Who can answer my heavy-haul questions? A collection of answers to common queries
To an outsider, hauling might seem straightforward, and some might even say easy. However, operators, fleet managers, dealers, and manufacturers know better.
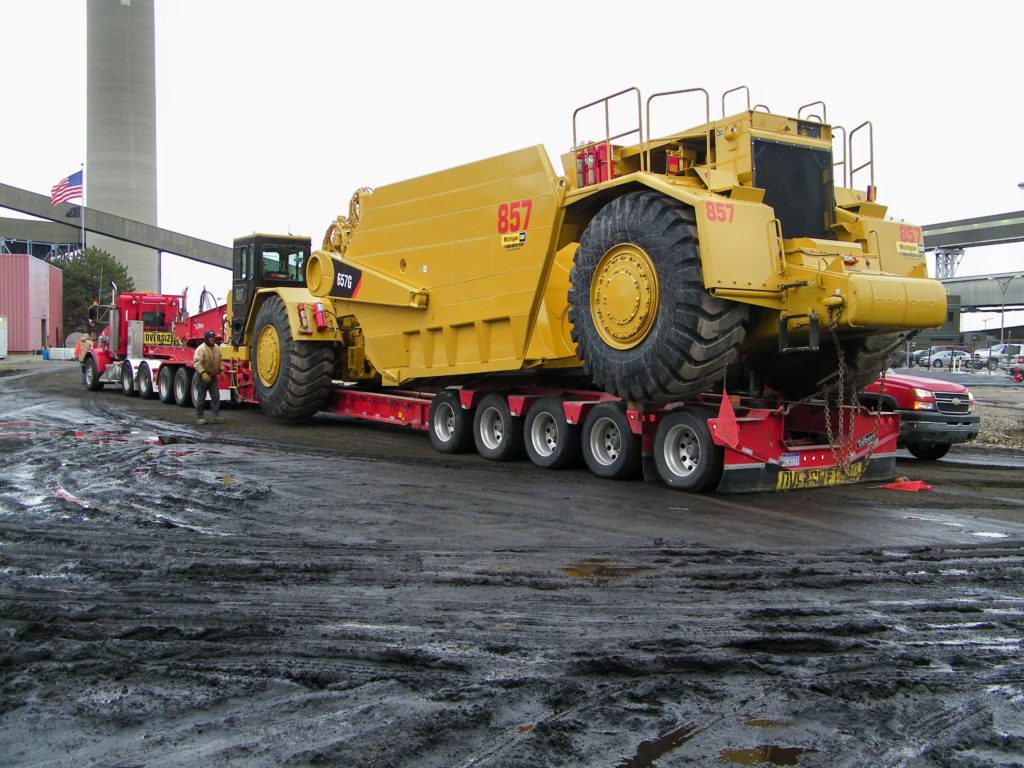
Hauling is a complicated process. Operators must consider the specifications of the intended load, road conditions in their operating area, and a variety of other factors up to and including which trailer will provide optimum safety and productivity. To maximize efficiency and minimize costs, operators rely on manufacturers and dealers to help identify the right trailer to fit their unique hauling needs: one with the capacity and features to transport the intended load legally and safely.
Working with these companies gives end users access to a wealth of knowledge, experience, and industry expertise. Though, as an operator, it might not be easy to know where to start. For the experts, the answer is easy: always start with the load.
To help get the wheels turning, here are some thoughts from industry leaders on a few of heavy-haul’s frequent questions.
