Innovating the smelting process
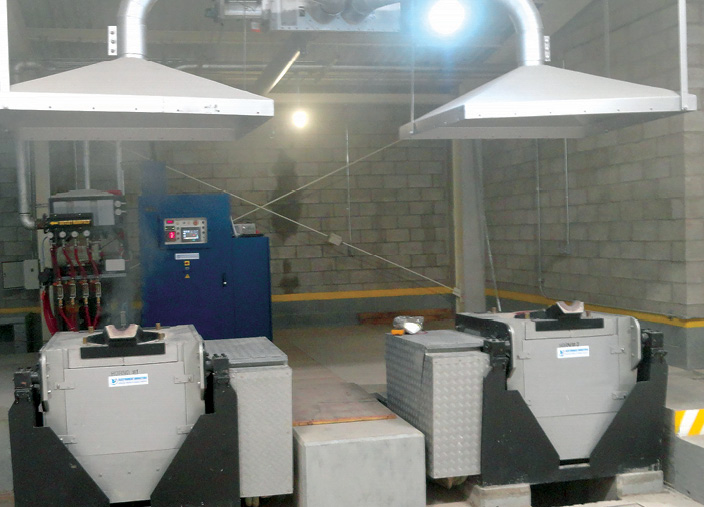
IGBT induction furnaces at the forefront
The smelting process, once considered a traditional and resource-intensive method, has now undergone a remarkable revolution, transforming the way metals are melted and reshaping the mining industry. This remarkable transformation can be attributed to the groundbreaking advancements in technology, particularly the emergence of the insulated gate bipolar transistor (IGBT) induction furnaces.
In this article, we delve into the fascinating world of smelting innovation, with a focus on the game-changing role played by IGBT-based induction furnaces. These innovative furnaces have ushered in a new era of efficiency, sustainability, and productivity in metal melting processes. Let us explore how IGBT-based induction furnaces have emerged as the driving force behind this revolutionary transformation, setting the stage for a more sustainable and optimized smelting industry.
Understanding induction furnaces
Let us delve deeper into the inner workings of these innovative furnaces and understand their significance in the realm of metal melting.
i. The technology behind induction furnaces
These furnaces utilize the principle of electromagnetic induction to generate heat, providing precise control over temperature and energy efficiency. Using high-frequency alternating currents, IGBT induction furnaces induce electrical currents within the metal, rapidly heating it to its melting point.
ii. Applications and significance in the smelting industry
IGBT induction furnaces have found extensive applications in various smelting processes across several industries, including mining. By providing efficient and controlled heating, these furnaces enable precise temperature regulation, ensuring optimal metallurgical properties and quality of the melted metal. They have become the driving force behind induction smelting process innovation.
Moreover, the adoption of IGBT-based induction furnaces has led to significant advancements in energy efficiency, reducing both operating costs and environmental impact. The ability to precisely control the heating process minimizes energy wastage and reduces greenhouse gas (GHG) emissions, contributing to a more sustainable and eco-friendly smelting industry.
Advantages of IGBT-based induction furnaces
IGBT-based induction furnaces offer many advantages that have propelled them to the forefront of the smelting industry. Let us explore the remarkable benefits they provide in terms of efficiency, productivity, cost effectiveness, and environmental impact.
i. Efficiency
By utilizing high-frequency alternating currents and precise temperature control, these furnaces enable rapid and uniform heating, resulting in faster melting times and enhanced operational efficiency. The efficient heating mechanism reduces energy consumption, contributing to lower utility bills and environmental sustainability.
ii. Productivity
With their advanced technology and precise temperature regulation, IGBT-based induction furnaces significantly enhance productivity in the induction furnace smelting process. The rapid and uniform heating ensures consistent and reliable melting, enabling smelting operations to meet increased production demands. Improved productivity translates into higher output and optimizes operational performance.
iii. Eco-friendly
The energy-efficient design of IGBT induction furnaces minimizes power consumption, resulting in reduced GHG emissions and a smaller carbon footprint. By minimizing energy wastage and supporting sustainability goals, these furnaces contribute to a greener and more eco-friendly smelting process.
