Electrifying from the ground up
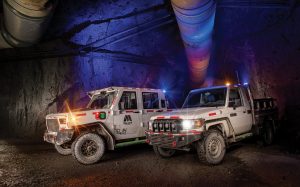
Miller Technology’s newest offering, the Relay electric vehicle (left) Credit: Miller
With the growing focus on reducing operating costs and curtailing greenhouse gas emissions, electrification of equipment for underground mines is a field that mine operators are keen to venture into. While the larger suppliers have taken the lead in tackling this challenge with bulk material handling equipment, North Bay, Ont.-based Miller Technology has taken on this task starting with personnel transport.
“Mine sites are actively planning and developing the adoption of this technology and, with an investment like that, the rate of payback is quite good for the end user,” Hugh McDermid, the company’s head of product research and business development, said in an interview with the Canadian Mining Journal.
For Miller, the focus throughout its development of electric vehicles has been on interoperability with resulting cost savings expected from simpler designs and easier operations.
The Ionic Drive: an interchangeable kit
Miller Technology was established in 1979 and started out producing its own proprietary gear for personnel transport underground. That same year, it built its first Miller Minecart, an underground personnel carrier. Since that time, Miller has established a global customer base and now has 50 employees at its manufacturing plant and head office in North Bay. Miller has also been an authorized dealer of the Toyota Landcruiser range, a mainstay at many underground mines, since 1989.
In addition to collaborating with a supplier to develop an electric conversion kit for this vehicle, Miller has developed the Relay – its first foray into battery powered equipment. The Relay is an electric personnel support vehicle that contains the company’s Ionic Drive kit, an adaptable, scalable battery electric drive system enabling it to operate without a diesel engine.
“The Relay is representative of a vehicle we’d typically sell to customers, that same (Ionic Drive) kit is adaptable and scalable to any number of pieces of gear underground,” McDermid says. “We’re working with existing OEMs (original equipment manufacturers) of diesel equipment to lend our knowledge in the electrification field to them.”
Having completed the Relay, Miller has also recently started to offer an electric grader. McDermid notes that the grader is being developed as part of a joint venture with Miller retrofitting the machine with the Ionic Drive system. (Miller hasn’t disclosed the JV partner yet.) As the company is aiming to maintain commonality of parts across its offering, while the grader is three times the weight of a personnel carrier, it features roughly 85% of the same parts in its drive system as the Relay. McDermid adds that Miller develops their vehicle programming in-house to be able to directly investigate any issues with its equipment and minimize downtime for end-users.
A standardized charging system
In designing a charger for its Ionic Drive, Miller developed a system that is compatible with a standardized, CCS type 2-compliant (combined charging system) charger, eliminating the need to purchase separate chargers for each electric vehicle model. According to McDermid, adopting a standardized charging system means a reduction in additional costs to mine sites. It also allows the company to maintain its focus on vehicle creation.
“We have adopted more of an automotive style of thinking in the sense that we want to focus more on vehicle design and development and any vehicle should be able to pull up to any charger and charge,” McDermid says. “We are one of the first in the market to adopt and commercialize this CCS type 2 charge standard for underground mining.”
Simplifying maintenance with printing
In order to maintain its technological edge, Miller has invested in a laser sintering wire printer for harness manufacturing that will allow the company to transition from a color-coded to an alphanumeric labelling in the physical system that relays information throughout a vehicle. McDermid says that the conversion to letters and numbers in labelling will simplify diagnostics for the end-users as they will be able to identify different aspects of each wire without needing to reference a colour code chart.
“Being a smaller manufacturer in kind of a niche market, it is fairly unique in our space to be offering that type of diagnostic option,” he adds.
Moving towards deployment underground
At this point, Miller Technology is sending out the Relay units to customers on a trial basis with an official launch of the vehicle, as well as the electric grader and Toyota Landcruiser, planned for the September MINExpo in Las Vegas. McDermid estimates a three- to nine-month lead time between order placement for an electric unit and its delivery with units currently in stock.
Comments