Sorting it out: Ore sorting gains traction
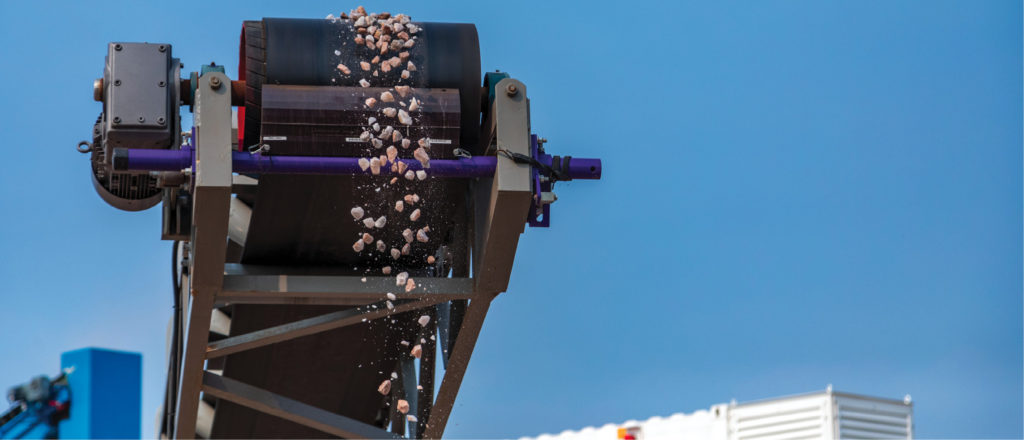
CREDIT: CHEETAH RESOURCES/BILLBRA DENPHOTO
Miners look to cut their environmental impact through ore sorting
When senior management of Vital Metals, an Australian company, went looking for rare earth deposits to develop, one of the deciding factors in their shortlisting exercise was each property’s suitability for particle ore sorting.
The Nechalacho project in the Northwest Territories met all of the company’s requirements. Aside from being a quality resource in a politically stable jurisdiction, test work confirmed that particle ore sorting using X-ray transmission sensors would be able to separate the quartz host rock from the bastnaesite ore.
Particle ore separation was important because of the technology’s ability to reduce Nechalacho’s footprint, says David Connelly, vice-president, government and corporate affairs of Cheetah Resources, Vital Metals subsidiary and operator of Nechalacho.
“In today’s world – and particularly when you are extracting resources for the green economy – you have to behave in an environmentally sound manner and sensor-based sorting has a much lower impact on the environment than other methods of beneficiation,” he said in an interview in August.
China’s control of the rare earth market and its history of dropping prices to squeeze out high and middle cost producers also drove the decision to go with an ore sorting solution.
“The previous developer of the property – Avalon Advanced Materials – based its bankable feasibility study on a traditional concentrator costing hundreds of millions of dollars,” said Connelly. Cheetah, which has only acquired Nechalacho’s near surface resource, opted for a simple open pit, seasonal mining operation with a footprint less than 5% of the size of a traditional concentrator and costing less than $12 million.
Cheetah began production at the small-scale operation this summer.
Crushed material at Nechalacho is introduced to the ore sorter via a conveyor belt and identified as either ore or waste by X-ray transmission sensors. The sorter maps the particles containing ore and engages selected air injectors to propel them into a separate ore stream.
There are no tailings, no chemicals, much less energy and water used, and the waste rock from the sorter can be used as aggregate for road building.
The high-grade bastnaesite product from the sorter will be shipped for further processing to Saskatoon and final separation into rare earth elements by REEtec in Norway.
Following the exhaustion of the near surface resource at Nechalacho, Cheetah plans to mine two recently acquired properties in Quebec using particle ore sorting technology.
Ore sorting was of great assistance in addressing the concerns that Indigenous groups had about the potential impact on the land and water, noted Connelly.
