Highlights from MINExpo 2024: Technology and equipment
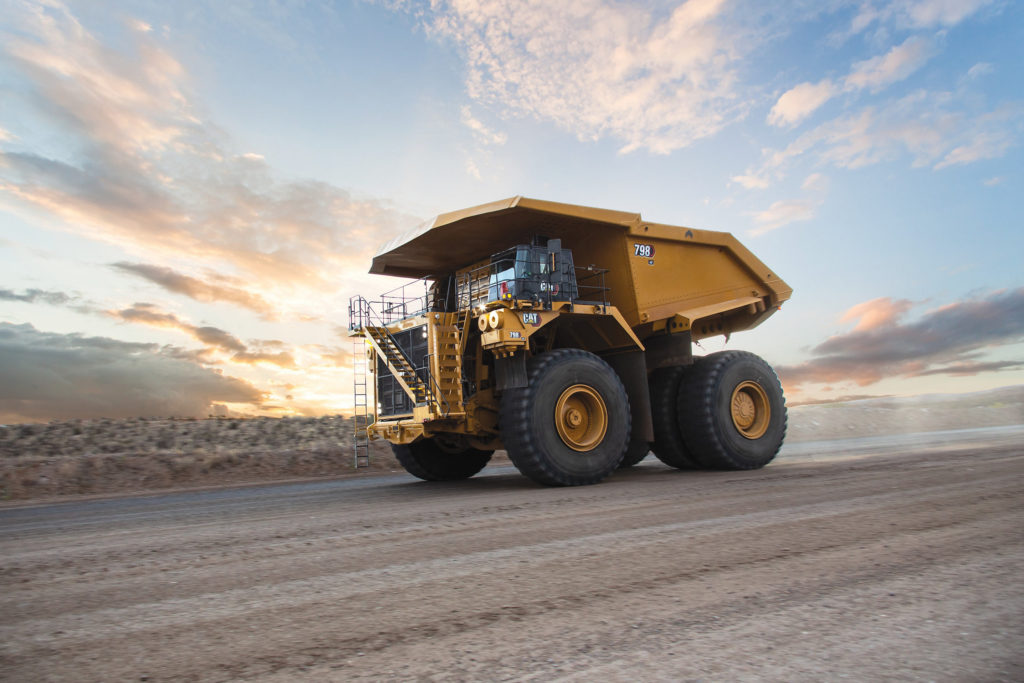
Caterpillar showcased industry leading technologies, cutting-edge innovation and customized solutions for mine sites around the world at MINExpo 2024.
Caterpillar’s MINExpo 2024 experience immersed visitors into the mine site of the future, featuring industry leading technologies, groundbreaking advancements in the energy transition, and first-of-a-kind customized solutions designed to increase customers’ efficiency, safety, and profitability. The exhibit reinforced Caterpillar’s position as the global industry leader in mining technology and showcased the company’s latest innovations to support the energy transition.
The towering, 372-tonne Cat 798 AC mining truck has the highest standard payload in its class and is configured for autonomous haulage with Cat MineStar Command for hauling. “Autonomous technology will help monitor and orchestrate the complex balance of onboard energy, available charging assets, and production targets to achieve the lowest operating costs,” said Marc Cameron, senior vice president, Caterpillar Resource Industries.
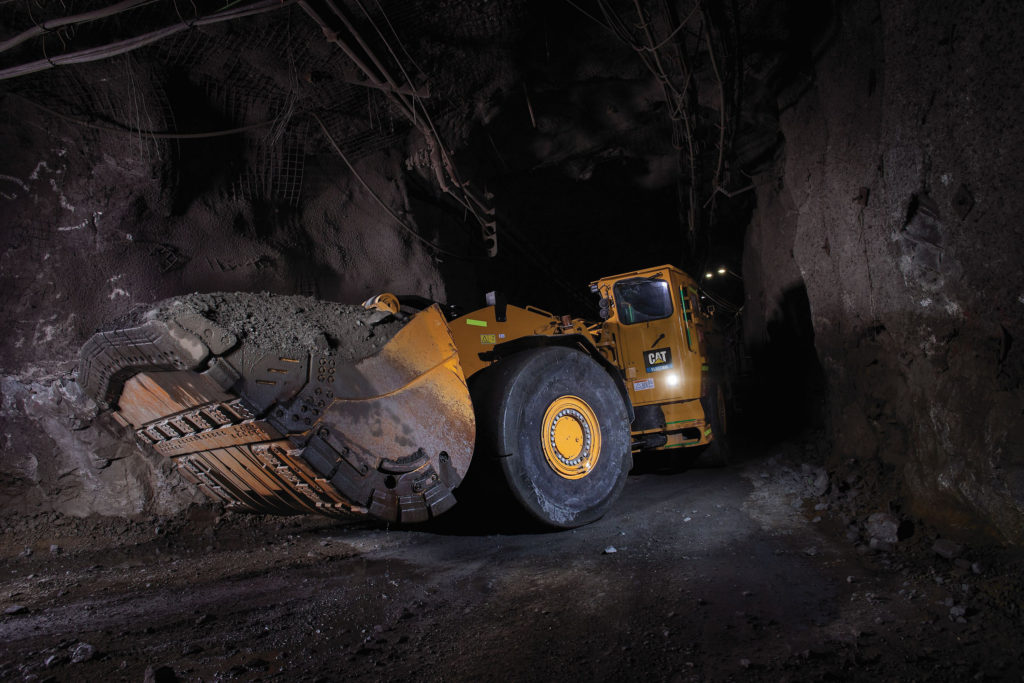
Also, Caterpillar’s underground Cat R1700 XE load-haul-dump (LHD) loader features battery-electric propulsion that produces zero exhaust emissions and generates less heat than a reciprocating engine powered model. Finally, Cat R2900 XE LHD provides a high efficiency switch reluctance electric drive system that meets the mining industry’s needs for bigger payloads, faster loading and lower emissions.