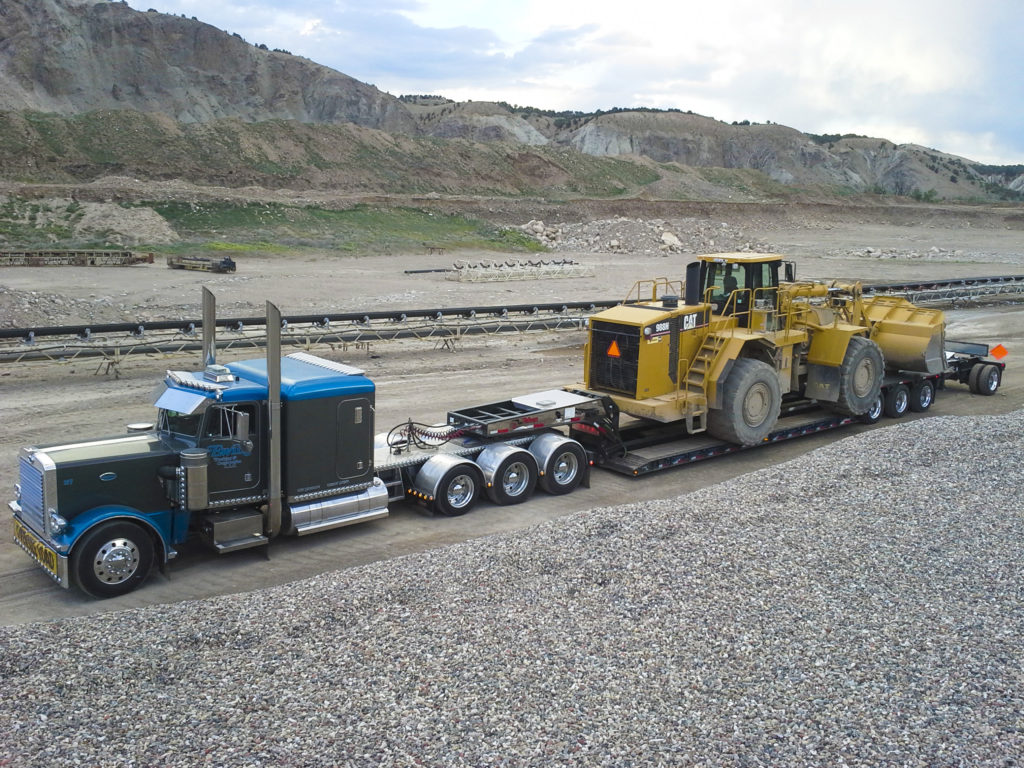
There are five key components calculated in a trailer’s capacity rating: size and weight of construction materials, the overall weight the trailer can carry, the area of deck that weight can safely be carried in, optimal travel speed, and the safety factor.
How does capacity factor in?
In a perfect world, a 55-tonne trailer could haul any 55-tonne load. However, any veteran operator will tell you that is just not the case. There is a lengthy list of factors that determine the capacity of a specific trailer.
To select the safest and most effective trailer for the project, dealers and manufacturers will ask a lot of questions, and some might even have a detailed checklist that covers specific equipment measurements and optional features, all the way down to the desired spacing and quantity of D-rings. Knowing the answers to some of the broader questions ahead of time speeds up the sizing process and will result in a trailer that safely meets the requirements of every intended job.
When operators approach a dealer or manufacturer about a trailer, they usually have a specific haul in mind. However, unless it is meant to be a dedicated trailer, it is important to consider all loads the trailer might haul. A 55-tonne trailer can be used for a 35-tonne haul, but the light load might mean it has a higher deck height than when it is fully loaded. Having the weight and dimensions of the largest intended load is vital, but it is also important to consider the specifications of any mixed loads, backhauls, or other pieces of equipment that the trailer might haul.
Dealers and manufacturers will also want to know if there are any unique requirements, such as equipment that requires special reinforcements or has a low clearance that might interfere with loading.
Working with a top-tier manufacturer often provides the best capacity rating, but operators should be aware of how each manufacturer determines their capacity rating because there is no industry-set or government-mandated system in place.
