Leveraging B.C.’s new technology readiness levels permit: A pathway to deploy innovative mine water technology
Developing a successful mine water management and treatment strategy is a critical aspect of every mining project. The plan needs to be protective of the environment, address the project needs, and pass regulatory approvals. It is the regulatory approvals that have often been the cause of confusion and frustration, as it can be difficult to come to a unified understanding of which technologies are currently considered best practices. Despite an ever-growing arsenal of water treatment technologies available to deploy, few can gain regulatory approval. Most mining jurisdictions use best achievable technology (BAT) processes, which are very useful in identifying which types of technology could treat the water. However, there is a feasibility aspect of the BAT process, which requires the technology to be “proven.” The lack of a clear definition of “proven” has typically been a matter of contention for permitting processes.
The new implementation of technology readiness levels (TRLs) for major mine projects in British Columbia is bringing clarity to the deployment of water treatment technologies and source control mitigation strategies.

In a regulatory context, TRLs are tied into step 3 of the BAT assessments, which are required for joint application information requirements (JAIR). There is a direct financial correlation between the cost of water treatment during mine operation, the cost of reclamation after closure, and the water treatment technology selections.
The TRL framework can be leveraged throughout the mine lifespan. Using the technology readiness assessment (TRA) guidance gives developers a clearer understanding of their site-specific conditions and enables them to mitigate risk scenarios. Through the provision of a common reference point, they also help expedite communication planning and stakeholder liaison to instill confidence throughout the project’s permitting process and into the lifetime of the mine.
An overarching challenge will be determining whether the application of the TRA guidance will be consistent across all types of water treatment, or if there will need to be different approaches taken for passive versus active treatment.
A technology readiness assessment (TRA) is a tool used to assess the readiness of a technology throughout its research and development. The TRA guidance document provides information on how to apply the TRA.
What is a TRL? And how are they determined?
First developed by NASA in the 1970s, the TRL scale was designed to measure and assess the maturity level of any given technology.
The process of advancing through TRLs is commonly referred to as “technology maturation,” a typical example of which follows: fundamental research (levels 1 and 2); research and development (levels 3, 4, and 5); pilot and demonstration (levels 6, 7, and 8); and early adoption (level 9).
Innovation, Science, and Economic Development (ISED) Canada provides broad guidance for the use of TRLs, intended to be applied to all types of technologies. The B.C. TRA guidance documents have based much of the discussion around TRLs on information publicly available from ISED and linked it to the B.C. regulatory processes for water treatment and source control at major mines.
In the fall of 2022, the B.C. Ministry of Energy, Mines, and Low Carbon Innovation (EMLI) and the B.C. Ministry of Environment and Climate Change Strategy (ENV) jointly released two documents to guide TRL selection and advancement within the mining sector. Entitled “Technology readiness levels interim guidance for major mines in British Columbia” (TRL guidance; v02.00, 2022) and “Interim technical guidance document for the technology readiness assessment” (TRA guidance; v02.00, 2022), these documents guide as to how to assess the TRL (i.e., the TRA process) for both source control measures and effluent water treatment systems for major mines in the province. This is unique in Canada as they discuss the level of technology maturity required for a treatment or control measure to be included in various stages of permitting a major mine project.
The B.C. TRL guidance documents provide clear indications of the TRL required for different permitting levels. One of the guiding principles of TRLs is the testing environment of a technology. In essence, a TRL is only valid for the specific operational environment for which it was tested. If a developed technology is to be deployed in an operational environment that is different from the one it was tested for, the technology would decrease in TRL and must go through testing and maturation again.
This TRL guidance is a key step forward in integrating more modern water treatment technologies into the regulatory process for major mines. It also provides clarity on progressing new and emerging technologies into full-scale implementation.
The guidance document defines it as a “systematic, evidence-based, process” with the primary objectives to identify risks and information gaps in the advancement of a technology, in addition to determining the TRL of the technology (v02.00, 2022).
According to the TRA guidance document, the TRA is not a requirement of any mines act (MA), environmental assessment act (EMA), or environmental assessment act (EA) regulatory processes. Rather, it is suggested to occur before these undertakings. The document states that:
“A TRA is independently initiated and developed by the proponent. A proponent can decide when and how to engage EMLI, ENV, EAO (environmental assessment office), and/or Indigenous groups in the development of a TRA but is not required to involve any additional parties. However, it is recommended that a proponent conduct a TRA before including an emerging technology in a MA, EMA, and/or EA regulatory process, as the outcomes of the TRA may help inform a proponent of the technology readiness and could help inform the regulatory review process” (v02.00, 2022).
These documents make it clear that undertaking a TRA will be beneficial to expediting permitting and review processes by avoiding the pursuit of potentially non-feasible technologies. While a lower-level TRL technology could be pursued, the timelines (and uncertainties) associated with bringing the technology to implementation should be considered in the context of the project timelines and risk tolerances. Based on this, a TRA may be well-suited to be undertaken in concert with a BAT assessment to ensure the efficiency of both processes.
