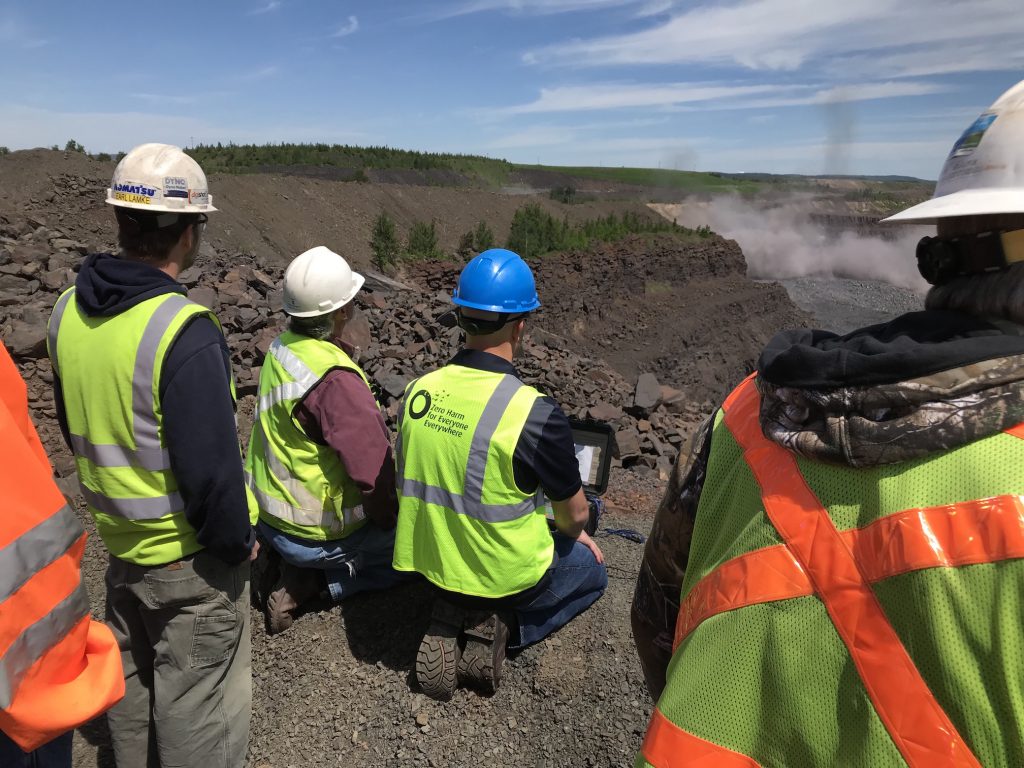
Dyno Nobel is a global leader in commercial explosives. Credit: Dyno Nobel[/caption]
SALT LAKE CITY – Commercial explosives leader Dyno Nobel has introduced a new software system that it says can reduce costs and increase efficiency.
The ΔE2 software system allows targeted placement of energy in the blast hole by incorporating data from outside sources, such as drills, face profiles or other data that characterizes rock properties. The ΔE2 system can also send loading instructions directly to the pump truck control system ensuring boreholes are loaded as designed, giving control back to the engineer or blaster.
Dyno Nobel says the system can improve shovel dig rates and crusher throughput, and lower overall drill and blast costs. And it can improve operator efficiency by simplifying the loading process and allowing explosives’ energy to be accurately placed in the blast hole, thus reducing oversize and/or fines.
The ΔE2 software system, which the company is calling “the next evolution of Differential Energy,” is designed to be easy to use and works with Dyno Nobel's proprietary in-truck control panel, DynoLogix.
The ΔE2 Pre-Load desktop software, part of the new ΔE2 system, allows users to precisely place energy within the shot and can be used by blasters and engineers to optimize energy placement within each borehole in the shot. The system can import data from multiple sources, including data from the Dyno Nobel mobile suite of applications that can create shot designs, to allow users an easy way to control the loading of a blast. Users can view powder factors that can be changed on the fly, which gives the engineer and blaster the ability to understand explosives usage prior to loading the shot, enabling them to control the actual shot cost.
For more information, see www.dynonobel.com.
Comments