Kal Tire opens recycling facility for ultra-large mining tires in Chile
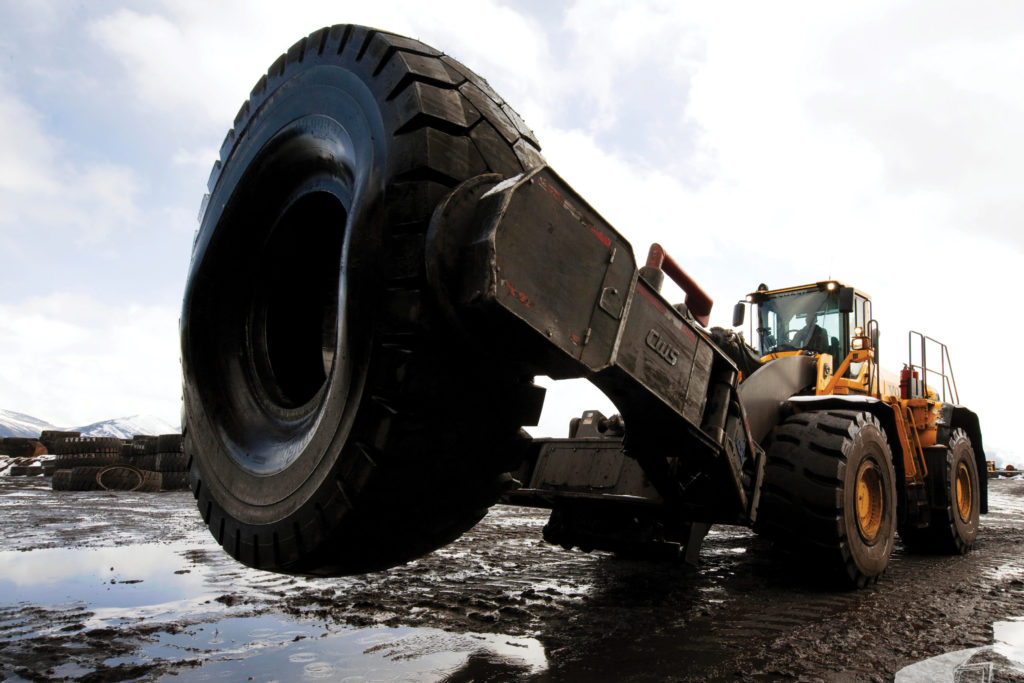
When it comes to waste in mining, liquid and solid tailings generally spring to mind first, but ultra-large tires – behemoths that can measure 4 metres in diameter, weigh 5,000 kg and cost up to $50,000 new apiece – are a close second. Indeed, at some major mines, the stockpiles of used and discarded tires are so big they are visible in satellite images created by Google Earth.
“We’ve heard miners talking about this problem for years and years,” says Dan Allan, senior vice-president of the mining tire division with Kal Tire, a family-owned business based in
Vernon, B.C. “The challenge has been that’s there’s never been a solution.”
Until now that is. Kal Tire has designed, built and commissioned its first thermal conversion plant, and the first for Chile, to deal with the problem of spent tires. It is located near Antofagasta, Chile, a major mining district in the north of the country, some 1,200 km from the capital of Santiago.
The plant will be capable of processing five ultra-large tires at a time in cylindrical reactors that rotate slowly. By applying intense heat, without oxygen, the reactors will convert them to 6,500 litres of light and heavy oil as well as synthetic gas, 4,000 kg of steel and 8,000 kg of carbon black.
Once the plant is operating around the clock, which is expected by year end, it will be capable of processing 20,000 kg per day, or 6,500 tonnes a year – enough to begin to put a small dent in some of the enormous stockpiles of used tires found at Chilean mines.
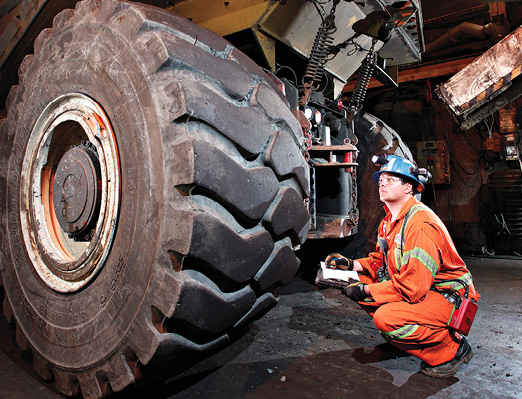
The scale of the problem can hardly be exaggerated. “I’ve seen mountains of tires in Chile,” says Scott Farnham, Kal Tire’s director of recycling services. “Some of the large mines have 80 to 100 of these trucks, there are six tires per truck and these mines have been operating for decades.”
