Observations about SART plant costs
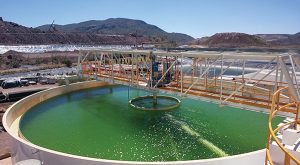
Gypsum clarifier showing the clean overflow of the neutralized leach solution ready for use in the gold extraction circuit. CREDIT: BQE WATER
As the modern gold mining sector tries to avoid the depletion of metal reserves, the importance of complex gold deposits are increasing. These deposits are characterized by elevated content of cyanide soluble metals such as copper and zinc, which increases cyanide consumption and destruction costs. As a result, additional steps in the metallurgical flowsheet are required to maintain gold extraction efficiency.
One tool available to the industry to manage these interferences is the SART (Sulphidization-Acidification-Recycle-Thickening) process. Although SART was developed more than two decades ago, the common perception is that SART is uneconomical to make it broadly applicable. To provide insight into the true costs of SART, we would like to share our experiences from our involvement in the design, construction, commissioning and ongoing operation of several large-scale SART plants and multiple feasibility studies assessing SART integration into different metallurgical circuits.
SART plants are perceived as too expensive
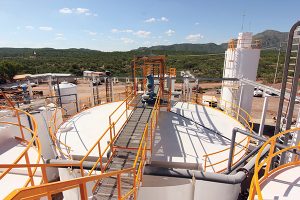
Enclosed clarifier where copper precipitated from the leach solution is settled and filtered to produce a high-grade copper concentrate with commercial value. CREDIT: BQE WATER
When plants are designed based on inaccurate criteria or by parties with no direct SART operating experience, the result can be a large plant that is expensive to operate. From our experience, the following are key to keeping SART costs down:
- Involving professionals with direct SART design and operating experience from the early stages of the project, including the initial metallurgical test work;
- Understanding the orebody by including base metals in geological and mine planning models to establish the base metal loading over the mine life and making appropriate provisions in the metallurgical flowsheet; and
- Planning carefully through all aspects of integrating SART into the existing metallurgical flowsheet.
Importance of project continuity
Maintaining a direct line of continuity from design through to operations will ensure that the design intent is fully realized when the plant is operating. Process design, control philosophy and SCADA programming are crucial to the final plant size and performance. Multiple party involvement can lead to disconnects and an overdesigned and costly plant. In worse case scenarios, the plant may never reach the target metallurgical performance or even create negative impacts on the downstream metallurgical processes.
Settling characteristics of sulphide product
SART removes the metallurgical interference of base metals by liberating them from cyanide and precipitating the metal as an insoluble sulphide product. The ability to design a system that produces a high-grade sulphide product with good settling and filtration characteristics in operations has been challenging.
Achieving success with this aspect of SART will allow for a small clarifier which reduces plant capital costs.
Gypsum slurry management
The acceptance or use of the SART gypsum slurry elsewhere within the mine site will determine whether dewatering is required. Since the tonnage of gypsum production in SART can be significant and gypsum dewatering and subsequent filter cake handling can represent a major ongoing operating cost, the elimination of gypsum dewatering can create significant life cycle cost savings.
Location & pre-fabrication
These factors contribute directly to SART installed costs.
Plant location, particularly the remoteness of the site and the country in which it operates, will impact on-site labour rates, shipping costs and the need for a building enclosure. Utilizing skidded equipment and/or modules built at the nearest major transportation hub can help reduce costs. The degree to which pre-fabrication of plant components are used will accordingly shorten fabrication and install schedules, while also reducing costs associated with shipping to site and on-site labour.
SART, when applied properly to the processing of complex gold ores, can yield many benefits. We have worked on SART projects from start to finish and we have also been asked to step in to help improve performance of SART plants designed by others. From these experiences, we hope we have shed some light on SART plant costs.
BRENT BAKER is the manager of process engineering at Vancouver-based BQE Water. He can be reached at bbaker@bqewater.com.
Comments