Rigid plastic ducts
An energy-saving ventilation option for underground mining
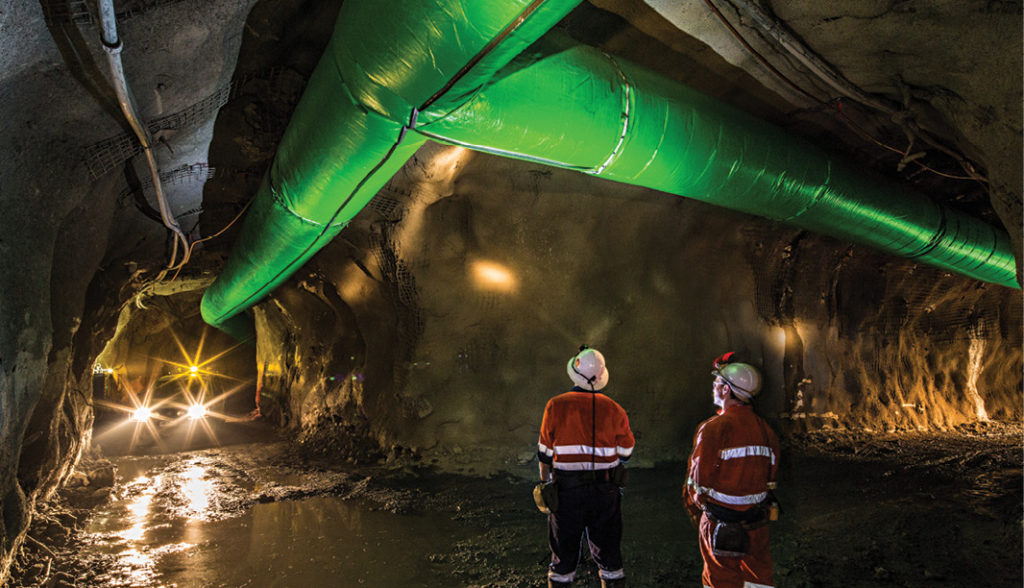
Ventilation serves three essential purposes in underground mines: (i) to provide fresh air for workers to breathe, (ii) to remove noxious contaminants and hazardous gases (which arise from diesel exhaust, blasting, and the rock itself), and (iii) to regulate temperature and humidity.
An underground mine ventilation system is comprised of fans, ducting, coupling, and curtains to get sufficient fresh air to the working face of the mine. As mines advance deeper, stronger airflow is required. Ventilation accounts for a large portion of energy use in underground mines and ranks second in terms of financial cost for these mines globally, behind ground support.
Energy conservation is a major concern, and there is an opportunity for energy-saving ventilation options. The Canadian Mining Journal spoke with Don Turgeon, director of sales at Rocvent, to discuss the future of underground mine ventilation.
Polyvinyl chloride (PVC) ducts
The most popular material used for underground mine ducts is a durable fabric coated with polyvinyl chloride (PVC). It is estimated that 60% of ducting used in underground mines is made of this PVC fabric material, and that PVC fabric is the only product used consistently around the world for underground mine ventilation.
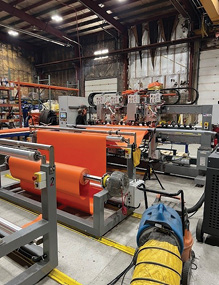
PVC is popular because it is lightweight and flexible. It can be folded and tucked away for storage, and it is easier to bring underground and install. It also has beneficial tensile and tear strength characteristics, which are important for use near heavy equipment and debris.
Future ventilation requirements
With the industry push toward carbon-neutral and net-zero mining, mines are looking for ways to cut carbon emissions and save energy. As mines switch from diesel-powered to battery-operated machinery, the following question arises: Will underground mines require less ventilation in the future?
Although there will be less diesel exhaust, batteries generate lots of heat. Ventilation will still be required to help regulate the temperature deep underground, especially because mines get hotter as they go deeper. There is also increased demand for the critical minerals used to create those batteries, resulting in many new underground development projects that will need ventilation solutions.
When it comes to energy conservation, reducing ventilation underground is not an option. Luckily, rigid plastic ducting is emerging as an efficient and energy-saving ventilation option and represents an opportunity for ventilation manufacturers like Rocvent.
The move toward rigid plastic ducts
According to Rocvent’s website, the company is a “major manufacturer of all types of mine and tunnel ventilation, tubing, and ducting”. Rocvent is based in Chelmsford, Ontario, within Greater Sudbury, the heart of the mining industry in Northern Ontario. The company was founded in 1989 and has historically focused on PVC-coated woven fabric ducting.
