The other BEV supply chain nobody is talking about
As mines continue to get deeper, operations become more expensive to develop and operate. One way to remedy these issues is through the adoption of underground battery electric vehicles (BEVs), which not only save on costs of ventilation and cooling, but they also improve worker health and safety by being emissions-free. This has led to unprecedented demand for BEVs coming from the mining companies eager to unlock the benefits downstream. What has resulted has been a herculean effort on the part of the mining equipment manufacturing community to design, develop, and deploy BEVs in a very short timeline. These underground innovators achieved this on their own by building new component supply chains from scratch and developing in-house expertise and engineering bench strength starting nearly at square one.
In response to the new demand, underground vehicle manufacturers have been able to rise to the challenge set out by their end user customers and build out advanced electric platforms at an incredibly quick rate in an industry not typically known for its speedy innovation to adoption timeline. In a time where all eyes are on the next new electric car being developed by the big automakers, it is important to highlight how mining equipment companies have rapidly developed emission-free alternatives. On top of the obvious technical challenges this feat has posed, it is noteworthy that the electrification we see taking place in the underground equipment space has occurred largely during a time marked by travel restrictions and unprecedented delays within the supply chain and work-from-home policies due to the global Covid-19 pandemic. This fact, coupled with the shear speed of this transition makes the feat even more unlikely and impressive.
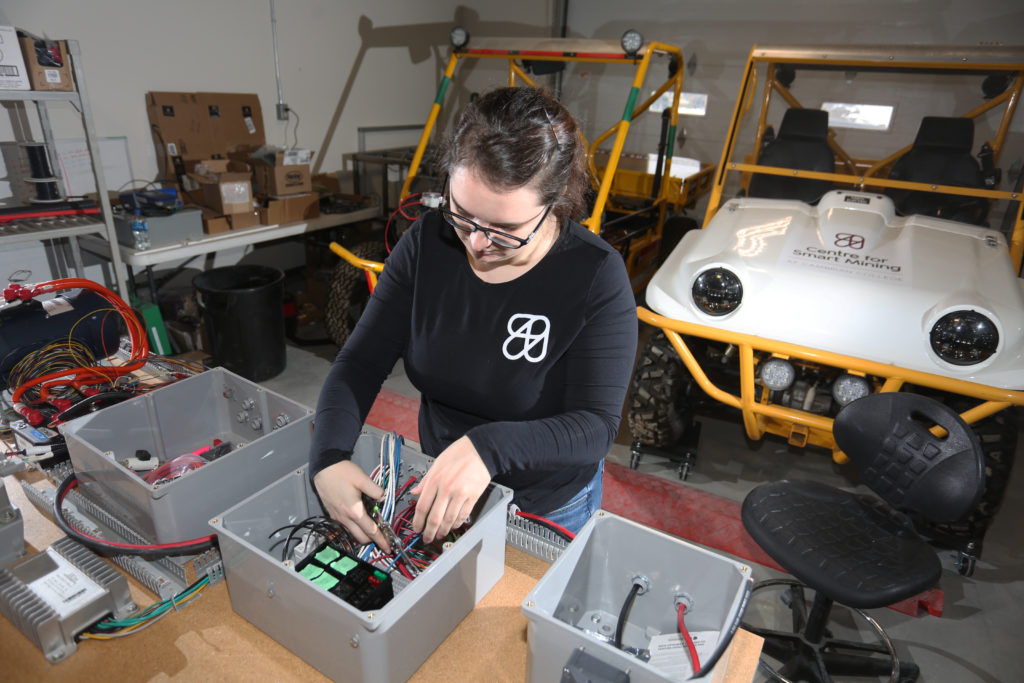
Credit: Centre for Smart Mining
Underground equipment manufacturers are not the same as car companies. Automakers have a closer relationship with the manufacturers in their supply chain as orders for vehicles sometimes total in the thousands of units and suppliers often develop unique assembly lines to meet vehicle-specific production quotas. As such, these long-term reciprocal relationships can result in a responsiveness among parts suppliers to pivot and make new components when required. Locally, we see this with tier one parts makers like Linamar, who have begun to make the shift from ICE (internal combustion engine) to electrified vehicles by investing heavily in R&D, design/validation expertise, and production equipment necessary to provide products needed for the electric auto sector of the future. However, this symbiotic relationship does not exist to the same extent in the mining equipment sector.
