Costmine: The cost of driving drifts in various scenarios
Within underground mines, the primary horizontal transportation openings are provided by drifts. A significant portion of overall development costs often account for their construction, and production costs may be noticeably affected by these excavations. To offer insight into the expense of excavating drifts and ramps, Costmine has designed an array of typical configurations and estimated the associated costs. These costs were estimated with the help of a software application from Costmine’s suite of engineering-based mining cost estimating applications, Sherpa Underground. The following table summarizes the results of these estimates in U.S. dollars (2021) per metre of advance:
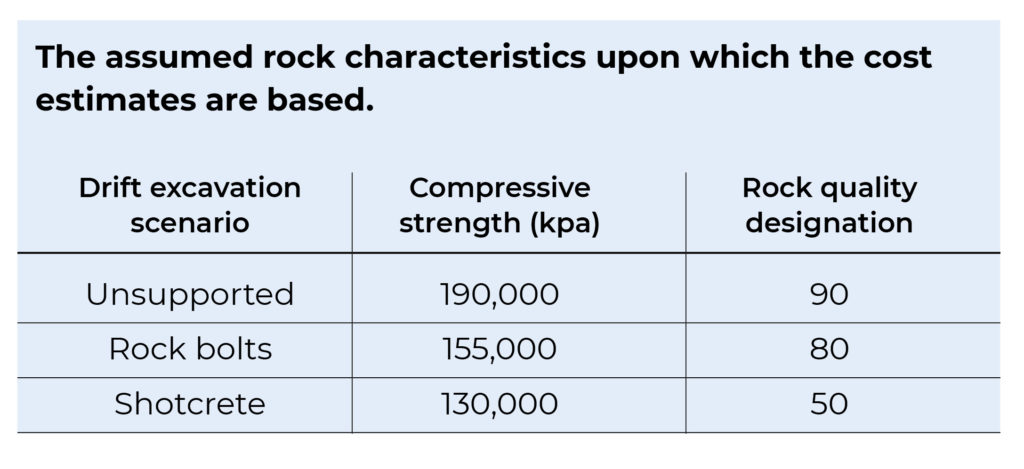
Equipment
In our designed configurations, blast holes for openings with face areas of less than 9.28 m2 are provided by airleg drills. Jumbos equipped with drifters drill the blastholes for the larger faces. In both the ramps and the untracked drifts, development muck is collected and transported using scoop trams. In tracked drifts, muck is collected and loaded into rail cars by overshot muckers. Diesel locomotives transport the cars away from the active face to the dump point. The costs of operating the necessary ancillary machinery (such air compressors, auxiliary fans, and pumps) are also included in the estimates.
Materials and supplies
In our designs, high strength emulsion-based explosives are used for all blasting. Powder factors are tied to the face area of the opening and to the quality of the rock and vary from a low of 0.53 kg/t to a high of 1.67 kg/t. Under appropriate conditions, less expensive blasting agents (such as Anfo) can be used, which in most cases would result in a reduction in the costs of the blasting supplies. However, the use of bulk explosives is often accompanied by an increase in the required powder factor. Blasts are initiated with non-electric millisecond delay caps. Where rockbolts are used for support, our designs assume that the bolts are placed 1.2 metres on center and one steel mat is used for every three bolts.
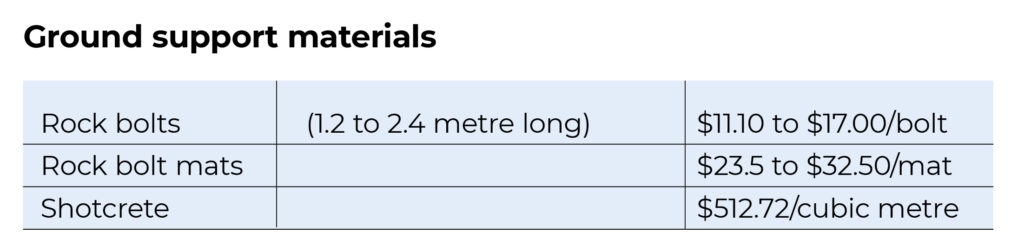
Excavation Cost
Finally, the drift development cost estimates are summarized below in units of U.S. dollars per metre of advance.
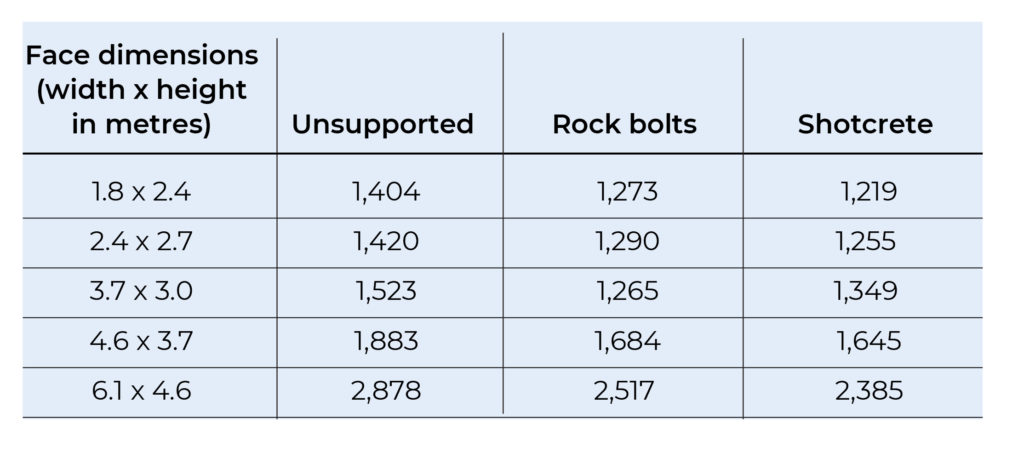
Costs are not included for items such as move-in and set-up, yard preparation, support equipment installation, camp facilities, design and engineering, or contractor profit.
Conclusion
For all the drift excavation scenarios investigated, expenditures for labour far exceed those for any other cost category. Labour’s contribution fell within the range of 50% to 60% of the overall cost estimates, with supplies accounting for about 15% to 20% depending upon the drift excavation scenario.
The estimated development costs may strike some readers for lower-than-expected distribution of costs between support methods. This may be the result of decrease in quality rock characteristics that would require stronger rock support methods, which was accounted for in the reported estimates. As the quality of the rock decreases, the consumption rates for drilling and blasting supplies fall. The associated reduction in costs is offset, to a degree, by an increase in rock support costs. This balance is the primary influence on the cost distribution among the excavation scenarios described above.
Sam Blakely is a senior mining engineer with Costmine, a division of The Northern Miner Group
Comments
abbas sharafi
very good site