Real-time tire performance data
Q & A with Dave Allan, vice-president of Canada’s Kal Tire Mining Tire Group
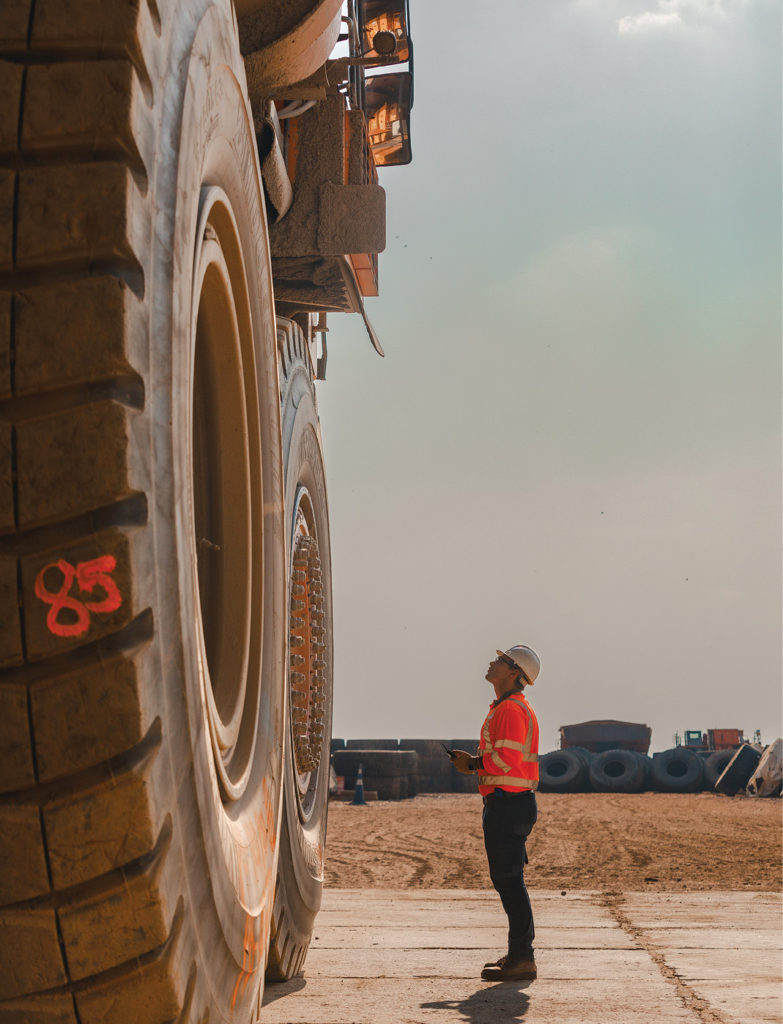
TOMS is a tire maintenance planning system that powers uptime, performance, and safety. With a focus on fleet productivity and accessible, near-live reports, TOMS enables informed decisions for today’s work plan and the road ahead. Using agreed benchmarks and maintenance schedules, TOMS automates planned work orders such as fleet inspections and front tire rotations. Regular fleet inspections can catch critical issues that require immediate attention and reduce safety risks.
Q: First, can you just give us a brief idea about the Mining Tire Group at Kal Tire; please mention examples of the tire manufacturers and/or suppliers?
A: At Kal Tire, the Mining Tire Group takes care of the customers in different regions in the world: Canada and Latin America, including Mexico, Colombia, Chile, Panama, as well as the U.K., West Africa, Southern Africa, and Australia. Some customers obviously work in multiple regions.
We benefit from being a multi-brand dealer with deep relationships across many suppliers. Our main suppliers are Bridgestone, Michelin as well as Maxam. That can be different depending on the region. For example, Goodyear is one of our suppliers in Southern Africa but not in Canada, so it depends on the region and the logistics. In Canada, we work with multiple suppliers to get the right product for our customers applications.
We provide both products and service. We sell tires to customers and provide the maintenance services for those tires, as well as inventory forecasting and more. Our services also extend to retreading and repairs of mining tires. Depending on the operating conditions at each site, we create a targeted tire program with the customer, which our site technicians will then follow.
