Seafloor mining takes a unique set of skills
When it comes to shipping heavy equipment to a mining location, few companies know more about the challenges of getting machinery to a site than Nautilus Minerals Inc., of Toronto.
In fact, it’s safe to say that Nautilus Minerals is a leader in this category when you take into consideration that it is reportedly the first company to commercially explore the seafloor for massive sulphide systems, a potential source of high-grade copper, gold, zinc and silver.
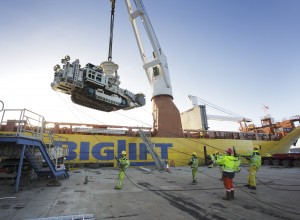
One of the seafloor production tools loading onto the ship.
Nautilus is developing a production system using existing technologies adapted from the offshore oil and gas industry, dredging, and mining industries to enable the extraction of these high-grade Seafloor Massive Sulphide (“SMS”) systems on a commercial scale.
Nautilus’ copper-gold project, Solwara 1, is under development in the territorial waters of Papua New Guinea. The company has been granted the Environment Permit and Mining Lease required for resource development at this site.
With that secured, Nautilus now plans to extend its tenement holdings in the exclusive economic zones and territorial waters of Papua New Guinea, Fiji, Tonga, the Solomon Islands, Vanuatu and New Zealand as well as other areas outside the Western Pacific.
Papua New Guinea
In 1985, SMS and hydrothermal sulphide systems were discovered in the territorial waters of Papua New Guinea (PNG) by the research vessel the RV Moana Wave at a site that later became known as the Solwara 2 Prospect.
The late 1980s and 1990s saw numerous research projects undertaken. PNG was the first country in the world to grant commercial exploration licenses for such SMS systems when, in 1997, Nautilus’s first tenement, EL1196, was granted.
In March 2007, it launched the world’s largest commercial exploration program for high-grade SMS systems. This program included extensive environmental studies, resource definition drilling, sampling and related metallurgical and production development studies on Solwara 1.
A successful exploration year culminated with the release of a NI 43-101 resource estimate for a portion of Solwara 1.
Following several more exploration and drilling campaigns, the initial resource estimate was updated in 2011 with the addition of a maiden resource estimate for nearby Solwara 2.
Solwara 1
The Solwara 1 Field was first identified by Australia’s Commonwealth Scientific and Industrial Research Organisation (CSIRO) in 1996.
Extensive research campaigns between 1993 and 1997 formed the base line knowledge for what would become more intensive commercial development activities. Solwara, means “salt water” in Tok Pisin.
Since 2006, Nautilus has used the term ‘Solwara’ to describe its PNG exploration projects and prospects during its reconnaissance and drilling campaigns.
Nautilus was granted its first Mining Lease in January 2011 for Solwara 1, and the Environmental Permit for Solwara 1 was awarded in December 2009.
The Solwara 1 deposit, which sits on the seafloor at a water depth of some 1600 metres, contains a copper grade of approximately 7%. That compares with land-based copper mines, where the copper grade today averages 0.6%.
In addition, gold grades of well over 20 g/tonne have been recorded in some intercepts at Solwara 1 and the average grade is approximately 6 g/tonne.
Technology Overview
Nautilus Minerals is utilising proven technologies from the offshore oil and gas industries, dredging and onshore mining industries to realise the new deep seafloor resource production industry. The result is a system which has three main components: the Seafloor Production Tools (SPTs) the Riser and Lifting System (RALS) and the Production Support Vessel (PSV).
The excavation and collection has been split into three individual tasks which will each be carried out by a different vehicle. The Auxiliary Cutter is designed as the pioneering machine which prepares the rugged sea bed for the more powerful Bulk Cutter(BC).
These two machines gather the excavated material; the third vehicle, the Collecting Machine will collect the cut material by drawing it in as seawater slurry with internal pumps and pushing it through a flexible pipe to the subsea pump and on to the PSV via a riser system.
On deck of the Production Support Vessel (PSV), the slurry is dewatered.
The dewatered solid material is stored temporarily in the PSV’s hull, and then discharged to a transportation vessel moored alongside. Filtered seawater is pumped back to the seafloor through the riser pipes and provides hydraulic power to operate the RALS pump.
Following dewatering of the material on the vessel, a cargo-handling system will be used to load the dewatered material into four storage holds. It will then recover the material from the storage holds and transfer it directly to a handymax vessel for shipment of the material to China.
Seafloor Production Tools
There are three Seafloor Production Tools (SPTs), the Auxiliary Cutter (AC), the Bulk Cutter (BC) and the Collecting Machine (CM). Nautilus’ Seafloor Production tools combine existing technology from the offshore oil and gas sector with rock cutting technologies used in land-based operations. The SPTs were designed and built at Soil Machine Dynamic’s facility in Newcastle Upon Tyne, UK.
The SPT design is an extension of existing subsea trenching equipment combining hard rock mining technology with that of subsea remote system technology. The SPTs will be deployed from the Production Support Vessel (PSV) using a lifting frame and operated via a power and control umbilical.
Many world-class companies have been involved in the design of the seafloor equipment. The cutting drum of the BC was designed and built by Sandvik (Austria), a world leader in hard-rock mechanized mining and rock cutting equipment.
The designs are based on similar designs used on large continuous miner machines used in underground mining and construction.