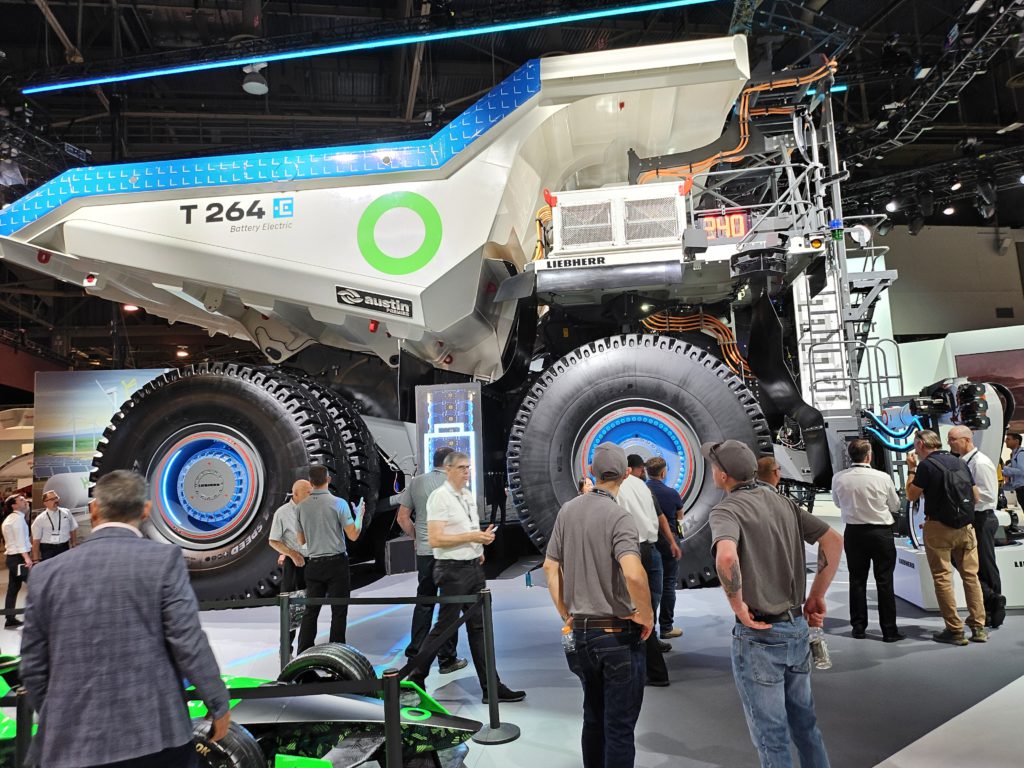
Liebherr’s motto for the event was “Your mining partner.” The company’s executives provided insight into Liebherr’s reliability as a partner for best-in-class equipment, decarbonization solutions, cutting-edge technologies, and service excellence.
During the exhibition, the company made several product announcements, including the unveiling of its autonomous battery-electric T 264 haul truck, the new PR 776 Generation 8 dozer, and the expansion of its integrated technology portfolio, IoMine.
Liebherr and Fortescue unveiled the very first autonomous battery-electric T 264 haul truck. This truck represents the culmination of years of hard work and the joining together of the autonomy and zero emission arms of the Liebherr–Fortescue partnership. The autonomous battery-electric T 264 has a 3.2 MWh battery (developed by Fortescue Zero).
A static charging solution has been developed alongside the autonomous battery-electric truck. The static charger will be available in both manual and robotic versions and includes an automated quick charger of up to 6 MW with a megawatt charging system connector that can charge battery-electric T 264 trucks in 12–58 minutes.
The truck on display was equipped with the Autonomy Haulage Solution (AHS) that was jointly developed by the two companies.
The tires on the T 264 at the exhibition are Michelin 50/80R57 XDR 4 SPEED ENERGYTM (see Michelin’s section below) — the first energy efficient tire for the mining industry. Because they are made with a new energy-saving rubber compound and have an optimized tread with increased flexibility, these tyres help reduce the amount of energy consumed by mining haul trucks. The 50/80R57 XDR 4 SPEED ENERGYTM tires have been shown to reduce fuel consumption by 3.6 % in flat conditions when compared to the Michelin 50/80R57 XDR 250 C tires running on a combustion-engine truck and are expected to have a positive impact on vehicle range for battery-operated trucks.
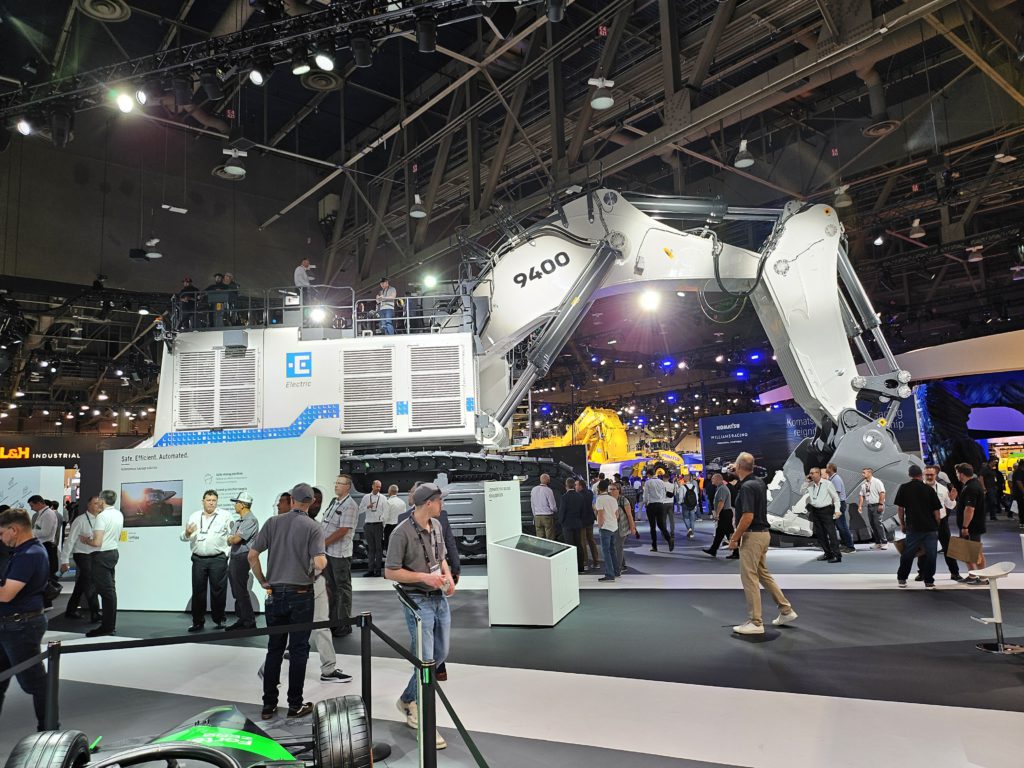
To highlight Liebherr as a reliable partner for decarbonization solutions, the booth included the R 9400 E 350-tonne excavator, featuring some of the mining product segment’s latest innovations and equipped with the company’s brand-new cable reel solution for increased manoeuvrability.