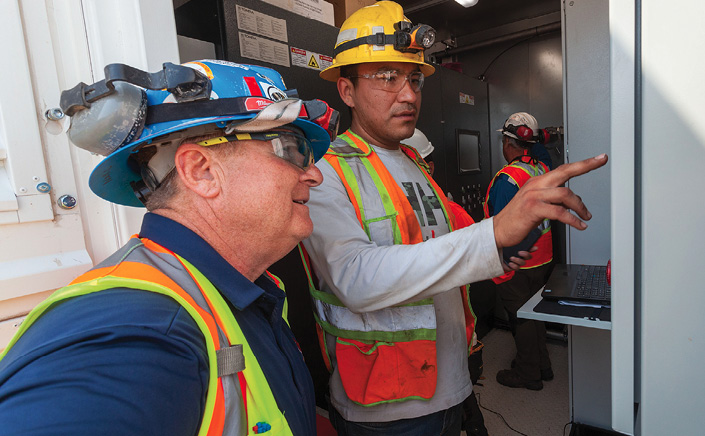
CREDIT: CHEETAH RESOURCES/BILLBRADENPHOTO
“In the Northwest Territories, you don’t even make it in front of the Mackenzie Valley Land and Water Board unless you satisfy all the concerns of the impacted First Nations.”
A TOMRA ore sorter was delivered to Nechalacho, 100 km southeast of Yellowknife over a 138-km ice road from Yellowknife in March. Mining began June 29th by the Det’on Cho Nahanni Construction Corp., owned by the Yellowknives Dene First Nation. The sorter itself is also operated by Indigenous personnel.
Mainstream acceptance
TOMRA Mining, a Norwegian company and market leader in particle ore sorting, says it has approximately 180 ore sorters deployed around the world, including close to 50 in North America.
According to Harold Cline, TOMRA’s area sales manager for TOMRA Mining, particle ore sorting is equally applicable for both greenfield and brownfield operations.
“There aren’t many greenfield projects that don’t at least consider ore sorting from the onset,” he said. “Even during exploration, we’re starting to get drill core to work with to see if there’s a possible sorting solution. We can also help with brownfield projects by sorting through old stockpiles when companies are running across life of mine problems and grades are getting low, so there are a lot of applications and I think it’s becoming much more mainstream.”
The mining industry’s acceptance of particle ore sorting is also being driven by engineering companies like Metso Outotec.
“Separating ore from waste rock as early and as efficiently as possible is essential in mineral processing,” said Guillaume Lambert, Metso Outotec’s vice-president, crushing. “The best result can be achieved by combining state-of-the-art crushing systems with advanced ore sorting. The combination of Metso Outotec’s crushing know-how and TOMRA’s particle ore sorting expertise is an excellent match, providing substantial benefits to our customers.”
Sensor-based sorting is well established in diamond mining operations, but is also being used for a wide range of other commodities, including rare earth elements, gold, tungsten, salt and phosphate.
“Gold is an interesting case because in some circumstances sorting can be very beneficial,” said Cline. “In other cases, we would point companies away from sorting. The onus is on us as the sorting vendor to demonstrate to the customer that we can achieve their objectives. Gold deposits are very complicated and even individual deposits vary, so we are very careful with our test work for gold.”
X-Ray transmission sorting
Ore sorters can’t easily identify gold bearing particles as they’re flying by the sensors because it’s often so disseminated. Instead, TOMRA relies on associations with quartz or pyrite mineralization. Metallurgical testing for Osisko Development’s Cariboo gold project in British Columbia, for example, has demonstrated that the mineralization can be effectively upgraded by flotation and X-Ray transmission ore sorting owing to the strong association of gold with pyrite.
X-Ray transmission sensors classify particles based on their specific atomic density and are used in 80% of TOMRA’s ore sorting applications, but several other sensors are also used to classify material based on their colour, near-infrared spectrum profile and conductivity. Laser sensors, which classify particles according to colour and pattern, are used in tandem to look at both sides of the rocks as they descend through a chute.
The test work for Cheetah Resources was performed at the Saskatchewan Research Council (SRC) in Saskatoon, which has been doing test work for ore sorting for many years and finally acquired its very own TOMRA ore sorter in January.
“Cheetah is a great example of ore sorting because the more waste rock you can get out prior to processing, the better,” said SRC business development manager Lucinda Wood.
TOMRA ore sorters can work with run of mine material as large as 25 cm in size to separate out obvious chunks of rock for further crushing. It can also work with particles as small as 1 mm in diameter.
One ore sorter was sufficient for Cheetah Resources, but some companies require multiple sorters to achieve the desired results.
