Shaking up safety culture
At a recent crew change heading up to Kennady Diamond’s Kelvin camp northeast of Yellowknife, a dozen or so geologists, camp workers and a cook milled around the loading bay at the Air Tindi hangar.
Pallets of fresh food and carts piled with duffle bags crowded the floor while a small fork lift jockeyed about, preparing to load the Dash 7 warming up outside.
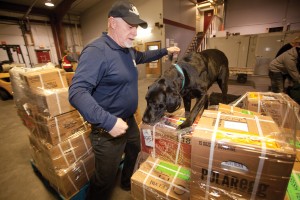
Dog-handler Mark Hicks leading a black Labrador retriever named OD (short for Over Dose) through his paces, sniffing luggage and freight for drugs and alcohol before the cargo flight heads north. (Bill Braden photo).
But before anything or anybody went aboard, a rambunctious, outrageously friendly Black Labrador Retriever named OD – short for OverDose – had a very serious job to do. His astonishingly sensitive nose quickly and thoroughly sniffed every box, bag and person to make sure they were clean of alcohol or illicit drugs.
OD and his easy-going handler, Mark Hicks of North of Sixty K-9 Services, were not there to find bad guys and turn them over to police. Rather, they are among the leading innovations that companies are using to foster a paradigm shift in values and attitudes around health and safety in the mining industry.
Benefits are Immediate
“The kind of behaviour about drugs or alcohol that was accepted 20 years ago in exploration camps is not tolerated today,” says Hicks, a retired RCMP staff sergeant with two decades of canine security experience. “I created the first canine company in Canada [in 2011] to do this from a health and safety perspective.”
His business strategy is simple: A well-trained dog, a skilled handler, and good policy will help companies and workers stay safe.
“At first it wasn’t met with open arms,” Hicks says. He had to overcome skepticism that if the dog did find bad stuff, there would be retribution against the employee. Here’s where the innovation comes it: Hicks works with clients across Canada to write their drug and alcohol policies to avoid threat or punishment, and open the door to helping a worker change behaviour and overcome substance problems.
“You get everybody together, explain what you want to do, and get buy-in,” he explains. And, if an employee makes a mistake and gets caught, it’s not the end. “There’s a grace period. You want to give them a chance to change.”
Aurora Geosciences of Yellowknife provides full program management for Kennady Diamonds at their Kennady North project. This past winter season, up to 60 drillers, geologists and camp support workers were on site, and that could grow to over 200 later this year.
Darrell Matchett, Aurora Geosciences Ltd. Safety Officer, brought NOS K-9 into the Kennady program late in 2014. “Even though the big mines have zero tolerance, this type of program at the exploration stage of the game is one of the most important steps to promote that.”
“It has to be driven from the top,” Hicks stresses. “The benefits are immediate… the savings in HR, in turnover, insurance, WCB premiums, and retention of good employees.”
Back at the airport hangar, the crew obviously respects the job Hicks is doing. They’re also quite fond of the gregarious OD, taking the test with considerable good humour and teasing if they’re outed. That signal comes when OD ‘sits’ at any bag or person he sniffs with a suspicious scent. That’s the cue for the bag to be searched or the person questioned.
Aurora has also employed Hicks to search aircraft, helicopters and the entire campsite, and yes, they have found stuff. But after a year in practice, Matchett says the program has been a huge success, and the incidence of real problems is now negligible.
Just how sensitive is OD’s shiny wet nose? It will easily pick up sealed medications, boozy breath from last night’s libations, or a trace of that joint smoked a few days ago. During a demonstration at one office, he nosed out an empty whisky bottle, forgotten for months in a storage box after last year’s Christmas party.
Growing a Culture of Safety
In interviews with lead safety managers from the North’s Triple D of diamond miners – De Beers, Diavik and Dominion – the values and culture of safety consistently come up.
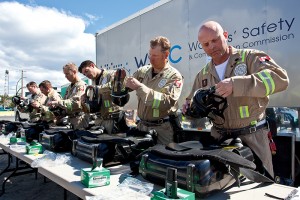
Mines across Canada invest heavily in training mine rescue teams as part of their mine safety programs. (Bill Braden photo)
“It’s changed tremendously in the past eight years,” says Doug Brown, Health and Safety Manager for De Beers Canada. “Gone is the attitude that it’s acceptable to get hurt, or contract any type of industrial disease or illness. It’s been quite a journey, to get people to believe in the possibility that no injuries can really occur.
“It’s been demonstrated in the Victor mine’s excellent safety records over its eight year life,” said Brown. “Part of the reason for that is the culture that’s in place there, and across all three De Beers sites in Canada.”
