The right lubrication can make all the difference in harsh mining conditions
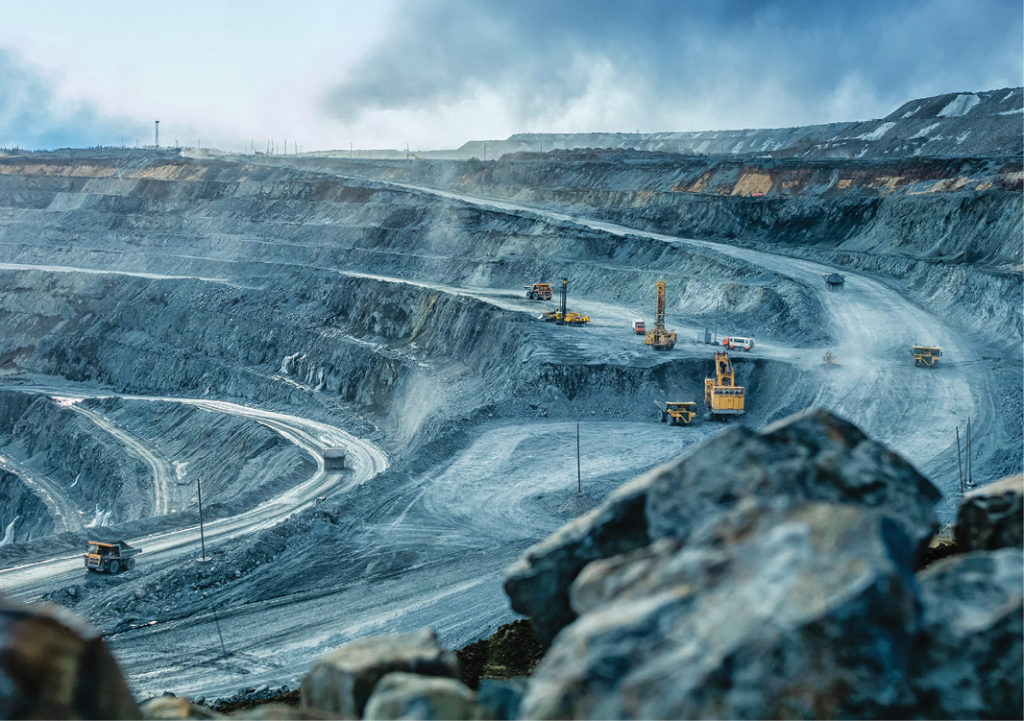
Mining operations can present significant challenges, especially when dealing with extreme environmental conditions. Equipment at mines is often exposed to the elements of the weather and other conditions 365 days a year, meaning that mining operators are trying to keep their equipment running and maximize uptime even as they combat dirt, weather fluctuations, and complications imposed by a heavy load. This is why, when it comes to extreme heat, severe cold, or wide temperature fluctuations, your choice of lubricants is your first and best defense.
Why lubricants over all the other components that can protect equipment? Because a properly selected lubricant can improve operations by protecting critical components and preventing premature wear. Extreme heat lowers viscosity, reducing the thickness of the lubricant film and ultimately rendering the protection provided inadequate. On the other hand, extreme cold can cause poor start up performance — or even damage to the equipment — because of the excessive viscosity that can negatively impact pumpability, efficiency, and most machine operations.
Mining operators are trying to achieve their performance objectives while also reducing their impact on the environment by lowering lubricant consumption and waste. High quality premium and synthetic lubricants can help extend oil drain intervals safely, thereby helping advance customers’ sustainability ambitions — but even that technological advantage can be undone by the realities of working in environments with both blisteringly hot summers and frigid winters. High performing lubricants inside a properly maintained machine can extend oil drain intervals beyond what was traditionally considered normal; however, mine sites are inherently dirty by nature, and in this environment, lubricants can become contaminated during maintenance services and can necessitate premature oil changes. These additional service events lead to increased product consumption and more time that technicians need to interact with equipment, which can impact safety and decrease machine availability.
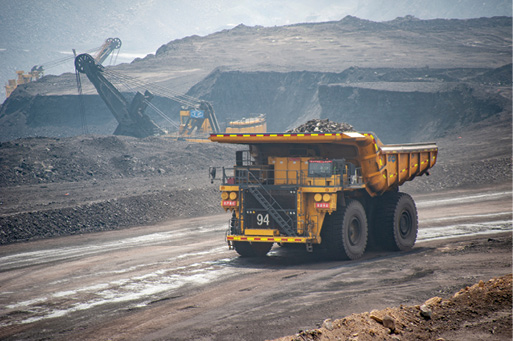
Fortunately, technological solutions exist for this challenge. High performance, multigrade lubricants formulated with a balanced base oil and additive solution can help equipment perform across a wide range of temperatures, allowing them to stay in service through wide ranging temperature fluctuations. This enables mining operations to avoid seasonal changeouts and offer an all-season solution, helping operators extract more value out of their oil and their equipment.