Liebherr has also launched its expanded technology portfolio, IoMine, at this year’s MINExpo. The products within IoMine are split into three distinct product families, each dedicated to a specific aspect of mining operations: Operate, Automate, and Maintain.
ABB is developing new solutions every day to help operators address their top needs and to advance the mining industry through electrification, automation, and digitalization. The event showcased ABB’s innovative solutions designed to meet the evolving needs of the sector.
ABB highlighted its eMine portfolio, with solutions for the electrification of mining operations, in alignment with the industry’s shift towards sustainability.
The company demonstrated its cutting-edge automation and digitalization technologies designed to optimize mining operations. Internet of things (IoT) and artificial intelligence (AI) tools showcased how digital transformation can drive greater efficiencies and extend the equipment life.
ABB’s commitment to sustainability was evident in its focus on the transition from diesel to electric-powered mining and conveying equipment. This transition is crucial for reducing the environmental impact of mining activities and promoting a greener future. High-horsepower, low-voltage electric motors, medium voltage motors, and a range of low and medium voltage drives were on display facilitating conversations around sustainable mining.
ABB’s booth was a hub of activity, with global experts discussing the company’s solutions and providing insights into how technologies can address the unique challenges faced by mining operators. Collaborations with other industry players, such as Komatsu, further highlight ABB’s dedication to driving innovation and sustainability in mining.
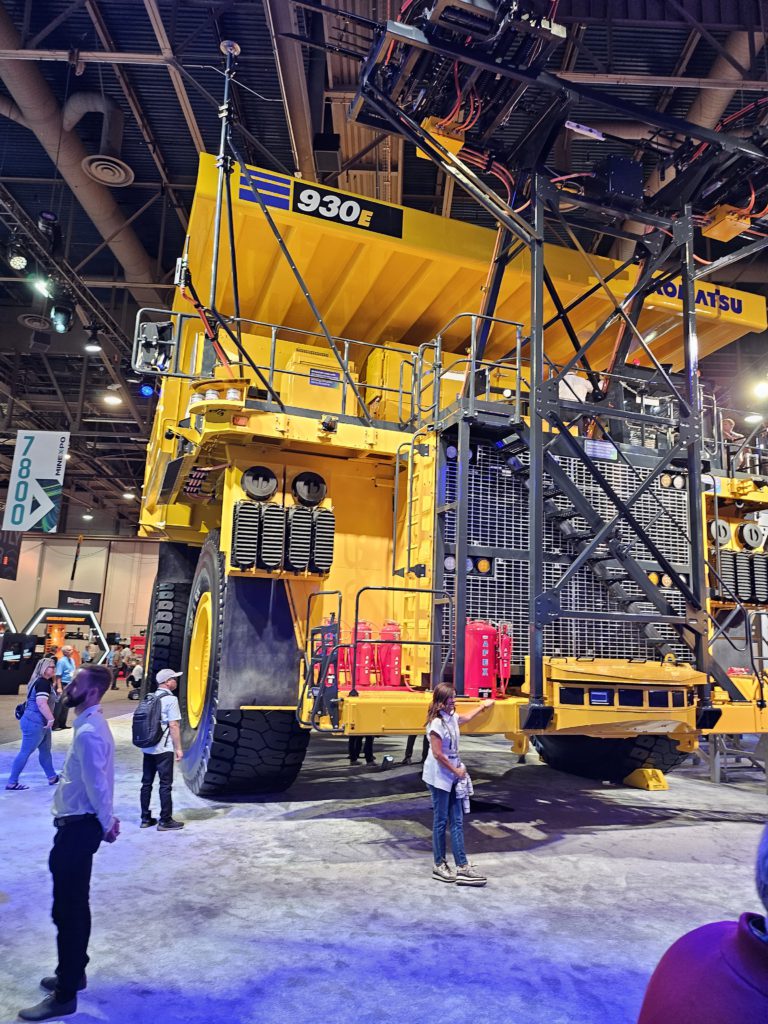
Komatsu’s show theme was “A sustainable future together.” Komatsu featured equipment, technology, and service solutions that address sustainability and electrification, surface mining, underground hard rock mining, underground soft rocking mining, blasthole drilling, quarry and aggregate mining, and crushing.
The “biggest” equipment in display was the first commercialized truck in the new Power Agnostic series, the Power Agnostic 930E truck. This cutting-edge haulage truck represents a significant milestone in Komatsu’s decarbonization strategy, offering unparalleled flexibility for mining operations transitioning toward zero emissions. The 930E sets a new standard in mining equipment by accommodating a wide range of current and future power sources, including diesel, battery, and even hydrogen fuel cells.
The 930E is built on Komatsu’s modular power-agnostic platform, allowing customers to future-proof their operations with a versatile approach to decarbonization. This platform enables mining companies to start with conventional diesel engines and gradually transition to cleaner energy sources as needed, including utilization of trolley assist for diesel or as one of the future dynamic charging solutions for battery trucks to reduce fuel consumption and emissions.
Komatsu also debuted the WX15 Load-Haul-Dump and the HX45 mining trucks, marking a major milestone in their underground mining journey. These machines were developed with expertise from Komatsu’s recent GHH acquisition.
Haver & Boecker Niagara featured its latest screening equipment and technology at MINExpo 2024. The company showcased a full-size Niagara F-class vibrating screen, along with other mining solutions. CMJ interviewed Karen Thompson, president of North American and Australian operations at Haver & Boecker Niagara.
