Metso celebrates 150 years
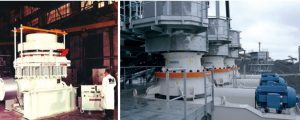
Old (left) and new Nordberg cone crushers.
Crushing and grinding giant Metso Corp. was officially established in 1999 through the merger of two Finnish-based industrial companies, Valmet and Rauma. Today, the leading manufacturer of mining and aggregate equipment has 12,000 employees in 50 countries. But Metso, which also makes and services equipment for the process and recycling industries, has a history that extends much further back.
In fact, the company can trace its beginnings to 1868, when Sunds Bruk, a small iron works in Finland, was founded. That company eventually ended up as part of Rauma.
Through a steady stream mergers and acquisitions over the years, Metso now has more than a dozen heritage brands that have contributed to its impressive expertise and depth of knowledge in comminution in particular. Looking back at the company’s history, it’s easy to see how Metso has achieved such scale and longevity.
One of its Metso’s oldest brands, Nordberg, was established in 1886. Nordberg designed and built the Symons cone crusher, which “revolutionized” coarse to fine grinding for mining plants, says Dusty Jacobson, sales and product support manager for mining.
With a different mechanical design that changed the concentric motion of the crusher, the Symons machine was able to handle larger tonnages and achieve a finer grind than ever before.
“It made it more practical to process more tonnes in a mining plant,” Jacobson explains. “It was really the gold standard for plant design from the 1920s until probably the ‘60s or ‘70s when semi-autogenous grinding mills and autogenous grinding mills started to get more popular.”
Although it’s now an older product, the Symons cone crusher is one of the biggest products overall in Metso’s lineage, with about 17,000 units sold.
Nordberg became part of one of Metso’s predecessor companies, Rauma-Repola, in 1986.
Another heritage company, Allis-Chalmers, made the first ball mill in 1898. It also made the first hydro cone crusher and was one of the first companies to modernize the primary gyratory crusher with a design that allowed for easier operation and maintenance.
“What they made in the 1950s is actually very market even today,” Jacobson says.
Megaliner
More recently, one of Metso’s most successful inventions has been the Megaliner, a mill lining product which was introduced about eight years ago.
Changing out mill components, which is typically done every three to 12 months depending on the application, is labour intensive and dangerous work, notes Todd Moir, director of product management.
“The Megaliner product reinvented the way these parts are installed,” he says.
By allowing the components to be fastened from outside the mill rather than inside, the Megaliner vastly improves safety – an accomplishment that has been recognized with an industry award for safety. The product also allows the job to be completed more quickly, slashing downtime by as much as 50%, Moir says.
Industry trends
Several industry trends have shaped Metso’s recent offering.
For example, in response to the decreasing ore grades and harder ore types that many mines are seeing, Metso has introduced products such as its HRC – a newer-style high-pressure grinding roll (HPGR) unit that handles higher tonnages with better energy and water efficiency.
And in the last decade, with miners facing financial pressures and uncertainty, Metso has really advanced its optimization efforts, says Jacobson.
“Customers are very focused on squeezing as much out of the plant for the lowest operating cost that they can, so our customers have actually pushed us to advance our technology and optimize our technology to a very high degree to make sure we’re getting the most utilization of the equipment that we can.”
Service focus
Since 2003, when it secured the first large-scale services contract in mining globally from a Chilean company, Metso’s focus on the services aspect of its business has only grown. In the company’s 2017 annual report, it notes that services make up 66% of its sales in the minerals segment vs. 34% from the sale of equipment.
Mines are running leaner – with fewer staff, fewer tradespeople and a different type of workforce overall than in decades past. This has given a boost to Metso’s strategic focus on services.
“The market is demanding being more servicedriven and a solution provider,” Moir says.
This means more than lifecycle service contracts – where the company offers a service along with its product. It also means helping mining companies more in their overall operations, in some cases even running equipment.
“We have some service contracts where we run a portion of the plant, so we kind of take ownership of a crusher or a mill and we supply the spares and wears for it along with the operation of the mill and the replacement of parts,” Moir explains.
Digitalization
Predictive maintenance and condition monitoring are other areas Metso has been hard at work on.
“That is something that we’ve really tried to focus on here in the last couple of years,” Jacobson says. “We have been focusing on data collection with the framework of condition monitoring to be able to put advanced analytics together to do predictive analysis, and help with maintenance planning as well as failure analysis.”
Currently, Metso has pilot projects at a dozen minerals processing plants in the U.S., South America, Africa and Australia to test its new cloud-based IoT solution to be launched in November. Metso’s platform is able to do predictive maintenance through “connected” crushers.
At 150, Metso is still reinventing itself. Last year, the company went through a reorganization of its overall structure and division of business lines, effective Jan. 1, 2018. As part of that change, and with the aim of spurring innovation, R&D teams were put in place in each of the company’s business lines, says Moir.
The first of the new products out of these teams – including its new IoT solution – will be released before the end of the year.
For Jacobson, who has been with Metso since 2003, the focus on innovation is invigorating.
“If I work for Metso for another 40 years, I know that I’ll constantly be challenged and that we’ll have new products and strategies and innovations always coming out,” he says. “That makes it exciting.”
Comments