How lubricants can play a vital role in reducing TCO
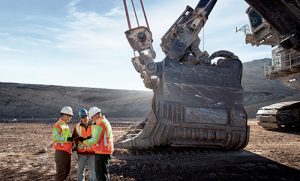
KGHM’s Robinson mine in Nevada. CREDIT: SHELL LUBRICANTS
Automated lubrication systems are designed to provide optimal performance and longevity of mining equipment by delivering lubricants in the proper amounts, at the proper times, to the appropriate places on these machines.
They also are designed to provide consistent distribution in the harshest environments.
If the systems are not properly inspected and maintained, however, damage can result. The cost of component failure can far exceed planned maintenance expenses.
A disciplined, ongoing inspection and maintenance schedule can save companies hundreds of thousands of dollars each year in lubricant, maintenance and repair costs. These inspections can also help avoid unplanned downtime by identifying components that need replacement before a catastrophic failure occurs.
In assessing the cost of routine maintenance, it’s important to consider the total cost of ownership, or TCO. This is the entire amount a mining company spends on its equipment, including purchase costs and lifetime operating expenses, along with the expense of lost production during downtime. Mine operators can improve their TCO by reducing operating and lost-production expenses, boosting both productivity and profitability.
“It is challenging to understand all of the factors that contribute to total cost of ownership,” says Duane Schulze, Shell Lubricants Service Expert. “It is even more challenging to identify and mitigate all of those potential risks before they become an expensive issue. By proactively managing your maintenance schedule and lubrication systems, you help put yourself in a better TCO position.”
Understanding automated systems
The first step to improving TCO is understanding the components of automated systems and how they work. These systems can be complex. A single-line grease system usually has a controller governing its timing and function; a pump that draws grease from a central tank and circulates it; injectors that meter the grease to the bearings; and a pressure switch that ensures the injectors deliver the proper amount of grease at each lubrication point. However, the systems on most mining equipment can be more complicated, and a typical shovel may have 95 separate lubrication points served by six different systems.
Given this complexity, leaks – especially small ones – may be difficult to find.
Some companies choose to accept a small level of leakage and replace lubricants more frequently. Unfortunately, more frequent lubricant replacement drives up costs. Even though the cost of lubricants is small relative to other components, it can add up to hundreds of thousands of dollars.
“Customers often get used to the issues they are having and do not realize they could help make their equipment last longer and reduce costs just by selecting better quality grease,” Schulze says.
The second step in improving TCO is to recognize the benefits of proper lubrication management. Companies should be sure to match grease selection to the equipment needs and the operating environment.
In addition, grease should be properly stored and handled to reduce contamination.
Choosing the right grease
Rather than saving money, buying lower- grade or improper grease may actually increase costs. Selecting the proper grease, however, is not as simple as it sounds. There is not always just one correct answer in choosing the best grease for an automated lubrication system. Usually, grease selection involves trade-offs.
Grease consists primarily of base oil and additives, which provide the critical performance characteristics. A thickener gives the grease its consistency and keeps it in place on the equipment. These elements enable the grease to lubricate despite temperature variations, vibrations and environmental conditions, while also staying in place and maintaining its consistency over time.
Choosing the correct grease helps ensure that equipment operates correctly while potentially minimizing the cost of maintenance and component replacement and improving operational efficiencies.
The first step in selecting grease is to review OEM recommendations and baseline operating conditions. Mining operators should focus on the Usable Operating Temperature. Depending on the geography and operating conditions, a grease’s ability to perform at low temperature is as important as performing at high temperatures. Some greases are specially designed to maintain their consistency and protection properties while operating in extremely low or high temperatures.
The benefits of an effective TCO program
Based on years of experience working closely with customers across various industries, Shell Lubricants knows that lubrication can reduce TCO and improve equipment efficiency and productivity.
Although lubricants account for less than 5% of most companies’ maintenance costs, lubrication issues may contribute to as much as 75% of all equipment failures.
