Searching for safety: Boost safety and efficiency in quarries with diagnostic tools
A vibrating screen is the heart of a quarry. It is the deciding factor in whether or not your product meets your specifications. Deadlines and quotas might tempt producers to overload the screen while attempting to increase their bottom line. However, this contributes to downtime due to premature wear and might create a safety hazard for workers near an unbalanced screen. And just as monitoring a heart rate is essential for optimal health, the same idea applies to a quarry operation.
Think of manufacturers as an operation’s cardiologist, there to diagnose and remedy operating issues before they become a safety hazard or halt production altogether. They provide producers with the necessities to streamline an operation and minimize downtime or injury. And these days, that starts with diagnostics.
Like a house-call from a doctor, onsite diagnostics enhance aggregate operations through vibration analysis service programs without having to transport the equipment into a shop. These programs offer producers insight on their screen’s performance to achieve optimum efficiency and ensure minor operating issues do not become major hazards. For the first time ever, manufacturers’ service programs provide producers the opportunity to monitor screening performance in real time. And recently, some manufacturers advanced these systems by using wireless technology. These advancements offer a hands-off approach to analyzing screening equipment by allowing operators to stand out of harm’s way from a potentially off-balanced screen when performing diagnostics.
In addition to safety, wireless technology offers operators remote, real-time monitoring, which ensures equipment is properly maintained and running optimally. This means less risk that strain is placed on the screen or other parts of the operation to maintain production quota. The increased efficiency and enhanced safety are the healthy choice for all areas of the operation.
Does it sound interesting? Here is how it works
It all begins with a close relationship with the OEM (original equipment manufacturer) and is enhanced by real-time equipment monitoring. Finding a key partnership where an OEM approaches the application as a solution provider rather than an equipment supplier is key to productivity and success. If your OEM is not providing consultative advice and real-time, proactive monitoring, it might be time to seek another solution.
A key aspect to safety is having equipment that runs at peak performance and knowing when and how to maintain it. The more time spent fixing and maintaining the equipment heightens the risk of injury. That is where real-time monitoring comes in handy.
An advanced vibration analysis program specifically monitors the health of vibrating screens. That real-time feedback ensures optimized screen performance and equipment durability. The hands-free system uses a wireless, industrial-grade tablet computer and eight tri-axial sensors to detect abnormalities the human eye cannot, such as a hairline crack in a side plate or an uneven or twisting motion. Even the slightest irregularities can result in diminished performance, decreased efficiency, and safety risk for the operator.
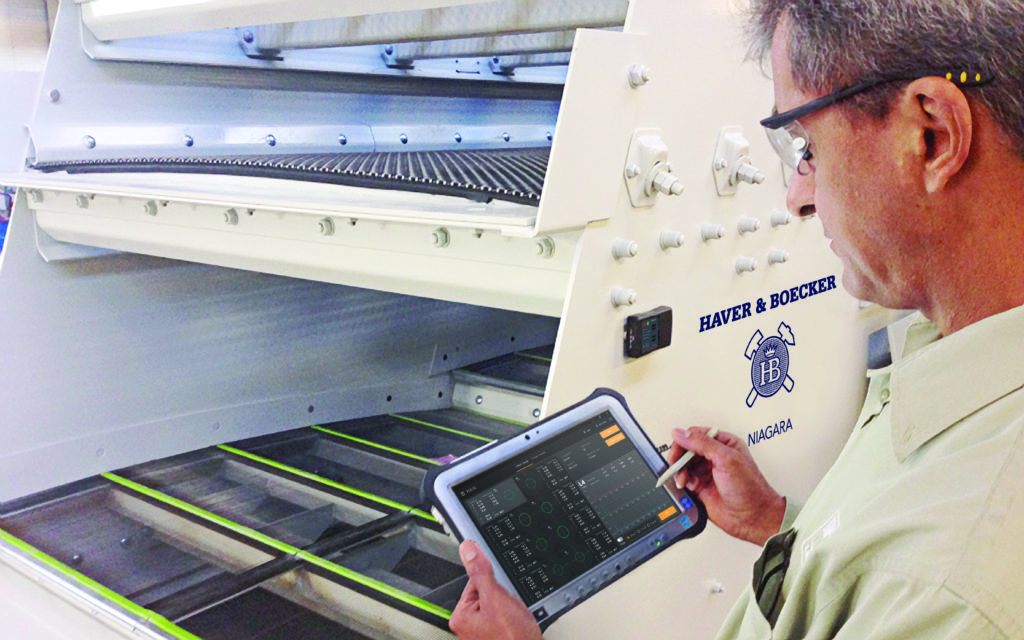
Credit: Haver & Boecker Niagara
The programs use wireless accelerometers to detect any irregularities, allowing operators to stand as far as 100 metres out of harm’s way. Each sensor attaches to key places on a machine to send 24 channels of data to the tablet via Wi-Fi, illustrating the machine’s orbit, acceleration, deviations, and more.
After the sensors record the data, trained and experienced engineers review, study, and interpret the results through the system’s database. This provides the engineers and producer with a detailed report of any concerns that might diminish productivity or risk operator safety. If an irregularity is detected, the service team travels to complete onsite service, which keeps producers on top of preventative maintenance and ensures a safe operation that runs at maximum efficiency and lower risk. Some vibration analysis systems store each machine’s historical data, which allows for quick comparison over time and easy troubleshooting.
Increasingly often, producers rely on diagnostics for safer work environments and a streamlined operation. Its hands-off approach offers aggregate producers a healthy operation, running at peak performance, which helps them efficiently meet deadlines and produce quality products for their customers. CMJ
Wilm Schulz is Haver & Boecker Niagara parts and service manager.
Comments