“MINExpo presents an exciting opportunity to have great conversations with mining industry members, and for both new and existing customers to see our mineral processing equipment up close,” said Thompson. “We are proud to be known not just as an equipment manufacturer to our customers, but as a partner with innovative end-to-end solutions to improve their operation,” she added.
The Niagara F-class vibrating screen is designed with new technology to simplify maintenance. This next-generation screen is now primarily built using vibration-resistant lockbolts instead of traditional welding, enhancing structural integrity and making maintenance more efficient and cost-effective. Lockbolts secure the bar rails to the cross beams, allowing for easy replacement if they wear out.
Also displayed were Niagara exciters, their signature brand of vibrating screen exciters, known for their durability and reduced maintenance. Additionally, the company presented its Pulse Diagnostics Portfolio, a suite of tools that monitors the health of vibrating screens to identify issues before they become critical.
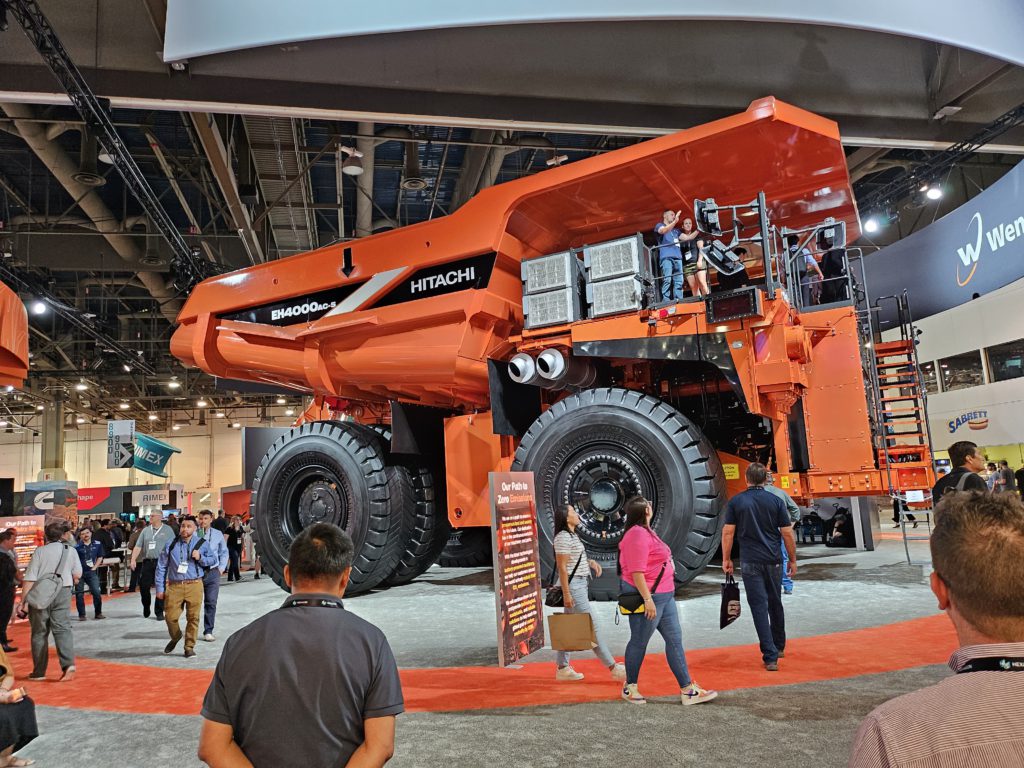
Hitachi Construction Machinery Americas highlighted the latest advancements and solutions designed to revolutionize the mining industry and demonstrated how their innovative technologies and reliable solutions are contributing to the realization of a safe and sustainable society. Hitachi Construction Machinery has been innovating electric technology and solving customer problems for more than 70 years. However, their electrification journey began in 1910 when the founder of Hitachi Limited designed a five-horsepower electric induction motor. Today, they continue to push the boundaries of innovation, developing products and solutions that help customers actively reduce CO2 emissions.
One of the standout innovations is the Hitachi Construction Machinery AC-3 truck, which allows operators to switch seamlessly between diesel mode to an optional trolley mode. In trolley mode, the truck is powered via an overhead catenary line, reducing emissions, and enhancing efficiency.
This system enables large, electrically powered dump trucks to draw power from overhead trolley lines on uphill roads and run on batteries in areas without overhead lines. Trucks with this configuration can achieve approximately twice the speed of diesel trucks on uphill slopes when in trolley mode.
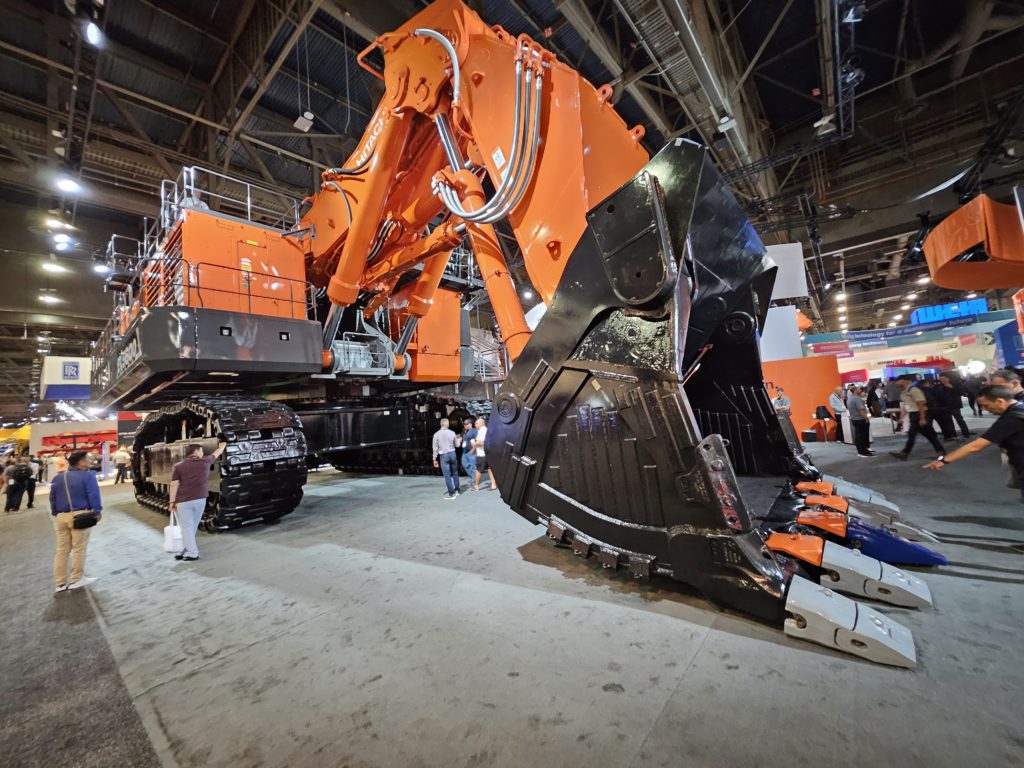
Adding to their suite of environmentally friendly machinery is Hitachi Construction Machinery’s EX-7 electric excavator. These machines offer numerous benefits over their diesel variants, not only helping reduce CO2 emissions, but also eliminating the need for consumables like fuel, engine oils, and disposable oil filters. the Power Agnostic 930E truck. represents a significant step towards sustainable mining operations reducing both operational costs and environmental impact.
