Legacy builds a truck maintenance shop at a remove Chilean mine
Even with highly experienced workers and the most sophisticated equipment, mining operations are often difficult to tackle simply because of their unusually remote locations. In other words, the actual function of mining is one thing, but providing the proper infrastructure and support to make it possible is quite another.
Located in the Andes Mountains about 65 km northeast of Santiago, Chile, the Los Bronces copper mine is one of the largest copper reserves in the country. It is also very well known for its many logistical challenges, due to the combination of extreme altitude, rugged terrain, and even occasional avalanches that characterize its environment.
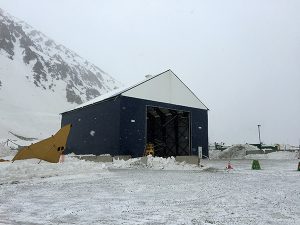
Legacy Building Solutions built a storage and maintenance shop at the remote Los Bronces mine in the Chilean Andes. CREDIT: LEGACY BUILDING SOLUTIONS
This tough landscape was a big enough factor that mine operator Anglo American Sur decided to add a shop specifically dedicated to storage and maintenance of a single CAT 975F off-highway mining dump truck.
Mining companies frequently utilize fabric structures when adding permanent or temporary facilities to their operations, due to the building style’s cost-effectiveness and ease of installation. In this instance, due to the building’s proposed location in a fully exposed area at the base of a mountain – a spot that always had high potential for harsh weather conditions – Anglo American would need look beyond typical building offerings and find a custom solution to meet its demands.
Legacy Building Solutions, one of the industry’s leading designers and constructors of fabric buildings, was contracted for the job. Among the advantages provided by Legacy was the ability to apply a tensile fabric membrane to a conventional structural steel I-beam frame.
This rigid-frame engineering concept – first introduced by Legacy about seven years ago – not only provides far more strength than the framing employed by traditional fabric buildings, but also it allows the structure to be customized to the exact dimensions required by the customer, down to the centimetre. This principle applies to any size building, from the Los Bronces truck shop to massive mineral storage facilities in Canada and the U.S.
Measuring 20.1 by 25 metres with a peak clearance of 14.75 metres to accommodate the precise measurements of the CAT mining truck, the building frame was designed to support an impressive snow load of 1,200 kg/m2 (246 psf) and withstand winds up to 120 km/h. Built with a 7/12 roof slope, the structure also meets seismic D parameters and all other required design codes.
To further counter the weather conditions, as well as to enhance safety by resisting any accidental damage from manoeuvring the mining truck or other vehicles, the building was equipped with a TNR rubber rolling door. This overhead door measured 11 by 8.5 metres and was reinforced with additional custom framing. A small service door for personnel was included as well.
Featuring 15-ounce flame-retardant polyethylene fabric cladding, the enclosed structure was ventilated by mesh soffit that allows fresh air to enter the interior while keeping debris and weather out. Two Schaefer RV-3000 peak-mounted passive vents help exhaust and hot air escape out the roof of the structure, thereby maintaining a comfortable interior for anyone working inside.
The polyethylene roof offers a substantial level of translucency, allowing natural daylight to help illuminate the inside of the building. The fabric’s properties also help keep the building interior cooler during the summer months and warmer in the winter.
Beyond the precise dimensions and other customized building elements, the structure was afforded further operational advantages by its solid steel beam design. Unlike the hollow-tube, open web truss framing historically used for fabric buildings, Legacy’s solid structural steel beams are not vulnerable to unseen corrosion originating inside a tube. Additionally, all building steel, components and hardware utilized on the mining truck shop were primer coated to resist corrosive elements.
The solid frame structure also provided the shop with straight sidewalls, as opposed to the curved wall designed normally associated with older style fabric buildings that limits storage space or use of equipment along the walls. In effect, the straight sidewalls allow workers to maximize the entire footprint of the building, from the 9-metre inside eave clearance inward.
All building materials were shipped in 12-metre cube containers from Legacy’s headquarters, allowing for simple packaging and effective transport to the remote jobsite. Legacy sent a technical representative to oversee local crews during building construction. Despite the challenges of working at a high elevation of more than 4,200 metres and often in snowy conditions, the building was erected within 40 days after the foundation was completed.
Remote mining locations will always present substantial challenges. But with the right support solutions – especially those that can be deployed in a timely fashion – companies like Anglo American Sur can tackle those problems head on – and get back to the primary task at hand.
This article was provided by Legacy Building Solutions (www.legacybuildingsolutions.com).
Comments