A revolutionary new lubricant can prevent hydrogen wear
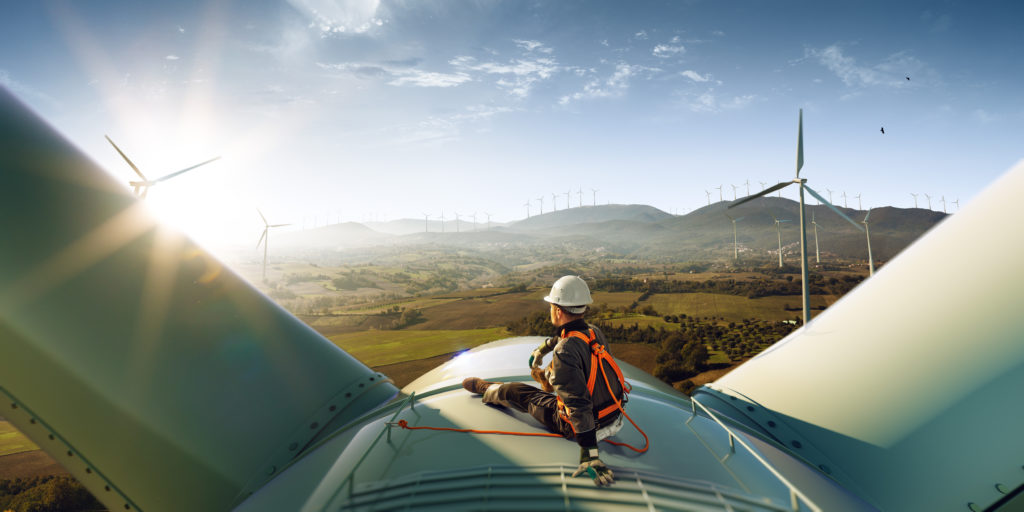
There is a widespread belief that four major wear mechanisms contribute to the damage and deterioration of industrial machine parts: adhesive, abrasive, corrosive, and surface fatigue. This report explains the presence of another no less important, if not more, mechanism that is largely underreported: hydrogen wear.
As hydrogen is the most abundant element in nature, its significance as a leading factor in the premature failure of machine components cannot be ignored. Studies have shown that at least three of the four wear mechanisms mentioned above (adhesive, abrasive, and surface fatigue) will contain the underlying effects of hydrogen wear whenever there is metal-to-metal contact with a temperature gradient, even on a micro level.
This report provides a detailed understanding of the hydrogen wear phenomenon, its causal effects in mechanical failures, and how it has presented the wind turbine industry, which is important for the green transition, with a substantial problem.
While knowledge of the hydrogen wear phenomenon is far from commonplace, what is even less known is the remarkable new solution in the guise of NEOL’s revolutionary copper filming lubricant technology. Its unique and environmentally friendly properties not only protect machine components from hydrogen wear with none of the downsides of traditional approaches such as ZDDP but also extend the lifespan and operational performance of industrial applications.
