What to look for in a heavy equipment fire suppression system
When evaluating a vehicle fire suppression system, it is important to know what choices are available. The most fundamental decision to make is whether to opt for a stored pressure system, or a side-cartridge system.
A stored pressure system holds both the fire-fighting agent and nitrogen that propels it through the distribution network in the same tank. On the down side, this type of system has a much greater likelihood of leaking through its pressure gauge, a fact which is amplified in situations where there is significant vibration.
This can be a major risk as it can lead to poor performance, or even system failure. However, in less demanding situations they can be sufficient.
Alternatively, side-cartridge systems store the nitrogen that acts as a propellant in a separate, sealed tank. This makes the entire system much more resistant to leaking, which is key to their robust nature.
These types of systems dominate in mining, forestry and other rough and tumble industries. If ruggedness is a concern, this type of system is the better choice.
Rubber hose is used to varying extents to create a fire suppression system’s distribution network. However, the more hose that is used, the more potential there is for wear and tear to compromise the system due to drying and cracking or even being cut.
Stainless steel tubing can replace much of the work hose does.
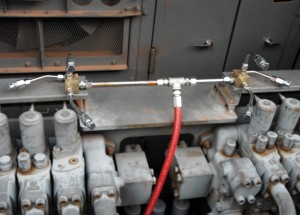
A fire suppression system with multiple heads for distribution of an agent throughout various areas of the machinery.
Not only does it last longer in a high-heat environment, it does not require extensive welding to install.
A “cleaner” looking finished product is not only more attractive, it serves the practical purpose of making it easier on technicians working in the engine compartment since it is less cluttered.
Beyond that, the stainless steel tubing doesn’t need to be replaced, at the end user’s expense, every few years like the hose does. Again, if ruggedness is a concern, tubing is superior to hose, especially when the cost of maintenance over time is taken into account.
Another design feature to look for is hinged nozzle caps. Not only do they keep debris from clogging the nozzle, they also negate the possibility of MSHA citations for missing blow off caps, a common inconvenience with a high price tag.
When considering the actual agent used in a fire suppression system, the main concern, beyond its ability to combat a fire, is the impact it has on the environment after discharge.
Due to its nature, liquid agent cannot be used below the freezing point without some chemical amendment. One chemical frequently used for this purpose is ethylene glycol (antifreeze). Though it gets the job done, it is deemed by OSHA to be a hazardous material.
Not all brands chose to utilize this harsh chemical as a result.
When shopping for a fire suppression system, if you plan to use a liquid agent as part of the solution, be sure to ask about this important factor.
Because it both cools hot surfaces and has a suppressing effect, utilizing a liquid agent for firefighting is sensible. However, when used instead of dry chemical, the tremendously fast suppressing ability of the A:B:C powder is lost. There is no reason for this compromise to be made.
As the standard of the vehicle fire suppression system market for nearly 50 years, dry chemical powder’s value has never wavered. Because it fills space in all three dimensions when discharged, it has the capacity to knock down flames wherever they may be in an engine compartment.
On the other hand, liquid agent requires direct application to the targeted area and it has to have an unobstructed “sight line” and be in close proximity, something which can be a challenge in a crowded engine compartment.
This physical constraint means that more nozzles are required to gain the same amount of coverage, which in turn means more agent is needed. The result is larger/more tanks. If space, weight or costs are a concern, an alternative to a liquid-only system should be considered.
Instead of focusing on the value of one of the two agent types, utilizing the two in concert is an effective approach to take.
When using a “dual agent” system, which has both a liquid and a dry chemical system deployed at the same time, the suppression of fire is fast and thorough and superheated engine surfaces are cooled significantly.
This latter fact is important because it dramatically reduces the likelihood of a reflash fire resulting from a surface which remains hotter than the flashpoint of a fuel that remains present.
Incorporating an engine shutdown function to limit the chances of fuel continuing to flow from compromised hose lines is always a wise choice regardless.
If the machinery being protected has large, hot-running diesel engines, especially if they are Tier 4 compliant, then a dual agent system warrants a close look.
*Information for this article provided by AFEX Fire Suppression Systems.
Comments