Hands off for (hand)some rewards
The thought of autonomous mining is a relatively new concept for many mining companies because it’s still considered a futuristic technology in the minds of many of today’s miners.
Having an expensive piece of equipment working without an on-board operator at the controls is something that’s still too risky for many owners to invest in because of the potential losses should something go wrong.
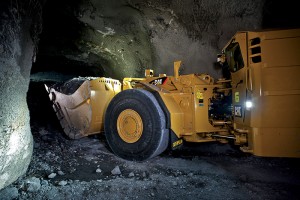
A Cat LHD works deep underground and far from the operators located safely at a command centre in a different part of the mine.
And, understandably, things can go wrong, and the potential liabilities are still too high, particularly when mine owners and operators are now watching their bottom lines more than ever thanks to today’s economy.
However, taking risks is the backbone of mining and regardless of how potentially dangerous they may be, some forward- thinking companies are venturing into the world of autonomous mining.
And, the concept of remote-controlled equipment isn’t new. In fact, Caterpillar’s Chief Engineer Michael Murphy says, “Some equipment manufacturers and their suppliers have been studying autonomous mining for more than 20 years and are now transforming their research into realities.
After years of building and testing prototypes, designers and engineers have now succeeded in making small components capable of controlling massive pieces of equipment through a hand-held device containing a few switches and a couple of joysticks.”
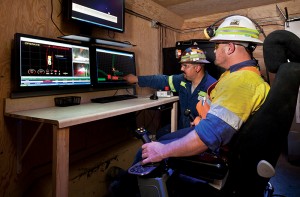
Joysticks and monitors make operating mining equipment underground much more comfortable – and safer – than actually sitting on the iron.
For example, Murphy says, automating underground loaders, also commonly known as load-haul-dump machines (LHDs), is a convincing one. He says there are at least a dozen mines around the world right now that are benefitting from autonomous mining and tele-remote control of their equipment.
Murphy says that Caterpillar has been a leader in this field by developing a system for semi-autonomous operation of LHDs, called Command for underground.
Command is a capability set within Cat MineStar System, which includes technologies for both surface and underground mining.
Technically, Murphy said the Command system for underground mining enables both remote and autonomous operation for part of the work cycle of the equipment.
Primarily, he said, it was developed for safety by reducing human exposure to the immediate workplace.
In addition to working at a safer distance from the equipment, Murphy said that by removing the operator from a potentially hazardous environment, it also allows the operator to work in a more comfortable, ergonomic operator station.
The station itself is modeled on the actual cab of the machine, with all ergonomic controls, alarms and features operating just as they do in the machine. The system can be equipped for line-of-sight operation, or for tele-remote operation with the addition of video feeds from the site and optional video and audio feeds from the equipment.
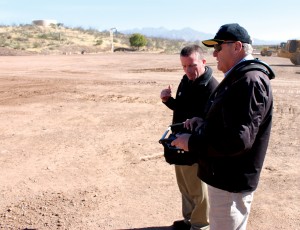
CMJ editor Russell Noble (foreground) operates a dozer-ripper with portable control strapped over his shoulders as a Cat instructor watches as the machine is put through its paces.
Grade control and avoidance zones are also designed into the system, and with a switching-control feature, the operator can move from one machine to another, which enables one operator to control multiple pieces of equipment when the work does not require simultaneous operation.
Murphy further explained that remote operation allows machines to be used under highwalls, and in other situations that present potential safety and health hazards. He described typical applications to include edge work, operation on, or near, unstable ground, leach-pad ripping and maintenance, aggressive ripping, and pushing stockpile material to underground feeders.
As mentioned earlier, safety is the main priority, but the remote operator station also helps contribute to productivity because shift changes are faster as one operator takes another’s place in the seat.
Faster shift changes also reduce machine downtime and optimize productivity.
“Remote operation also enables a machine to continue working immediately after blasting operations, rather than waiting for the air to clear,” said Murphy.
It’s estimated that automated haul trucks can provide an extra 500 machine hours per year, which in some cases, can mean upwards of 10 per cent more hours of machine life.
Murphy said that automation also decreases the need for expensive training there’s worker turnover. A breakdown of mining costs shows that 16 per cent of the cost of mining is in training and administration; followed by 14 per cent for haul support, 45 per cent for actual hauling, 15 per cent for loading, six per cent for blasting, and four percent for drilling.
Adding to this, conventional mining takes 4.5 people per truck to operate and, “When you take people out of the operating picture, it’s far more controlled by allowing for the improved execution of the tasks which ultimately, often means greater production and profitability,” said Murphy.
“I think that’s what people forget about automation; it allows for a better way to measure the process, and then measure process variants, thus improving on that process.” Building on its fixed-location control stations, Murphy continued by saying that Caterpillar is working to develop a semi-autonomous dozing system, which enables one operator to manage multiple dozers simultaneously.
On a recent trip to Caterpillar’s equipment testing facilities in Arizona, Editor Russell Noble was given some hands-on time (see adjacent photo) to operate one of CAT’s large dozers.
As you can see in the photo, one small device can control one large machine, but as mentioned earlier, multiple machines can be controlled simultaneously to improve productivity.
However, Command for underground is the main focus with its three levels of operational control that are supplemented with video from on-board cameras to provide a real-time view of the machine location and status.
In co-pilot mode, the operator is able to monitor equipment locations in a mine plan, and by using joysticks to give the machine directional input. On-board scanners, combined with radio network infrastructure, ensure the machine selfsteers along a safe path.
The most advanced element of control, auto-pilot, allows the machine to auto tram, dump and return for operator control of the loading process. Zones within the operations area can be configured to regulate machine speed and to establish boundaries at required points.
At any time, full operator control of the system can be obtained through tele-remote mode and by providing three different levels of operational control, helps maintain the versatility that an LHD provides to a mining operation.
Separate radio networks can be fed to a single operator station allowing the control of multiple machines in different areas of the mine. Automatic camera switching and the staggering of load cycles ensure the operator maintains safe control of all machines at the same time.
The system also has features that reduce hazards in the working area of the machine.
The Area Isolation System ensures that Command for underground will not operate in the event of personnel entering or equipment leaving the operations area while the machine is being controlled from the operator station.
The system has the ability to be relocated to allow for changing operational needs. In brief, a barrier control panel is located at each entry to the operations area. Connected to either a gate proximity switch, or LADAR, these barriers ensure that the machine is disabled if it has detected entry into the operations area.
Command for underground components are purpose-built for underground mining with rugged features targeted to underground applications. Additionally, they can report extensive machine health and operational data to the operator station if needed. There is no need to send a technician to the machine to check machine health.
Command for underground only requires a mine map to be loaded into the server, and the system is designed to work within the mine profile. There is no need to drive a machine manually to “train” the system initially and each time routes or road conditions change.
Many greenfield mine developments now include automation in the overall scope of the project due to cost-per-tonne analysis. Mining companies that operate automated systems now understand the efficiencies gained and develop their mines to take best advantage, but the automated and autonomous mine is not something that’s built overnight.
As mentioned earlier, the journey to autonomy is made from years of trial and error, but as technology gets more advanced, and technologists become more familiar with the capabilities of today’s mining equipment, there’s no denying that automation will continue to make operations more predictable and consistent, but most of all … safer.
Comments