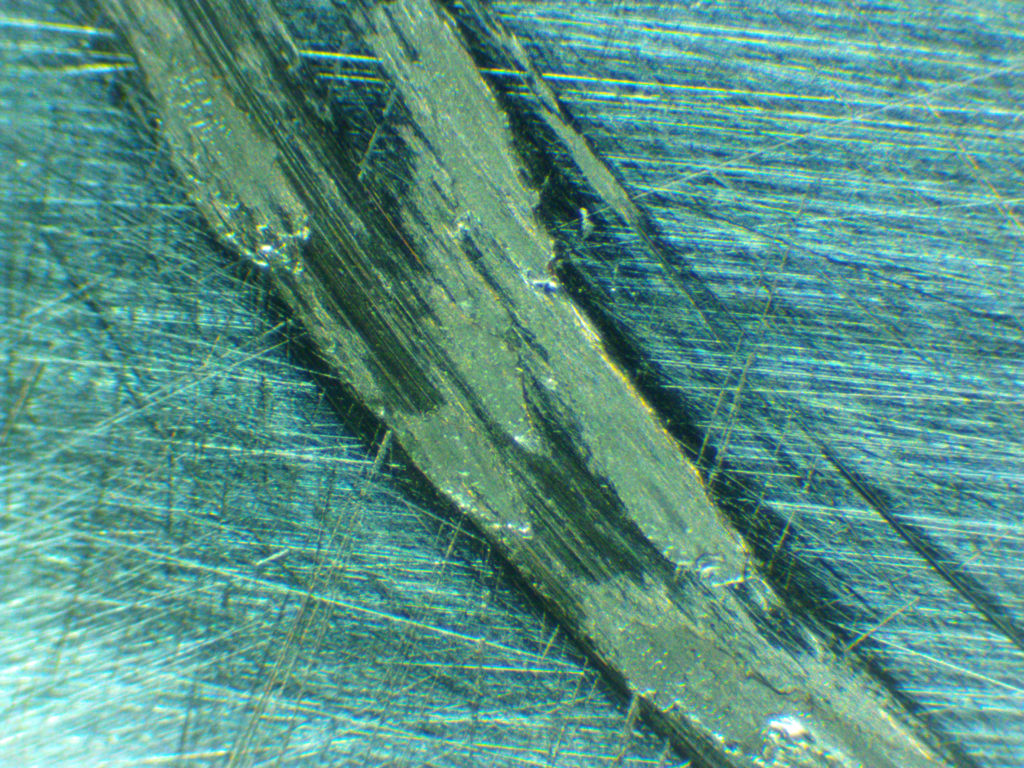
Furthermore, as emerging hydrogen technologies become a potential key source of sustainable energy solutions, this report presents a compelling case for how this revolutionary lubricant’s ability to take advantage of the hydrogen wear mechanism could have far-reaching consequences in the enablement of future technologies.
The hydrogen wear phenomenon
The wear of machinery is found in almost every industry where two surfaces meet and move against each other. This naturally occurring phenomenon is a significant cause of mechanical failure and requires extensive maintenance, time, and cost in the repair or replacement of damaged parts.
The science behind hydrogen wear can be traced back to the 1960s, when Dmitry N. Garkunov made two startling discoveries while investigating mechanical failure in aircraft’s landing gears. First, he discovered that during friction, copper ions were being selectively transferred into the crystalline grid of iron forming a thin film. Second, he found that hydrogen was the primary cause of metal surface deterioration.
These two discoveries, which were consequently named “the wearlessness effect” and “hydrogen wear of metals,” marked the beginning of a revolutionary new approach towards anti-wear protection and the potential to extend the lifespan of machine applications.
At this point, it is important to distinguish the substantial differences between hydrogen embrittlement and hydrogen wear.
The phenomenon of hydrogen embrittlement, which has been well-known for over a century, is a reduction in the ductility of a metal because of absorbed hydrogen. It usually manifests itself in terms of singular sharp cracks. This process typically occurs owing to contact in hydrogenous media and is promoted by high temperatures, atmospheric pressure, high loads and deformation, and cathodic processes. As such, hydrogen embrittlement is a common issue for steelmakers.
In contrast, hydrogen wear only occurs during sliding and rolling contacts that are found in rotating machinery such as gears and hydraulics. The high contact pressures cause a higher rate of hydrogen absorption, and therefore, an abnormally high concentration of hydrogen. As hydrogen invades the surface it increases internal pressure and causes cracks to form. Through repeated cyclic stresses, these cracks grow and eventually produce the formation of wear particles.
Unlike hydrogen embrittlement, where a different law of hydrogen distribution applies, the phenomenon of hydrogen wear creates an unusual pattern of failure.
Dr. Sergei Mamykin, a global leader in the study of hydrogen wear, defines this pattern of failure as the “self-organized destruction in the material’s top layer during friction; it is characterized by a considerable non-equilibrium of processes and by joint impact of co-factors that contribute to absorption of hydrogen in the top layer and destruction of this layer.”
Additionally, if hydrogen is adsorbed on the friction surface and driven by a temperature gradient, it can diffuse deep into the surface and concentrate there, making the top layers fragile and provoking more intense deterioration.
