XPS innovations get to the root of plant problems
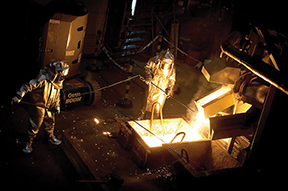
Tapping and sampling of XPS’s 350-kW pilot scale electric arc furnace. CREDIT: XPS
XPS Expert Process Solutions has a long history of solving complex metallurgical problems, designing and automating processes and supporting physical asset integrity programs and activities since its origins as the Falconbridge Technology Centre in 1952.
Since then, it’s gone through several transformations, starting with its move in 1984, from Thornhill, Ont., to Falconbridge, Ont., just outside of Sudbury. The acquisition of Falconbridge by Xstrata in 2007 and then Glencore in 2013 have brought further changes.
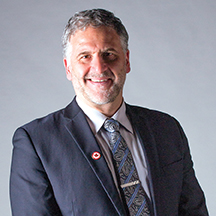
Dominic Fragomeni
The biggest was probably its transition in 2007 under Xstrata when the corporately funded and exclusively in-house technology centre was asked to convert to an autonomous business with a mandate of being self-supporting.
“When we first started out we knew we had the technical horsepower and we were quite efficient, but it became very clear that we needed to improve our competitiveness by reducing our costs while maintaining our high quality work,” says XPS vice-president Dominic Fragomeni.
“We even have to compete on a quality and cost basis for internal (Xstrata and then Glencore) work so that made it even more important that we focus on this.”
Fragomeni says the team has done a good job of continuing to improve efficiency and costs, particularly over the last six or seven years during the last downturn.
“Of course, we’ve been able to pass these savings along to our clients and have become very competitive when you consider the very high end technical expertise we offer,” he says. “Metallurgical test work is often commoditized. We don’t believe in this.
Accurate, high-quality and complex process development and testing takes the right equipment and right people with high end skills. We have the right formula and our clients like it.”
XPS has increased efficiency by harnessing the entrepreneurial spirit of its people, Fragomeni said in a November interview in the XPS Technology Centre. The company looked at changes to work styles and training, equipment and equipment set up, automation and other solutions.
“I think the whole change management from a corporate technology centre to a business has been pretty successful.”
However, Fragomeni adds that XPS continues to evolve – as any stand-alone business would need to in order to grow and adjust to market conditions.
Fragomeni, a professional engineer and CIM Fellow who has been XPS vice-president since 2012, leads a team of 45 engineers and technicians at XPS. Last year, he was chosen as a 2018 CIM Distinguished Lecturer in recognition of his contributions to the Canadian minerals industry through his work in mineral processing. Before he became VP at XPS, he spent about nine years in technology and projects and 15 years in operations with Falconbridge and Noranda.
XPS’s business is currently around 50% external clients and 50% internal – a ratio Fragomeni is not necessarily looking to change.
“Glencore acquired Xstrata in 2013 and they’re a big organization… as we got to know each other better, we both saw more and more demands and need for our expertise. The work within Glencore is very rewarding.”
Fragomeni says the organization is looking to grow the business rather than changing the ratio of internal and external clients. “We want to add more value to our internal Glencore clients and still to do external work, these are both really important to us.”
External work broadens the expertise of XPS – for example the company is currently doing work on lithium – a metal that Glencore doesn’t produce. At present, about 35% of XPS’s business is within the Glencore nickel business.
“Our wheelhouse is nickel, nickel-cobalt, copper, zinc, lead, platinum group metals, gold, lithium and a whole suite of other commodities, even antimony.”
While they are a part of a large, multinational company, Glencore has allowed and in fact encouraged XPS to operate pretty autonomously, Fragomeni says.
“The key thing with Glencore is they’re very value driven and I really like that. They’re also entrepreneurial, so we are well aligned.”
He adds: “With our twelve-year track record in this business model, I think Glencore has confidence that we can run a business.
They definitely see the value of the technical expertise that we have, they are a very good company to work for.”
One such example of the high-end technical expertise is XPS’s use of QEMSCAN technology (Quantitative Evaluation of Minerals by Scanning Electron Microscopy). While other labs have the same or similar technology, Fragomeni says XPS uses it in a different way. The company uses QEMSCAN, an automated technique used for measurement and characterization of minerals at a microscopic level, including mineral type, mineral grain size distribution and liberation characteristics. It is used in combination with Electron Microprobe and now Laser Ablation to solve complex metallurgical problems.
“QEMSCAN and Microprobe and the mineralogical data they produce is hugely valuable when you’re designing a process or when you’re trying to optimize it,” Fragomeni explains.
“We’ve made use of this technology to shorten the time required to do the testing because you understand a lot more about the minerals and the ore variability. Generally, the combination of these disciplines, mineral processing and mineralogy is called process mineralogy. This makes the testing and process design less expensive, the process more relevant across the whole life of the mine because of better samples, and produces a more accurate scale-up which generates huge value when the operation is up and running.”
The importance of all of this is magnified when you consider that the capital cost to build new mining operations is in the billions, he adds.
“We also use the data generated from the QEMSCAN to model performance, so we can calculate what the recovery should be,” Fragomeni notes. “What should the yield be from that specific ore mineralogy? This helps focus the greenfield process design or the operating plant optimization to realize the full economic performance or ‘entitlement.’ We can quantify it. So if we’re not getting it, we know what we need to do to improve our process.”
Remote control loop monitoring
XPS’s Process Control and Automation division has introduced several cutting-edge technologies and services in recent years, including remote control loop monitoring. Control loops are designed to automatically stabilize various plant processes, such as the flow of water, the flow of a chemical or the power to a piece of equipment, and most modern plants can contain hundreds of them.
