Exploring the emerging technologies helping to improve the sustainability of steel
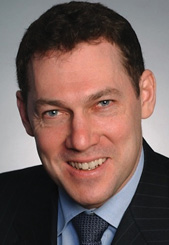
Emerging from tariffs set by the US government in 2019, Canadian steelmakers are experiencing strong market conditions from growing global demand. Whether driven by oil drilling, infrastructure or government investments, the International Energy Agency forecasts production will grow by 30% by 2050.
But as demand for steel grows, so does the call for low-carbon supplies. At the recent COP26 environmental summit, Canada signed on to the Industrial Deep Decarbonization Initiative, requiring green factors to be considered for the purchase of materials. This is pushing many companies – such as automakers who use about 12% of the world’s steel – to accelerate decarbonization initiatives and seek cleaner inputs in an effort to reduce Scope 3 emissions.
The challenge is that steel is one of the world’s most energy-intensive industries, accounting for an estimated 9% of global carbon emissions. The good news is Canadian steelmakers are among the greenest compared to their global industry peers, and are expected to see continuous improvement as they strive towards 2050 net zero goals set by the Canadian Steel Producers Association.
The industry is already seeing great progress. Algoma Steel announced a $703-million plan to go electric by converting its blast furnace to an electric arc furnace (EAF) – with support from the federal government. The Government of Canada will also be investing $400 million in ArcelorMittal Dofasco, which is pursuing a $1.7 billion project to phase out coal-fired steelmaking at its facilities. These two projects combined will look to remove up to six million tonnes of carbon a year.
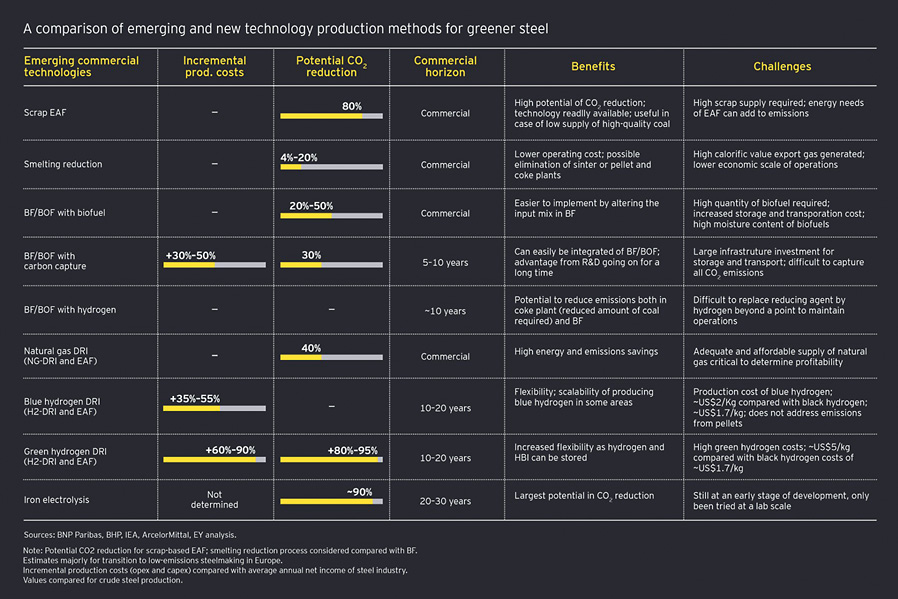
Though, the journey to net zero won’t be easy. The continued move to EAFs will help to drive down emissions, but creating a genuinely sustainable industry will require broader, bolder measures from all players across the steel value chain. Achieving this will depend a lot on technology – much of which isn’t commercially available yet. Steelmakers considering adopting some of these emerging technologies to reduce emissions should consider the following:
> Carbon capture: Can recycle up to 90% of the exhaust gas from blast furnaces, reusing it for combustion. The remaining highly CO2-concentrated 10% can be stored or used. Determining whether carbon capture is suitable may depend on overall operating costs, with technology costs still high at this stage of maturity.
> Innovation in production mix: Moving to scrap-based EAF production will reduce emissions, but each steelmaker will need to decide whether and how to transition based on the affordability and availability of scrap and the desired quality of the end product.
> Hydrogen: Use of green hydrogen (generated by renewables) with direct reduced iron (DRI) and EAF is likely to be the cleanest alternative for steelmakers in the future, although it’s likely to be some time before hydrogen is economically feasible and scalable.
> Alternative smelting reduction process: Some newer commercialized smelting reduction processes can offer better emission control compared with integrated plants, but their economic viability depends on overall power consumption and use of export gases.
Producers don’t currently receive a price premium for lower carbon steel, but tighter procurement rules could further boost demand for it. Companies must take advantage of today’s market environment and stronger balance sheets to invest in initiatives that will position the company as a low-cost producer in the future. Making this shift includes realizing the potential of new technologies and achieving economies of scale, while improving sustainability across the steel value chain. While this will require substantial up-front capital, aligning investments with cyclical market conditions can help to fund the high cost of capital, providing long-term benefits of more sustainable operations and improved ESG performance.
Global emissions may be high, but we can’t let that paint a negative picture. Steel is one of the world’s most sustainable materials – permanent, forever reusable and the most recycled substance on the planet. Building a more sustainable production process is a long-term investment that will yield enormous environmental benefits over the full life cycle of green steel.
ALEX MORRISON is a partner and Strategy and Transactions central market leader at EY Canada, based in Toronto. For more insights visit www.ey.com/en_ca/mining-metals
Comments