Factors that determine the intensity of hydrogen absorption include the composition and state of the medium, the treatment of the metal surface, its chemical composition, its atomic structure, its stresses and deformations (in particular, deformations of the metal lattice which raises its energy level), the hydrogen saturation time, and the conditions of hydrogen desorption from metal.
Further research has shown that hydrogen wear has increasingly become a significant factor in the wear of machine parts in a vast array of industries, including mining, transportation, aviation, farming, chemical production, and microbiological production equipment.
Another significant factor is that hydrogen imparts higher fragility to products of hardened steel, especially those used under alternating loads such as crankshafts, piston rings, cylinders of internal combustion engines, and bolted joints.
In some cases, hydrogen impact during friction determines the service life of the friction part. This last point has significantly changed our understanding of the nature of friction and wear. The thermal, electrical, and magnetic effects of friction, all of which control the hydrogen concentration in metals, are now proven to be factors that determine deterioration.
Additionally, during desorption and lubrication, hydrogen can occupy numerous adsorption centres and enters the top layer in much larger quantities — its concentration in steel rises rapidly to a level above equilibrium. At the same time, defects become more numerous with deformation. This effect will go on until internal pressure finally causes the destruction of steel along all emerging and interconnected cracks.
While hydrogen wear is not as well-documented as hydrogen embrittlement, it is no less important in understanding how hydrogen invades the metal surface of machine parts, and how this invasion leads to premature failures.
Hydrogen wear gearbox failures in wind turbines
When metal surfaces connect with each other, they generate heat and pressure, causing particles to separate. This provides gaps that allow hydrogen atoms to infiltrate the metal, pushing out its own particles and causing the deterioration of machine parts.
An example of this can be witnessed in the wind turbine industry. Mechanical wear in large multi-megawatt (MW) wind turbines has become an increasingly serious issue over the last decade. Investigations have found widespread gearbox failures in wind turbines that have occurred in less than five years of operation, so much so that operators now consider it the single most expensive failure mode for all wind turbine components.
This is a serious problem. The global wind turbine sector is growing exponentially. In 2022, the Global Wind Energy Council forecasted 1,221 GW of new capacity to be built worldwide from 2023-2030, yet there is already talk of a “graveyard of gearboxes” in the wind turbine sector.
Research is ongoing to determine the causes of this high failure rate, but it is generally concentrated on the amount of energy required to remove hydrogen ions from either water or from the base oil. When one considers the sheer size of turbines, the amount of torque that goes through their gearboxes, and the power that flows through their blades, the energy is extreme.
Consequently, cracks have appeared on the inner ring of high-speed shafts and high-speed intermediate shafts of bearings. If left ignored, these cracks will extend to the gearbox itself and eventually lead to premature failures.
When examining this phenomenon closely, researchers concluded that three factors appear to be working together: non-metallic inclusions, sliding, and hydrogen. However, as the wear phenomenon occurs below the surface, it is impossible to detect with the naked eye, and by the time it reaches the surface, the damage is done.
Researchers have called this phenomenon “white etching cracking” (WEC), and although they agree that its exact cause remains unclear, many suggest that lubricants may play a significant role.
Tellingly, their description of WEC is near-identical to the description of hydrogen wear.