“It’s like the cruise control in your car, you set the speed and the loop adjusts the throttle to maintain the speed. Most of our processes are more complex though.”
Starting in 2018, XPS set up a centralized control loop performance monitoring system at five Glencore sites. The system was set up to remotely monitor the control performance of 50-150 loops in real time, in each plant in Ontario, New Brunswick and New Caledonia, all from the XPS Technology Centre in Sudbury.
“This type of approach has been around for a while, but the challenge has always been the communication technology hadn’t quite evolved yet. Now it’s pretty robust so you can get clean data transmitted around the world,” Fragomeni says. “It was also the fact the systems required on-site maintenance and support that is not always available due to other priorities at the operations.”
After a rigorous review process and then testing, Control Station’s PlantESP software was selected to collect and analyze the data in order to deliver the service to clients.
With the system, XPS has been able to identify performance issues that would have been otherwise difficult to detect, including poor performance in some valves, under and over-sized actuators, poor PID tuning, and in one case, an oscillation created by a loss of control in the previous stage of the plant process.
XPS is now offering the service to all clients, and applying the tool to hundreds of loops in mines, mills and smelters to focus maintenance of these under-performing loops.
“If one of five hundred loops in a processing plant is not operating properly, this will pick that up, the diagnostics will tell you there is a problem and what it is. It will very quickly focus on a solution,” Fragomeni explains. “We maintain the system and provide a KPI report to the plant. This helps the very busy plant people to focus on their regular activities. We also maintain the system and ensure its sustainability as plant personnel change.”
Currently, XPS relies on its own team’s expertise in close collaboration with the site to identify why a loop is not operating according to spec and perhaps re-tune it.
“The next thing is having the artificial intelligence (AI) engine basically looking at this doing the diagnostics and ultimately providing recommendations to improve performance,” Fragomeni says.
XPS is looking to AI to do more than just this and has selected an AI tool to improve performance in the Sudbury operations.
It has selected the software for the task and Fragomeni says its first trials have already delivered some exciting results.
“AI is very well equipped to handle all the data coming from our processes. It’s bound to identify opportunities for improvement.”
XPS is also leading a Canadian Mining Innovation Council (CMIC) project that will evaluate what tools operations use to collect data and what other value and models AI can extract from these databases.
“It’s early days, but we have several other major companies interested with support from CMIC, XPS, Corem, McGill University and Compute Ontario.”
XPS PyroCam
Another new product, the XPS PyroCam, was designed by XPS’s Extractive Metallurgy group for a client who wanted to see what was happening inside their very high-temperature nickel smelting furnace.
Temperatures in these furnaces can run up to 1,500° Celsius in order to produce high-grade molten metal and a barren, molten discard slag. Until now, these high operating temperatures made it impossible to see inside, which could be helpful if something isn’t working correctly, Fragomeni says. After all, at those temperatures, electronics tend to malfunction – and then just melt.
XPS solved the melting problem by using an existing, off-the-shelf video camera and still camera technology – coupled with a proprietary cooling chamber that allows the camera to operate inside the furnace.
The company designed a portable cooling chamber that does not use water, eliminating the risk of water entering the hot furnace. The PyroCam allows clients to see anything from the dynamics of the electrodes to where the feed is coming into the furnace. This could be very important in some furnace designs.
“The high-definition video, captured and controlled by a smaller-scale test work done in the lab and pilot plant,” Fragomeni says. “Now if something is off, you will have some other information to help diagnose the problem.”
XPS has so far sold several PyroCams, most recently in South Africa and have had many other inquiries.
Lithium expertise
In the battery minerals market, XPS has a couple of projects that have helped it develop expertise in the nascent lithium space, in particular in the spodumene hard rock deposits found in Canada. The company is developing a milling process flow sheet for Frontier Lithium, which is advancing the PAK deposit in northwestern Ontario.
The company is also working on a joint project with Frontier and Ahmad Ghahreman, a professor at Queen’s University, to develop a process to refine spodumene concentrate into lithium hydroxide, which is the form of lithium compounds preferred by premium battery producers. More work needs to be done, but the process shows promise for being able to produce lithium hydroxide at a higher purity and for a lower cost compared to the industry average.
Ore particle and bulk sorting
Fragomeni is also excited by new technologies being developed to improve the mining process and selectivity well before the ore hits the concentrator, including ore sorting or pre-concentration.
The sensor-based technology has applications for some ores and the challenges of capacity and accuracy of measurement are being quickly addressed by some of the vendors. The particle sorting technology is used very effectively at Stornoway Diamond’s Renard mine in Quebec and is being tested and evaluated on base metal sulphides and gold, Fragomeni says.
“The accuracy of the measurement and equipment capacity are always improving,” he notes. “Diamond mines don’t typically run high tonnage rates but when you get into some of the lower grade sulphide ores, you have to run very high tonnage rates so the pre-concentration machines need to have higher capacity.”
He adds: “The bulk sorting machines are definitely meeting this challenge and some full-scale testing is ongoing in South America.”
Fragomeni says this technology will have enormous benefits in the mine and comminution part of the process as it cuts down on the amount of material that operations need to hoist, haul, crush and grind. As a result of the ore sorting, the ore grade will increase as more of the waste is rejected and possibly left underground in the mine.
“It reduces the comminution energy required, it usually results in better recoveries and then there’s less tailings to deposit, too.
If thirty to forty per cent of the material is sorted and left in the mine before it goes to the mill, there’s that much less tailings that need to be stored and managed and lower long-term liability, so it has all sorts of positive ripple effects. It’s early days, but it will be possible in the future.”
Comments