Load concentration is a key area of difference between industry leaders and other manufacturers. It is not enough to know a 55-tonne lowbed can carry 55 tonnes. Informed operators also know just how much of the deck can handle that weight based on the manufacturer’s capacity rating. While some trailers will need the entire deck length to haul 55 tonnes safely, a trailer from another manufacturer might only need half the deck length for the same weight. Having a trailer rated in half deck capacity gives operators a more realistic indication of what the trailer will be able to handle safely and without structural failure. These manufacturers usually design with a two-point rigid load base that accounts for the tire spacing, or hot spots, of large equipment and heavy machinery. This makes trailers with a half-deck rating more versatile and efficient for these loads.
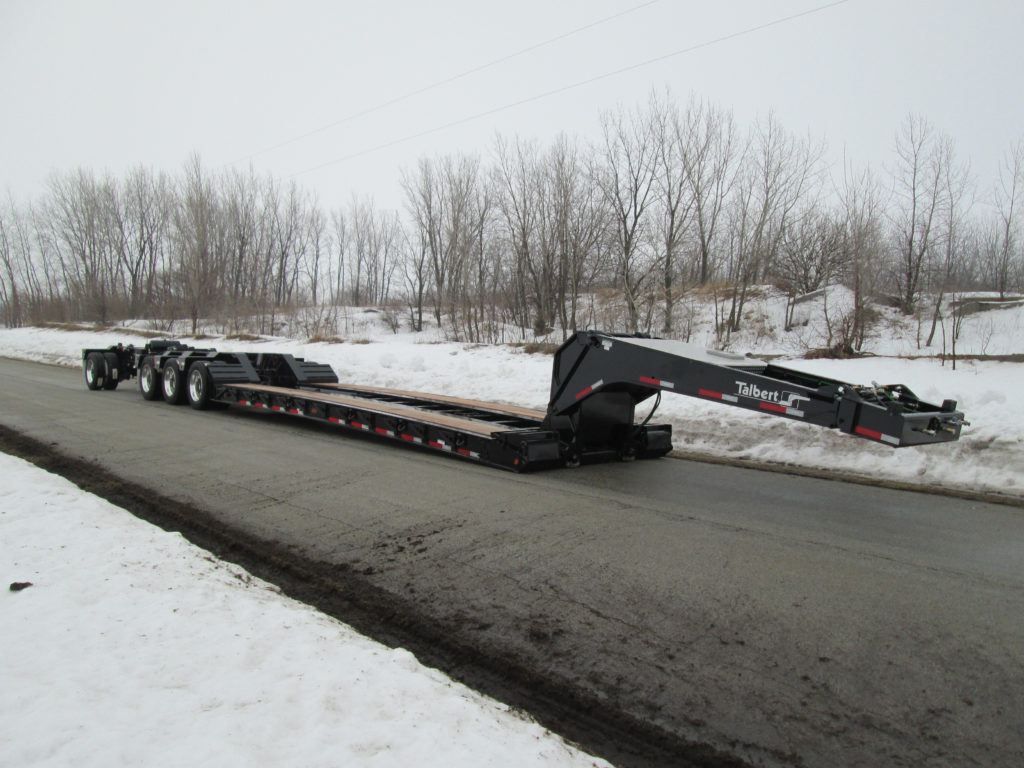
Load concentration is the most evident differentiation, but speed and overall safety ratings also put industry-leading manufacturers in a class above. Trailers from these manufacturers might be rated at 105 km/h rather than 90. They might also offer a 2.5:1 safety factor, well above the minimum 1.8:1 ratio that leaves no cushion for adverse road conditions.
There is no one-size-fits-all when it comes to trailers. For safety and dependability, partnering with a trusted dealer and top-tier manufacturer ensures operators are outfitted with a trailer that meets their individual requirements. In some cases, that might mean a custom design. Not all manufacturers provide this service, but some industry-leading companies will design and build a customized trailer that maximizes safety, durability, and resale value.
What specialty features are important?