Original equipment manufacturers (OEMs) of battery electric equipment in mining have had to build out a supply chain without the R&D budget, devoted parts ecosystem, and talent pool enjoyed by the auto sector. Electric propulsion in underground mines is by no means a new concept, as electric locomotives and plug-in jumbo drills have been around for some time. However, starting around a decade ago, underground mobile equipment manufacturers began developing untethered battery-powered equipment. While there are fewer parts on electric units, OEMs had to forge brand new relationships with parts providers. To put that into perspective, the diesel powertrain components were now being replaced by electric parts. At minimum, vehicle engineering teams were being asked to source reliable providers of components not used previously, such as inverters and power control units, onboard and offboard chargers, DC-DC converters, electric traction motors, auxiliary batteries, powertrain thermal management solutions, high voltage cables and connectors, charging ports, battery packs, and battery management systems to name a few. The fact that these talented teams were successful in such a short period in establishing reliable sources of the technologies they needed should be recognized as a significant accomplishment.
Adding to this already difficult task, OEMs were making these relationships without the “carrot” of thousands of unit orders in hand which are commonplace in the auto sector. While the sale price for an underground EV is nearly 1.5 times that of its ICE counterpart, unit totals per OEM number in the dozens per year. This inherently makes developing strong, long-term linkages more difficult. As a result, companies have had to employ partnership strategies for this enterprise to make business sense. Some OEMs have opted to secure their supply chain via mergers and acquisition with suppliers in the ecosystem. Others have worked with intermediary engineering firms that work with multiple OEMs to pool demand and set-up adequate volumes for component ordering. Each OEM has developed a strategy for supply chain management of electrical components that is right sized for their needs. To avoid painting an overly rosy picture, it should be noted that gaps in the supply chain do persist and procurement departments at OEMs must be nimble and adapt; especially as equipment changes and evolves over time.
Perhaps as important as the component supply chain, the mining equipment OEMs did not have an initial pipeline of talent to shift to electric vehicle development. There are relatively few electric vehicle experts with decades of experience hanging around to draw from. And, if there are, many of them are looking to the automotive sector for their next career move and not the heavy-duty mining sector. Again, mining OEMs had to innovate and overcome. Some OEMs have found talent in obvious places such as engineering departments at automotive and automotive parts manufacturers while others have found people working at mobility start-ups as far away as Silicon Valley. Others still have taken it upon themselves to develop talent internally by retraining and augmenting the capacity of existing engineering staff to design and develop EVs. The good news is there is a nascent talent pipeline developing in Canada. Namely, engineering programs that focus on electric drive train development at Ontario Tech University, MacMaster University, and the University of Windsor have started producing high-quality graduates, and I have even seen some of them starting to trickle into the mining OEM space. Moreover, the new battery electric vehicle lab at Cambrian College will be the first academic facility to focus on the heavy-duty electric vehicle sector, and it will start turning out highly skilled graduates later this year.
Despite these challenges, the OEM ecosystem in Canada has performed admirably. By last count, there are at least 12 companies that are either Canadian-owned or that have a strong Canadian presence currently manufacturing electric equipment in the sector. There are about a half-dozen more that are currently working diligently on the R&D needed to offer BEV versions of their equipment. Adopting EVs at mine sites comes with its own intricacies and complexities, and perhaps that is a story for another time. For now, all indications are that the demand we are seeing for electric equipment is expected to sustain and even increase and we can expect our OEMs to continue to rise to the challenge.
Steve Gravel is the manager of the Centre for Smart Mining at Cambrian College.
Comments