Improving backfill efficiency and worker safety in underground mining

Victaulic explains how diverter valves are changing the playing field
Over the past decade, mine owners have increased the use of backfill systems to manage waste and enhance ore recovery in underground mines, and automated systems are now playing a significant role in helping to improve efficiency and worker safety.
Historically, mine owners were slow to adopt paste reticulation systems due to the cost of backfilling equipment and the amount of time required for manual operation. Owners opted for mining top-down in some cases, using cemented rockfill to stabilize stopes even though this approach is less effective than backfill paste to ensure full confinement of hanging walls.
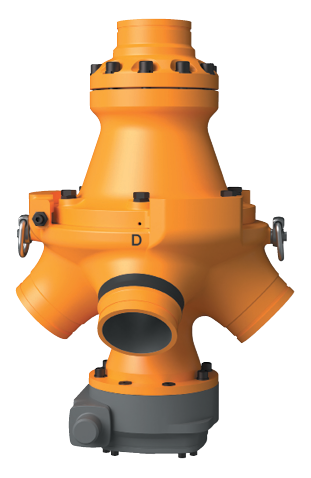
There is no question that manual backfilling is a time-consuming process. In reticulation systems where there are no diverter valves, a worker must travel to the lockout location, perform the lockout (which in some mines takes place on the surface), travel to the switching location, manually switch the pipe, and return to the lockout location to remove the locks. Performing this can take a team of three paste operators anywhere from two to five hours, depending on the layout of the mine and the lockout procedure employed.
Diverter valves change the playing field. Using a remotely operated valve that allows paste to be diverted without manual intervention eliminates delays so paste filling can begin quickly and seamlessly and removes workers from areas where they are at risk. An automated system also enables rotation to occur during otherwise nonproductive times, such as shift changes. There is no need for physical intervention, which makes it possible for workers who were previously required for paste operations to perform other tasks. This gain in productive time has a significant impact on the bottom line.
Unfortunately, many owners have not yet adopted this technology, assuming that automated equipment is cost-prohibitive. And that means they not only miss out on the financial benefits, but they also miss the opportunity to improve worker safety.
New Victaulic remotely actuated diverter valve
The remotely operated Victaulic Series 725T 4-way diverter valve builds on the original design for enhanced functionality. The internal rotating plug has three flow positions, with two primary outlets for directing paste or hydraulic backfill through the reticulation system to fill the appropriate stopes and a third, clearly marked, drain outlet for flush water diversion and emergency backfill dumping. The 90-degree rotation to the tapered drain port enables quick diversion of flow to mitigate water hammer during flush water diversion.
The valve is compact for easy install in tight underground environments and can be configured with several styles of grooved end connections. Manufactured with high-performance, resilient materials, it can accommodate pressures to 1,500 psi. A polyurethane seat provides long-life wear resistance, and martensitic stainless-steel wetted surfaces prevent premature erosion and corrosion.
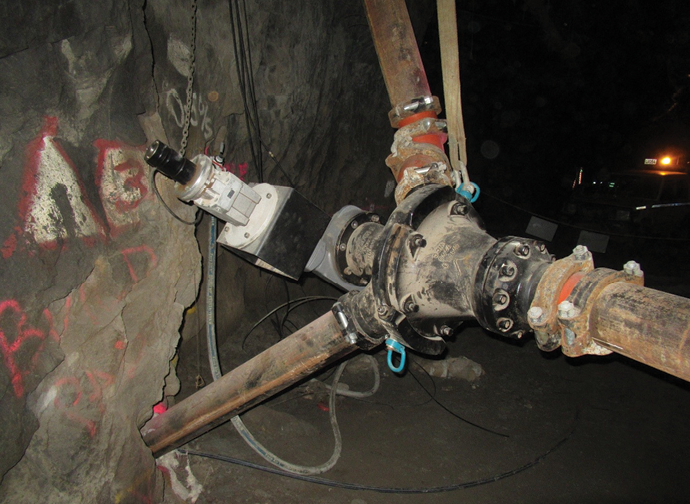
Proving value through performance
In a recent installation, this automated diverter valve replaced manual diversion in a reticulation system. The mine had been using an open stope, retreat mining method to extract gold ore. The open stopes ranged from 500 cubic metres to 2,700 cubic metres, with an average size of 1,500 cubic metres, requiring between 100,000-110,000 cubic metres of backfill per year. Because of the relatively flat dipping nature of the orebody, the hanging walls required topping up with a flowable mixture of sand, cement, and water to prevent hanging wall failure. Although this manual backfill method was effective, it was slow, and operating costs were high.
The operator decided to switch to paste backfill to ensure that the backfill achieved full confinement of hanging wall voids while increasing mine productivity, lowering dilution, and reducing operating costs. The installation employed automated diverter valves in the reticulation system that could be monitored and actuated from an aboveground control room. The installation of an automated diverter valve streamlined the paste reticulation process, minimizing nonproductive time and moving workers out of harm’s way.
The enhanced design of the diverter valve itself eliminates all exposed moving parts, which further improves worker safety. In the unlikely event of seal wear on the valve, all media remain contained within the valve body. This feature offers advantages over other diverter valves that rely on exposed compression seals between the body and sliding plates or rotating discs that expose operators to high-pressure media spray and seal leakage if there is a failure during operation or during the flushing process.
This valve also allows for local actuation. An operator can switch the diverter control unit to local actuation, move the valve away from the line that is being worked on, and lock out the actuator to isolate the line. This functionality provides the highest level of safety for operators because it allows them to manage the process without relying on someone else to ensure isolation.
Facilitating efficient operations
Today, valves developed specifically for backfill are more compact and safer to operate underground than ever before, and as backfill systems continue to evolve, so does the development of automated diverter valves. The results gained by installing these advanced valves prove that functionality and worker safety can be improved through automation and that better designs can deliver greater efficiencies and better economics for facility owners.
Marc Carriere is global mining manager with Victaulic (www.victaulic.com).
Comments