The race to electric power
How demolition machines provide safe electric power
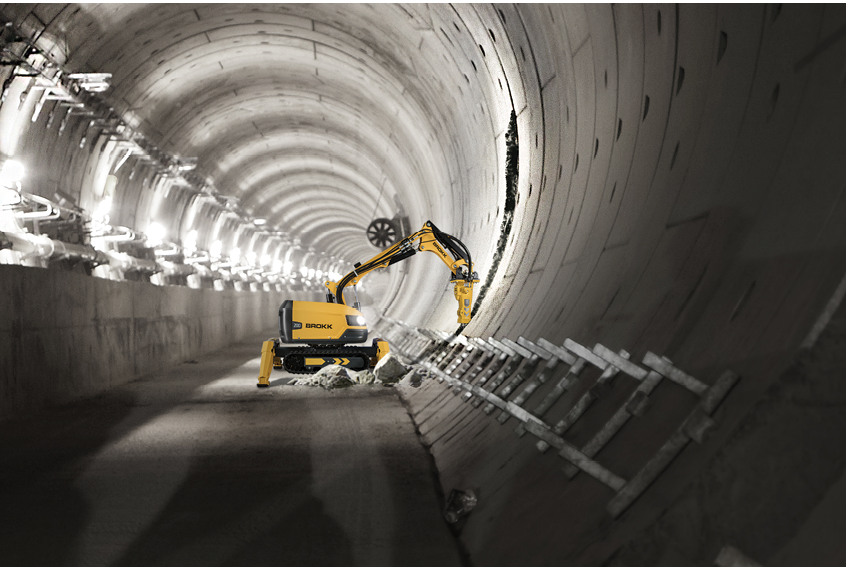
Alternative power is a worldwide trend. Virtually all large and midsized heavy equipment manufacturers have released an electric option in the last few years. The real question comes in optimizing performance. Does the product have the power to get the job done?
No matter how impressive these new models are, remember some equipment manufacturers developed electric equipment decades ago and have spent years perfecting it. Long before electric equipment became a trend, demolition equipment manufacturers created innovative, safe ways to accomplish dangerous, labor-intensive tasks. As time goes on, these manufacturers have continuously optimized their machines for the best power and performance.
In the beginning
Demolition has always been dangerous. Back in the 1970s, there weren’t many options available to solve the issues contractors ran into: limited access, confined spaces, low floor loads and nearby occupied spaces. The only way to get the job done was to send in workers with hand tools. This put workers at risk of injuries, both long term and short term.
The first remote-controlled demolition machines were born out of the need for safer, more efficient options. While some diesel models are offered today, these machines started and continue to be electric more than 45 years later.
After being introduced in 1976, the technology continued to evolve. Today’s machines look like small excavators with a three-part arm that often wields a breaker but can use a variety of attachments. Robots range in size from 600 mm wide and 560 to 2,150 mm wide and 11.4 tonnes. The smaller robots can drive through a standard doorway, fit in a passenger elevator or even climb stairs.
But do not let the compact size fool you. Demolition robots are engineered starting at the tip of the breaker for maximum hitting power. The result is that, pound-for-pound, demolition robots provide the highest power-to-weight ratios in the industry, delivering the same results as an excavator three times the size. Combine that with a three-part arm, an electric-powered demolition robot offers exceptional reach and power in all directions, providing maximum prevision and accuracy while the operator works from a safe position.
Advancing attachments
A variety of attachments further increases the value of compact electric power. Equip the robot with a shears attachment and efficiently and safely tear out concrete reinforcements, sprinklers, conduit, wire and cables. Or use a concrete crusher for “silent” demolition. The crusher attachment “chews” down a wall as opposed to using the force of the breaker to knock it down, reducing noise and vibration. For top-down applications where noise and vibration are primary concerns, crushers allow contractors to work during the day, sometimes without neighbors noticing.
These capabilities have years of experience behind them, making electric demolition machines the go-to for everything from soft demolition to refractory removal, ladle cleaning, underground mining, tunneling and many other unique applications, including driving helical piers.
Looking toward the future
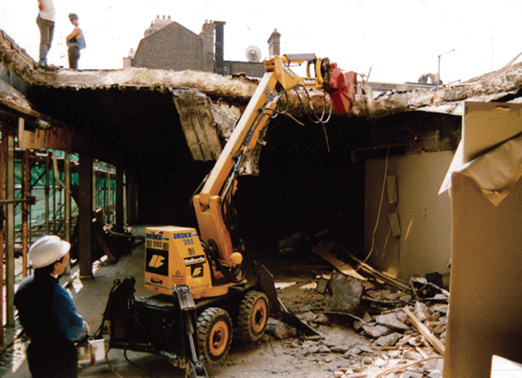
Electric equipment solutions are nothing new in the demolition sector. For many contractors, it has become just another day on the job. As manufacturers continue to develop their electric equipment, they will need to focus on creating equipment that can meet the high-power demands of the demolition and construction sectors. Luckily, some manufacturers have already figured out the power-to-weight ratio of their equipment and continue to work toward perfecting these processes.
Jeff Keeling is vice-president, sales and marketing, Brokk Inc.
Comments