Prepping for conveyor maintenance and upgrades
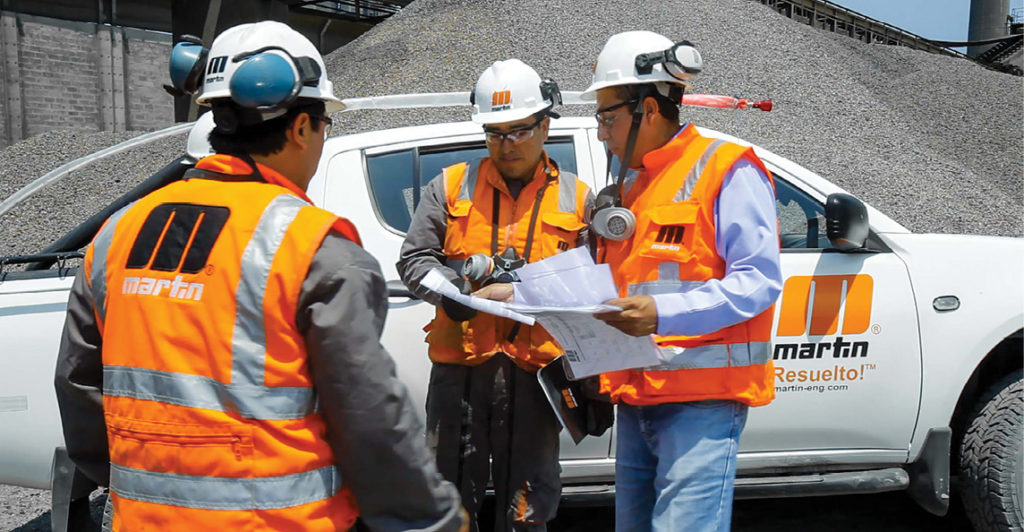
Scheduled mine shutdowns ensure optimum productivity and are also necessary from both a maintenance and safety standpoint. Some unwritten truths about shutdowns include the following: (1) there is never a “convenient” time, (2) it is impossible to be totally prepared, and (3) completing a shutdown with zero injuries equals success, regardless of how much was accomplished.
Demand and the need to control costs have pressured mine managers to extend periods between scheduled outages. The amount of time allotted for the outages has also come under pressure, often with many (sometimes conflicting) projects scheduled at once. Shutdowns are busy times, with in-house and contractor personnel working on tight timescales to complete an array of projects before the scheduled restart date.
Budgets, timelines, and production quotas complicate mine shutdowns. Despite the best planning, pushing to stay under budget and ahead of time can put sub-optimal equipment back into service, resulting in early failure. The rush to get back into production can also quickly cascade into a workplace hazard causing “turnaround injuries,” or incidents that result from working too quickly under stringent (sometimes unrealistic) timelines.
In bulk handling, it is critical for conveyors and material flow systems to be brought online for production to resume. Choosing the correct contracting and servicing partner to perform maintenance and improvements on conveyors can be the key to mine shutdown success. For retrofits and new equipment installation, manufacturers may supply a supervisor and use a subcontractor or in-house staff. This works well if both parties are experienced with the manufacturer’s equipment.
Common conveyor shutdown improvements
Operators are always looking to improve safety, efficiency, and production, and rightly so. Shutdowns are the optimum time for major retrofits and reconstructions to accomplish these goals.
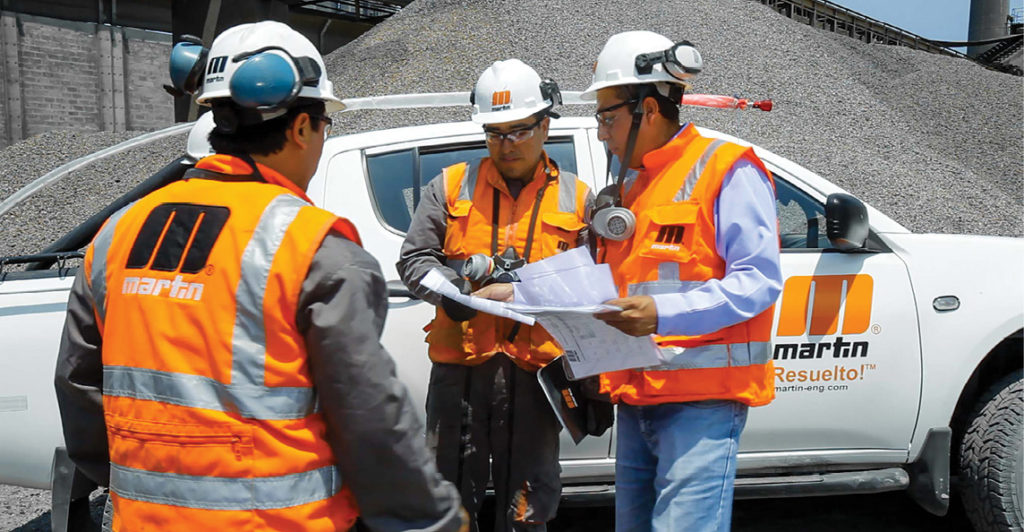
Upgrading a single piece of equipment is not going lead to greater production; it usually requires a well-engineered solution that considers all related aspects of the operation. For example, increased production might involve redesigning a transfer chute to handle greater material volumes with different trajectories at faster speeds in a well-sealed environment to control wear and avoid additional spillage and dust. Ideally, any solution should also improve safety and reduce the amount of required maintenance.