A highlight of Hitachi’s presentation was their Autonomous Haulage System (AHS). This system combines advanced technologies with Wenco International Mining System’s fleet management system (FMS) to enable unmanned operation at open-cut mines, optimizing both efficiency and safety.
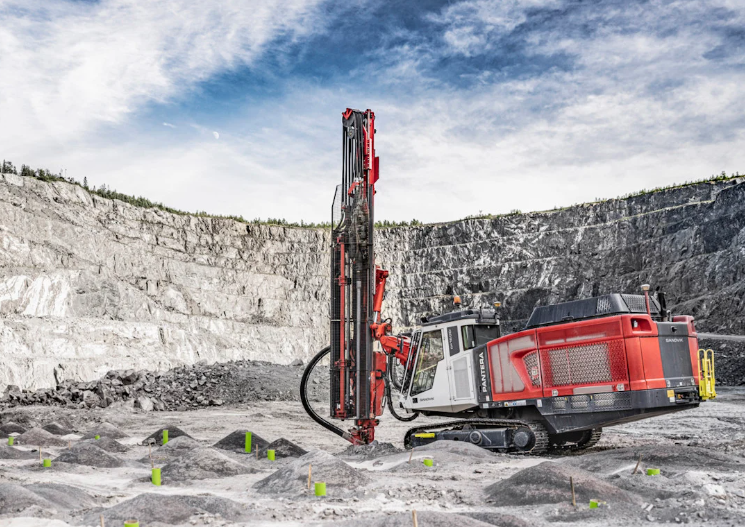
Sandvik Mining and Rock Solutions showed off the updated Pantera DP1510i drill rig for a hole diameter range of 89 to 152 mm. While the rig redesign covered all its key components, the heart of the new rig is a new, more powerful rock drill with 15% more efficient conversion of hydraulic power to percussion energy, translating directly either to lower fuel consumption or higher penetration rate.
The updated Pantera DP1510i also makes the operator’s life easier with advanced digital solutions: the RockPulse system to ensure optimized drill bit response, increased tool life, and feed level adjustment; the iClean option to provide an easy automated drilling sequence through the overburden; and feed-to-tram automatics to enable fast and easy transition from the drilling position to tramming position with a single button push.
Another innovation displayed at Sandvik’s booth was its new battery-electric concept surface drill rig — a testament to the company’s mission to gear its value chain towards net-zero emissions.The new battery-electric concept surface drill rig is set to accelerate decarbonization efforts in surface mining. The first in its size class, the BEV can drill holes up to 229 mm in diameter with its DTH hammer and seamlessly blends the autonomy of battery operation with the continuous endurance of a power cable. The battery pack lasts up to one hour of drilling or up to seven hours of tramming. The battery is primarily intended for tramming and drilling individual holes, while the bulk of production relies on power supply via more than 180 metres of tethered cable. Battery operation means more freedom and flexibility, and higher utilization rates, as the rig can start drilling immediately while the cable is being set up.
The Leopard DI650i Gen2, an even more autonomous and connected “diesel-powered,” self-contained, and crawler-mounted rig for a hole diameter range of 115 to 229 mm, was also launched. This rig features a new MicroFeed system for unprecedented accuracy in feed control. The precise control of the feed force and feed speed will often make a floating sub between the drill string and the rotary head unnecessary. The new rig also includes a new breakout table to eliminate dirt accumulation problems for easier pipe changes and better serviceability.
Orica showcased a range of cutting-edge solutions across its four key verticals from Orica digital solutions, mining, quarry and construction, and specialty mining chemicals. A major highlight was the TREAD MMU truck, showcasing the best in technology with a BlastIQ and 4D enabled Mobile Manufacturing Unit. The revolutionary 4D bulk explosives system matches a wider range of explosives energy to changes in geology in real time, offering unprecedented flexibility and efficiency in blasting operations.
