Managing mining equipment throughout its lifecycle
Limble discusses how maintenance management software can help
Mining operations depend on a blend of moveable and fixed assets to conduct exploration, extraction, processing and transportation. The nature of these operations dictate the size, criticality and equipment technology that a company needs to meet its business goals. Companies utilize asset lifecycle management to maximize productivity and realize valuable financial returns on assets.
Asset lifecycle management (ALM) is a series of activities that monitor the reliability, cost of operation, efficiency of maintenance activities and profitability of equipment. The execution of ALM activities covers the entire life of the equipment, beginning from the planning and purchasing stage to the disposal stage. Lifecycle management of mining equipment is crucial as it allows an organization to:
> maximize revenues by enhancing asset productivity
> minimize operations and maintenance costs
> minimize depreciation by extending the useful life of assets
> streamline financial planning strategies, and
> enhance compliance to safety and statutory requirements.
Lifecycle management stages
Lifecycle management of mining equipment occurs in several stages and requires the input of experts from different departments. Technological advancements have continuously improved lifecycle asset management by providing tools that enhance cross-sectoral collaborations, visibility of mining operations and central supervision of multiple assets.
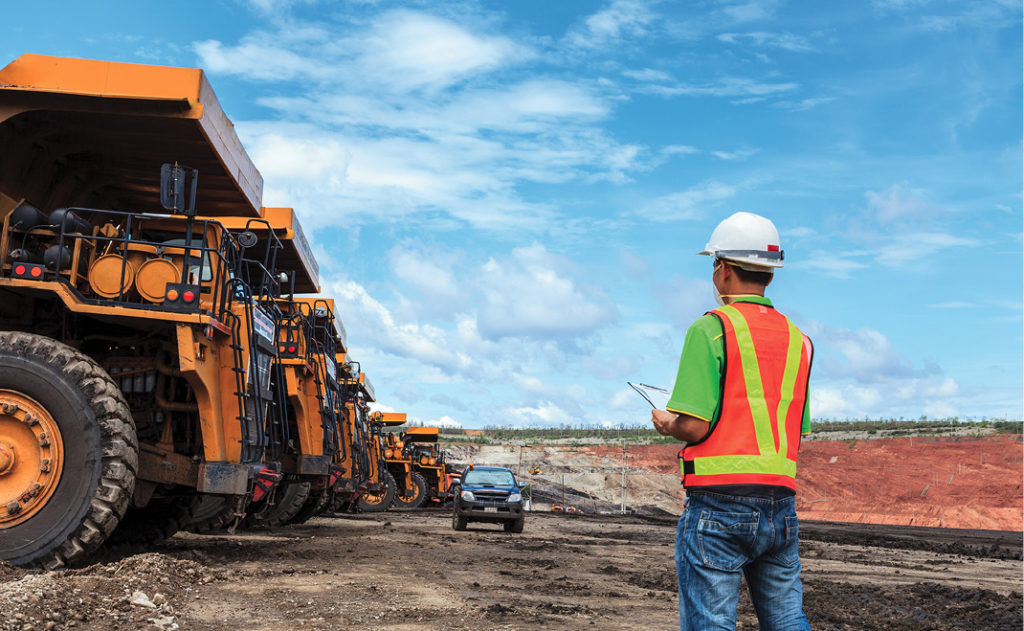
So, which are the main lifecycle management stages, and how do they affect mining operations?
1. Investment planning
During the initial stage, a company will evaluate operations to identify bottlenecks and opportunities for improvement. The company collects information from different stakeholders and analyzes equipment and mining records to formulate an investment plan. A planning team develops mining and business objectives, equipment selection criteria and budgeting considerations for better decision-making.
At this stage, the company rolls out a financial plan to cover acquisition (capital expenses), operation and maintenance costs. Once a budget is in place, the company engages different manufacturers or vendors to review its equipment and compare acquisition costs, technical capabilities, warranty conditions, operations and maintenance requirements.
Proper investment planning enables the company to identify equipment that will create economic value throughout its useful life. Companies acquire physical assets when:
> there is a need to scale up mining activities
> existing equipment or mining technology become obsolete
> safety risks and non-compliance increase due to the aging, or
> the efficiency of processes decreases.
Before purchasing additional assets, it is prudent for companies to audit the efficiency, operational and maintenance costs of existing mining equipment. Technological solutions expedite fact-finding, report generation and comparative analysis of mining utilities. Companies can choose between enterprise asset management and computerized maintenance management systems to collect, analyze and verify the accuracy of equipment operating data.
2. Purchase and deploy
Once the company pinpoints the exact product to acquire, it releases funding to the procurement department, which takes care of all the financial transactions and verifies the delivery of the equipment. As procurement deals with the suppliers, internal technical teams will be making preparations for the deployment sites.
The company and the supplier will work together to install newly acquired assets at site. After a test run is executed to confirm whether all components are working correctly, training will be provided to equipment operators, maintenance and other technical teams. During this stage, the company tags the mining equipment and creates a digital entry in the asset management software for better tracking.
Maintenance teams conduct an initial audit of condition-monitoring utilities and verify if they are compatible with existing communication channels. They develop a maintenance plan and update it on the computerized maintenance management software (CMMS) – if they are using one.