Recently, Rocvent expanded its product offerings to include steel ducting and rigid plastic ducting. Don Turgeon said the company has cornered 75% of the mining ventilation market in Northern Ontario and is expanding business into the U.S., Mexico, and Chile via distribution. Its customers are usually technical services (engineering) and mine planners at both new mines and those that are advancing farther underground. Rocvent conducts ventilation surveys on site and employs engineers that can recommend mine-specific solutions. The company’s goal is to become a “one-stop shop” for all underground mining ventilation needs.
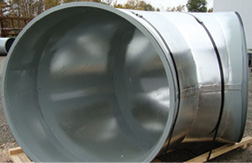
Rocvent has taken a leading role in product development to help mines reduce ventilation costs and improve the amount of fresh air at the face. A large part of this is its rigid plastic ducts, including rigid elbows and lateral pieces, made of fire-resistant high-density polyethylene (HDPE).
Benefits of rigid plastic ducting
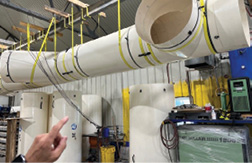
Flexible PVC fabric ducts create a fluttering effect when air is blown through them. This creates a loss known as “friction loss.” Rigid plastic ducts, as their name implies, do not produce this fluttering effect. They have less friction loss, are less porous, and can push fresh air at longer lengths than PVC fabric ducts. This results in higher-efficiency airflow, which in turn requires less energy from fans, generating energy savings. Rigid plastic ducts work with both positive and negative pressures.
Challenges of rigid plastic ducting
Unlike PVC fabric ducts, rigid ducts are difficult to bring underground, since they are not flexible or foldable and take up a lot of space. When a mining project concludes, rigid plastic ducts cannot easily be brought back up to the surface and cannot be recycled. For these reasons, rigid plastic ducting often ends up sitting in a yard underground.
The inflexibility of rigid plastic also makes its transportation difficult and costly. One pallet can fit about 304.8 metres of flexible ducting, but only 24.3 metres of rigid ducting. For shipping, a truck can fit more than 9,100 metres of PVC fabric ducting, but only about 61 metres of rigid plastic ducting. Thus, there are large expenses and a substantial carbon footprint associated with shipping rigid ducts. Turgeon said this is especially relevant for Rocvent, who makes all its ducts in Northern Ontario (Sudbury and North Bay) and ships them out to mines across Canada and internationally. Mine planners often prefer flexible ducting because of these costs, but mining engineers prefer rigid ducting for its higher efficiency.
Rigid HDPE ducting is also seven times more expensive to produce than its PVC fabric counterpart, but according to engineering calculations, the savings on energy costs over the course of a mining project are often worth the higher initial investment.
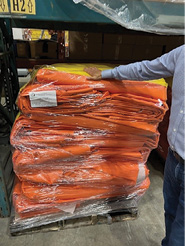
Another challenge is getting operations teams to buy in to rigid ducting. Although executives and managers may want to use rigid ducting because of carbon rebates and energy savings, miners do not always like working with rigid ducts, as they are not the easiest option for installation underground. Furthermore, miners are not as invested in the energy consumption or long-term planning of a mine, so they may not fully appreciate the benefits of rigid ducts. It can take time and effort to resolve disagreement between management and operations and to create buy-in among miners. “If the miners do not buy in, it is not going to work,” said Turgeon. Rocvent assists in this process by training operations teams on the proper installation of its products.
Choosing a ducting material
Turgeon noted that Rocvent has not seen any existing mines switch their ducting from PVC fabric to rigid HDPE, but in the last five or six years, new mines tend to favour rigid ducting. Many products from competing ventilation manufacturers are interchangeable, so mines that are advancing or have damaged ducts do have the option to change from one ducting material to another, or to have rigid ducts branching off into flexible ducts. Rocvent is creating fittings between rigid plastic ducts and PVC fabric ducts to make it easier for mines to adapt. However, there are other factors to consider when selecting a ducting material.
Different materials are used based on the volume of air being delivered to the working face. Certain parts of the mine may require a different material. For instance, flexible ducts can be used for headings, whereas rigid ducts can be used in the main ramp underground and areas where there are longer runs. The various types of ducting are built to withstand different climatic conditions and can be used around the world, but they may face country-specific regulations.
Despite the potential challenges, underground mines appear to be moving toward rigid ducting for efficient airflow, energy conservation, and carbon rebates. Is it worth using rigid plastic ducts for underground mine ventilation? Each mine will need to weigh the pros and cons — and costs and savings — for themselves.
Kesiah Stoker is a Canadian multiskilled freelance writer.
Comments