Optimizing ventilation systems for underground mines
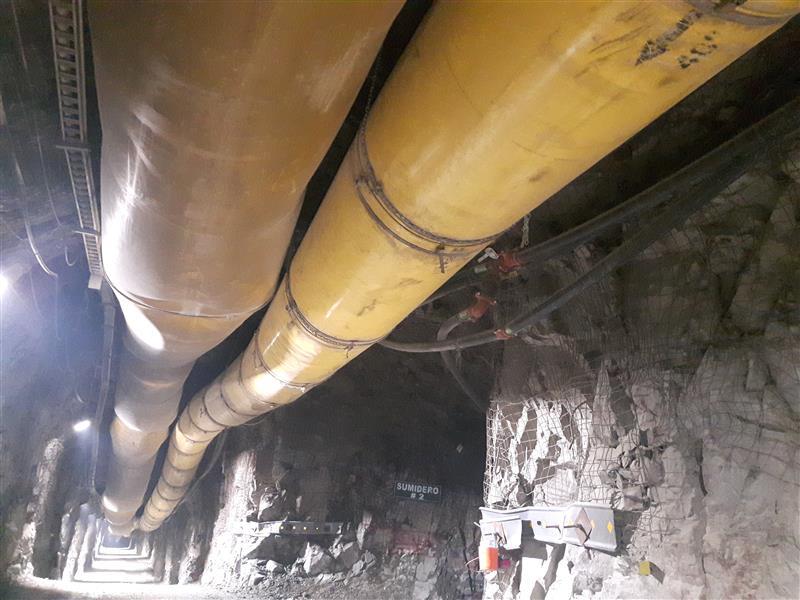
An underground mine’s ventilation system is an intricate series of drifts and raises connected to a main backbone designed to deliver fresh air throughout the mine while safely exhausting contaminated air to the surface. As mines expand deeper underground and further laterally, the ventilation system must work even harder to push fresh air to where it is needed. This increased demand could lead to higher costs — whether from installing larger fans, adding more equipment, or perhaps constructing a new vent raise, which could easily range from $200 to $300 million.
With operational costs under constant scrutiny, mining companies are looking for smarter, more cost-effective solutions. Implementing ventilation control strategies offers a viable option for reducing energy consumption without compromising air quality. Given that ventilation accounts for roughly 50% of an underground mine’s overall energy consumption, implementing the right strategies could extend the system’s capacity, ensuring fresh air where it is required, essentially maximizing efficiency, and making the most of existing infrastructure.
Three key strategies for optimizing mine ventilation
Controlling fresh and exhaust air fans efficiently can significantly improve ventilation performance and reduce costs. Here are three key strategies:
1) Scheduling: Fresh air requirements during regular operations are generally based on mobile diesel equipment airflow requirements or heating and cooling conditions. However, when blasting occurs, additional contaminants enter the airflow, requiring a clearing period that forces personnel to remain on the surface for two or more hours, cutting into valuable production time. By strategically scheduling and increasing main fan airflow using variable speed drives (VSD s) on the main surface fans and remotely controlled starters on auxiliary fans, the blast clearing period can be reduced by up to 50%. This allows personnel to return underground sooner and resume mining operations more quickly.
2) Telemetry: Equipping personnel and mobile equipment with radio-frequency identification (RFID) tags allows for real-time tracking of underground activity per location by control room operators. These tags communicate via wireless signals, requiring additional underground network infrastructure to transmit data back to the surface. A telemetry or asset-tracking system could then provide the precise or general tag location, allowing auxiliary fans, when equipped with normal starters, two-speed starters or, in some cases, VSDs, to adjust airflow based on equipment type or operational needs in specific headings.
3) Environmental monitoring: Installing sensors throughout the underground mine to track airflow, temperature, and parts per million (ppm) concentrations from contaminants produced by diesel or other equipment enhances ventilation control. Regulations dictate airflow requirements based on diesel equipment horsepower and the presence of contaminants such as carbon monoxide (CO), diesel particulate matter (DPM), nitrogen oxides (NOx) and other hazardous gases. By monitoring air quality continuously, ventilation systems could be programmed to increase fresh air flow automatically when hazardous gases reach critical levels, ensuring a safer work environment.
Smart investments that deliver long-term value
No matter which ventilation control strategy is implemented, investing in automation enhances worker health and safety while optimizing infrastructure and equipment. The capital cost must be weighed carefully against potential energy savings, the fresh air requirements of different mine areas, production impacts, and the projected end-of-mine life.
Depending on the selected strategies, additional expertise in ventilation or automation may be required to support system upgrades.
The importance of a thorough assessment
Before implementing ventilation automation, a comprehensive assessment of current mining operations and infrastructure is essential to determine feasibility. Key factors to consider include the following:
Energy consumption: Estimating the ventilation system’s current energy use based on the total fan horsepower.
Mine plan: Evaluating long-term development leading to end-of-mine life.
Operational schedules: Reviewing shift changes and blasting schedules to identify efficiency opportunities.
Ventilation model: Ensuring fresh air is available when and where it is needed.
Maximizing efficiency and safety
Integrating ventilation control strategies is a proven way to lower operating costs, extend equipment efficiency, and gain deeper insights into system performance. It also enhances health and safety by reducing hazardous contaminants and improving real-time tracking of personnel and equipment using telemetry.
By taking a strategic approach, mining companies can achieve a more efficient, cost-effective, and safer underground environment.
Mark Lafontaine is BBA’s Sudbury office director.
Comments