Cost savings
Maaden Phosphates in Saudi Arabia operates the largest sorting plant in the world with nine TOMRA sorters, says Cline. “They use nine gigantic 2.4-metre wide sorters. Four are dedicated to working with small particle sizes. Three work with medium-size particles and a couple work with large particles.”
The Saudi Arabian operation reports that particle ore sorting allows it to use 45% less water. Its flotation plant is 40% smaller, its crushing and milling costs are significant lower – 75% and 45%, respectively – and it saves $10 million per year on reagents.
Bulk ore sorting, another sensor-based sorting technology, can also remove waste early in the process and is suitable for deposits of geological heterogeneity in which there are large areas of waste and other areas of disseminated ore, explained the SRC’s Wood.
“You can make sure that these large areas of waste don’t go to the plant, whereas in particle ore sorting, you’re seeing heterogeneity on a particle basis and removing waste from the mineralized ore on a particle level,” she explained.
HydroFloat
Eriez Manufacturing offers another ore sorting technology called HydroFloat, which employs a variation of flotation technology based on the use of coarser material and a liquid fluidized bed.
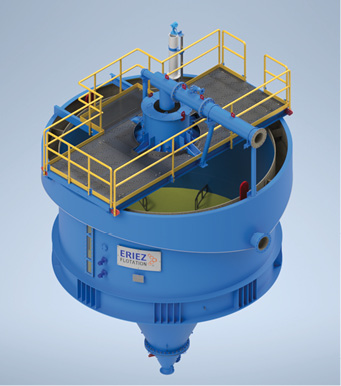
CREDIT: ERIEZ
“Conventional flotation has a fundamental limitation,” explains Eric Wasmund, vice-president, global flotation. “It only works in a certain size range, so if it’s too fine, it won’t float, or if it’s too coarse it won’t float.”
Wasmund says there’s a significant amount of ore that is not recovered. And from an environmental point of view, the extent of grinding is higher than it needs to be, which requires more energy and produces fine tails that are potentially geotechnically unstable for long-term storage. Using copper as a benchmark, Eriez has found that between 10-15% of mined copper goes through the entire flow sheet and ends up going to tails.
There are two coarse particle flotation (CPF) flow sheets where the HydroFloat is being used: tails scavenging and coarse gangue rejection. The former intercepts the material that would end up as waste, recovering up to half of the copper that would otherwise be lost.
Newcrest’s Cadia mine in New South Wales is using a HydroFloat tails scavenging solution and Anglo American’s Quellaveco greenfield copper operation now under construction in Peru will be deploying it to treat 100% of the concentrator tails.
Waste material of 500 to 600 microns –
the size of beach sand – is much easier to dewater than slimes containing much finer particles, and also it is more stable. This allows mining operations to recover the water and have dry tailings that are geotechnically stable and safer.
“There are parts of the world like the Atacama desert in Chile where water resources are very limited, so being able to recycle the water is a huge advantage,” said Wasmund.
The coarse gangue rejection flow sheet removes coarse gangue instead of sending it to conventional flotation, so that is how it is akin to an ore sorting technology.
“Using a fluidized bed you can float something that is twice the size, so instead of grinding so fine, we can grind it coarse,” Wasmund says.
The very coarse ore will be recovered. What’s left is waste and bypasses the rest of the concentrator, being rejected at a coarse size of 500 to 600 microns, he says.
“The material that goes to conventional flotation is greatly reduced because you’ve removed thirty to forty per cent of it at an early stage.”
Eriez has more than 70 installed commercial-scale HydroFloat deployments around the world and is in engineering and piloting stages for 10 large scale copper projects, each of which would have at least six units.
Each of the ore sorting options currently available can contribute to reducing the deleterious impacts of mining on the environment, facilitating social licence to operate and certifying companies as compliant with environmental, social and governance (ESG) standards.
“We know there’s an increasing demand for metals to build out the backbone of the new green economy,” said Wasmund. To be seen as part of this economy, “the mining industry has to be serious about finding ways to extract these metals more responsibly and efficiently.”
Norm Tollinsky is a freelance journalist and former editor of Sudbury Mining Solutions Journal.
Comments