Next generation low-cost technology for high-performance batteries

Li-Metal’s founders, Maciej Jastrzebski and Tim Johnston, recognized that rapid electrification of transportation, and the adoption of next generation high-performance batteries (solid-state, lithium-sulphur, lithium-air, etc.) will require a vast expansion of lithium anode and lithium metal production.

Li-Metal’s CEO
Leveraging their respective engineering expertise in the metallurgical and lithium chemicals industries, they founded Li-Metal in response to this need.
Since its inception in 2018, the company has made dramatic progress in developing patented and patent-pending technologies that will allow the lithium anodes and lithium metal needed by next generation batteries to be produced from widely available feedstocks, at scale, and at a fraction of the cost of the conventional processes.
As the world moves away from oil-based fuels and toward renewable energy sources and battery-powered technology, the need for new lithium batteries and lithium foil anodes has become more prevalent.
Recently, I caught up with Li-Metal’s CEO, Dr. Srini Godavarthy (SG), to discuss the progress made by Li-Metal in the pursuit of next generation technology.
CMJ: As a conversation starter, could you please talk to us about the history of Li-Metal, your background, and how you became CEO?
SG: Li-Metal Corp. was founded in 2018 by Maciej Jastrzebski and Tim Johnston to address an emerging and prevailing underlying trend in the electrification of transportation – the transition from conventional lithium-ion batteries to next generation high-performance batteries, such as solid-state, hybrid liquid electrolyte, and lithium-sulphur. Tim and Maciej met at Hatch, one of the foremost engineering companies in Canada. Tim is a serial entrepreneur in the lithium space, and Maciej brought the technological innovation – what started out as a series of interesting lunchtime and coffee chats in Toronto, quickly gave birth to the concept for Li-Metal, which was technically developed and economically evaluated over the subsequent few months.
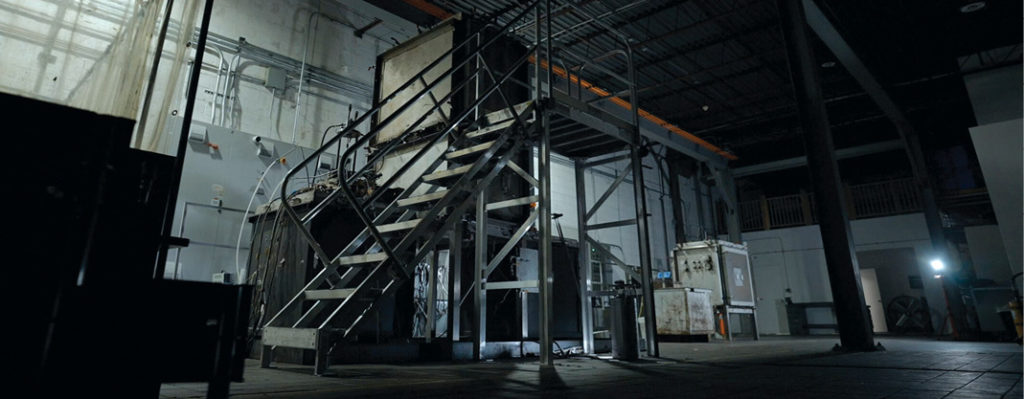
Fast forward to present day, Li-Metal is working at the forefront of the next generation battery supply chain, developing and commercializing production technologies to help produce lighter, cheaper, cleaner, and better-performing batteries for electric vehicles (EVs) and other transportation applications, such as electric aviation. We are working to become a leading domestic battery anode supplier to battery developers and automotive OEMs (original equipment manufacturers). We believe our ultra-thin high-performance anode materials for next generation batteries will play a key role in unlocking the future of electric transport.
Our vertically integrated process begins with lithium carbonate and ends with cost-effective, high-performance anodes ready to go into next generation battery cells utilizing two core technologies: a lithium metal technology and a next generation battery anode technology. We are currently engaged with 27 automakers and battery developers, with 15 leading next generation battery developers actively sampling our anode materials, as we continue to strengthen relationships with key players in the next generation battery ecosystem. We have also secured a recurring commercial order for our anode materials, which in addition to generating revenues provides us with the opportunity to further validate our products and advance our anode business.
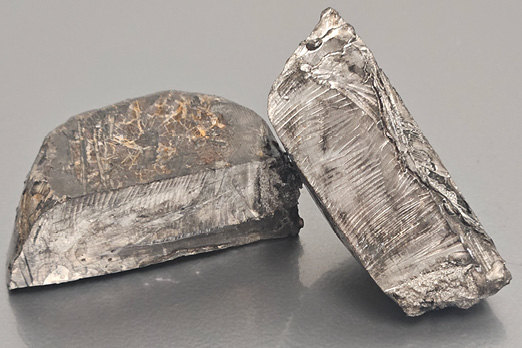
Li-Metal has an advanced anode pilot plant in Rochester, N.Y., capable of producing thousands of metres of anode material per year and a lithium metal pilot plant in Markham, Ont. At the same location as our lithium metal pilot plant, we also house an advanced anode lab and our corporate offices.
