Ventilation on demand: it is the mine that guides us

Clean, safe air is essential to life and too often overlooked or taken for granted. However, not in the mining industry. Two years ago, the global mine ventilation market was projected to reach a value $565.4 million by 2030. “Among the other noteworthy geographic markets,” said France’s ReportLinker Consulting, was Canada, forecast to grow “at 3.3% over that period.”
The reason for the global acceleration in mining ventilation and refrigeration, said BBE Canada’s director of operations, Morné Beukes, “is older mines going deeper and further away from current infrastructure. The more you do that, the more ventilation activities become necessary. Today, an entre science is facilitating development of robust, well-managed ventilation systems for underground mining in Canada.”
Just imagine
No company is more aware of that than Epiroc, which acquired Meglab in Val-d’Or, Que., in 2021. Meglab clients, like Newmont Gold at its Borden mine in Chapleau, no longer rely exclusively on ventilation doors, large 400 HP intake fans at surface and smaller fans to re-direct gas-filled air to the ends of a spiderweb of tunnels and out the mine.
To that mix, Meglab has added a ventilation on demand (VOD) control system called “Imagine,” which, among other things, pays close attention to the actual ventilation needs in particular zones of the mine to prevent over-ventilation.
The Imagine system features automated fan start-up and shutdown, networking each fan starter to an anchor or “tag reader” to detect the presence of Imagine tags on workers and vehicles in a specific ventilation zone.
“The first step is to monitor all the information from underground as to where the people are and what the quality of gas emissions are,” Meglab general manager, Kim Valade, explained. “We then interact with the driver controlling the fans.”
Today, when a worker or vehicle enters a vent zone and the Imagine ventilation system is activated, air flow accommodates the specific needs of the equipment within that particular work environment. The fans can also be linked to each other to create a start-up sequence.
A good example of this, said sales manager, Duane Berry, is installation of the Imagine system at Borden. Each workday, forty-tonne underground haulage trucks routinely dump particulate matter into the bowels of the mine, requiring a major ramp up in in CFM (cubic feet per minute) of clean, safe air.
“At Borden, airflow requirements range between 23% (the minimum) and 100%. A ventilation team first does a sweep of a tunnel using handheld gas and airflow monitoring devices to determine the operational capability of the fans at different air flow percentages,” explained Berry.
“That produces a nice curve which is then put into our VOD engine which then knows what I can expect in CFM, say at 10% of airflow. And if I know what each vehicle requires for CFM (e.g., an electric versus an emission spewing diesel engine), we can maintain a safe, breathable air, but no more or less than is required.”
“In other words, it is really a system of components that talk to each other. Part of the automated situational awareness system’s success is because of the software. But also, central to knowing where workers and vehicles are located at any given time is hardware component of the tracking system,” said Valade.
“You have fans, you have variable speed drives. Our system permits all of this to work together. Because of this, we know where the workers are, so we can send the right amount of quality air to them. Not to be overlooked, is a 40-50% reduction in energy consumption and related costs,” She noted.
All VOD, all the time?
Like Epiroc, BBE Canada develops solutions to optimize mine ventilation, including VOD, but also controlled recirculation applications, thermal ice and water storage, and solar application for absorption refrigeration. Director of operations, Morné Beukes, understands the challenges of reducing deadly, airborne contaminants in an underground mine in both hot and cold climates.
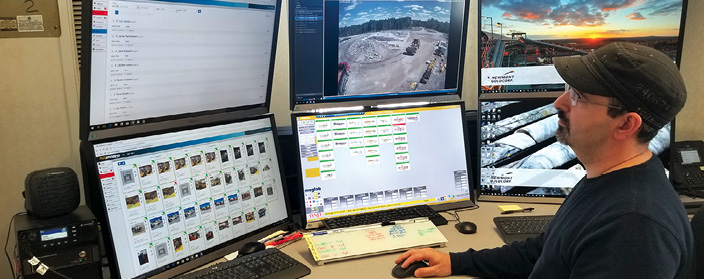
A case in point, he noted, is paralyzing, sub-zero northern Canada where air-to-air heat exchangers “distribute waste heat from upcast air down through mine shafts to prevent them from freezing. Where heat exchange does not apply is where mine shafts, because of the nature of the mine, are too close together.”