The right solution involves a head-to-tail examination of material flow in the system, and consideration for appropriate changes in the capabilities of every component. This includes reviewing any equipment that supports a clean and well-centered belt return, and controls access for improved safety around the belt, such as guarding and emergency shutoffs.
Choosing servicers and contractors
The volume of work required for a smooth and timely shutdown usually exceeds the number of trained and experienced internal staff needed to complete all tasks, so there is always a need for expert services and contractors. For safety and efficiency purposes, it is wise to choose trusted providers who are familiar with the site and involve them early in the process to gather bids, discuss details, and obtain their expert input.
The terms “servicer” and “contractor” are sometimes used interchangeably, since servicers are contracted, but their roles can be specific. Servicers are technicians who perform specialized scheduled tasks such as belt cleaner replacement or other conveyor maintenance. Contractors are often generalists supplying outside labour or specialists used for major equipment installation and construction, such as crane operators or structural engineers. However, during a shutdown, these may be the same person or company. In most cases, factory-trained technicians will have greater experience and expertise than in-house personnel or third-party workers, because they do not need to be trained on the nuances of products and installation techniques while on the job.
The goal should always be a project completed safely within the allotted time and budget. But that is not often the case. An unexpected obstacle that requires a pivot in the plan, a logistical issue with receiving the proper equipment, or a serious workplace injury can derail a timeline, resulting in extended downtime and increased costs.
The benefits of using the right specialized servicers during a shutdown are the following:
> Training and expertise –
They can quickly get the job done, identify potential issues, and troubleshoot if necessary.
> Faster access to the supplier –
They often have maintenance and installation documentation on hand and quick access to support from the supplier.
> Safety and certification –
Certifications are required for some specified tasks for safety purposes. Using an uncertified individual can increase the risk of injury and could be a liability issue.
> Equipment considerations –
Specialized contractors have the proper tools on hand to overcome obstacles.
> Engineering solutions –
When unforeseen problems arise mid-project, experienced contractors can devise a safe workaround either onsite or by communicating with the equipment manufacturer’s engineering staff.
> Logistical considerations –
Servicers often work for or have a parts agreement with the equipment manufacturer, providing them quick access to replacement parts.
> Insurance – Specialty contractors typically carry specialized liability and workers compensation insurance, which provides better protection for the customer than general insurance coverage.
Elements of a mine shutdown
The planning should start directly following the previous shutdown, as it can take months to complete all the required steps. Scheduled shutdowns have the following five general (often complicated) steps:
1 Scope
2 Plan
3 Schedule
4 Execute
5 Evaluate
There are commonly unfinished projects remaining from the previous shutdown, and checklists always grow leading up to the next one. Often, tasks that seem independent of each other can be symptoms of a larger issue. For example, idler fouling, spillage issues, belt damage, and more might seem like independent problems, but could all stem from the same mistracking belt. Identifying the root cause, addressing it, then testing the solution can help reduce the overall scope of a shutdown.
Once the primary areas of concern have been identified, prioritize the list by adding task labels to checklist items according to need: testing, repairing, replacing, deferring, or doing nothing.
Gathering bids
Detailed proposals are among the reasons why contractors and servicers are so valuable. Identify outside resources that can help complete items on the checklist and then solicit plans and bids, i.e., a request for quote (RFQ). These bids –
delivered as a proposal or statement of work (SOW) – will offer a detailed account for materials, purchased components, contract services, and in-house labour.
