Inertial navigation paves the way for resilient mining
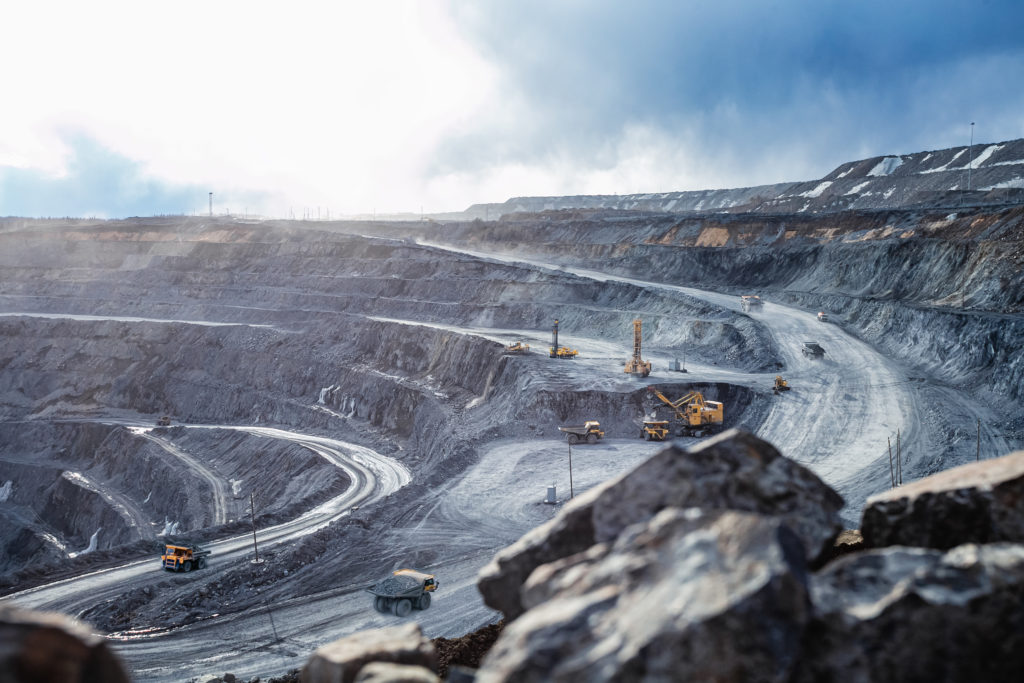
Since the late 1990s, the earthmoving sector has been utilizing GPS technology for advanced machine guidance and process optimization. By receiving signals from a network of satellites orbiting the Earth, GPS receivers mounted on mining machinery can provide real-time positioning information, enabling operators to pinpoint and monitor the exact location of all equipment.
Nonetheless, relying solely on GPS comes with setbacks. For one, GPS is only suitable when the equipment has a clear view of the sky with decent satellite coverage to provide positioning information. This means underground mining must rely on alternative navigation methods. Projects in open-pit mines are also susceptible to multipath GPS signals.
Further, GPS is vulnerable to ionospheric scintillation, where the signal waves are disrupted by small-scale irregularities in the ionosphere. This issue is most severe in sub-equatorial regions and at auroral latitudes, which covers much of Canada — the fourth largest nation by mine production volume.
Inertial navigation as a redundant system
Mining operators often leverage a myriad of technologies consisting of GPS and other redundant solutions, such as an inertial navigation system (INS). An INS uses a variety of environmental sensors, including accelerometers and gyroscopes, to detect and measure the change in motion of an object. Using this sensor data, the INS can determine the position of the object relative to its starting point — a process known as “dead-reckoning.”
When mounted onto a mining vehicle, this presents several fundamental advantages. Firstly, an INS can provide updates at a higher rate than GPS. This allows it to output data much faster and provide orientation data, roll, pitch, and heading, which the traditional GPS system is incapable of achieving.
INS can also operate in GPS-denied environments. Mine sites are often located in distant, rugged terrains with dust, low light, and unideal weather conditions with signal interruptions. By applying the principle of dead-reckoning and data fusion to estimate position, an INS makes for a reliable technology when GPS positioning information is unavailable.