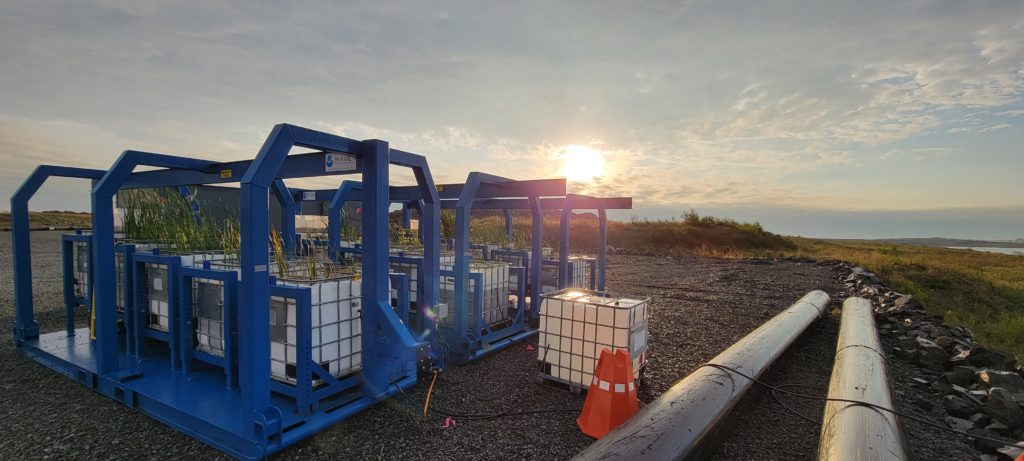
Working with site specificity
TRLs level 5 and higher are linked to B.C. permitting processes and are all required to have information gathered “under relevant site-specific conditions,” but herein lies a challenge, as it is unclear what will be considered relevant or site-specific.
Active treatment systems typically gain regulatory permits faster because they “actively” modify (control) the site-specific conditions. A range of site-specific dynamic variables can be controlled using heat and reagents. For example, the pH range can be modified before entering the core steps of a water treatment plant, or a temperature range can be fixed with heating. This removes a large amount of the uncertainty associated with the site-specific variations. In contrast, “passive” treatment systems must have their foundational designs modified to accommodate and address site-specific differences.
This means that even if a passive treatment technology has previously been implemented at full-scale at other sites, the TRL will be lowered from a level 8-9 to a 5-7 when looking to implement at a different location, as it needs to be modified for the site-specific conditions at the new site. As such, longer timelines need to be considered for the implementation of such technologies. There is also a risk as to whether a technology can be advanced through multiple TRLs for a specific site. This could be a major hurdle for getting the more passive, lower greenhouse gas-emitting water treatment technologies permitted.
One potential solution to this challenge is to design a hybrid of active and semi-passive water treatment, sometimes referred to as an enhanced passive treatment (EPT) system. The emergence of EPT systems is intended to be a “happy medium” between active and passive. While an EPT system will have higher capital expenditures than a passive system, the day-to-day operating expenditures are significantly less than an active system, and the timeline to implementation is much faster and less risk-prone than passive treatment.
An EPT system is intended to operate passively but is designed and built with the ability to turn on active features. For example, flow control or reagent additions can be implemented in response to changes in treatment needs (e.g., change in flow or chemistry) or system upsets. This could help to place boundaries on the range of variables needed to gather site-specific information.
Collecting data for “site-specific relevancy” is one of the greatest challenges for all water treatment systems. Although it is often expected that testing on-site will be most relevant, if a treatment system is being designed for a different phase of the mine life, it may not be possible to undertake the testing early enough to advance the technology in time for implementation.
In these situations, simulated environment testing is a useful tool. These apply to TRL 3-6 but could also be supportive of TRL at higher levels that require further development of their risk management plan.
In simulated environments, the ability to control factors such as temperatures, lighting conditions, humidity levels, flow rates, and chemistry variables enables the rapid collection of information to identify potential risks for further optimization. This information gathering process greatly contributes to the development of a comprehensive risk management plan.
Relevant site-specific information is also important to gather on-site when possible. Skid-mounted mobile EPT pilot-scale testing units enable site-specific customization and optimization and can be integrated with other technologies for treatment train validation. An example of these units being implemented for a constructed wetland treatment system (CWTS) at the Rainy River gold mine in Ontario is shown in the picture. These are often well-paired with off-site controlled environment testing to expedite the testing programs and focus the parameters for testing on-site. These testing units would be relevant to TRL 5, 6, and possibly 7.
Although the B.C. guidance documents do not provide a clear definition of the required size for “near full scale” at TRL 7, this concept is synonymous with what others have previously referred to as “demonstration scale.” At this stage, the system is typically in its near-final configuration and is being implemented on-site in a manner like how the full-scale system would be implemented. An example of this is a CWTS that has been operating at the Minto copper mine in the Yukon since 2016.
Closing thoughts
Technology readiness levels (TRL) have been a useful tool in many sectors, and it is exciting to see them being clearly connected to permitting and regulatory processes for major mines in B.C. While there are areas requiring additional clarification, such as determining how similar a “relevant” site or application must be and defining how much site-specific data is needed, there is at least now a foundation of mutual understanding and language from which to move these conversations forward.
While the technology readiness assessment (TRA) may take additional up-front time, co-ordinating it with best achievable technology assessments may save proponents substantial amounts of time and effort that could be spent pursuing non-feasible technologies. An overarching challenge will be to determine whether the application of the TRA guidance will be consistent across all types of water treatment or if different approaches need to be taken for passive versus active treatment.
The emergence of hybrid technologies, also known as semi-passive or enhanced passive treatment, holds the potential to bridge this gap and accelerate the maturation of technologies required for closure and/or with a lower carbon footprint across the TRL scale. These hybrid approaches offer promising solutions that can expedite developing and implementing innovative technologies in the water treatment sector.
Monique Simair is CEO and principal scientist at Maven Water and Environment.
Comments
George Rodger
It would be more productive to not have to use any process water. Ten years ago I developed a dry gravity process and not could interest any mining company in it? The syndrome of let someone else try it first.