Raising the bar on pumps
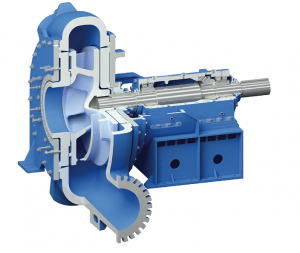
Some of the important features of the MDX slurry pump for mill circuits are a lower specific speed design, a slurry diverter, a range of high chrome white irons and multiple suction liner configurations. Credit: KSB Group
It is widely recognized within the pump industry that the extraction of minerals from rock places the greatest demands on fluid handling equipment. Not only must pumps contend with aggressive slurries and ever-changing working conditions that cause aggressive and excessive wear, they have to deliver the highest levels of reliability.
As a consequence, manufacturers have responded by designing highly specialized, heavy duty slurry pumps capable of reducing downtime, lowering the total cost of ownership and delivering increased efficiency.
Mining is not an industry that pump companies can simply dabble in opportunistically; they need be fully committed to it. This commitment begins with research and development that drives the continuous improvement of pump and material technology, introduces new technology like artificial intelligence, machine learning and remote sensing, and improves the manufacturability of complex parts. Reputable pump companies provide specialized pumps for various applications such as SAG and ball-mill circuits, mill discharge, cyclone feed and screen pumping, hydro-transport and tailings booster stations. The onus is, therefore, on the pump manufacturer to have the expertise in hydraulic design, mechanical design, wear technology and materials technology to provide the best and most reliable products for transporting slurry. Furthermore, they should be willing and able to collaborate with their customers over the entire lifecycle of the pumps to extract the best performance and value for money.
Aggressive slurries demand heavy-duty slurry pumps.
“While no two slurries are the same, all slurries place extreme demands on pumps,” says Jonathan Samuel, vice-president, sales and marketing, for KSB in hard rock mining. “Slurry pumps used for solids transport have to move a variable composition of rocks, sands and chemicals. Under such abrasive and corrosive conditions, pump parts can wear out very quickly. When pump parts wear out before planned outages, the entire production process comes to a grinding halt, resulting in exorbitant costs and production losses. That means reliability is essential in any slurry transport system.”
The KSB Group has been serving the mining industry for the best part of 130 years and today it is active in mining operations around the world. The headquarters of its mining operation are at its GIW Industries plant in Grovetown, Georgia, and it is here where over many years some of the largest centrifugal slurry pumps for hard rock mining, dredging and the oilsands industry have been designed, tested and manufactured. GIW makes a wide range of slurry pumps in a variety of materials for every application in mining.
In addition to slurry pumps, the KSB Group’s portfolio includes a wide variety of process pumps that are suitable for the myriad non-slurry applications found in mines and minerals processing facilities. Submersible bore well pumps, vertical turbine pumps, horizontal split case pumps, multi-stage high-pressure pumps, single stage horizontal pumps and more.
Hard rock experience
To a large extent, the most extreme duty conditions in hard rock mining are found in the mill circuit and these impose considerable demands on pumps. The highly aggressive nature and density of the slurry being pumped can result in early wear on components, leading to failure and expensive mill downtime. This means that the pump design and materials have to withstand solids-laden slurries, deliver reliability and give long wear life. It is essential that the slurry passes through the pump with the minimum amount of wear to the pump casing, liners, impeller and shaft sealing mechanism. Furthermore, they must be capable of delivering high flows and withstanding harsh operating environments.
By introducing features that address these issues, it becomes possible to create a head/quantity and efficiency curve critical for efficient mill operation. This means that productivity is maximized and operating costs minimized as the pump is matched to operating cycle times with mill outages. Some of the important features that KSB offers in its MDX slurry pump for mill circuits are a lower specific speed design, a slurry diverter, a range of high chrome white irons and multiple suction liner configurations.
MDX pump development
A large diameter impeller allows for slower pump operation and this extends the wear life of wet-end parts, even under variable flow conditions. A slurry diverter dramatically increases suction liner life by reducing particle recirculation between the impeller and the liner.
“The diverter is based on the theory that if particles can be excluded from the nose gap, wear life is enhanced,” explains Jonathan Samuel. “Research has shown that internal velocity and pressure gradients between the impeller shroud and the suction liner can allow particles to migrate toward the suction eye. These solids contribute to the wear-induced degradation of the gap between the suction liner and the impeller. As this gap grows, wear rates increase and pump efficiency is reduced.”
Laboratory tests undertaken at the GIW plant verified the particle flow and this led to the development of different solutions to counter it. By ‘diverting’ particles away from the pump’s suction liner, their flow direction can be reversed. The result is the slurry diverter, which has been patented by KSB, and significantly extends the average service life of the MDX pump while processing the same amount of ore.
Running at slower speeds and the development of the slurry diverter are not the only elements that provide the MDX pump with the capabilities to combat wear. The patented design of the impeller inlet allows both liquid and solid phases within the slurry. Minimizing aggressive particle impingement by giving the pump a deep base circle delivers a sliding wear that reduces abrasion. Oversized shrouds result in enhanced vane performance by providing an added clearing action that reduces recirculation and wear between the impeller and the suction liner. The suction liner is adjustable, enabling the user to maintain a tight nose gap thereby extending wear life and maximizing productivity. This is of immense value to the plant operator as it minimizes costs by matching operating cycle times with scheduled mill outages. Thicker cross-sections of the wet end parts enable the MDX pumps to offer long and reliable pump life. GIW also offers several configurations of Suction Liner design to combat wear caused by velocity issues.
GIW’s commitment to materials R&D has led to the development of a range of high chrome white irons that offer customers multiple options depending on their ore characteristics, operational philosophy and production goals.
“The MDX has an established and successful position globally for mill discharge pumps, e.g., in SAG mill, ball mill discharge, cyclone feed and screen feed application,” Samuel says. “It is more than capable of delivering flows of up to 14,000 m³/h, heads of 45m at slurry densities in excess of 1.65.”
What customers in hard rock mining are looking for is a pump that is capable of operating over a wide range of duty conditions while still delivering maximum throughput at the lowest cost. Now having built up a wide international installation base for the MDX, KSB is seeking to meet and exceed these demanding expectations.
Bryan Orchard is an independent technical author and journalist who has been working in the global pumps and valves industry for over three decades. This article was supplied by GIW Industries. For further information visit www.giwindustries.com or www.ksb.com.
Comments