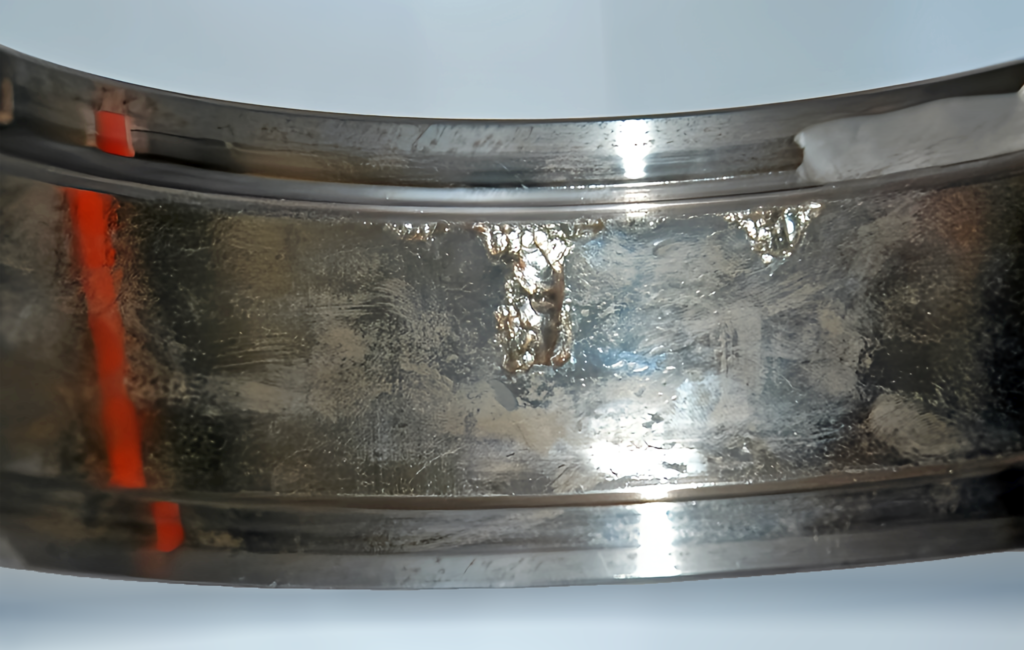
A 2020 report by ExxonMobil speculated on the activity of hydrogen in the subsurface zone and concluded that it was most likely the result of a complex interaction between several mechanical, electrical, operational, and chemical factors. Even so, the report admitted that “the scale of this tribochemical reaction — the chemical changes that occur to a lubricant and a lubricated surface when separated by a thin tribofilm, generated as a result of interactions between lubricant additives and lubricated surfaces — is not well-understood.”
Thorsten Süling, European EB/OEM manager of ExxonMobil, posited that “it is possible to select gear oils that do not contribute to the phenomenon.”
Given the fact that many wind turbine gearboxes are not achieving their expected 20-year design life, and around 60% of the industry’s gearbox failures are caused by the WEC phenomenon, it is unsurprising that wind turbine operators and OEMs are conducting extensive investigations on how to fix the problem.
A method of protection from hydrogen wear
The research conducted into the hydrogen wear of metals and the wearlessness effect has long concluded that evolutionary discoveries of “the wearlessness effect” and “hydrogen wear of metals” simply identified the cause of two different phenomena; that is, why ions are transferred in the process of friction and what causes metal surfaces to deteriorate in machines.
However, by combining these two discoveries together, the double detection of the wear-free effect and the hydrogen wear in tribological engineering uncovered both the cause and solution for mechanical wear.
Dr. Sergei Mamykin, who has been developing revolutionary copper filming technology for more than 30 years, defines the wear-free effect as “a type of friction that can be described as a non-oxidizing thin metal film (servovite film) that emerges spontaneously in the contact area; the film possesses low shear resistance and cannot accumulate dislocations through deformation. On top of this film, an additional protective film (surf film) can be formed, entering in a chemical bond with it; the latter film is made of degradation products left from hydrocarbon lubricants.”
Furthermore, as friction units are manufactured, Mamykin found that the selective transfer effect helped to reduce their weight and dimensions by 15% to 20% thanks to greater load capacity of their friction pairs, and to significantly increase the efficiency of respective machinery while simultaneously reducing consumption of energy, increasing reliability, and extending the service life and overhaul periods of these machines.
In operational terms, this would allow operators to significantly decrease the costs of labour, time, and energy spent on maintenance and repair.
Lubricant additives based on copper ions (Cu2+) have been widely known for more than five decades. Professor Garkunov, who first discovered the hydrogen wear of metals, discovered the effect of friction and wear reduction by copper films, and that layering occurs when the copper particles were compressed between two friction bodies.
Garkunov and other researchers also found that the copper film does not oxidize, and material can be transferred to the counter body. Consequently, a copper–copper sliding interface is formed.