“Each employee owns safety. It’s not owned by or policed by the safety division – it’s embedded into each employee’s own responsibilities,” he says.
Brown says good safety practice is even crossing into employees’ homes and communities. It’s a culture that’s firmly embedded at the top corporate level, says Tom Ormsby, Head of External and Corporate Affairs at De Beers Canada.
“Without [the involvement of leadership] people would see it won’t need to apply to them. We’ve had to make it real.
We don’t want to just be compliant. We have to be ahead of where we see any potential harm.”
De Beers’ first measure of performance – ahead of tonnes or carats or budgets – is safety. Incentive rewards for all performance matrix can be as high as 25% of salary. Cash bonuses are paid to employees quarterly, while managements is assessed twice a year and paid annually.
De Beers has moved beyond the typical lost-time accident reporting standard to its own Total Recordable Case Frequency (TRCF)matrix. It covers all incidents, including minor medical aid. The Victor mine in Northern Ontario is in the running for this year’s eastern division John T. Ryan trophy – Canada’s top award for safety achievement – with an impressive TRCF of only one medical aid incident and zero lost-time events in 2015.
The Diavik Diamond Mine, owned 60 per cent by international miner Rio Tinto, is in the early stages of rolling out Rio’s world-wide safety campaign labelled CRM – Critical Risk Management. It’ll take about two years to fully implement from the top down, says Steve Bourn, Diavik’s Manager of Health, Safety and Environment.
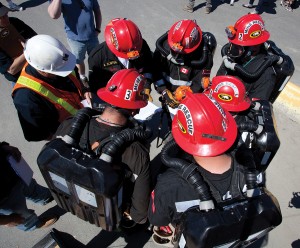
A mine rescue team huddles for a safety briefing at Dominion Diamond’s Ekati mine. (Dominion Diamond Corporation photo)
CRM uses years of Rio Tinto and mining data on what can cause serious accidents or fatalities to standardize the checklists and practices that crews will apply to critical tasks, every day.
“A lot of that already happens, but this standardizes it,” says Bourn. Diavik’s bonus program for operational crews is tied directly to safety along with production and financial performance, awarded monthly, “so rather than waiting ‘til the end of the year, it’s reset every month.”
Bourn says they get upwards of 15 suggestions a month in Diavik’s peer-to-peer recognition program, where workers nominate each other as “unsung heroes” for following and promoting safe practice. Its rewards might not be big – a jacket or a travel bag – but the value of peer-to-peer recognition is what counts.
Bourn is also responsible for Emergency Response Teams at the 1,000-plus employee diamond mine. To cover for shift rotations and maintain experience, Diavik keeps its ERT squad at between 65 and 80, investing three days in every two week rotation in training.
“We definitely promote it with a lot of pride. There’s benefits for the guys and girls on the team, they’re getting a lot of world class training that they’ll be able to take with them the rest of their life. Lots of them are volunteer firefighters back home, and the camaraderie among each other is unreal.”
Elite ERT members serve on Diavik’s mine rescue competition team, dedicating weeks to intensive training before annual competitions in Yellowknife. And along with De Beers, Dominion and Agnico Eagle mines, a mutual aid protocol pledges support in the event of a large-scale emergency. Annual joint rescue exercises have also been staged over the past three years, and Bourn anticipates that T-Mac Resources, Baffinland Iron and Giant Mine will also sign on.
“For Dominion Diamond, safety is a value rather than a priority,” says Chantal Lavoie, President of Dominion Diamond Ekati Corporation. “In order to shift our safety culture in a new direction, Dominion Diamond is implementing a behavioral-based safety program called the Zero Incident Process (ZIP).”
Taught by industrial psychologists, the program aims to change the way people think about safety. By giving employees the tools to take control of their thoughts and feelings, they will learn how to make the proper choices as they pertain to safety, says Lavoie in an email.
Noting that most injuries happen at home, Dominion hopes that employees and contractors will take ZIP’s learning and apply it to all facets of their lives.
Dominion has also shown safety leadership as the NWT’s first COR-certified diamond mine, awarded in 2015. It’s a national certification that demands compliance with a tough set of standards for safety practice and protocol. Dominion’s mine rescue team has done the company proud as the overall underground winner in 2015 at the 12th Biennial National Western Regional Mine Rescue Competition in Fernie, BC. And earlier this year, the company’s Jay Pipe expansion project marked 300,000 hours without a single recordable injury, earning Dominion accolades from the Association for Mineral Exploration BC.
Comments