Overland conveyors go the distance

In the world of bulk material handling within a mining operation, clients have options at their disposal with regards to how best to transport a product from point A to point B. These options are often evaluated and traded off against each other at the early stages of a project and aspects that are often considered include (but not limited to) the following:
1 the value of the product,
2 the amount of material to be transported,
3 the physical area (mountainous, swamp, urban, through an industrial complex, etc.) of the proposed routes,
4 budgets,
5 distance (e.g., 10 km versus 500 km),
6 environmental impacts (noise, visual, dust, etc.),
7 expected timelines,
8 safety (e.g., trucks having to pass through or close to rural villages or going downhill), and
9 future capacity
For the purpose of this article where the focus is to share with those in the industry some of the world records (in length) with regard to “overland conveyors” but limited to cable belts, trough belts, and pipe conveyors, as these types of conveyors can be included in the term “overland conveyor”, and as such, are the major contenders for claiming the title of the world’s longest single-flight conveyor.

Multi-flight versus single-flight conveyors
A conveyor flight is a single conveyor section, from the tail end loading chute to the head end discharge chute. A multi-flight conveyor is a string of single-flight conveyors in which the discharge from one conveyor loads the next conveyor in line. There are many multi-flight conveyors in current operation whose total combined length exceeds 80 km. The longest multi-flight conveyor system on record is the 98 km Bu Craa conveyor in Morocco and Western Sahara, and there are currently several systems of similar length under construction around the world. However, none of the individual flights in these conveyors are as long as the longest single-flight conveyor.
Cable belt conveyors
In a cable belt, the belt is relatively flat, supported by external cables that run on sheaves.
Currently holding the world record for the longest single flight conveyor in the world is the 31-km long flight of the 51-km cable belt conveyor system at the Worsley Alumina mine near Boddington, WA, Australia. This conveyor was designed and built by Cable Belt Conveyors in 1982. Cable Belt has since been acquired by Metso.
Trough belt conveyors
A trough belt runs on a cradle of idlers that bend the belt into a trapezoidal trough, allowing it to hold more material in a narrower cross-section than that used for an equivalent capacity cable belt and to negotiate tighter horizontal curves. The steel cables that support the belt are sandwiched between the top and bottom covers of the belt, where they are more resistant to corrosion. The second longest single-flight conveyor in the world is a trough conveyor installed at SASOL’s Impumelelo mine in Secunda, South Africa. It is the longest single-flight troughed belt in existence. Designed by CDI and built by ELB, it transports up to 2,500 t/h of coal to a processing plant that converts the coal into diesel fuel.