Quotes for materials should consider lead time not only for the delivery, but also for the secondary operations such as preparatory engineering, electrical installation, or component fabrication. When the RFQ is issued, ensure that all necessary specifications for purchased components are provided. Of the four areas requiring hard quotes, accurate estimates on contracted labour can be the most difficult to obtain.
Any potential suppliers should review the scope, specifications, drawings, and photographs to note any exceptions or revisions that could be required as the job progresses. The project manager will also need to discuss direct labour with various resources within the company to outline both requirements and duration. The most accurate method to accomplish the estimate is to break the work into individual tasks, assess for each task and then summarize to generate the total.
Once the checklist has been prioritized and categorized, and contractors have provided their bids and requirements, estimate the time for each task and create an overall timeline. This may change during the planning and scheduling phase, but it provides a baseline to work from.
Planning a mine shutdown
Here is where the budget comes in. Once the scope, specifications, and timeline have been established, operators find that a substantial portion of planning has already been accomplished. However, sign-off is needed on the bids, which can take time. Be aware that each SOW may have a purchase order (PO), and once that is signed, the mine has committed to the provisions on the SOW.
A PO contains a payment schedule with an upfront payment before the shutdown begins to complete material orders, confirm commitments to sub-contractors to secure their schedule, etc. Early project delivery requires a careful review of the entire supply chain, including labour requirements and site conditions regarding access and storage.
When planning, be aware of weather, holidays, pending labour contracts and compliance (permitting) issues during the closure period. All of these can bring a project to a grinding halt.
This is also the phase when key performance indicators (KPIs) are set for each project. These are metrics that indicate the performance and measures of success of each project involved in the shutdown. It is important to keep KPIs realistic, as they will later provide valuable data in the evaluation phase. Choosing to install modern automated equipment and monitoring technology connected to logistical software and mobile apps can provide critical data and help with ongoing equipment condition and system efficiency monitoring and reporting.
Scheduling a mine shutdown
When designs are finalized for components and subassemblies, the handoff between design and manufacturing must take place. The schedule, scope, and specifications should be reviewed by the project manager with all of those involved in the supply of the project components and subassemblies. After a project is underway is not the time to experiment with new vendors.
As materials, components, and subassemblies are delivered, they need to be inventoried and inspected. To avoid project delays, vendors need to be informed immediately of any shortages or nonconforming items and the intended resolution determined. Material shrinkage (through damage or pilferage) is a concern in many sites the world over and can affect both project cost and schedule.
Scheduling and safety
The scheduling process is a suitable time to ensure all the required safety protocols and equipment are clearly understood by everyone involved in the shutdown. Ensure that proper certifications are up-to-date and that any specialized equipment is available, lockout/tagout procedures are explicit and followed religiously, and all contractors certified with the appropriate health and safety authorities.
Underestimating timelines for projects can rush the work and drastically erode safety. Several different projects overlapping in the same area can also become a major safety concern and must be avoided.
Execution
The project manager (PM) is responsible for controlling all work produced within the project scope. The PM must watch for (and carefully control) any changes in scope, commonly called “scope creep.” Changes for any reason must be documented by a “change order” that will normally also require a contract revision or addendum to ensure validity. Scope creep can quickly erode both the project budget and schedule and is one of the primary reasons for extending downtime.
Sometimes internal employees (direct labour) will overlook safety needs when planning shutdowns, because they work at the mine every day and are familiar with the hazards that are present during operations. Most projects that are undertaken during a mine shutdown are considered “non-routine tasks” with “non-routine safety hazards.” These are projects that are out of the normal operations for the mine and should be approached with prescribed safety protocols.
Evaluation of a mine shutdown
Step-by-step instructions should be provided for both start-up and adjustment procedures. Before testing installed equipment, the project manager should ensure that the start-up checklist is reviewed, and all components and systems are thoroughly inspected and adjusted. This includes visually inspecting all moving equipment to confirm that all components are performing as anticipated. After initial testing of the new equipment, check performance by loading the conveyor and watching it run, then making final adjustments as needed.
This phase of the project will utilize the pre-defined KPIs to measure the success of the solution. Evaluation regarding the performance of the system should be ongoing to ensure that it meets or exceeds expectations measured against the initial requirements in the scope and specifications phase of the project.
An important part of the evaluation phase is also measuring the ROI (return on investment) for each project. This will often inform budgets moving forward and could serve to raise budgets in future shutdowns to deliver greater improvements.