The effect of wear reduction by copper tribofilms has been demonstrated by many experiments, including both tribometers and real applications. In 2016, scientists led by Matthias Scherge at the MicroTribology Center in Karlsruhe, Germany, added copper ions as an additive to fully formulated engine oils. The copper additive was in colloidal form, with an inner core of Cu2+ atoms covered by surfactants to form stable reverse micelles that are completely dispersible in the base oil. The tribological performance was then investigated using atomic force microscopy, a microtribometer, a pin-on-disk tribometer in combination with continuous and high-resolution wear measurements with radio nuclide technique, and high pressure stressing in a thrust roller bearing test rig.
The results were revelatory. First, laboratory tests and tribological investigations confirmed that this innovative stable copper additive delivers long-lasting reduction in friction, protection against wear, and extended service-life. Second, the mechanism and function of copper tribofilms involved a three-step process: an instantaneous reduction in the coefficient of friction, the formation of a solid lubricant composed of copper monolayers, and plastic flow of the copper tribofilm combined with mechanical intermixing and tribochemical reactions.
Furthermore, near surface polymerization of monomers from the base oil led to a protective top layer that helps to shift the systems towards hydrodynamic lubrication and prevents further attacks of oxygen.
The test results provided additional proof of “self-sustained friction reduction and wear protection.” Building on the work of Garkunov and other researchers, the following conclusions were reached:
The protective and friction-reducing action of copper-based additives can be extended to the tribological regime at ultra-low wear rates.
When severe wear is examined under artificially extreme four-ball machine test conditions, thick films are necessary to protect the surfaces; while in real-world and representative ultra-low wear regimes, thin films provide sufficient protection.
Copper filming technology: From research to reality
Friction is often only associated with the process of wear, but when paired with the selective transfer of copper ions, it becomes an evolutionary process and, as a result, the destruction of surfaces becomes secondary.
Owing to the exchange of energy and matter between the friction surface and the external environment, as well as the collective behaviour of copper ions, the developmental nature of friction is revealed in the form of a thin copper film that coats the metal parts, protecting the friction surfaces from wear. And because friction creates a protective film, it can no longer destroy it. Simply put, the system has become self-organizing.
This is where NEOL’s unique copper filming technology comes into play. This revolutionary lubricant technology can solve the issue of hydrogen wear while lowering friction and reducing other mechanisms such as adhesive, abrasive, and surface fatigue wear. As soon as hydrogen finds metal-to-metal contact, it starts causing wear, but rather than allowing uncontrolled hydrogen invasion to the friction surface, NEOL’s additive technology first uses its properties to “polish” the friction surface at the elementary level. The hydrogen wear is then terminated with copper ions. Copper ions are embedded in the crystal lattice of iron or iron-containing alloys, thereby “healing” damaged areas. They gradually form an even copper film covering an entire surface, at which point, continued hydrogen wear and other wear mechanisms will virtually cease.
This results in a significant increase in the efficiency and longevity of machinery — iron being the most abundant metal in machine components — while substantially decreasing expenditure on maintenance and replacements, plus a considerable reduction in fuel consumption. Additionally, copper filming technology means there is no longer a dependence on toxic phosphorous and sulfur compounds which have traditionally been used as anti-wear agents by the global lubricants industry, mainly as ZDDP (zinc dialkyldithiophosphate).
ZDDP has been the world’s most popular lubricant oil additive since it was patented in 1944. Cheap to produce, its multifunctional additives are used in engine oils, transmission fluids, hydraulic fluids, greases, gear oils, and many other applications. While commonly known as zinc, it is the phosphorus and sulfur compounds in ZDDP that do all the hard work in reducing wear and controlling oxidation.
However, while ZDDP has been proven to extend machine longevity, its negative effects on the environment have become a critical issue. Additionally, zinc-induced neurotoxicity has been shown to play a role in neuronal damage and death associated with traumatic brain injury, stroke, seizures, and neurodegenerative diseases.
In stark contrast, NEOL’s proprietary additive package is based on oil soluble organic copper salts. This unique composition contains ultra-low to no SAPS (sulfated ash, phosphorus, and sulfur) and does not require a high base content. As a result, used NEOL oil is easily recyclable and, in some cases, fully biodegradable.