Pipe conveyors
Pipe conveyors are sometimes referred to as tubular belts, probably to avoid confusion with pneumatic conveying systems that use steel pipe. A pipe conveyor uses a belt construction similar to the troughed belt, but in between the head and tail pulleys, where the belt is flat, a set of six idlers force the belt into an enclosed pipe shape. This prevents the egress of material, which reduces material loss and environmental impact due to spillage and windborne particulates and prevents contamination of the transported material by rainwater and other external sources. Due the higher idler friction, the pipe belt generally has a operating power cost that is approximately double the power cost of a troughed belt with the same capacity, but can negotiate much tighter horizontal and vertical curves, which can significantly reduce the capital expenditure cost of the conveyor right-of-way. The longest pipe single flight pipe conveyor is part of the Hebi conveyor system at the Hebi Coal mine, in Henan, China. Known as Yubei B, it was designed by CDI and built by HHI. It is 15-km long and carries 1000 t/h of coal per hour.
International conveyors
Not specifically a “type,” but a geographical and political circumstance, an international conveyor crosses national borders. The 61-km multi-flight Bu Craa conveyor mentioned above crosses a disputed border between Morocco and Western Sahara and could be considered by many to be an international conveyor system. However, the longest single-flight conveyor that crosses an international border runs 17-km from Meghalaya, India, to Chhatak, Bangladesh. Designed and built by Larsen & Toubro of India for Lafarge Cement, it carries 960 t/h of either limestone or shale used to produce cement for construction projects in Bangladesh. Both of these conveyors are trough conveyors.
World’s longest single-flight conveyors
Table 1 provides a comparison of the current world record holders for overland conveyors of each type. These records were made by moving stone but are not carved in stone. Somewhere, right now, someone is working on the next record-breaking project.
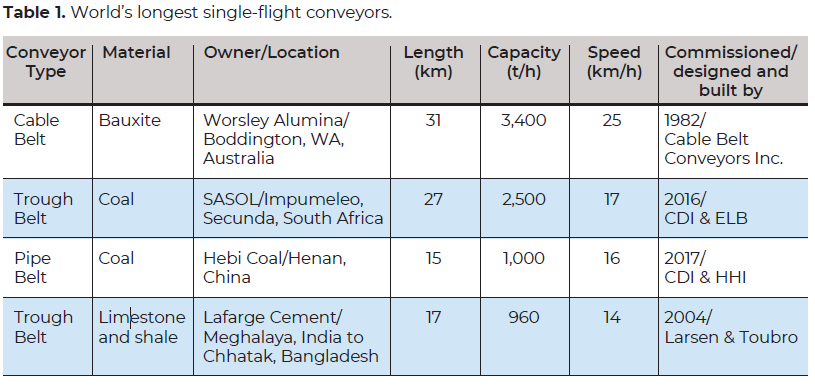
Physical and carbon footprints
A frequently asked question is why conveyors? Why not trucks or trains?
The answer is in footprints, both physical footprints of the roadbeds and structures required to support them, and the carbon footprint created by the act of transporting the material.
Physical footprints are the widths and depths of the roadbeds needed to support the load. A typical conveyor, including its parallel maintenance access road, takes up about half the space that a two-lane highway would. In the case of elevated conveyors, even maintenance access can be accommodated as part of the elevated structure. No wide roadbeds required; no deep, multi-layered road surfaces are required to cope with the concentrated axle loads. In addition, conveyors can take steeper slopes than rails, for a more direct path from point A to point B than is possible with trains. While trucks can handle steeper slopes, they require thicker pavement to support the concentrated weight of the load and the vehicle. Capital costs and physical alteration of the environment can be significantly reduced, especially if there is not already a road or a rail line in existence, as is frequently the case.
Carbon footprints can be envisioned by comparing the capacities of the conveyors listed above with the capacity of the largest bulk resource haul trucks allowed on the major highways of the western United States. There are a lot of lesser highways in the U.S. and around the world where this truck cannot go due to weight restrictions on roadbeds and bridges. The 10-axle resource hauler, shown in the image below, has a maximum allowable weight of about 58,513 kg GVW (gross vehicle weight). Approximately 44% of this GVW, or about 25,628 kg is the weight of the vehicle. The net weight of the transported material is about 32,885 kg or 33 tonnes.
The Chhatak conveyor can load 29 of these trucks every hour. The Boddington belt can load 103 of these trucks every hour. Imagine if you will, adding 30 to 100 of these huge semi-trucks every hour to the traffic flow along your current work commuting route, and then imagine this same traffic running through 17 to 31 km (or more) of rugged Australian outback, virgin Amazon rainforest, heavily populated clusters of Bangladesh or Chinese villages and fields, or any busy industrial seaport anywhere in the world.
These trucks return empty, burning 44% of the fuel required for a fully loaded truck. The empty return side of a conveyor belt returns automatically at a cost of approximately 20% of all the energy required for the transport process. Even if the operating fuel cost for the loaded trucks can be brought down to equal the operating electric power cost to move the loaded side of the belt, the empty return belt power represents 50% or better savings in the return trip energy cost.
Michael E. Thompson, P.Eng. is a senior mechanical engineer at Conveyor Dynamics Inc.
Comments