How to design successful potash conveyors
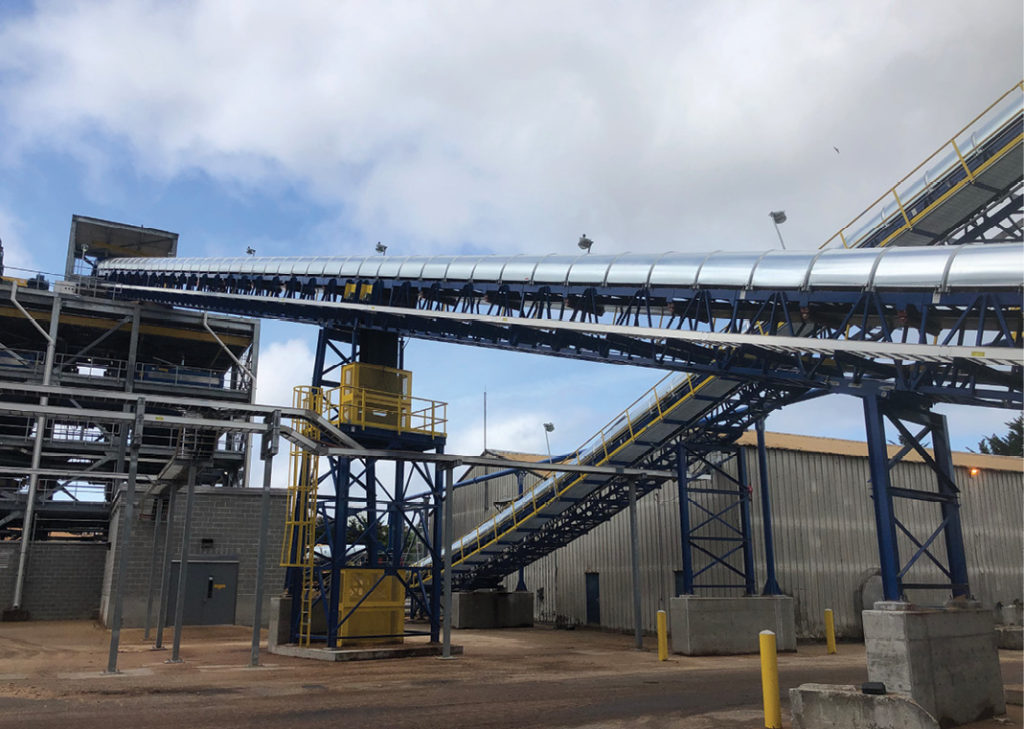
The potash industry continues to see growth as the world looks to feed its surging population. Amidst the array of machinery facilitating this effort, one indispensable, yet often overlooked type of equipment stands out: The belt conveyor.
From the rugged terrain of the mine site to the meticulous operation of the processing plant, belt conveyors serve as the lifeblood of potash operations, providing seamless continuity from extraction to loadout. Combined with the high tonnages and demanding conditions associated with potash operations, conveyors must be expertly engineered and incredibly robust to uphold reliability and ensure potash producers can meet their production targets safely and efficiently.
The following information covers essential aspects of designing this critical equipment for use in the potash industry and the sector-specific challenges.
Potash can present producers with a litany of challenges that must be addressed through thoughtful equipment design. When it comes to handling equipment, there are two primary concerns: corrosion prevention and dust management.
Corrosion prevention
Potash can be highly corrosive, particularly at higher moisture contents. And while different types and sources of potash exhibit varying levels of corrosion, corrosion prevention must always be factored into the conveyor design process. Inadequately designed equipment can quickly lead to frequent outages, excessive maintenance costs, and eventual equipment failure, as corrosion works to degrade components. As such, preventing corrosion is a top priority in conveyor design, playing into several components.
Original equipment manufacturers (OEMs) must consider corrosion at all points of potential contact with the material during the design stages. Most importantly, this translates to:
> Composite Idlers Composite idlers offer a more effective alternative to steel in handling corrosive materials. These lightweight idlers boast a longer service life and better protection against corrosion (and abrasion).
> Belt Cover Compounds As the component most in contact with the material, the belt requires special consideration. FEECO recommends chemical-rated belting that protects against corrosion and the amine solutions commonly employed in processing potash, which could otherwise degrade the rubber belt.
> Materials of Construction Stainless steel or specialty alloys may also be used in conveyor construction to protect against corrosion, as might surface treatments such as specialty paints, coatings, or galvanizing.
Dust and fines management
Dust and fines are problematic for several reasons; this fugitive material can present multiple safety hazards, result in product loss, create housekeeping issues, and damage equipment. These factors, combined with potash’s high potential for dust generation, makes dust prevention and management a top priority.
Conveyors offer ample opportunity for customization to minimize the potential for dust. The following measures are implemented at feeding areas and transfer points, where dust and fines are most apt to occur:
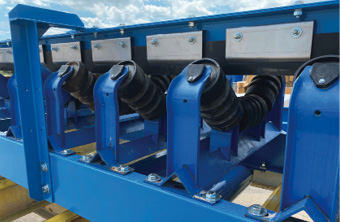
> Skirtboards Skirtboards are integrated along the sides of the conveyor (on the trough interior) to contain fugitive material. They are most common at load points but can also be utilized for the complete length of the conveyor to contain material.
> Apron Seals Apron seals, consisting of an additional piece of rubber, can be incorporated into skirtboard designs to create a double seal against fugitive material.