NEOL’s additive is also a highly effective detergent keeping machines free of the sludge deposits and varnish that plagues modern engines, compressors, turbines, and hydraulic systems. This makes it an environmentally friendly alternative and completely safe for use with modern catalytic converters and diesel particulate filters.
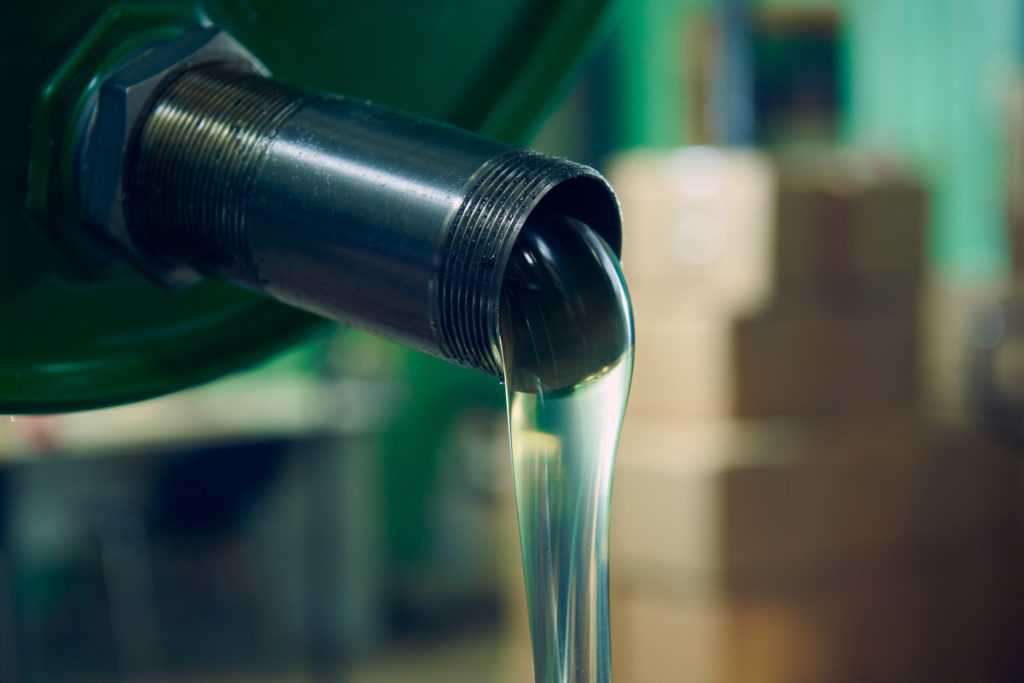
Mining applications
To prove the effectiveness of its unique properties, NEOL evaluated the performance of CuGlide powered oil formulation packages in a series of real-world applications. One test study involved a one-year trial of full-synthetic ISO VG 220 industrial gear oil in a well-worked Sandvik CG820i gyratory crusher during mining operations. Phase one consisted of a 1,500-hour pilot test. This was followed by a second phase of using the industrial gear oil in the crusher for more than 5,000 hours to test the longevity of its lubrication and cleaning properties.
