Epiroc introduces mechanical miners
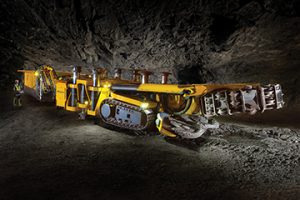
The 22H model of the Mobile Miner, which is currently being tested at Anglo American’s Twickenham mine.
It’s no wonder Epiroc is fielding calls from miners around the world about the company’s new Mobile Miners, officially launched last July.
The continuous mining machines deliver something the industry has long been asking for – a mechanical miner that’s capable of cutting through hard rock, streamlining the stop-and-go underground mining process.
The machines have the potential to reduce drill and blast in most underground mines and completely replace it in mines with small orebodies.
The technology is not entirely new, but represents a twist on well-established tunnelling technology, says Mikael Ramstrom, Epiroc’s director, global strategic projects and alliances.
“We use the technology that is commonly used in civil engineering for big tunnelling projects, but what is really unique here is to use this technology in underground mining – this is something that we haven’t seen before in this format or configuration,” Ramstrom says.
The mobile miner is an upgraded and redesigned version of equipment that Epiroc was selling in the ‘80s and ‘90s.
“For Epiroc, this has been something that’s been in our portfolio for a very long time but we have modernized it over the past six, seven years in cooperation with customers.”
The original version of the mobile miner struggled with performance and had a high cost of consumables as the cutting head wore down quickly. The modernized machine uses steel disc cutters to introduce stress to the rock as it rolls over the surface, causing the rock to split and fall from the face.
“The machine touches the rock, but not by dragging something over the surface of rock” as continuous miners used in coal mining do, Ramstrom says. “In our case, we are rolling something, and that can take a lot harder type of rock than if you try to rip it down the rock.
Ramstrom says company has succeeded in eliminating performance issues encountered with the older version of its continuous mining machine, but as a new product, it doesn’t yet have enough operation time to prove that costs will be lower.
“We need to run a little bit more time for the hard facts on that, but on the performance, we have achieved that, absolutely.”
Advance rates
In addition to being safer than drill and blast, the Mobile Miner is also faster.
“We are around twelve metres per day in advance rates,” Ramstrom says. “That’s a completed tunnel with ground support, etc. If we benchmark this to a typical underground mine that is doing drill and blast, you typically find that the advance rates are at four, five metres per day. So we are at least twice as fast compared to drill and blast.”
While harder rock (from 200 to 220 Megapascal and upwards) will slow the performance of the machine, Epiroc hasn’t encountered rock that is too hard to be cut by the mobile miner.
As a selective mining method, the mobile miner also reduces dilution.
Models
The 22H model of the mobile miner is being tested at Anglo American’s Twickenham mine in South Africa since 2016.
The original 55V model, which was built for Rio Tinto, was sold by the miner but is now in use at a nuclear waste storage testing facility in Sweden. And Hecla Mining just ordered the first 40V model for its Lucky Friday mine in Idaho in November.
All models are fully electric and can be manually or remotely operated and consist of a rear power unit and a front miner, which includes the steel disc cutting head. The front frame attaches to the excavation to provide stability while the cutting head works.
Each model has a different tunnel profile, turning radius, and other features.
The 40V produces a 4- by 4-metre tunnel; the 55V produces a 5.5- by 5.5-metre tunnel; and the 22H low profile mining produces a 2.3- by 5.5-metre tunnel.
Because Epiroc is starting a new generation of machines, Ramstrom says the company has the flexibility to add to the product line based on customer need.
“We hope that customers will be attracted by the ones that we have made so far,” Ramstrom says. “If there happen to be customers that want something different than what we have, then we will add to our portfolio and do a new project together with customers.”
Lucky Friday
And as mines go deeper, and encounter more issues with rock stress and stability, heat and diesel particulates, there are increasing concerns about safety, productivity and costs for ventilation and cooling.
Those are all factors for Hecla Mining at its Lucky Friday silver-lead-zinc mine, which has been in operation for 75 years.
In 2017, the company completed a new internal shaft to 2.9 km depth to reach the high-grade 30 Vein.
Hecla and Eprioc began working on a continuous miner to meet conditions at Lucky Friday in 2015.
“At Lucky Friday, the orebody’s about two to three metres wide and that means that you can actually cut the whole orebody with this technology,” said Ramstrom.
“They will replace the drill and blast completely and go for mechanical cutting both in ore production and mine development.”
Hecla’s first mobile miner is in the manufacturing and testing phase at Epiroc’s facilities in Sweden. Before it’s shipped to site for a field trial at Lucky Friday in early 2020, it will undergo a test trial at an Epiroc test mine.
“Next year, they will take delivery of the first machine and then they’ll make the decision on the next and the next.”
In the meantime, Epiroc has been busy arranging visits to see the Mobile Miners in action in South Africa and in Sweden.
“It is a big step to take and also a large investment,” Ramstrom says. “I would say that after seeing what we did in these places it’s a lot easier for these potential new customers to make the decision to go forward.”
Comments