When I joined as CEO of Li-Metal earlier this year, I was confident in the opportunities in front of the business as we develop ground-breaking solutions that will shape the next generation of batteries. I hit the ground running as on my first day of the job we were granted our first patent for our lithium metal technology. In terms of my background, I bring more than two decades of commercial and operational experience with a specialization in chemicals and lithium battery materials.
Before joining Li-Metal, I led the lithium metals and specialty salts business at Albemarle Corp., the world’s top lithium producer. I started out my career at Huntsman International as an engineer and have always had a passion for chemicals. I earned my Ph.D. in chemical engineering from Oklahoma State University and my MBA in Finance from Colorado State University.
For some background for how I got to Li-Metal, Maciej, Li-Metal’s previous CEO and now our CTO, recognized the benefits of installing a CEO to lead the company through its next phase of growth while he focused his efforts on leading the innovation, product development, and R&D, which is core to the success of any technology enterprise. I am really excited about the road ahead as we look to reach commercial scale anode production capabilities as soon as 2024.
CMJ: Conventional lithium anodes are made of lithium foils, can you please explain why this is a problem, and what is the solution offered by Li-Metal’s technology to this problem?
SG: Before Li-Metal, the existing technologies for producing next generation anodes faced significant challenges, as conventional anodes are typically made by extruding and rolling lithium metal into thick foils.
To increase the penetration of EVs, the industry is focused on attaining cost parity compared to internal combustion engines (ICE). The battery plays a significant role in this, and the industry is targeting battery costs of $100/kwh. In Li-Metal’s experience and discussions, many of our customers are focused on the goal of getting to cost and performance parity (range) with ICEs. However, given the cost of lithium metal, the use of thick lithium foils as anodes makes their technology more expensive.
A core challenge with foil extrusion, as a production method, is that it is difficult to scale, especially as the foil gets very thin, a critical requirement to reduce the cost of anodes. Furthermore, because it is difficult to customize the thickness of foils, the energy density (and the range of the vehicle) is reduced. To add to all these challenges, excess lithium in the battery, because of combining traditional cathodes with thick lithium anodes, contributes to increased risk of a fire, impacting safety requirements.
Li-Metal is focused on solving these challenges with our innovative roll-to-roll PVD (physical vapour deposition) anode technology. PVD is a ubiquitous technology, and anything that looks metallic but made of plastic is likely made from a PVD process, such as the shiny metallic coating inside a bag of potato chips. This technology, in other industries, has been able to produce millions of square metres of low-cost materials for decades, and we are applying this proven technology platform to produce advanced anode materials for the next generation battery industry.
Technically speaking, we use a one-pass double-sided roll-to-roll deposition approach as micron-scale material starts on a substrate roll, unwinds, then passes through a treatment zone where lithium metal (which we plan to produce ourselves) or a combination of materials is deposited. This is then collected on the product roll, to produce the final anode product, which can be used directly in new battery cells. In other words, using a vacuum environment, we apply vaporized lithium metal on a copper substrate to build these anode materials from the “bottom up.”
Using our PVD approach to anode production is the opposite of the traditional approaches, as instead of squeezing, flattening, or pressing a piece of lithium metal down to the thickness we want, we build it up by depositing it directly on a copper substrate. By building these lithium metal films from the bottom up, we minimize the amount of lithium metal used in our process, which reduces excess lithium to improve safety. This also increases the cost effectiveness of our process by limiting waste of a highly valuable feedstock. Not only does our process allow us to minimize the amount of lithium used, but it also allows us to co-deposit other materials to enhance the performance of our anode materials, as we eliminate the need for graphite in battery anodes.
At our advanced anode pilot plant in Rochester, we have proven our ability to produce lithium metal anode products with lithium thickness between 3 and 25 micrometres, as we continue to customize our offerings to meet customer demand. Furthermore, through our work in Rochester, we believe we are operating one of the highest intensities PVD lithium metal anode processes in the industry. In other words, we believe our PVD process operates at an unmatched efficiency rate in the next generation battery industry. As of June 2023, the team has produced more than 5,787 metres of sample lithium metal anode material, compared to 4,200 metres in 2022.
We believe our work with PVD technology is just getting started, as this highly flexible technology platform can be upgraded to accommodate unique combinations of materials to optimize cost and electrochemical performance, unlocking a suite of future product development opportunities.
As we continue to advance our anode business, my short-term goal for Li-Metal is to approach 0.5 GWh of anode capacity as quickly as possible, or the equivalent of 4 million to 5 million m2 of anode material per year. To support the growth of our anode business, we are evaluating options for the best location for a future anode facility in addition to government incentives to help us scale up faster to meet accelerating customer demand.