Determining mine shutdown ROI
Contractor proposals often include estimated ROI but calculating it after the fact using KPIs is important. The goal is to get the payback period as close to (or under) one year as possible (Table 1). Keep in mind that less expensive equipment which might indicate a quicker ROI is often more costly over the long term. Categorize all probable causes of increased costs (e.g., maintenance labour, downtime, production loss, and extra equipment costs) and then determine the costs associated with each category. The true measure of the expense is the “life cycle cost,” not simply the purchase price.
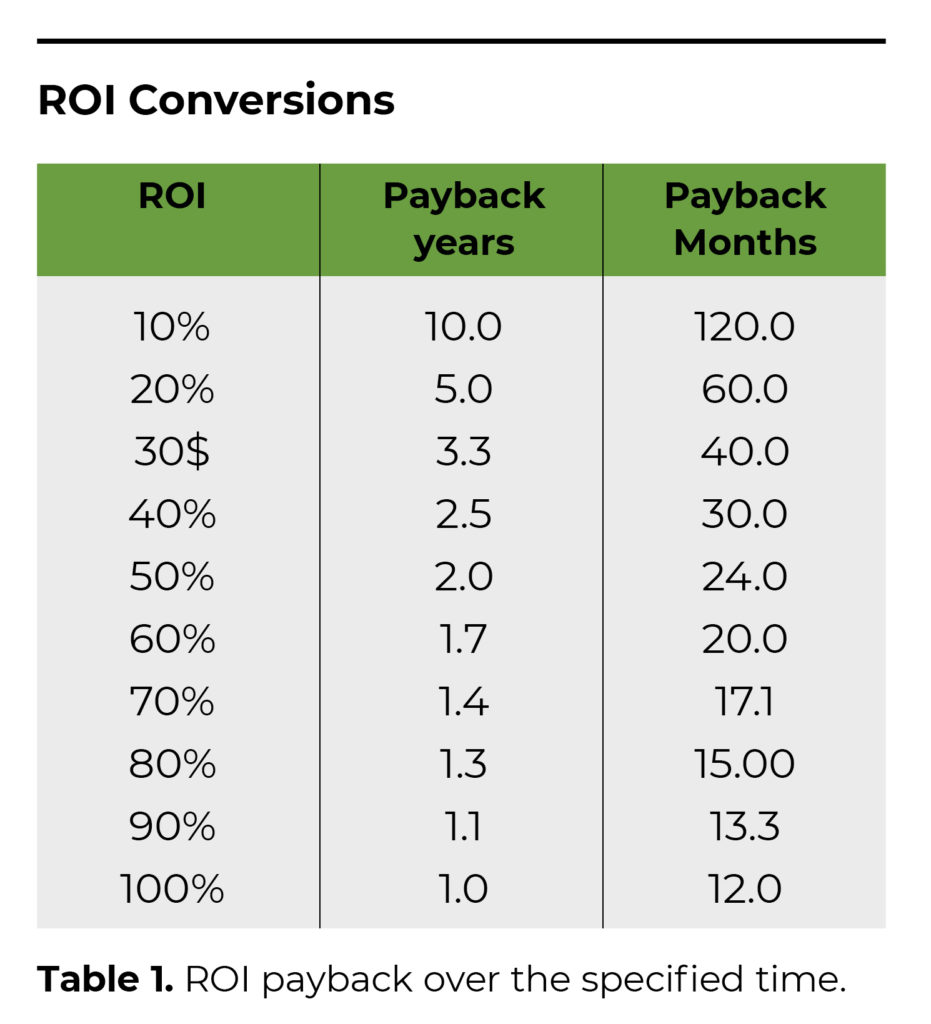
For example, calculating ROI to upgrade a belt cleaner begins with identifying the challenges associated with it. Likely, one category will be spillage from carry back. Some of the common costs associated with spillage are cleanup time/labour, low air quality, safety (e.g., lockout/tagout and personal protective equipment), replacement parts (fouled rollers and machinery), and unscheduled downtime (Table 2). There are resources available that help build a compelling case for projects and upgrades that include both direct and indirect costs such as safety.