Surprisingly, many companies fail to recognize the critical role of lubricant selection and application in reducing TCO. An independent survey found that 60% of companies believe lubricants can reduce maintenance expenses by less than 5%. In fact, for some sectors, improving lubrication practices can cut maintenance and repair costs by as much as 30%. In other words, companies that fail to incorporate lubricants into their comprehensive TCO assessments are potentially leaving money on the table.
Proper lubricant selection and management can affect costs significantly.
In a survey, 46% of users acknowledged that errors in lubricant selection or management caused unplanned downtime.
Twenty-seven percent said their cost exceeded $250,000, and more than one in 10 admitted the associated costs exceeded $1 million.
TCO programs do not always generate benefits that are immediately obvious.
Getting TCO right is often about balancing short-term and long-term costs with long-term improvements. Mining equipment is designed to be durable, and its tolerance to poor or lax maintenance can make it difficult to quickly demonstrate tangible benefits of a TCO program. For a program to succeed, companies must look ahead and recognize that selecting better quality grease today and having a strong grease management and reliability program can reduce maintenance costs in the long run.
How to help prevent a failure
Given our years of experience working with all types of mining equipment, Shell Lube Service Experts can help spot early signs of trouble before they result in unplanned downtime or equipment failure. When our experts conduct preliminary assessments on a shovel, they typically start with a visual examination of all components, looking for loose bolts, cracks in the frame, noises, and other general housekeeping. Next, they check the gear box temperatures and take oil samples (if the customer requests it).
They also inspect all pumps and injectors for grease and air leaks, check the system pressure and review all lubrication points throughout the machine to ensure each component is receiving the proper amounts of grease. In addition, they examine the open gear lube system, dipper handle, rack and pinion, slew gear and pinion, and spray or drip feed system.
They also conduct by-pass checks on all injectors.
An example of one inspection underscores the importance of regular inspections.
In 2016, a Nevada copper and gold mining company began working with Shell Lubricants to reduce its TCO for critical equipment at the mine. During the coldest winter months, Shell Lube Service Experts working alongside the mine’s staff found a cracked tooth in the crowd bull gear of an electric rope shovel – a discovery that wound up saving the company almost $900,000.
Shell Lubricants’ team worked with the company to analyze the potential for component failure and identify signs of weakness or fatigue in key system components including: open gearing, pins, bushings, bearings, and automated lubrication systems. In examining the automated systems, the team determined if they were functioning properly and delivering the right amount of lubricant at the right time. The Shell Lubricants team started by establishing a baseline.
On the company’s electric rope shovels, Shell Lube Service Experts visually inspected the systems and noted areas that appeared to be under- or over-lubricated.
Team members inspected both the hoist and crowd bull gears by cleaning a tooth flank on each to identify wear, fatigue or plastic deformation.
It was during this inspection that the teams identified the cracked tooth.
The team immediately notified the maintenance crew’s lead mechanic and the shovel and drill crew supervisor. If the shovel had returned to operation without removing the tooth, the gearing may have failed. Using an ultrasound, the maintenance crew checked adjoining tooth flanks and found another crack.
The maintenance crew scheduled repairs for the crowd bull gear and monitored the shovel operations daily until the repairs were completed.
If the gear tooth fatigue had not been found, a catastrophic failure could have occurred causing extensive damage to the crowd bull gear, crowd drive pinion or crowd gear box. It also could have resulted in unscheduled down time. The $900,000 savings represents the difference between the cost of the repair and the expense of replacing the crowd bull gear and the associated downtime and production losses.
The mining company’s inspection shows how in today’s environment, taking the time for preventative maintenance can have a big impact on operations. Shell Lubricants works with mining companies globally to help them improve their TCO approach to lubrication, resulting in more than $55 million in documented customer savings from 2011 to 2016. By working together to develop a TCO program specific to each company’s needs, Shell Lubricants can help clients improve the efficiency, productivity and reliability of their automated grease systems.
This article was provided by Shell Lubricants.
Comments