There are three primary advantages to using high performing lubricants in your harsh environment mining operation:
- Saving money By switching to an all-season, multigrade product, mine operators can lower their total cost of ownership (TCO) through extended oil drains, increased component life, and improved fleet uptime. We are often able to work with large mining customers to extend the oil drain intervals in engines — sometimes up to 2,000 hours. With filtration, transmissions can often be extended up to 6,000 hours, hydraulics up to 10,000 hours, and differentials to around 12,000 hours. Of course, when extending drains, it is important to use oil drain analysis to ensure that drains are being extended safely. As alluded to, one of the more significant impacts is because of the logistics of seasonal changes. High-end engines can go out to 1,500 hour oil drain intervals (ODIs), transmissions out to 6,000 hours, hydraulics out to 10,000 hours, and differentials to 12,000 hours (with proper filtration) in a single year — but if your fleet is using oil with a limited temperature range, the transition from summer to winter (or the reverse) can necessitate a switch long before the oil reaches the end of its useability. The unpredictable nature of weather compounds this challenge further: a sudden cold-snap or heat wave can necessitate an unplanned seasonal changeout with very little notice. Multigrade lubricants can work across a wider temperature change, and in some instances eliminate the need for seasonal changeout, or at least provide more operational flexibility.
- Improving safety Most experienced miners know that the best way to maximize safety is to minimize the time your team spends working hands-on with the machinery. Increasing ODIs can help reduce the number of oil changes, which in turn reduces the number of hours spent interacting with equipment. Furthermore, less time spent conducting routine maintenance can reduce the chances of contaminants entering the lubricant or components, which can reduce the chances of the unplanned future downtime or, in extreme cases, the dangerous catastrophic equipment failure that can result.
- Minimizing waste and in-use greenhouse gas (GHG) emissions Extending drain intervals can also help reduce product consumption and, as a result, the waste oil generated in an operation. High quality synthetic lubricants can also help equipment run more efficiently and, in some cases, reduce in-use GHG emissions.
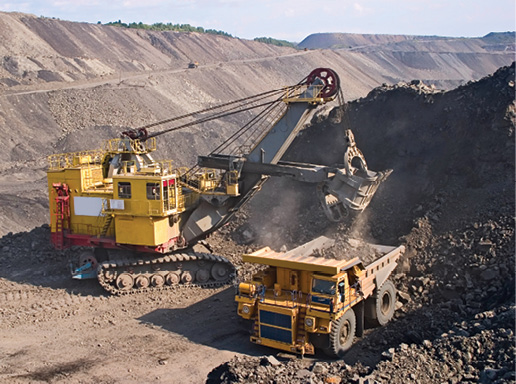
What to expect from the future of mining
Mining is an old business based on simple principles — you extract minerals from the ground — but it is also a rapidly growing, innovating, and evolving industry. Every year, equipment gets lighter, smaller and can do more work — and these improvements often place a greater demand on the lubricants. From fully autonomous vehicles to smaller gearboxes capable of bearing heavier loads, lubricants play a key role in many major mining industry innovations and will only become more essential to cutting-edge performance as we improve our operations in the many industries we serve.
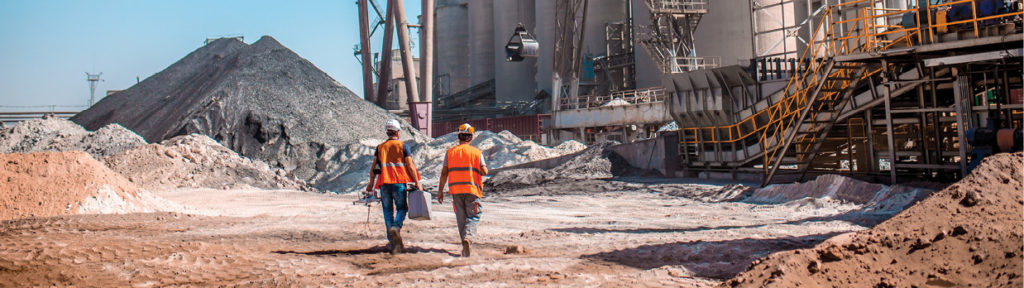
Roger Young is a senior field technical advisor for Imperial Fuels & Lubricants, part of ExxonMobil’s Canadian Operations. His focus is to provide solutions to the mining operation around productivity, environmental care, and safety.
Comments