A combination of GPS and INS data can ensure position, velocity, and attitude estimates of higher accuracies and better dynamic performance. in a real-world example, a bulldozer can have INS units mounted on the chassis and on the blade, with GPS antennas mounted to the cab. The INS units can measure the angle, tilt, depth, and motion of the blade, while the GPS captures real-time positioning data around the dozer’s location, blade position, and the surrounding terrain. All this information would be sent back to the control centre, allowing managers to make strategic decisions over time that would drastically improve efficiencies and yield.
A combination of INS and GPS data can advance the automation capability of certain types of mining equipment, such as autonomous haulages. This means an autonomous, connected fleet where machines can communicate with one another to perform tasks with minimal human intervention onsite, greatly improving safety.
Lowering entry barrier to precise navigation
Across the mining industry, the market for INS equipment is broadening. Manufacturers and system integrators often face trade-offs between a unit’s cost and performance. Where a system provides superior performance, its power consumption and cost often come across as unattainable for mining operators; whereas a system that sits within budget constraints may not achieve the precision and accuracy required to carry out the job effectively.
A less perceptible but increasingly important attribute is the system’s size and weight. Mining operators are trending towards the adoption of smaller, lighter systems that can optimize the use of space in every vehicle’s junction box. Further, with the proliferation of drones and uncrewed air systems used for tasks such as surveying and mapping, having a reliable navigation unit that does not weigh down the overall system is critical.
Advanced Navigation recently rolled out the Certus MINI series. Available in three variants, the series includes a GNSS-aided Certus MINI D and Certus MINI N INS, while Certus MINI A functions as an attitude and heading reference system (AHRS).
Certus MINI D features dual-antenna GNSS heading, allowing it to deliver superior accuracy in heading, position, and velocity. With a maximum weight of 0.055 kg, the series fills a critical gap in the market for a dual-antenna INS in a lightweight and compact size. This level of miniaturization owes to a breakthrough algorithmic technology. This software-enhanced hardware delivers navigation data superior to outputs based on traditional filter methods, offering new levels of performance for miniature INS in GPS-challenged environments.
Certus MINI is the ideal solution for surface drilling OEMs and integrators seeking precise rig alignment. Best-in-class accuracy provides precise alignment even in deep pits where multipath errors occur, and a ruggedized design delivers durability and reliability in harsh mining conditions.
Designed with flexibility in mind, the series is easily integrated into existing and new system builds with simple plug-and-play connectivity, minimizing development time and costs.
Additionally, by operating on the L1/L5 multi-constellation GNSS, the Certus MINI series offers leading capabilities in interference immunity, position accuracy, and multipath resistance.
For mining operators deploying land-based vehicles, this value-driven breakthrough unlocks new possibilities for those using lightweight airborne platforms, such as drones.
Continuing to breakthrough:
Ditching GPS for fingerprints
Recently, Advanced Navigation entered an agreement with UK-based NILEQ to co-develop a resilient INS solution, integrating NILEQ’s absolute positioning technology — suited for a multitude of airborne platforms.
NILEQ’s patent-pending technology is underpinned by the use of novel neuromorphic sensors to derive and match terrain fingerprints. The sensing technology captures data of the changing terrain as an airborne system flies across it and matches it to an existing database of the Earth’s surface.
The concluding solution is set to enable systems, such as uncrewed air systems, to secure an absolute position fix over land with a solution that is passive and resistant to electronic interference.
The solution is expected to enable faster and easily repeatable mining surveys carried out on low-cost drones. This is suitable for large-scale projects, such as site-mapping and infrastructure inspection. It also enhances the safety of beyond visual line of sight (BVLOS) operations, allowing drones to navigate dangerous or inaccessible areas, such as unstable terrains, high walls, or underground tunnels where GPS is not available. Advanced Navigation and NILEQ will validate the system in an airborne demonstration planned in Australia this year.
Inertial navigation is a tested and proven method for maintaining resilient positioning on mine sites when GPS is unavailable. Mine operators should pay special attention to advancements in this technology as they will be pivotal to commercial success.
Chris Shaw is the CEO and co-founder of Advanced Navigation.
Comments