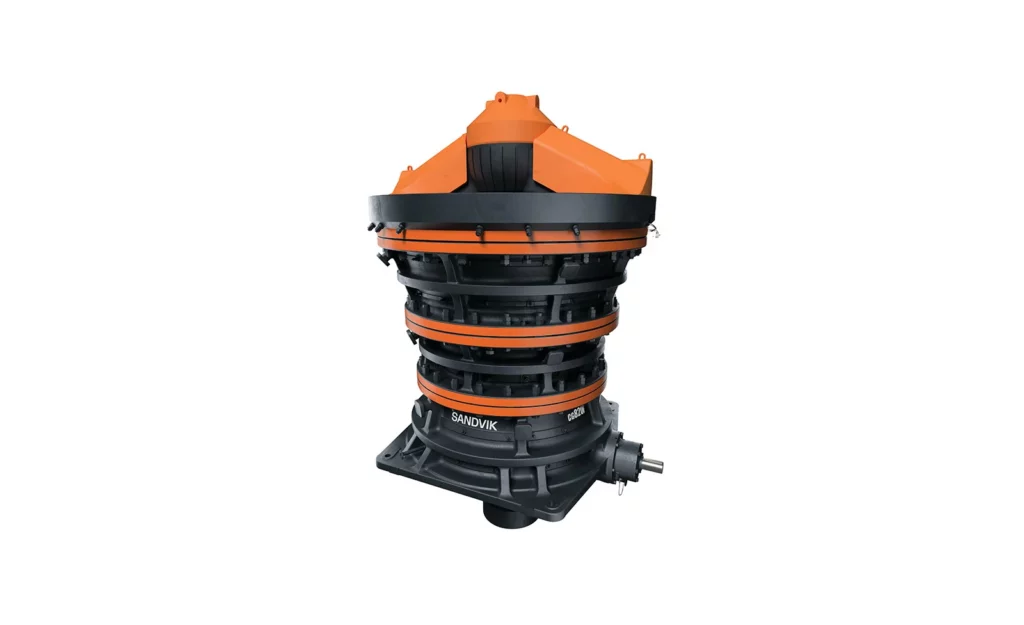
It was important to have two extensive testing phases to fully evaluate the oil’s performance on the 244-tonne gyratory crusher, which had a 525-kW motor, a 1,200-L oil charge, and was capable of processing up to 4,000 tonnes of material an hour. It also allowed NEOL to appraise the viscosity, acid control, wear protection, and the detergency properties of the oil under long-term, heavy in-service conditions.
The one-year field test delivered exceptional results. The industrial gear oil proved to have excellent viscosity control at 40°C and 100°C while also offering thermal and oxidative stability. There was no increase in in-service oil acidity, with the lubricant providing oxidation and corrosion protection, and no degradation in performance.
The gyratory crusher’s gear parts that were subjected to high load, stress, and hot temperatures did not wear during contact. Additional oil analysis also showed there was no iron, chromium, or nickel detected. The lubricant helped to effectively clean the gyratory crusher’s gear parts and restore efficiency, as previously immoveable remnants and engine debris were washed out. Furthermore, during the pilot test phase, there were six filter changes that revealed particles of metal and bronze shavings also washed out of the crusher.
Overall, the industrial gear oil delivered a robust level of protection, worked as a detergent, and offered long-term lubrication. This allowed operators to run the equipment more efficiently while saving on maintenance costs.
Another test study involved a 500-hour standard service interval field trial on three CAT 777E haul trucks equipped with Caterpillar C32 V-12 engines in an open cast mining operation.
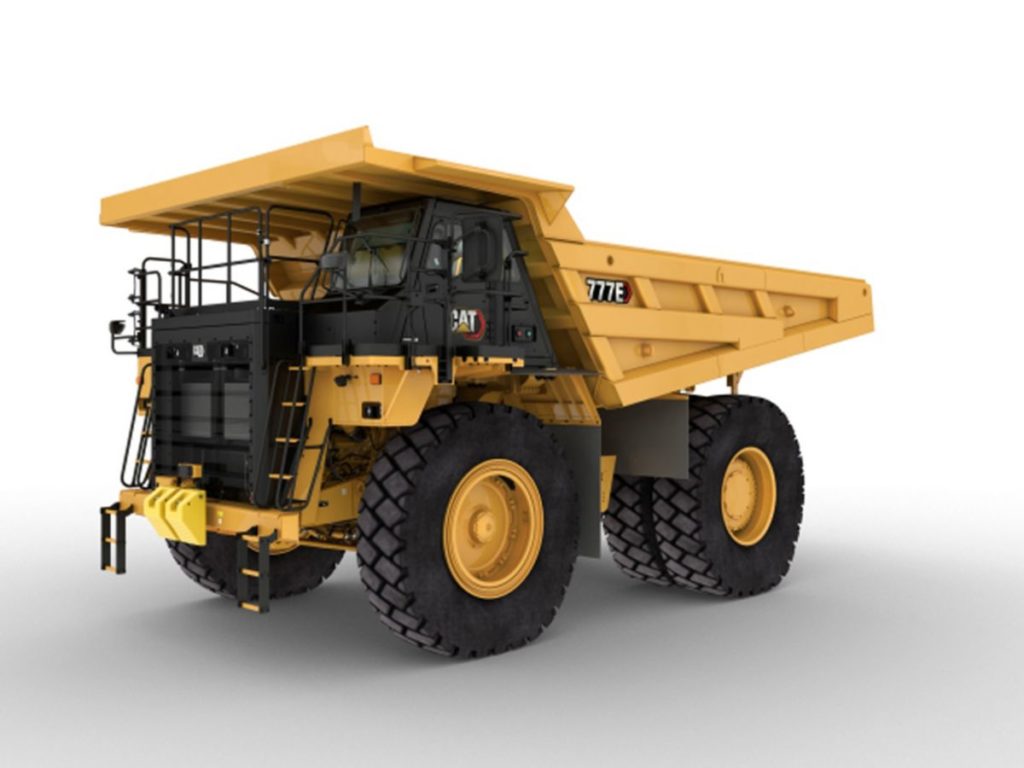
The objective was to assess engine lubricant performance and quantify operating savings, particularly in fuel consumption, for mining operators. Additionally, the innovative formulation aimed to solubilize and remove harmful deposits, repair engine wear, and extend engine life, thereby reducing total cost of ownership (TCO) and enhancing productivity.
The trial deployed CuGlide powered no-SAPS synthetic 10W-40 HDDEO formulation in the three trucks, with each vehicle having accumulated 28,000 to 33,000 hours of service. The lubricant consisted of a unique blend of additives, including a highly concentrated additive package (~300 ppm copper), performance polymers, pour point depressants, and a mix of API Group-III, PAO, and ester base oils.
