Top Tips for oil selection
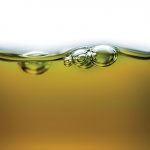
Understanding oil viscosity is essential.
Mining equipment has many specialized requirements due to the significant power levels at which they operate. It is expected to perform at full capacity for 24 hours a day, seven days a week. Combining these factors with operations in some of the world’s harshest conditions, the role of engine oil becomes a crucial factor in the reliability and performance of mining equipment.
Working throughout these extreme conditions, lubrication is especially important to ensure the necessary equipment protection by minimizing metal-to-metal contact between moving components. This is particularly important during cold starts, which are a significant factor in contributing to engine wear.
Extended warm-up periods can adversely affect the lubricant’s viscosity and in turn, affect the protection offered to vital components.
Lubricants are limited to optimal temperature ranges and consequently, when their temperatures change and reach the “critical” zone, lubricants can become overly viscous. The consequence of this can be harmful to equipment; if improper lubrication occurs, under these stressful conditions, equipment can seize up or even fail.
With the impact of downtime being so significant in a mine, selecting the right lubricant requires careful consideration. To ensure the correct selection of lubrication, there are four key tips to consider:
- The decision should always begin with consulting the original equipment manufacturer (OEM) vehicle manual – or contacting the manufacturer directly for further advice when deciding upon a suitable product.
- Consider what conditions the equipment works in – both how the oil is used and the climate in which it operates should be reviewed. Lubricants are available in different SAE (Society of Automotive Engineers) grades, which dictate the acceptable temperature range in which they can perform optimally. According to the engine oil viscosity classification, the “W” following SAE viscosity grade stands for “winter” and not “weight” as many believe. This indicates that the oil is suitable for use in, and most importantly, provides protection in colder temperatures. For mining equipment working in warmer conditions, a heavier grade oil such as SAE 30 or 40 grade may be more suitable. These oils can resist the lubrication breakdown that comes with higher operating temperatures by ensuring adequate lubrication flow and the subsequent protection of critical engine components.
Understanding oil viscosity is essential for selecting the correct lubrication for mining equipment as it dictates the oil’s ability to flow, or its internal resistance to flow. If the oil’s viscosity is too high, the oil will resist easy movement which could delay lubrication and protection of critical engine components during a cold start-up event. This could increase engine wear and affect equipment performance.
- Review the benefits of synthetic vs. non-synthetic – Full synthetic and synthetic blend engine oils possess better stability than conventional oils. Full synthetic oils are formulated with synthetic base stocks that are blended with high quality and often unique, performance-enhancing additives. These formulations offer a greater level of protection in a variety of weather conditions.
- Proof of performance – the final consideration should be whether the oil manufacturer can demonstrate their product line’s credentials with proof – such as OEM approvals, field data in same engine and vocation or customer testimonials.
To provide solutions for these recommendations and to adhere to the highest industry standards – including North American API CK-4/ FA-4 – Petro-Canada Lubricants developed the DURON heavy-duty engine oil product line.
Successfully extending oil drain intervals and providing protection in extreme environments within a range of heavy-duty mining vehicles, DURON has a proven history of helping mining fleet operators reduce their maintenance costs.
Selecting an incorrect grade of lubricant or adding an aftermarket additive to it could result in the invalidation of warranty, increased aeration issues causing foaming, increased wear, inefficient engine operation or unnecessary downtime.
Therefore, ensuring that professional recommendations play a part in the decision-making process should be a priority for mining operations. Brian Humphrey is OEM Technical Liaison with Petro-Canada Lubricants.
To find out more about DURON, visit www.lubricants.petro-canada.com and search DURON.
Comments