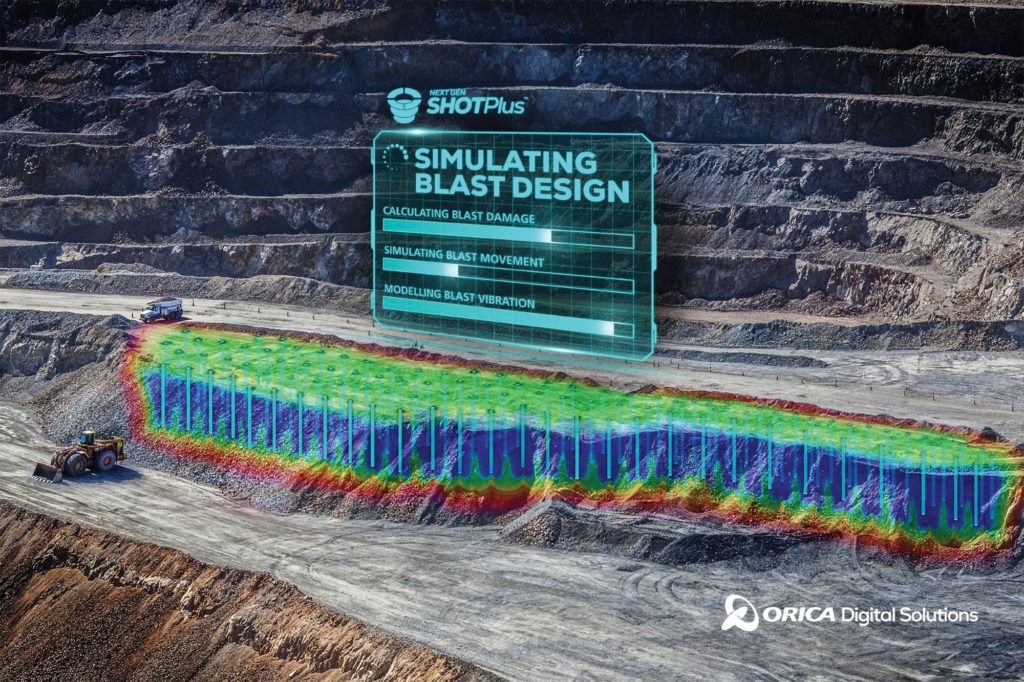
In other surface and underground blasting technologies, Orica displayed WebGen, the world’s first wireless initiating system. Revolutionizing mining, WebGen Wireless primers have been the catalyst of many innovative mining techniques improving safety, boosting productivity, maximising blast flexibility, and reducing mining complexities of blasting in sensitive areas or close to communities.
Orica Digital Solutions offered “Orebody Intelligence” with Axis Mining Technology, enabling customers to gain accurate insights into their orebodies from the outset, leading to informed decision-making throughout the value chain.
For blast design and execution, OREPro 3D software application predictively models blast movement without hardware or surveys, enabling iterative blast design for outcomes and improved grade control. SHOTPlus is a highly performant and intelligent blast design product for surface and underground operations. The application is the centre point for drill and blast decision-making.
Cummins shared how Bridge Technologies close the gap between what is practical and possible. Bridge Technologies will be used to support the mining industry’s energy transition. Speaking at MINExpo 2024, Molly Puga, executive director of strategy, digital, and product planning, highlighted that the global need to reduce emissions in mining will be achieved most effectively with the support of power solutions that can be implemented today, with a low total cost of ownership (TCO) and a high level of performance for miners.
Cummins anticipates that the mining industry will need multiple power technology solutions for the foreseeable future. The energy transition in mining will be driven by the availability of solutions that help achieve TCO parity or improvement, combined with the ability to meet varied Environment Sustainability Goals in operation. Whilst longer term, zero-emission technologies — such as full battery-electric solutions and hydrogen — have exciting potential, a lack of infrastructure availability, high upfront costs and performance of current equipment limits how effective this technology can be over the coming years.
Puga elaborated that Cummins will continue to invest in its internal combustion engine range whilst advancing its Destination Zero strategy for mining, which includes further development of two bridge pathways — hybrid and clean fuel capabilities. Both technologies provide fuel savings and emissions reductions from well-to-wheel.
Throughout MINExpo, Cummins also showcased the company’s commitment to advancing internal combustion technology, which serves as the base for both Bridge pathways in development. Visitors were able to explore Cummins’ latest power solutions, including the QSK60 and QSK95 engines.
Attendees also had the opportunity to see Cummins’ PrevenTech digital solutions in action.
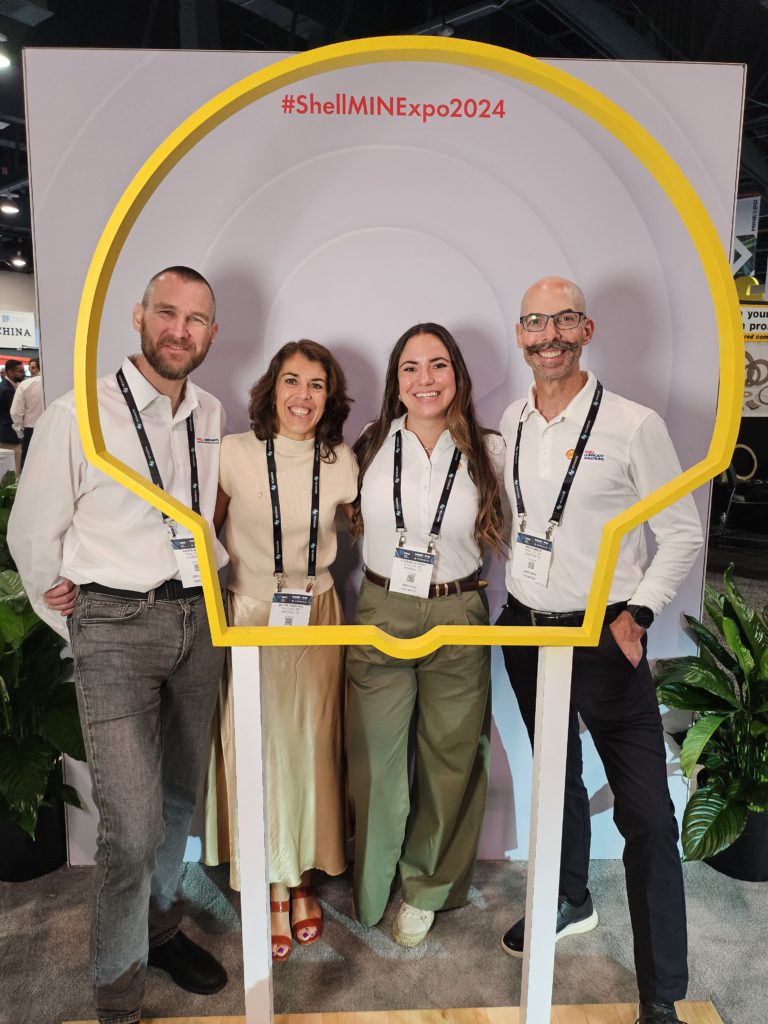
Shell Lubricant Solutions experts were available at MINExpo to discuss the products and services offered by both. They spoke about many industry topics, including the role of lubrication in a smart mine ecosystem, challenges miners are facing, and how advanced lubricants drive operational efficiency and sustainability.
