Recognizing the importance of auxiliary ventilation

G+ Plastics argues miners should pay closer attention to auxiliary
ventilation, given its extensive use and energy intensity
More than ever, the mine ventilation community and underground mine personnel must be educated about the significance of auxiliary ventilation because of its critical role and substantial power consumption. If ventilation is an essential underground mine system, its importance is rarely recognized; this is especially true with auxiliary ventilation made of an assembly of ducts and fans. While the latter technologies have evolved considerably in the past decade and duct-fan systems have become increasingly complex, auxiliary ventilation design, operation and maintenance practices are lagging.
Auxiliary ventilation refers to the systems that are used to supply air to the working faces of blind headings and is independent from the full mine ventilation network. Generally, North American hard rock mines resort to duct-fan systems for their auxiliary ventilation, most made up of a single fan and layflat tubing.
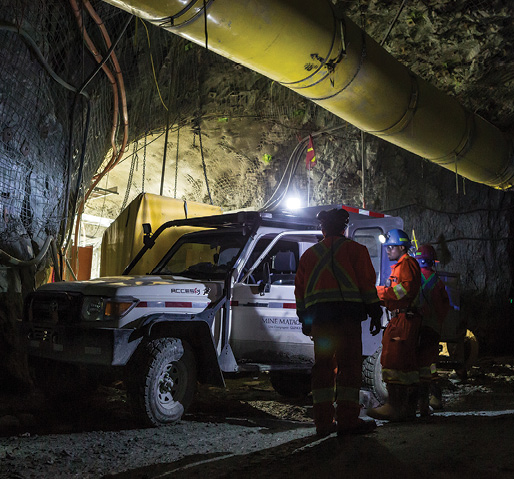
While most duct-fan systems are designed to ventilate production and development headings on a temporary basis, more permanent systems are put in place to ensure adequate working conditions in shops, garages, underground hoistrooms, etc. Malfunction or failure of these systems results in interruption to operations.
There has recently been an increasing interest for extensive duct-fan systems to ventilate long development headings and exploration ramps. Changes in mining practices and economics are driving this shift, especially in greenfield projects, for which the dominant rationale is that decline development is more economical than shaft construction. Reliable auxiliary ventilation is vital to ensure safe and timely development.
New technologies available to the mining industry are enabling construction of efficient duct-fan systems that can convey great air flow over several kilometres.
But extensive duct-fan systems are also energy intensive. Compared with conventional heading ventilation requiring 15 kW to 113 kW, these long development duct runs can require power inputs ranging between 250 kW to more than 1 MW.
It is generally assumed that 25% to 40% of an underground mining power consumption is dedicated to ventilation, excluding heating and refrigeration. Yet hardly any mine can disclose what proportion is assigned to auxiliary ventilation.
An audit performed in 2014 at Vale’s Garson mine in Sudbury, Ont., determined that auxiliary ventilation accounts for nearly 20% of its entire energy consumption.
Is such figure representative of an average hard rock underground mine auxiliary ventilation power consumption? Probably, according to experts.
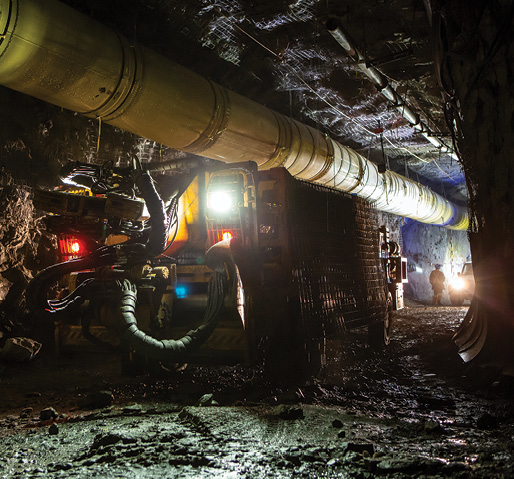
In the case of greenfield underground projects, auxiliary ventilation may be the only source of fresh air for all mining operations. An outstanding example is Newmont’s Borden gold mine: during its initial stages, the decline was ventilated with two independent duct-fan systems extending over 2,000 metres and composed of a total of eight 186 kW fans, for an approximate power consumption of nearly 1,500 kW at full length. It operated for about two years before establishing flow-through ventilation. On average, a similar system would operate for 12 to 18 months.
Extensive auxiliary ventilation systems have tremendous operating costs. Besides, they may represent important capital investments: recent systems have exceeded the million-dollar mark for fans and ductwork only.
Importance of design, installation
One would expect that such an energy-intensive system be meticulously designed to optimize its performance and power consumption, yet many designs disregard potential issues arising from quality of installation, mobile equipment clearance, and maintenance practices.
Quality of installation dictates air losses and fan outputs; clearance and maintenance practices influence the system’s degradation and loss of performance in time, as damage results in additional air losses and reduced reliability.
While a single hole or dent in a 2,000-metre-long ductwork may be inconsequential, damage effects are cumulative and result in decreased air volume at the face or even system failure, inevitably interrupting development.
A common corrective strategy is adding more fans to the system to boost its performance, which leads to an increase in power consumption. This can, however, be avoided by properly addressing potential operational issues during design.
The situation is worst for production or short or medium development auxiliary ventilation, which are often designed with basic rules of thumb introduced some 10, 20 or even 30 years ago. Today, these rules of thumb have been replaced by software. However, by blindly trusting these rules or software simulation outcome, mining engineers often disregard clearance, installation, and maintenance issues altogether.
Why is so little consideration given to auxiliary ventilation? Maybe too few have realized its extent and substantial power consumption. Conducting energy audits may help provide a more accurate portrait of auxiliary ventilation in North American hard rock mines.
But it may also have to do with education.
The North American mining engineering curriculum includes an average of 45 hours of ventilation in a program spanning over four years during which students must become proficient with fluid dynamics and thermodynamics applied to mine ventilation, main and auxiliary ventilation system planning and operation, climate control, and dust and contaminant mitigation. Together, these concepts help design and operate efficient ventilation throughout a mine to provide a safe environment for underground personnel and prevent fires and explosions.
‘Necessary evil’
Many mining engineers regard mine ventilation as complex and a ‘necessary evil.’ Mine ventilation often falls on engineers in training (EITs) with little to no experience in the field. These EITs are expected to learn new concepts on the fly and are urged to apply outdated rules of thumb rather than modern best practices. This is particularly true for auxiliary ventilation.
It may be time for all industry stakeholders from academia to operations together to acknowledge that auxiliary ventilation practices and technologies have evolved and that duct-fan systems have become more complex and energy intensive and require commensurate attention to design and installation. Renewed focus should be placed on re-evaluating auxiliary ventilation practices with cost sensitivity and reliability in mind rather than preference for simplicity.
Fortunately, manufacturers and consultants represent available resources to mining engineers to help them design efficient auxiliary ventilation systems that fulfill airflow requirements while minimizing energy consumption. CMJ
Myriam Francoeur is ventilation projects and communications director with G+ Plastics (www.plasticminer.com).
Comments