When looking at the price tags, it is common for operators to ask what added value makes a top-tier manufacturer’s trailer worth the cost over other models. Depending on the intended use, certain specialty features, like a hydraulic beaver tail or in-deck winch, may be unnecessary. Others are vital for safety, durability, and productivity.
When evaluating the added value of specialty features, start with the basic materials. Industry-leading manufacturers use high-quality materials like steel with 689,500 kPa minimum yield, which allows the most capacity with the smallest impact on trailer weight. They also use apitong decking to provide the toughest, longest-lasting decks. Tightly woven and incredibly dense, this South Asian wood is less susceptible to chipping and cracking and provides more traction than metal. These features come with a higher price tag, but quickly pay for themselves in increased efficiency and durability.
Other design features might be less obvious in the dealer lot but make a clear difference with the first load. The most misunderstood of these is camber. Camber is the term used to describe the arc that forms in the centre of a well-designed trailer. It helps prevent excessive deflection in the main beams. When properly loaded to capacity, the arc will flatten, resulting in the trailer’s loaded deck height. A top-tier manufacturer can adjust camber in custom designs to meet the operator’s specific needs, but in general, a trailer that presents a slight upward arc in the centre has positive camber which will flatten with a full load.
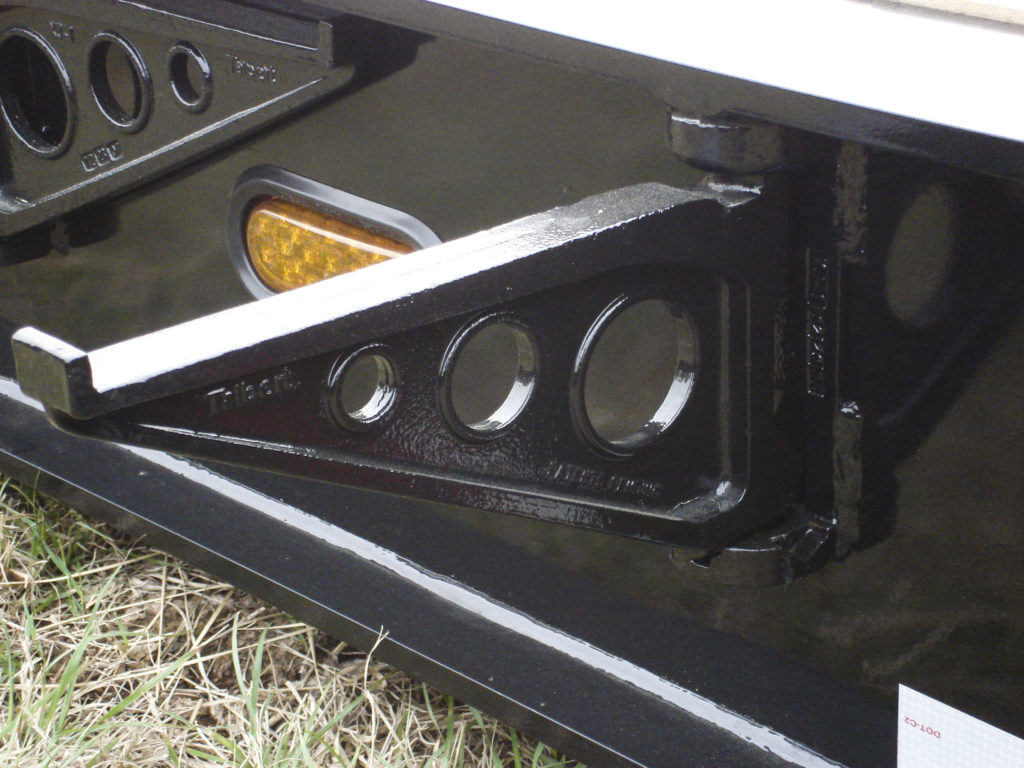
In addition to high-quality materials and special in-trailer design features, trusted manufacturers might also have a catalog of optional add-ons that allow operators to maximize their capacity and potential. For example, some offer deck extensions made from the same quality materials for a perfect fit. Nitrogen dampened axle extensions with a self-tracking pivot design that allows for consistent load transfer even over uneven terrain might be another desirable option.