CMJ: So, what are the advantages of Li-Metal’s new technology?
SG: Li-Metal’s vertically integrated technology platform offers many distinct advantages for producing high-performance anode materials compared to traditional and alternative methods on the marketplace.
First, our ability to produce lithium metal ourselves is a key differentiator for our business, as it enables us to secure a reliable and sustainable domestic supply to feed our anode operations. Traditionally, lithium metal has been produced using lithium chloride as feedstock, which generates approximately five tonnes of harmful chlorine gas by-product for every tonne of lithium metal produced. Lithium chloride is typically made by treating lithium carbonate; however, Li-Metal’s patented carbonate-to-metal lithium metal technology can eliminate this costly conversion step by producing metal directly from lithium carbonate. Of note, to our knowledge, conversion capacity to produce lithium chloride from carbonate is limited, and significant capital investment would be required to meet the added demand for lithium metal. Given past experience in the lithium industry, these types of expansion projects could take at least four to five years from design to production. This means that it is highly unlikely that traditional lithium metal production processes will be able to be scaled up quickly to meet the growing needs of the next generation battery industry in North America and Europe.
With the demand for lithium metal expected to increase by 10 to 12 times to more than 40,000 tonnes per year by 2030, our cleaner, cost-effective, and energy efficient lithium metal production process that avoids producing toxic by-products will be key. We have had great momentum with our lithium metal technology as in May of this year, Li-Metal successfully produced lithium metal directly from lithium carbonate. We believe Li-Metal is the first company in the world to do this and we accomplished this metallurgical process breakthrough at our facility in Markham, Ont.
For our next generation battery anodes, as mentioned, by using our highly flexible and scalable PVD technology platform, we can produce lithium metal anodes from the “bottom up” compared to the traditional or alternative “top down” approaches. This minimizes the amount of lithium metal used in our process compared to other processes, which reduces excess lithium to improve safety and limits waste. Furthermore, our PVD platform allows us to customize our anode materials to fit the specifications of our customers, which is a key advantage, as we can be flexible to meet the unique needs of our growing customer base.
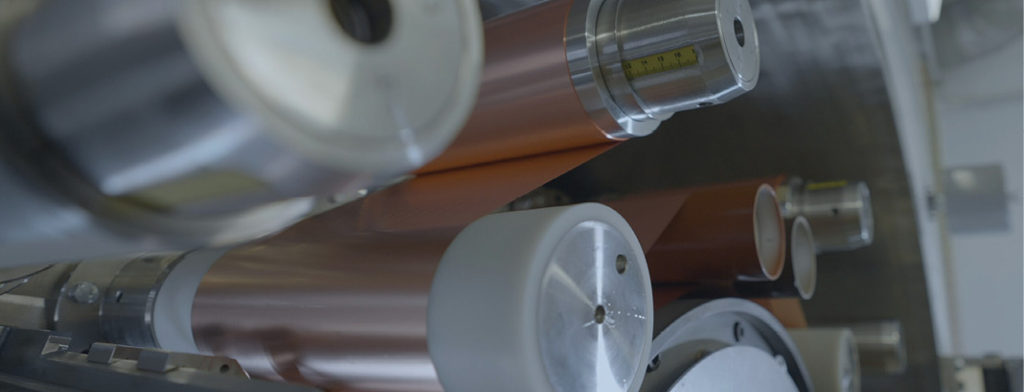
CMJ: Were you able to partner with the battery industry leaders to commercialize the technology at this point?
SG: As we position ourselves as a leading domestic battery anode supplier and battery materials innovator to the next generation battery supply chain, we continue to expand and strengthen our relationships with key battery developers and automotive OEMs. Currently, we have ongoing discussions with 27 battery developers and automakers, 15 of which are sampling our anode materials in next generation batteries to qualify our technology. We have also secured a recurring commercial order for our anode materials. As protecting our customers is a key priority for Li-Metal, currently, we have not publicly disclosed many of the names of the battery industry leaders we are working with.
We do have one publicly disclosed relationship, as we have a joint development and commercialization agreement with Blue Solutions, the largest commercial producer of solid-state batteries, to advance the development of next generation batteries. Blue Solutions, a subsidiary of the US$14 billion French conglomerate Bollere, is the largest commercial manufacturer in the market, supplying an all-solid-state lithium metal battery for real-life applications running on every continent. Blue Solutions has been working on solid-state batteries for decades, and their batteries power Mercedes Benz electric buses in Europe. The partnership combines our technologies with the know-how of a proven battery solid state battery producer to advance solid-state batteries for passenger EVs.
CMJ: Last April, Li-Metal signed an exclusive agreement with Mustang Vacuum Systems, why are agreements like this important, and what does this specific agreement mean to you and to Li-Metals?