When deploying assets, the company may be interested in implementing asset tracking to optimize operations and supply chain planning. Telematics software allows miners to track geographical positions of movable assets through GPS technology, monitor operator behaviour, and collect accurate energy consumption data. For tools and stationary assets, companies might consider using QR codes and Bluetooth technology for easier asset identification and tracking.
3. Operations and maintenance
Companies recoup capital expenditure during the operation and maintenance phase. Since this is the longest stage in the lifecycle of mining equipment, it is vital to keep operations costs at a minimum, as well as adhere to safety and maintenance recommendations.
Proper maintenance interventions guarantee the availability and reliability of mining equipment throughout their useful lives. Proactive strategies like condition monitoring avert unexpected breakdowns, limit maintenance costs and extend the useful life of mining equipment – allowing the company to generate more revenue in the long term.
During operation, the company may intend to scale up operations or optimize functionality without replacing costly assets. In such situations, companies upgrade or modify mining equipment through:
> Component and machine rebuilds: Aging components or machines nearing the end of their useful lives are rebuilt, making them operate like new equipment. The cost of rebuilding mining equipment is small compared to the purchase of new units.
> Retrofits and upgrades: Critical parts of the equipment are replaced with advanced components that enhance safety, reliability and productivity.
> Remanufacture: Some manufacturers salvage older mining equipment and give them a second life. Manufacturers can build earth-moving equipment around the chassis of disposed of excavation equipment to create a cheaper one with nearly the same reliability and performance capabilities as a newly manufactured unit. This cost-saving measure also strengthens the sustainability of mining equipment.
For mining companies to gain value from their assets, they should undertake targeted and timely maintenance of equipment. CMMS solutions allow companies to merge all maintenance operations into one package. They retain accurate maintenance records for every asset, keep manufacturer manuals to enhance troubleshooting processes, reconcile maintenance inventories, and contain a list of recommended original equipment manufacturer (OEM) parts.
Modern condition-monitoring sensors, couple with predictive analytics, can be used to track common failure modes on critical assets and generate alerts when there are signs of deterioration. As a cheaper alternative, managers can urge the maintenance teams to perform regular non-destructive testing to track the condition of expensive assets.
Both approaches will generate data helpful for root cause analysis and for minimizing overall maintenance costs.
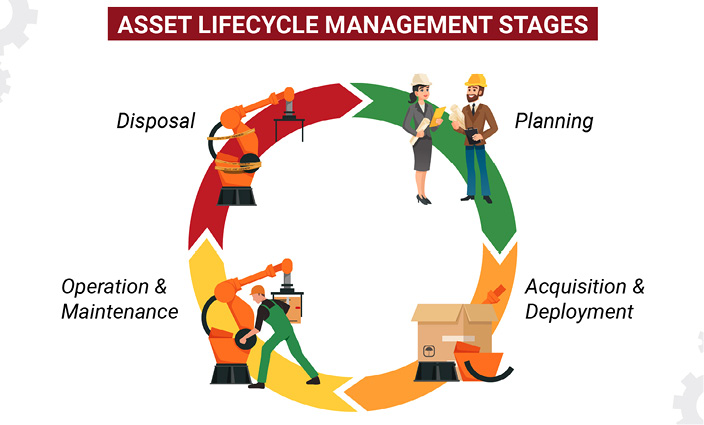
4. Retirement and disposal
Mining equipment, like all physical assets, undergoes tear and wear, which eventually renders the machines irreparable or inefficient. Frequent breakdowns, lower productivity, high energy consumption or higher operational costs indicate that an asset is nearing the end of its useful life. At this stage, the company performs a cost-benefit analysis to quantify revenue generation throughout the useful life of the equipment.
A repair and replace analysis will assist an organization in deciding whether to repair the equipment or decommission and replace it. After an asset is removed from service, disposal can take different forms like:
> Recycling and remanufacture:
The company may sell the scrap to the original manufacturer for recycling or remanufacture.
> Auction or sell: Targeting second-hand markets.
> Disposal in junkyards: The mining equipment is thrown away as scrap.
Before retiring mining assets, the company needs to evaluate the performance parameters of every piece of equipment like overall equipment efficiency (OEE), cost of maintenance and depreciation.
Quantifying performance parameters requires access and evaluation of multiple streams of data. By implementing CMMS programs, mining companies can collect accurate information throughout the lifecycle of equipment and refer to it whenever necessary. Unlike manual record-keeping techniques, CMMS records are accessible via multiple devices, are more secure and easier to summarize using visual graphs and charts. The management can decide when and how to retire assets and identify salvage values based on depreciation rates.
Summing up
Productivity and profitability in mining –
a capital intensive industry – depends on the appropriate selection and usage of mining equipment. Miners that execute proper management of their equipment throughout the entire lifecycle will enjoy better profit margins and ensure smooth operations.
Bryan Christiansen is the founder and CEO of Limble CMMS. Limble is a modern, easy-to-use mobile CMMS software that takes the stress and chaos out of maintenance by helping managers organize, automate, and streamline their maintenance operations.
Comments