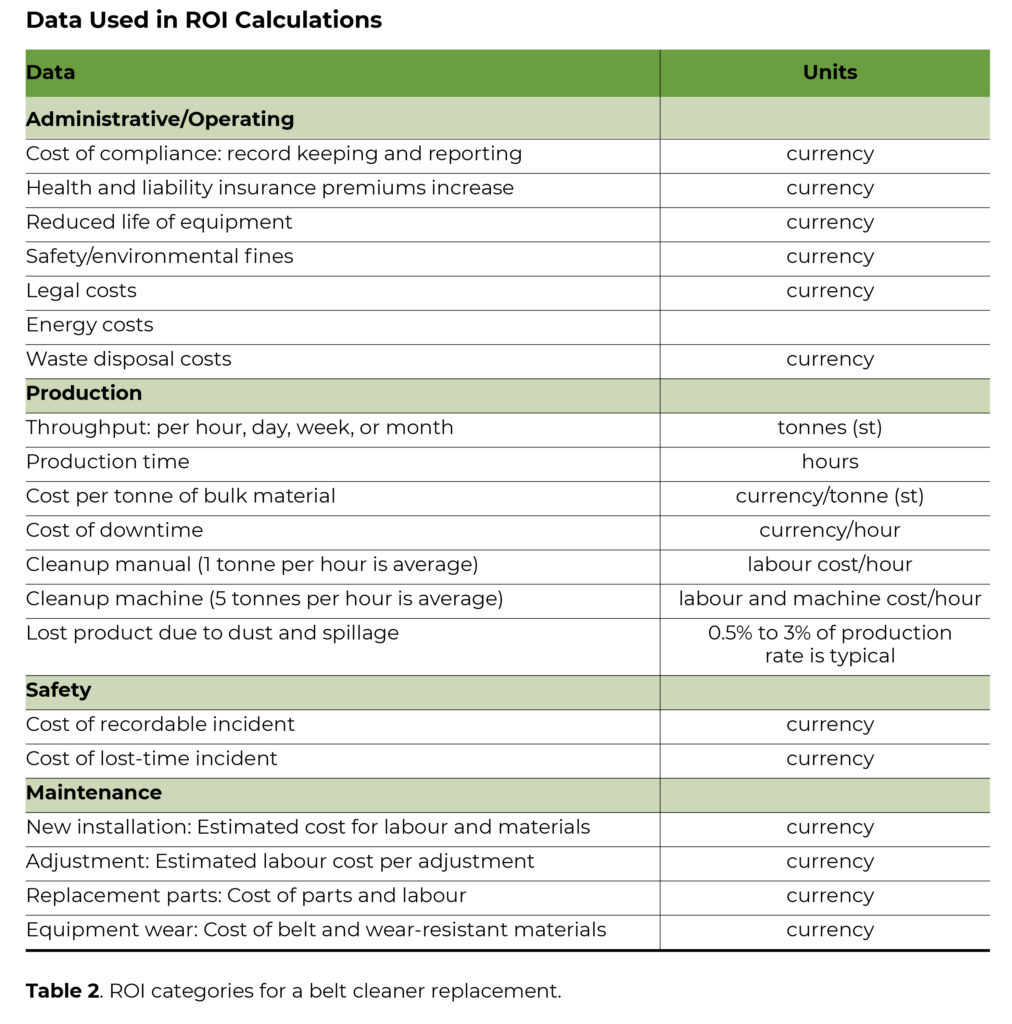
Installing only a portion of a project to meet the budget or using lower quality equipment to save costs does not necessarily translate to faster ROI. Often, half a solution does not equal half the savings. Staying with the example above, lower quality equipment might only clean 80% of material from the belt and deliver a shorter service life before unscheduled downtime starts all over again due to dust and spillage. Higher quality equipment with proven performance may carry a higher purchase price with a slightly extended ROI, but the cost is justified over the long term. It is recommended to review equipment specs, examine the materials of construction, and evaluate case studies from similar applications prior to purchase.
Conclusion
Generally, planning for a mine shutdown is not the task of a single individual but a co-ordinated effort between assigned project managers, supervisors, operations managers, contractors, and partners (e.g., equipment manufacturers and contractors). The key component is effective communication throughout.
Relying on the expertise of internal staff and contractors who have experienced similar shutdowns is an excellent step toward success. By thoroughly following the steps described, maintenance managers will have a good starting point from which to deliver a successful shutdown. Skipping any steps may result in more unanticipated complications that could extend downtime and reduce overall efficiency. Allowing the time for projects to be completed in a safe, systematic, and compliant manner results in fewer injuries and better performance of installed equipment over the long term. CMJ
R. Todd Swinderman, P.E., is CEO emeritus, Martin Engineering, and Daniel Marshall is a process engineer at Martin Engineering.
Comments