Managing fall maintenance: It is a small weld after all
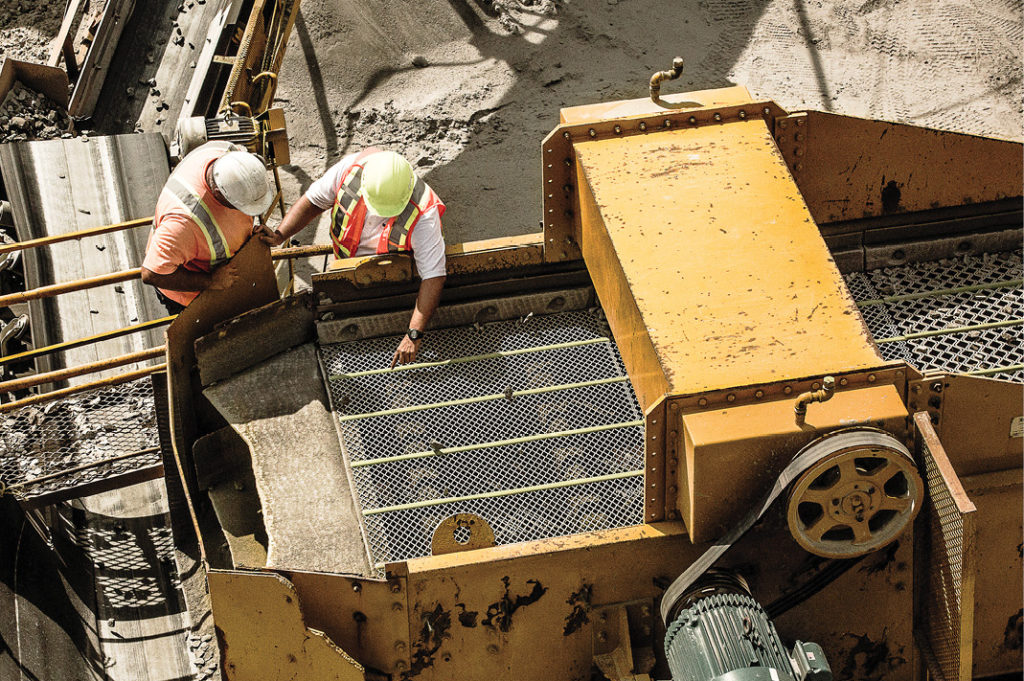
For processing plant managers, vibrating screen maintenance can feel like a tricky tug of war. What maintenance items are so urgent they must be handled now, and which can be temporarily patched and get more full attention later? Which of these can be done between shifts, avoiding costly downtime, and which will require a complete plant shutdown?
The tension is especially high in the fall when many plants try to meet their production goals before the inevitable winter off-season. Depending on whether the year went as planned, this can be a stressful time. Small welds and replacement of minor wear parts are typically handled between shifts, but larger maintenance may require a painful pause in production. It is sometimes tempting to delay certain maintenance items and try to push through to the end of the season.
Here are a few tips for navigating fall maintenance and setting plants up for success next spring.
1 Look and listen
Diagnosing needed repairs is a year-round priority, but especially so in the fall, when unexpected breakdowns can be especially unwelcome. Be sure to continuously listen to the vibrating screens and pay attention to unusual noises. The source of grinding noises in particular should be identified and addressed as soon as possible. Also inspect the machine for signs of wear, cracks or other damage. This includes looking out for worn or broken screen media.
The weeks and months leading up to winter shutdown are a good time for a service visit from the equipment manufacturer. Vibration analysis software can identify problems undetectable to the eyes and ears. This tool measures things like g-force, stroke RPM, and lateral movement. It can generate a viewable report within seconds, providing useful information that can help analyze the condition of the machine and show where to direct maintenance efforts.
2 Pick your battles
Once all current and potential maintenance issues are identified, it is time to prioritize. Small maintenance items can often be completed between two shifts to avoid shutting down the plant. Replacing wear parts like U-channel rubber, for example, should not be put off. This part is critical for protecting the support bar and replacement should remain a priority in the fall, even though it may be tempting to skip it. Other items like clamp rails may be worn from the impact of falling material and once again can be changed quickly enough to avoid a prolonged shutdown. Smaller maintenance items like these are common sense fixes to make no matter the season before they turn into bigger problems.
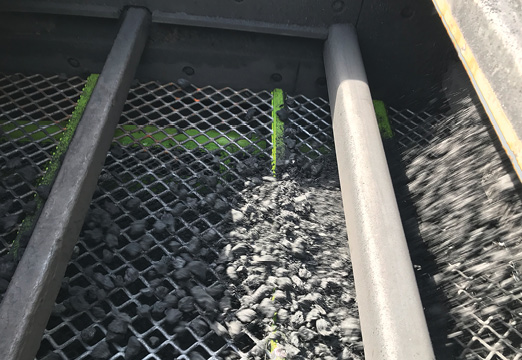
Larger maintenance items, such as changing all the machine’s bearings and springs or replacing support bars to maintain the crown, require a more significant time investment. These are the items for which it is tempting to look the other way in the fall if you are behind schedule, but they can also cause the most damage if a sudden breakdown does occur. If observation, or a service professional armed with vibration analysis technology, shows the problem needs addressing, it is better to take care of it right away than to wait and potentially face worse consequences later.
3 Take notes
Fall is the perfect time to gather data about the state of employed equipment and a plant’s overall productivity. Machines that gave trouble during the year might be good candidates for more in-depth service in the off-season, or complete replacement if necessary. Evaluate equipment for required maintenance in the fall and take notes on any issues that were not urgent but should be addressed before spring. Documenting winter maintenance needs can ensure critical maintenance is not forgotten about.
The end of the year is also a good time to evaluate plant productivity. Were there any bottlenecks in the process? Which machines seemed to hinder productivity? Isolate any equipment that held back the entire plant’s performance. For vibrating screens, it could mean it is time to upgrade to a machine with more capacity or screen media that better suits the conditions the equipment is taking on.
A strategic mindset
When winter is fast approaching, it is often easy to try to get away with a “patch maintenance” approach to avoid taking the time to do it right. Sometimes the maintenance can wait, but often it could be a critical mistake to leave it to chance. Being intentional about maintenance, even when rushed, is the best way to ensure the safest and most productive plant operations.
Serge Raymond is a product specialist at Major Screens.
Comments