Shell is leading the way with cutting-edge lubricants that boost miners’ productivity, reduce operational costs, and align with the industry’s growing focus on sustainability. This includes the immediate and long-term benefits of using high-performing lubricants, showcasing how they contribute to both financial savings and environmental goals for mining companies. Miners must operate more sustainably while lowering the total cost of ownership, which means improving operational efficiency. Shell’s high-performance lubricants increase the productivity of equipment operations. An essential part of mining operations is using the right services to ensure equipment reliability. Shell services for mining include Shell LubeExpert, Shell LubeAnalyst, Shell RemoteSense and more.
Mining tire innovations
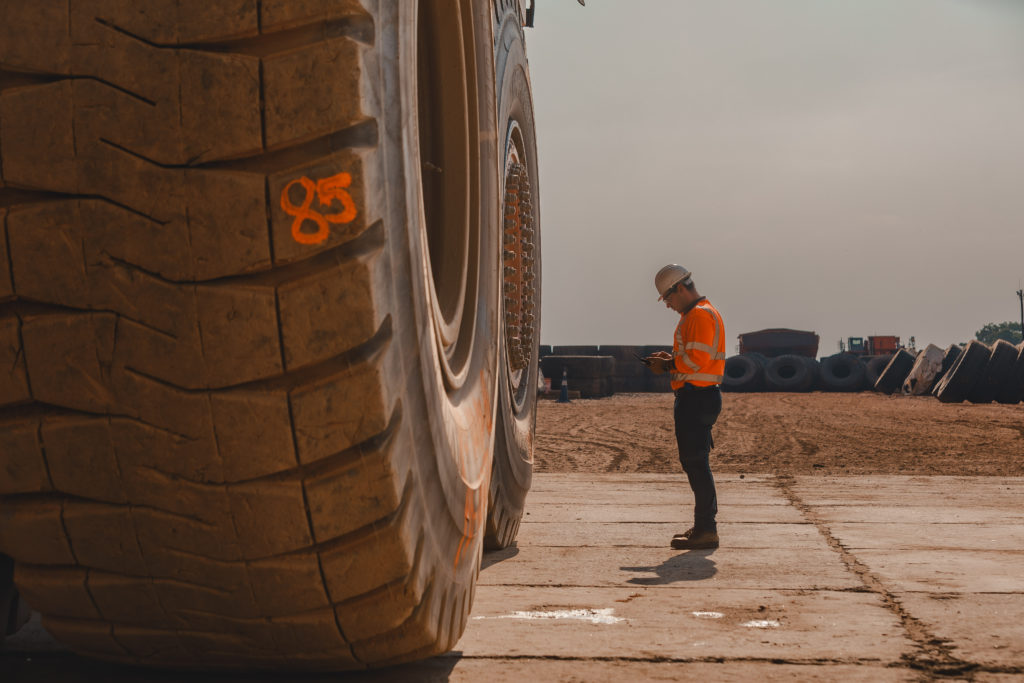
Michelin revealed two groundbreaking solutions during MINExpo 2024 that are set to advance safe, smart, and sustainable mining, including the industry’s first-ever energy-efficient tire: MICHELIN XDR 4 SPEED ENERGY (see also Liehberr’s section above), a tire that enables rigid dump trucks to use less energy thanks to an optimized, more flexible tread and a new energy-saving rubber compound, and MICHELIN BETTER HAUL ROAD, a digital solution to optimize haul road maintenance at mine sites. Known worldwide for on and off-road tires, Michelin created the Better Haul Road, a digital solution designed to enhance safety and efficiency in mining operations. The solution was developed with the collaboration of three mines around the world.
Michelin Better Haul Road provides a solution that allows mine managers to keep a close eye on these critical infrastructures. By monitoring haul roads in real time, operators can swiftly identify incidents such as debris or road damage that may arise. The system then allows them to register the issue within the app or through dispatch with the web, track its status via the app or web, and efficiently assign a repair team to address and resolve the problem.
Better Haul Road allows prioritization of data-driven actions and supports a mine’s constant pit evolution with cleaner haul road conditions.
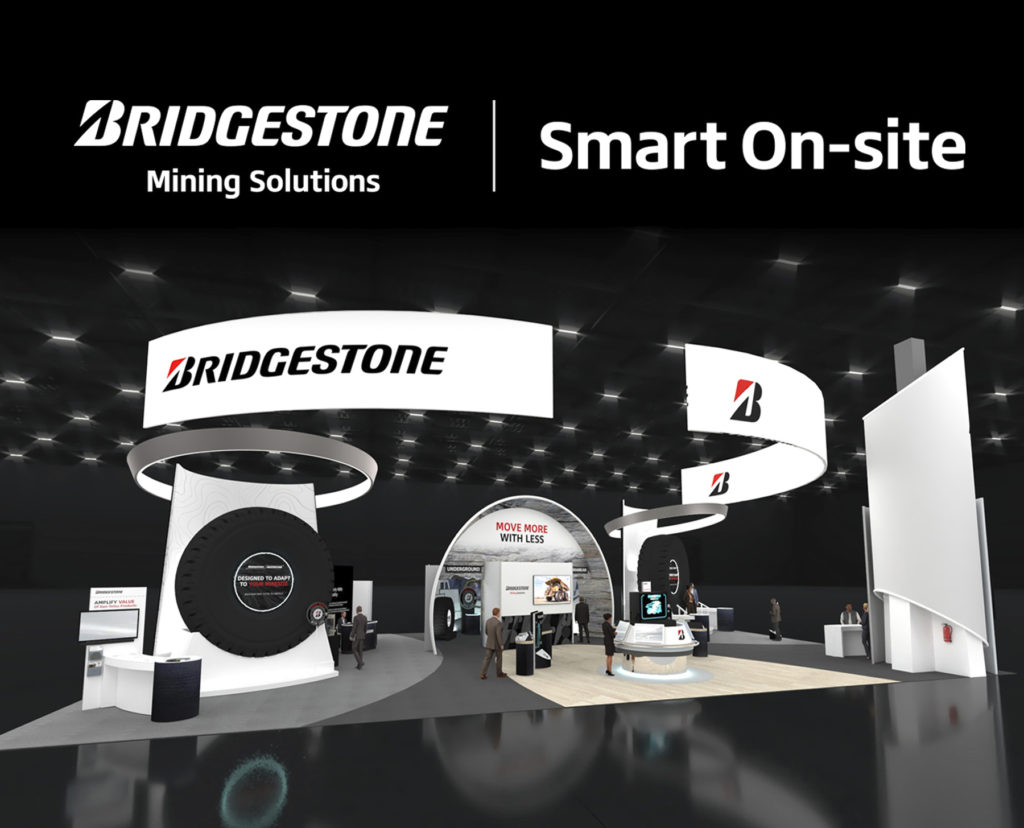
Bridgestone. The Bridgestone booth showcased the company’s new “Smart On-site” program, a seamless, customizable solution for fleets that combines premium tire products, mobility solutions, and industry-leading service into a single package. By developing a comprehensive approach to mining operations, Bridgestone can offer enhanced connectivity and optimized performance for customers. Smart On-site programs were co-created with customers and utilized the latest operational data to establish a one-of-a-kind suite of solutions for each customer to address pain points. This comprehensive approach enables operators to work optimally and leverage real-time and historical data insights to continuously improve. Smart On-site is the latest example of Bridgestone’s commitment to enhancing the mining industry with modern technologies and data-driven insights.