SG: Our strategic binding agreement with Mustang Vacuum Systems for the exclusive supply of high performance PVD machines and services to produce anode materials is expected to be a key development for our anode business.
Mustang Vacuum Systems is a leading global manufacturer of industrial scale PVD equipment, and this agreement helps advance our position as the preeminent domestic anode supplier. When it comes to PVD as a technology platform, the equipment plays a key role in the productivity of the technology. Securing the right equipment and partner to support us on the manufacturing side opens the door for us to really maximize the potential of our novel roll-to-roll PVD anode technology. It is a key step in the roadmap for our anode business and enables us to continue to focus on scaling our capabilities, enhancing our technological advantage, and focus on supporting our customers with the confidence that we have the right machine building partner backing us.
Furthermore, through this strategic partnership, we expect to collaborate on additional commercial business opportunities for providing lithium-based anode materials to current and prospective customers. Mustang Vacuum Systems is also expected to become a Li-Metal shareholder, which further strengthens our alignment and collaboration.
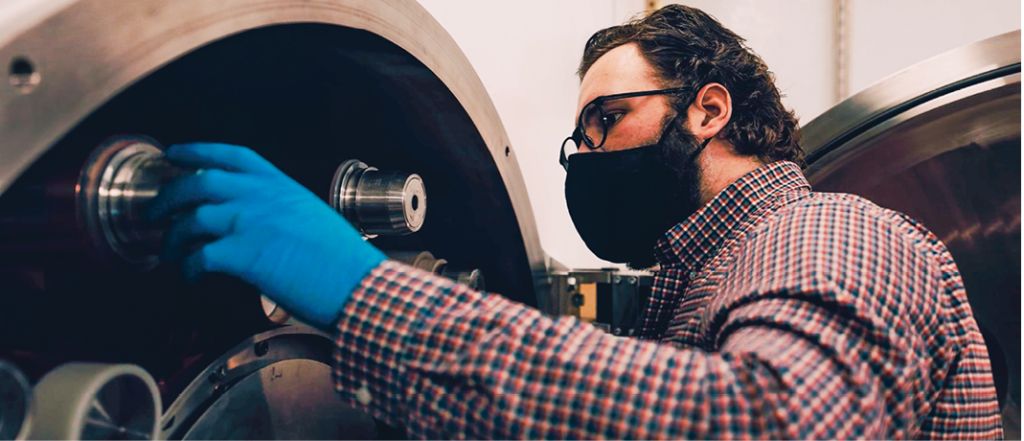
for next generation batteries CREDIT: LI-METAL
CMJ: How do you intend to use the recent $1.4 million grant sponsored by the government of Ontario?
SG: We were awarded more than $1.4 million in non-dilutive grant funding from various programs sponsored by the government of Ontario to develop and commercialize our lithium metal production technology. The funding consisted of funding from the Ontario Vehicle Innovation Network (OVIN) and the Critical Minerals Innovation Fund (CMIF).
We plan to use the funds from OVIN to support scale-up of our production and refining capabilities for battery-grade lithium metal. We will also use these funds to advance the piloting of new lithium metal products, such as specialty lithium alloy ingots for next generation batteries.
We plan to use funds from the CMIF to advance our environmentally friendly and patented lithium metal production technology to help support the development of battery supply chain in Canada.
Scaling up our metal business helps further differentiate Li-Metal in the market as a vertically integrated domestic anode supplier and helps advance the development of our anode business by securing a cost-effective and sustainably produced feedstock. The funding from the government of Ontario validates our technology and endorses the role we are poised to play in building a sustainable battery supply chain in Canada.
CMJ: Finally, how does the future of batteries manufacturing in Canada look like to you?
SG: We are pleased to see major players in the battery ecosystem set up shop in Canada, such as Volkswagen, LG Energy Solution, Umicore, and many more. Furthermore, Canada has a substantial amount of potential upstream – or the raw materials – to help create a prosperous battery supply chain. Although the Inflation Reduction Act in the U.S. has been making many of the headlines, we are excited about some of the initiatives the Canadian government has taken to support our own battery materials supply chain and the opportunities that have followed suit.
Even though Canada continues to make great strides for electrifying our transportation system, it is essential that we do not overlook the emerging next generation battery supply chain. The Canadian next generation battery ecosystem has made progress; however, the U.S. continues to maintain the highest concentration of key players. If Canada does not divert more attention towards supporting the development, and the supply chain, of these better batteries, then we will be left behind.
Not only the future of the EVs lies within these battery technologies that are under development, but also the future of transportation more broadly. Lighter and more powerful batteries are the future, and it is important that Canada starts to focus its attention on the battery supply chain of tomorrow not the current lithium-ion battery supply chain, which will eventually become obsolete. Canada is a natural leader in innovation, it is time for us to really get in the game.
Comments