iv. Cost effectiveness
The efficient heating mechanism and precise temperature control of IGBT based induction furnaces reduce energy consumption, leading to lower utility bills and operational expenses. Additionally, the minimized material waste and improved yield achieved through precise temperature regulation contribute to cost effectiveness by reducing material costs and enhancing overall profitability.
v. Long-term savings
These furnaces require minimal maintenance and offer extended operational uptime, resulting in reduced maintenance costs and increased productivity. Furthermore, their energy-efficient design and reduced environmental impact may qualify smelting operations for various incentives and certifications, opening doors to potential financial benefits and improved market positioning.
Several companies embraced IGBT induction furnaces and experienced remarkable outcomes in their smelting processes, contributing to smelting innovation and the induction furnace smelting process. Their success story with IGBT technology in the mining industry highlights the immense potential and transformative power of these advanced furnaces.
ElectroHeat induction is a leading provider of induction heating and melting solutions, specializing in the design and manufacture of IGBT-based induction furnaces. With a strong focus on the mining industry, they have pioneered the integration of IGBT technology to enhance smelting operations.
Their advanced furnaces provide precise temperature control, ensuring uniform and efficient heating of metals during the smelting process. This level of control has resulted in enhanced productivity, as it enables consistent melting and optimized operational performance.
The utilization of IGBT technology has also led to improvements in the quality of the melted metal. The precise temperature regulation and uniform heating provided by these furnaces contribute to better metallurgical properties and superior product quality. This is particularly crucial in industries where the integrity and reliability of the final product are paramount.
Overcoming challenges and driving innovation
Several challenges are encountered in the smelting industry, and IGBT induction furnaces have successfully addressed these challenges. Additionally, innovation and ongoing research can further enhance the capabilities of these advanced furnaces.
i. Challenges in the smelting industry
The smelting industry faces several challenges, including energy consumption, temperature control, and environmental impact. Minimizing energy usage, maintaining precise temperature control, and reducing the environmental footprint are pressing concerns.
ii. Addressing challenges with IGBT-based induction furnaces
IGBT induction furnaces have emerged as a viable solution for overcoming the challenges faced by the smelting industry. Here are how these advanced furnaces address these challenges:
> Energy efficiency: IGBT-based induction furnaces utilize high-frequency alternating currents and precise temperature control to achieve efficient heating. By minimizing energy wastage and optimizing power consumption, these furnaces significantly reduce energy consumption and associated operating costs.
> Precise temperature control: IGBT technology enables precise temperature regulation during the smelting process. This ensures uniform heating and minimizes the risk of overheating or underheating, leading to consistent product quality and enhanced metallurgical properties.
> Environmental sustainability: The energy-efficient design of IGBT induction furnaces results in reduced GHG emissions and environmental impact. These furnaces contribute to a greener and more sustainable smelting industry by minimizing energy consumption and promoting eco-friendly practices.
iii. Role of innovation and research
Continued innovation and research play a vital role in further enhancing the capabilities of IGBT induction furnaces. Ongoing efforts focus on the following:
> Advanced control systems: Innovations in control systems aim to enhance temperature control, automation, and process optimization. This leads to improved smelting efficiency, accuracy, and overall productivity.
> Material science and design: Research in material science explores the development of new materials and designs for induction furnace components, improving durability, performance, and energy efficiency.
> Integration of advanced technologies: The integration of advanced technologies, such as supervisory control and data acquisition (SCADA) can further optimize furnace operation, increase productivity, and enhance predictive maintenance.
Future perspectives and industry impact
The future of smelting is undoubtedly intertwined with the advancements in IGBT-based induction furnaces. As technology continues to evolve, we can expect even greater efficiency, higher productivity, and enhanced sustainability in the smelting industry. The potential applications of IGBT-based induction furnaces are vast, ranging from metal production to recycling and beyond. By embracing these innovations and investing in research and development, the smelting industry can pave the way for a more sustainable and economically viable future and unlock new possibilities and drive continuous improvement in the performance and efficiency of IGBT-based induction furnaces.
Comments