Key considerations for planning a ventilation system on demand

Mining consultants and suppliers have equally advocated the energy benefits of installing a ventilation on demand (VOD) or ventilation control system (VCS) in many underground mines but the mining industry has yet to fully embrace this technology. With the strong emphasis on reducing greenhouse gases (GHG) to slow the acceleration of global warming, progressive ESG investors are scrutinizing mining companies based upon long term sustainability while regulators are simultaneously applying carbon consumption penalties.
As a cofounder of Maestro Digital Mine, a key supplier of ventilation monitoring systems, I’d like to explore some of the reasons for the cautious uptake based on observations from the 150 mines we serve globally. To provide as wide a view as possible, I’ve also asked for the input of 20 global mining professionals in both the ventilation and automation sector on this question.
First, a VOD/VCS system should not be viewed as a magic bullet to achieving the lowest possible energy input into a mine. Above all, the acute and long-term safety of the miners must not be compromised in a normal production mode as well as in an emergency state from a fire or unplanned explosion.
Second, from a cost/benefit perspective, a 20% savings in energy is not the same as a 20% increase in production. Production trumps energy savings 100% of the time, therefore energy savings should never be the sole reason for the system. Or put another way, maximizing energy efficiency does not necessarily maximize the mine’s overall profitability.
Third, as much as humanly possible, a ventilation system should not impede production. Mining is in a constant state of flux with levels being mined, old levels being shut down and the ongoing development of new levels.
Where to start
Before embarking on your journey, subject matter experts and ventilation consultants should prepare a potential business case with mine management that will define what success should look like, positive impacts and counterbalancing risks, and a suitable approach where the economics work.
Since there are different levels of VOD/VCS automation, the appropriate level and the reasons for deployment must be determined by an experienced team that understands the orebody, mining methods, life-of-mine (LOM), supporting technical team and project goals. Simply put, a strong business case must be developed that includes de-risking the project and on-going technical and maintenance costs through LOM.
Assuming the mine is a suitable candidate, feedback from early adopters can provide valuable information to improve the outcome and more importantly avoiding the land mines that can derail a successful deployment. Five different themes are currently holding back successful VOD/VCS deployment.
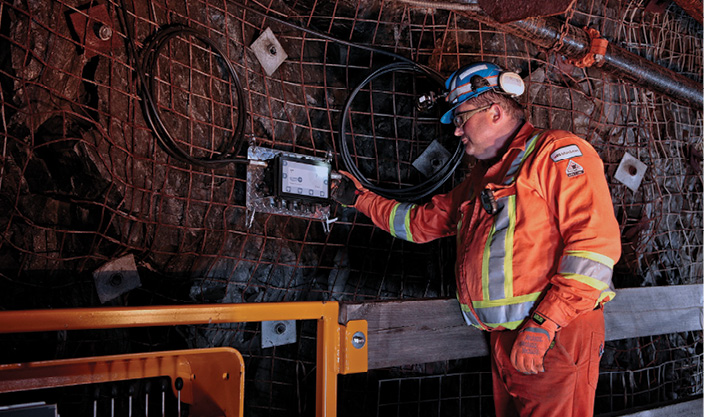
People
VOD/VCS systems are complex and require support from the project engineering, operations, ventilation, mine construction, electrical/instrumentation/network, control room and occupational safety and health departments. The mining leadership often underestimate the requirement from both a top down (mine manager) and bottom up approach in order to sustain proper change management. If the mine manager views the project as an impediment to his production schedule, it will experience an early death. However, if the system is viewed as getting workers back to the face quicker and safer by increasing face time, it stands a stronger chance of success.
A final working system will ultimately be transferred to the mine from the project team. At that point, the system needs internal champions from the ventilation and automation department to sustain the ongoing benefits. Product champion stability is often a challenge since the ventilation role is viewed as a stepping stone to production roles by either young technologists or engineers. The domain expertise as well as the unique mine ventilation system must be relearned with the next ventilation champions. Many of the successful systems today have avoided this pitfall with long-term stability in the mine ventilation and automation department.
Technical
Any VOD/VCS system will require a robust network to support connectivity of fixed assets like secondary fan starters, air quality stations (AQS) that measure air flow, gas, dust and worker heat stress, automated regulators, ventilation doors and booster fans. Networks connecting fixed assets are straightforward and easy to deploy whereas connectivity to people and mobile assets are far more difficult and less reliable due to their requirement for wireless connectivity, be it Wi-Fi or LTE. Accurate tracking systems required for the higher levels of VOD/VCS systems are one of the remaining challenges to ensuring a robust system. It is still very difficult to determine when miners enter and depart from the working stopes in order to turn on and off the secondary fans.
Complexity is increased multifold as the system climbs up the pyramid of control hierarchy. Such complexity relies on an astute automation and maintenance team that will work in step with the ventilation and production teams.
Obsolescence and interoperability play an important role in assuring that the system can operate effectively for the LOM. Mines need to specify open communication protocols and open systems to avoid future problems and liabilities.
Communication
Sustaining the system will require constant communication from the mine management downwards. Tracking and displaying the outcomes using dynamic KPI screens is critical. Measuring and comparing the before and current conditions like re-entry time, gas levels, worker heat stress, air flow and energy inputs in a graphical format will provide a quick and simple re-enforcement for a weekly update at the wickets or health and safety meetings.
Staged roll-out vs. all-in approach
Confidence in the system can be quickly eroded if the control system plan is implemented too quickly and one or more components fail. Successful projects often stage the ventilation system in smaller segments for early success and system confidence.
As a first step, adding a last mile network starting from the electrical substation out to the return air raise will allow air quality stations (AQS) to be added to monitor the level entry and return air raise conditions. This first stage can provide drastic production improvements by reducing re-entry times by 30-90 minutes per day depending on the travel requirements to the face and the number of shifts per day. This alone could fund the complete project due to the shortening of the production cycle resulting in more tonnes.
Manual control is the next biggest win, enabling a control room operator to view and adjust ventilation levels to areas of the mine with people and equipment while allowing the control system to turn on/off secondary fans in between shifts or in areas without people by event scheduling. In some cases, this can represent up to 25% savings in energy alone while providing the production team more time at the face. Digital ethernet based motor soft starters, door controls and automated regulators will be required at this stage in conjunction to the ethernet AQS stations to reduce capex by eliminating additional PLC/DCS cabinets and software.
The next stage is far more challenging since it requires a robust tracking system that can determine with good accuracy and reliability the location of both people and mobile assets. Only then should a mine consider automatic control that will optimize the ventilation on each level as well as the primary fans. Successful systems at this stage can lower energy consumption up to 50% by optimizing the primary fans.
Maintenance
All current deployments confirm the requirement of ongoing maintenance and calibration of gas sensors, airflow sensors and the training of the electrical/instrumentation department. Often this has not been accounted for in the original business case to their detriment. Newer digital solutions offer real-time diagnostics to pinpoint equipment problems from the surface control room as they occur and gas sensors that can be calibrated on surface and brought to depth to swap out quickly and simply. But maintenance can’t be eliminated so consideration should be given to the addition of a well-trained instrument and network technician to achieve maximum system uptime.
Michael Gribbons is CEO and co-founder of Maestro Digital Mines (www.maestrodigitalmine.com).
Comments