The track sets for all three SPTs have been designed and built by Caterpillar, based on an existing Caterpillar excavator track design. Modification to the track set for subsea operation and required cutting duty was completed by SMD in consultation with Caterpillar and Sandvik.
The dredge pumps for all three SPTs have been supplied by Damen. The hydraulic equipment for all three SPTs is based on existing off-the-shelf Bosch Rexroth hydraulic equipment, with adaptations by SMD.
The flexible hoses for all three SPTs have been designed and supplied by ContiTech AG (Germany), and are very similar to the rubber hoses used in the dredging industry. Companies and institutions involved in the simulations and test work of the BC include CSIRO, Cellula Robotics, Deltares, Istanbul Technical University, ContiTech Oil & Marine Corp and Paterson & Cooke Consulting.
Riser and Lifting System
The Riser and Lifting System (RALS) is designed to lift the mineralised material to the Production Support Vessel (PSV) using a Subsea Slurry Lift Pump (SSLP) and a vertical riser system.
The seawater/rock is delivered into the SSLP at the base of the riser, where it is pumped to the surface via a gravity tensioned riser suspended from the PSV.
It comprises a large pump and rigid riser pipe hanging from a vessel which delivers the slurry to the surface. The proposed positive displacement pump is designed and built by GE Hydril (Houston, TX). The SSLP hangs from a solid vertical (riser) pipe suspended beneath the support vessel. The pipe is deployed to the seabed by a derrick and draw works system on board the vessel.
GE Oil and Gas have been involved in the development of the Subsea Slurry & Lift Pump and the riser has been designed by Nautilus’ RALS main contractor, Technip USA, and built by subcontractor General Marine Contractors .
Production Support Vessel
The Production Support Vessel (PSV) provides a stable platform for operations using world-class dynamic positioning technologies to ensure it stays on location at Solwara 1 irrespective of wind and wave conditions. The PSV will be designed for use in offshore construction and seafloor mining The PSV will be equipped with a moonpool through which the Subsea Slurry and Lift Pump (SSLP) and riser system can be deployed. On deck of the PSV, the slurry is dewatered. The dewatered solid material is stored temporarily in the PSV’s hull, and then discharged to a transportation vessel moored alongside the PSV about every five to seven days. Filtered seawater is pumped back to the seafloor through the riser pipes and provides hydraulic power to operate the SSLP.
Discharge of the return water at the seafloor from where it came eliminates mixing of the water column, and minimizes the environmental impact of the operation.
When completed, the PSV will measure 227m in length and 40m in width with accommodation for up to 180 people and generate approximately 31MW of power. All of the below-deck mining equipment will be installed on the PSV during the build process to minimize the equipment integration to be completed following delivery of the PSV.
The Company has entered into an agreement for the charter of the PSV with Marine Assets Corporation (MAC), a marine solutions company based in Dubai which specialises in the delivery of new build support vessels for the offshore industry.
MAC will own and provide the marine management of the PSV. The PSV will be chartered to Nautilus for a minimum period of five years at a rate of US$199,910 per day, with options to either extend the charter or purchase the PSV at the end of the five year period.
Under the terms of the arrangement, MAC had to enter into a contract with Fujian Mawei Shipbuilding Ltd., based in Fujian province in south-eastern China, to design and construct the PSV in accordance with Nautilus’ specifications. The PSV is expected to be delivered by the end of 2017.
Status of the Equipment
In January 2016, the company took delivery of the three Seafloor Production Tools (SPTs) from SMD. The SPTs have since been shipped to Oman where they are scheduled to undergo extensive wet testing at Duqm Port (Q2 2016) which is designed to provide a submerged demonstration of the fully assembled SPTs and will involve submerged testing of:
- Control systems operations and feedback
- Hydraulic functions
- Collection system functions
- Survey and visualization systems
United Engineering Services LLC (UES) will provide the support services associated with wet testing the equipment and storing the equipment as it is delivered from various suppliers prior to integration onto the Production Support Vessel (PSV) which is expected to occur in 2017.
The three umbilical winches that store and manage the power and control umbilicals were designed, procured and assembled at SMD. In March 2015 the Company announced that the umbilical winches for the three SPTs had successfully completed testing. The umbilical cables have since been installed onto the umbilical winches and shipped to the shipyard for integration on to the vessel.
Launch and Recovery System (LARS)
The Launch and Recovery System (LARS) which will be used to lift the tools in and out of the water, is comprised of A frames, lift winches, hydraulic power units, electric power units and deck control cabins.
Riser and Lifting System (RALS)
GE Oil and Gas, the primary contractor for the Riser and Lifting System manufacture, has begun retrieval and inspection of the components that were previously in storage or in mid assembly when the contracts were terminated in 2012. The manufacture of components such as the derrick and riser handling systems, surface seawater pumps, pull in skids, riser transfer hoses and other ancillary equipment is to be resumed with delivery dates dictated by the shipyard requirements for the PSV. These components are to be integrated onto the PSV during vessel manufacture.
The Subsea Slurry Lift Pump (SSLP) recommenced assembly in Q3, 2015 and in February 2015 commenced Factory Acceptance Testing.
Production Support Vessel (PSV)
Fujian Mawei Shipbuilding Ltd. (FMSL), based in Fujian province in south-eastern China, has been contracted by MAC to design and construct the PSV in accordance with Nautilus’ specifications.
In September 2015, the first steel for the PSV was cut.
Comments