Bridgestone OTR also presented the following:
- The new V-Steel Mining Smooth Tread (VMMS) and V-Steel Mining D-Lug (VMDL), two innovative tires designed with subterranean technology for the underground hard rock segment.
- Additional intelligent products, including the new Firestone SRG DT LD 2, one of the company’s largest tire products for the surface mining segment.
- Integrated technologies like IntelliTire and Toolbox provide data-driven insights.
- Advanced on-site tools offered through Bridgestone Engineering Solutions.
Kal Tire showcased inspiring innovations at MINExpo. Those curious about some of the most-anticipated solutions developed by Kal Tire’s Mining Tire Group had the chance to experience the company’s innovations first-hand at MINExpo 2024. From autonomous tire inspections to a new post-recycling process that refines carbon ash, KalPRO innovations created a buzz among those exploring viable and impactful ways to enhance sustainability, safety, and productivity.
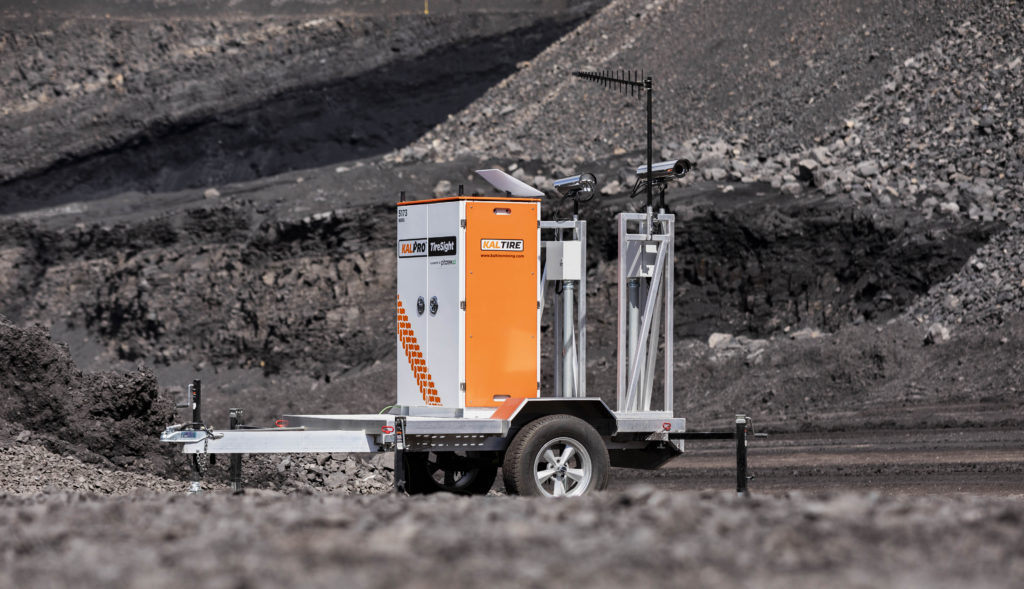
“Our journey into mining tire management innovation has allowed us to help customers reach goals in impactful ways, and it has also allowed us to make our work around the wheel safer,” says Dan Allan, senior vice president, Kal Tire’s Mining Tire Group.
One of those solutions is KalPRO WheelJaws, which eliminates risk during the last and most dangerous step during tire installation and removal. At MINExpo, people had a chance to see firsthand how WheelJaws’ secure, remote-controlled clamps take technicians out of the danger zone.
Today, WheelJaws is just one KalPRO solution among a collection of six tools and six unique offerings.
Kal Tire’s MINExpo visitors also had the chance to take in a virtual tour of its thermal conversion OTR tire recycling facility in Chile. The facility helps mines solve the challenge of scrap tires and promote a circular economy by making the best use of recycled rubber. Kal Tire also unveiled its new process that refines carbon ash to high grade recovered carbon black (rCB).
Mines looking to keep tires in production and divert scrap had the chance to learn more about Kal Tire’s newly expanded Maple Program. Customers who choose Kal Tire retreads and repairs receive a Maple Program certificate with verified data on the carbon and fuel emission savings compared to buying a new tire. Now, Maple Program includes all tire sizes from 25 inches and up, and customers now also receive the emissions saved in transportation from a regional repair facility or on site versus a distant new tire manufacturer.
Lastly, those interested in learning more about the company’s TireSight autonomous tire inspections got to view a demonstration of a mini haul truck passing by a thermal imaging camera before setting off a chain of automated events that ensure critical tire issues are caught and addressed early — enhancing safety, productivity, and tire life.
Comments