> Impact Idlers & Beds Impact idlers or beds can be used at loading areas (typically in combination with skirtboards) to prevent material from escaping between idlers. Similarly, idler spacing may be reduced at load points to provide additional support for impact loading.
> Dust Pick-Off Points Dust pick-off points are also common at feeding areas and discharge points. These create a vacuum, or negative pressure, which captures any fugitive dust, redirecting it to a baghouse. From there, the air can be recycled after dust has been filtered out.
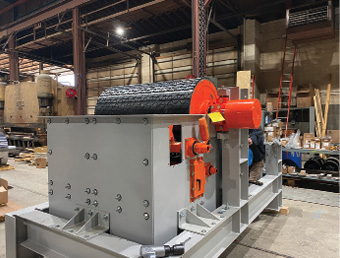
> Motorized Head Pulleys Dust allowed to infiltrate equipment components can quickly degrade equipment, particularly when it comes to drive components, which are costly to replace. Combined with the corrosive (and sometimes abrasive) nature of potash, keeping dust out of drive components is essential to equipment reliability and service life. One upgrade FEECO recommends in this effort is a motorized head pulley. With a motorized head pulley, both the motor and the reducer are internally contained within the head pulley, preventing the potential for dust infiltration.
> Taconite Seals Taconite seals are useful in keeping dust out of bearings. These additional bearing seals are filled with grease and purged, mitigating the potential for dust to contaminate the lubricant and damage the bearing.
Abrasion
Albeit less of a concern than corrosion and dust management, it is important to note that abrasion can also be a concern in some potash settings as well. When the unique potash source exhibits an abrasive quality, additional measures are necessary to protect equipment. This typically involves reinforcing high-wear areas such as transfer chutes, inlet loading areas, and the like.
Reinforcement may be implemented through increasing material thickness to provide an additional wear allowance, incorporating wear-resistant liners, or both. It is common for contact points such as discharge hoppers and skirtboard side plates to be lined with AR400 plate (quenched and tempered carbon steel).
General handling considerations
Beyond the specific material challenges potash presents, a few other general considerations are vital to the success of a handling system in the potash industry:
> Spillage In addition to dust abatement, minimizing product loss resulting from spillage is another common objective in potash handling systems. Spillage can be prevented through a number of approaches.
• Optimizing feed area design, as well as incorporating skirtboards and decreasing idler spacing (or employing an impact bed) go a long way in preventing the potential for spillage at loading areas. Beyond this, spillage can be prevented by designing for proper belt tension according to load conditions.
• Further, increasing trough depth by utilizing a higher angle of idler helps to keep material contained.
> Safety Safety is a top priority at all mining and processing facilities, no matter what the material. The primary concern with conveyor safety is protecting people from pinch points and moving parts through guarding. There are mandates to the various points at which guarding is required, though additional guarding beyond what the mandates require is also available.
• E-stops and pull cords can also be integrated into the system to minimize risk in the event of an incident. FEECO also recommends closed-end housing bearings and return idler guards as added safety precautions.
> Reliability The high capacities and demanding conditions associated with conveying potash require equipment that is exceptionally robust to be reliable for the long term. This translates to higher belt tensions and material loading, which in turn influence several factors:
> Belt Selection Belts running at high capacities must be rated for proper tension and ply. Specialty belting can be rated as high as 1,800 PIW (pounds per inch width). In some long conveyor applications, a steel corded belt may be implemented in lieu of the standard fabric cord belting to reduce belt stretch.
> Pulleys Since belt tensions apply their forces on pulleys, pulleys must also be more robust. FEECO often recommends the use of mine duty or engineered class pulleys in high-capacity applications. Both pulleys are designed for higher operating tensions. Engineered class pulleys are custom designed for the application and use special profiled end discs to eliminate critical welds at high-stress areas on the pulley.
> Idlers Idlers should be higher rated, typically CEMA D or E. In these classifications, idler shaft size and shell thickness increase accordingly to handle higher load ratings.
> Drive Components Drive components such as motors and reducers, head shafts, head pulley, bearings, and external backstops will need to be heavy-duty and appropriately designed for the application.
Operating conditions
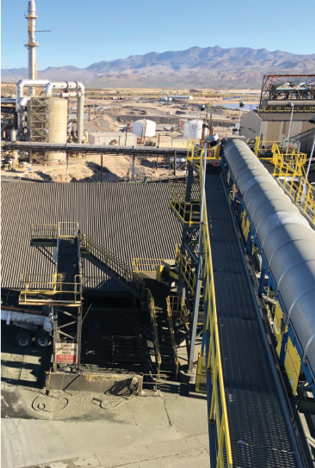
As with every industry, facility operating conditions also play into potash conveyor design. Mine sites or plants with conveyors operating outdoors are advised to incorporate weather covers or even full gallery enclosures to protect potash from the elements. As potash is hygroscopic, readily absorbing moisture from the air and resulting in caking, protecting potash from precipitation is especially important.
With most potash mined in Canada, conveyor systems must also be equipped for reliable handling in cold weather. Low-temperature grease in bearings is recommended, as are ductile iron bearings instead of cast iron, which can be brittle in extreme cold. Low-temperature-rated instruments, as well as a heater in the reducer, are also typically recommended.
Concluding remarks
As potash producers continue to ramp up production to meet growing demand, belt conveyors remain a critical aspect of ensuring a safe, reliable, and efficient operation.
The demanding conditions associated with potash conveying mean that the safety, reliability, and performance of these systems relies on addressing the unique challenges this industry presents through careful design, engineering, and fabrication.
Dan Baxter is in material handling sales at Feeco International
Comments