Reusing air, entailing whole or partial recirculation of air, has its own limitations, once again depending upon the nature of the mine. For example, freeing up 50 CFM from 200 CFM per second underground, said Beukes, provides an immediately more efficient and cost-effective use of air.
“But that can only be in mines that have filtered out the pollutants. Most will filter out, but not radon, for example,” said Beukes. “A global ventilation consultant, BBE places a high premium on protecting workers from unbreathable air, while meeting its client’s bottom line technical requirements,” Buekes added.
BBE is particularly pumped up about a product called “Vuma,” acquired and developed in South Africa, that simulates heat duct calculations, pollutants monitoring, fire preparedness, and ventilation. “Vuma can be linked to instruments underground that provide real-time monitoring and feedback at strategic points on pollutants, temperature, velocity, etc. And that also works well in conjunction with VOD,” said Beukes.
But Beukes offered a caution. “What we do not do is push specific brands for these underground instruments. These can be procured from various manufacturers or OEMS for use in spoked instrumentation, for example, for location and how these can be adequately maintained.”
Again, everything depends upon the specific areas of the mine you are endeavouring to safeguard. That applies to VOD. We may be at risk of asking too much of this approach to underground mine ventilation,” Beukes said.
“I think VOD is underutilized where there are more opportunities for it. But it depends on the mine, infrastructure, and capital cost for implementing VOD.” That is why so for older mines that lack the necessary communications and other equipment may need to retrofit that into their infrastructure,” added Beukes.
Beukes advised, “first, optimize the ventilation resources you already have in place to full effect and efficiency. Once you are using it 100%, get VOD under your belt and implement it properly so it is also working at 100%. Then look at other things like energy recovery systems and re-use of air and waste heat so that all of these complement one another.”
Fans are the heart, ducting the veins in mine ventilation
You will get no argument about that from Epiroc, which boasts its own system design and installation of fan stations and ducting, or from BBE Canada’s Buekes that ductwork is very important especially when opening new ground. It is the material ducts are made of that determines what the friction factor is during airflow and how much effort is required to advance the air.
“Reducing the friction inside the duct allows the air to travel further, with better flow and better pressure,” explained Jocelyn Lacroix, marketing director of Rouyn-Noranda, Quebec’s Mecanicad. “Because we have the lowest friction factor in the industry, we can move air even longer distances and with improvements in both airflow and pressure,” added Lacroix.
Lacroix attributes this to Mecanicad’s use of plastic instead of fabric or steel ducting, providing five times longer distance for air to flow than fabric ducting. Pressure resistance inside the ductwork naturally depends on the type and size of the fan in use.
This frees his clients to use bigger fans where needed. Or they can reduce both the fan and duct size to provide more space for higher volumes of rock in haulage trucks. Creating higher payloads reduces mine costs, as do reductions in fan speed.
“If the mine is 500 meters long, for example, you do not need to use the fan at 80% efficiency; you can probably use it at 50% because the friction of plastic ducting is so low. Our plastics have good memory shape and resistance to hits from rock. Their properties give us tremendous advantages,” Lacroix added.
But why plastic rather than fabric or steel? Lacroix acknowledges fabric and steel ductwork have their place in underground mine ventilation. Steel is durable enough to withstand the effects of blasting and easily connects using flanges and v-locks or can be built with a plain end connected by a 12-inch draw band.
Its higher weight, however, makes underground installation more cumbersome compared to lighter plastic, and steel typically has a high friction according to Lacroix.
Round or partially round fabric ducting (made from polyester and known as air socks or textile ventilation) are advantageous and can do the job in smaller tunnels where air volume requirements, too, are comparatively small,” said Lacroix.
Its usefulness diminishes in larger mines and the higher the air requirements are. That is perhaps one reason why Lacroix’s assessment of plastic’s importance is so bold. “I have no hesitation in saying that 90% of mines in Canada employ plastic underground ducting,” said Lacroix. CMJ
David Godkin is a freelance writer.
Comments