Our tire and operations management system (TOMS) is how we track all our tire data, but it is also a maintenance planning system. It provides us the ability to proactively plan for tire maintenance based on the agreed tire program. This means we can ideally schedule a large amount of tire work at the same time the vehicle will be in for maintenance to maintain fleet productivity whenever possible.
Q: Do you have any systems supporting TOMS?
A: TOMS is built on a foundation of industry-leading technology, and it integrates well with third-party systems and sensors. In 2021, we integrated the thermal imaging camera and AI software of Pitcrew.ai into TOMS. As a result, we are now able to offer customers autonomous tire inspections. As a truck passes the stations that houses the camera, a thermal image is captured and the AI picks up any anomalies, such as hot spots, belt edge, or tread separations. The information is automatically transmitted into TOMS, which enables required action to be aggregated with other identified tire work to drive smarter planning and decision-making that will further enhance fleet productivity and safety. TOMS also integrates with the principal mining TPMS systems, automatically adding the pressure and temperature data into collected inspections and enabling work orders to be created to address issues such as low pressures to faulty sensors.
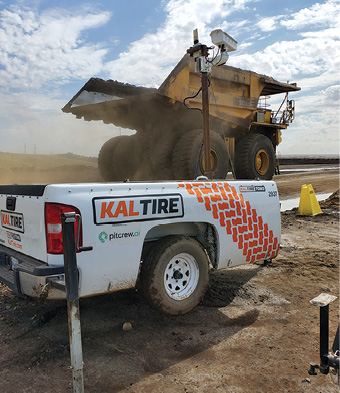
Q: Can you talk to us about TOMS and how it could be useful for fleet management on mining sites?
A: As mining increasingly automates, TOMS understands that interoperability and the integration of sensors and the effective use of artificial intelligence to pull actionable insights from multiple data streams are key to meeting the needs of tomorrow’s mining sector. We wanted to integrate that technology into our tire management system to give people capabilities to see things that they cannot see with the human eye. For example, when technicians are inspecting a tire that is four-metre high, there are many areas that the technician just cannot see when around the truck.
TOMS also enables comparative analysis and benchmarking thanks to a common language for describing assets and processes. Using standard measures and KPIs (key performance indicators) ensures consistent reporting and service performance measurement.
One useful feature is that it enables Kal Tire teams around the world to share insights as they perform tire service using a common platform. Aggregated data benchmarks tire performance, downtime, haul fleet productivity, and more to identify ways to improve fleet use. That kind of predictive analytics help support workflow planning, tire repair decisions and inventory management.
Additionally, the automated priority-based work orders could lead to opportunities to improve mean time between service (MTBS). Generally, TOMS empowers team leaders to spend more time providing leadership than recapturing data.
TOMS employs metrics used to track truck productivity to measure tire life so teams can gauge how changing operational conditions are impacting tire performance and make more informed tire recommendations.
Q: How does TOMS communicate the data to crews?
A: TOMS facilitates a fluid communication flow between inspectors in the field, tire supervisors and technicians in the shop, and the customer planning team; and back again. Near real time PBI dashboards and reports allow managers to remain updated on service KPIs and performance trends, permitting informed and timely decision making.
With TOMS’ mobile fleet inspection app, inspectors instantly capture and share tire damage images and prioritized findings. So, real-time data capture drives meaningful decision making, enabling tire managers and miners to discuss when to best schedule required tire work.
A key output of TOMS is its planning report. This is a summary, by truck and by priority, of all the required work for the upcoming period that requires scheduling – whether planned tire maintenance activities are part of the agreed tire program or operational damage identified from inspections or sensors such as TPMS or Pitcrew.ai. The planning report can be shared directly with the customer planning team through integration into their ERP system or via automated email. For our teams, and to close the feedback loop, agreed scheduled work is available for them by several methods – by tablet, screens in the tire shop or as pre-printed work orders. At the same time, apps such as TOMS on the Go allow tire teams and our customers to see the latest information on installed and removed tires or rims. CMJ
Comments