When is a permit required?
Permits are another area of heavy haul that can cause frustration for operators. Dealers and manufacturers are constantly bombarded with questions like, “what permits do I need to haul X through states Y and Z?”
Unfortunately, there is no easy answer. In the U.S., a legal load is no more than 2.6 metres wide; 4.12 metres tall; 14.6 metres long; and no more than 36,300 kg gross weight (including truck, trailer, and payload). If a load exceeds in one of these areas, it may require a permit.
But this does not consider axle weight or other regulations that may vary from state to state. As with capacity rating, there is no nationwide standard for permits. Anything above 36,300 kg comes under the state jurisdiction, and each state has its own set of rules based on infrastructure, legislation, and other regional factors.
Kingpin laws are another good example of regulations that change from state to state. Most states along the East Coast have laws that limit the length to 12.5 metres from the kingpin to the centre of the tandem axle or 13.1 metres to the centre of the rear axle on a trailer exceeding 14.6 metres. There is no specified length for states in the centre of the country. California has the strictest kingpin laws. It requires a permit for anything over 12.2 metres. So, if an operator were to travel from Texas to New York or Oregon to California, they would need to make sure they had permits for every state in which the trailer would be considered oversized.
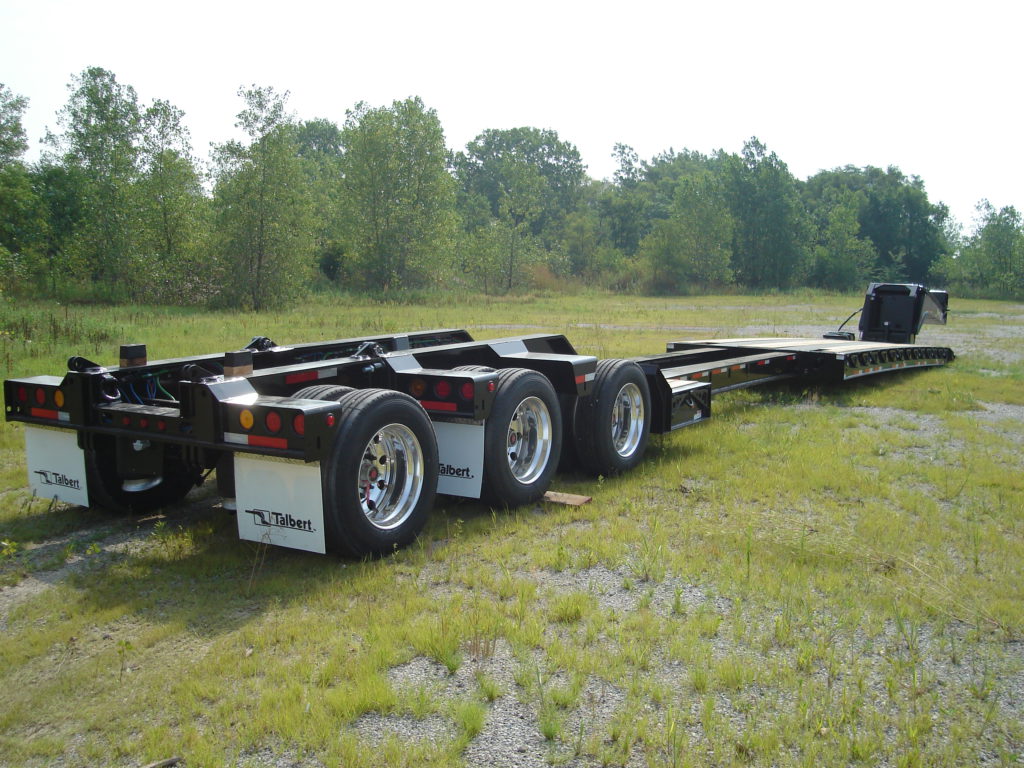
That is why the intended area of operation is as important as capacity when selecting a trailer. Dealers, manufacturers, and industry associations, such as the Specialized Carrier and Rigging Association (SCRA), have a wealth of information on this subject that they are willing to share with operators and managers, but operators are encouraged to submit a configuration to states they plan to operate in to ensure proper permitting.