Previously, the trucks had been using a market-leading SAE 15W-40 oil with various additives. Despite satisfactory operational conditions, NEOL sought to explore the potential benefits of its unique additives in these heavily utilized vehicles.
The field trial yielded remarkable results and demonstrated the efficacy of CuGlide powered lubricant in enhancing engine performance. Oil analysis revealed minimal wear, efficient removal of lead-containing deposits, and excellent control of oxidation and nitration.
In terms of operational costs, fuel consumption data indicated potential annual savings ranging from $83,000 to $178,000 per truck, contributing significantly to reducing TCO. Drivers also reported improved vehicle acceleration and speed, highlighting the rejuvenating effects of the oil on engine components.
By delivering improved efficiency, protection, and productivity, the copper filming technology allowed operators to optimize engine performance and mitigate operational costs in harsh mining environments, indicating a radical advancement in asset management that could generate profitability for other mining operators.
Future-proofing emerging hydrogen technologies
The untold possibilities of the copper filming technology to prevent and reverse the effects of hydrogen wear and other wear mechanisms not only has far-reaching consequences for the industries of today but also extends to the emerging industries of tomorrow.
For some time now, hydrogen has been recognized as one of the most promising carriers of non-fossil energy on the pathway to net-zero. The transportation industry, one of the largest fuel consumers of the global energy market, is investigating hydrogen as a potential future solution in providing clean, reliable, safe, and affordable energy for our planet.
The obvious advantages of hydrogen — its abundance, energy density, and ease of transportation — also make it a serious contender to replace our deep-rooted addiction of fossil fuels. However, as hydrogen technologies emerge, the processing, storing, and utilization of hydrogen in a safe and sustainable manner requires high production expenditure, being almost triple the cost compared to fossil fuels. For this very reason, the protection and maintenance of hydrogen technology is paramount.
Leyla Alieva is CEO and co-founder of NEOL Copper Technologies. Dr. Sergei Mamykin is a tribologist and copper filming technology developer at NEOL Copper Technologies.
A version of this article has been published previously in Lube Magazine. However, this version has been updated, modified, and made exclusive to the Canadian Mining Journal.
Comments