Kal Tire began working on the project in 2015 when the Chilean government was in the early stages of developing a comprehensive recycling program to cover everything from oil and packaging to tires and plastic.
“Tires happened to be the first material that they legislated,” Farnham says. “It goes into effect next year. It’s really quite forward thinking.”
Thermal conversion is a well-established process, but it had never been applied to anything like the ultra-large tires used in mining. Farnham and his team had to research the engineering behind thermal conversion, determine what technology was available, what could be adapted and what they had to design and develop themselves. They worked with European manufacturers of reactors as well as companies that produce heating and condensing equipment.
“We started with a clean sheet of paper,” says Farnham. “Nothing like this existed.”
The equipment was developed following engineering discussions between Kal Tire and the equipment manufacturers. Kal Tire then made further improvements and developed a process control system.
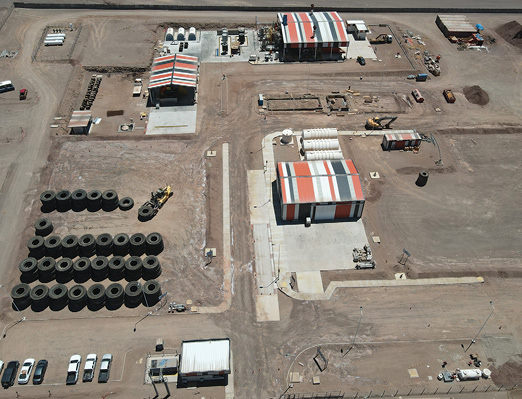
How it works
The plant contains two reactors, which Farnham likens to very large ovens. Each is 6.5 metres long and 3.5 metres high. Tires are first cut into eight pie-shaped pieces using a large band saw, then those are cut into smaller pieces before being placed in the reactors.
While the plant uses liquified petroleum gas (LPG) on initial startup, it then switches over to the syngas that is generated by the thermal conversion process, which the company says makes the process very energy efficient. The tires themselves provide the energy to continue the process.
Processing of five tires takes 24 hours and breaks them into their constituent components of steel, carbon and hydrocarbons. The intense heat converts the hydrocarbons to gases, which are captured and cooled, yielding light and heavy oil as well as a third substance – synthetic gases – which do not condense and are fed back into the reactors to serve as fuel. The carbon is converted to a powdery substance called carbon black while the steel is reduced to a wire mass measuring about 1 metre thick by 6 metres long.
The next challenge is to find markets for the light and heavy oil, the steel and the carbon black. “The steel is the easiest part because it comes out extremely clean and it’s a high quality, highly-engineered product,” says Farnham. “There’s a local steel recycler not far from the plant who’s looking for material like this.”
ANFO potential
The company has shipped samples of the oils to manufacturers of the explosives used for blasting in mining. Most manufacturers currently mix diesel with ammonium nitrate fertilizer to produce powerful explosives commonly known as ANFO (ammonium nitrate/fuel oil). “If oil from recycled tires can go back into blasting, it’s a great circular economy story,” says Farnham.
There are other potential uses for the oils. It can be mixed with the diesel used in generators, and some companies are experimenting with it. The oils could also be used to dilute heavy oil that is pumped through pipelines.
The carbon black requires secondary processing to clean and purify it to the standard required for use in plastics or the production of rubber. It will also have to be pelletized before it can be sold. “We can use established equipment to do that, but we have to develop the techniques to use that equipment on our material,” Farnham says. The company is in the process of doing that, but in the meantime, it’s shipping the carbon black to a rubber manufacturer who is incorporating it back into rubber products.
Both he and Allan are reluctant to disclose how much it cost to develop the plant, but say there were delays and cost overruns for a number of reasons. Permitting took longer than expected. Covid-19 made travel to and from Chile difficult and, at some points, wasn’t possible. And, as with any new process, there were unanticipated technical difficulties and setbacks.
Nevertheless, both see a bright future for the Chilean plant. One local mining company has already sent them 700 tires in order to clear space on its already congested property. But the real potential lies in building plants elsewhere in the world, including Canada.
As a supplier of ultra-large tires to 150 mining companies with long-term operations in countries including Mexico, Chile, Colombia, South Africa, Zambia, Ghana and the United Kingdom, Kal Tire is well-
positioned to expand internationally.
Furthermore, Kal Tire has a big jump on potential competitors like the French multinational giant Michelin, which announced earlier this year that it will build a tire recycling facility in Chile.
“We decided we wanted to be first in,” says Farnham. “We didn’t want to be second or third in the market.”
D’Arcy Jenish is an eastern correspondent for CMJ and the author of several books.
Comments