Permits can be quite the quagmire, so in addition to offering their expertise, manufacturers are doing their best to work with end users to design trailers that limit the need for extra permits, all the while adapting to ever changing equipment. Telescopic trailers, trailers with dual kingpin settings that can be operated empty without a permit in states with a 13.1-metre kingpin law, as well as flip up and removable axle attachments are just a few examples of versatile designs from leading manufacturers.
Even these versatile options can still require permits. Operators are encouraged to work closely with the department of transport (DOT) in every state they operate in to ensure each load is properly permitted.
What is overloaded?
Safety is a core value of many of heavy-haul’s top-tier manufacturers. That is why they work with dealers, managers, and operators to find the right trailer. It is why they hold themselves to a higher standard with capacity ratings. And it is why they do their best to help operators determine what permits might be required for an oversize load. Top-tier manufacturers are concerned with the safety of operators, equipment, and the payload, but also those sharing the road. For that reason, they highly discourage overloads. A single overload might not cause the trailer to fail, but it reduces the manufacturer’s safety factors and puts unnecessary stress on the trailer components, putting it at risk of future failure.
It is also inadvisable to add aftermarket elements to a trailer to try to increase capacity. Trailers are designed for certain setups, reinforced where they need to be. Adding more axles, a spreader bar, a jeep, or any other element to a trailer that it was not designed for does increase the span but does not add capacity to that trailer. In some cases, it will reduce the load rating of the trailer. If not designed for the trailer, adding aftermarket pieces can create stress and lead to failure.
While simply adding axles and extenders cannot increase the capacity of a trailer, that type of versatility can sometimes be designed in. Certain top-tier manufacturers can design trailers that have a rating such as 55 tonnes in a spread axle setting then can increase to 60 tonnes with a close-coupled one.
To help operators navigate variable axle weight regulations without making risky after-market modifications, manufacturers have also developed trailers that are East Coast or West Coast specific. These trailers are designed to use variable axle and booster configurations that make it easier for end users to haul safely and legally in different regions.
Another safety concern dealers and manufacturers often hear about is the misuse of outriggers. Outriggers, also called swinging side brackets or extension brackets, can extend the useful width of a deck by up to 30.5 cm on each side. This makes the load oversized, and it will require a permit. It also requires proper loading to ensure safety. At least half of a machine’s tire, track, or grouser should be on the main body of the trailer. Any less and the outriggers are considered overloaded, putting the whole load in jeopardy.
Who can help answer my questions?
In the world of heavy haul, there are easy questions like, “is it safe to travel with the flip axle down?” Yes, but there is a good chance it will put the load over the length and require a permit. Or “what is the difference between spread axle and close coupled?” This is due to how an additional axle is attached. The additional axle is attached to the rear only on a close coupled model. Spread axle configurations allow for more versatility; with a nitro booster, operators can add as many additional axles as the trailer is designed for. The presence of pin tubes is another indication, as pin tubes are required and reinforced for split axle configurations only.
Then, there are those tough questions that require more thought like, “how much can a 55-tonne trailer haul?” To which a reputable dealer or manufacturer might reply, “let us start with what needs to be hauled and where it is going and build up from there.”
In an industry where so much is riding on what operators choose to run between the road and the load, taking the time to work through the easy and the tough questions with experienced dealers and manufacturers ensures everyone’s safety and the trailer’s dependability and longevity as drivers hit the highway.
Troy Geisler is the vice-president of sales and marketing at Talbert Manufacturing.
Comments