Digging deeper to achieve net-zero in the mining industry
In the past, accumulations of waste and contaminated water have been unmistakable indicators of precious metal extraction, often with little consideration for the Earth. However, a shift is underway. Consumers are increasingly preferring products made with sustainable materials, and producers are adapting accordingly.
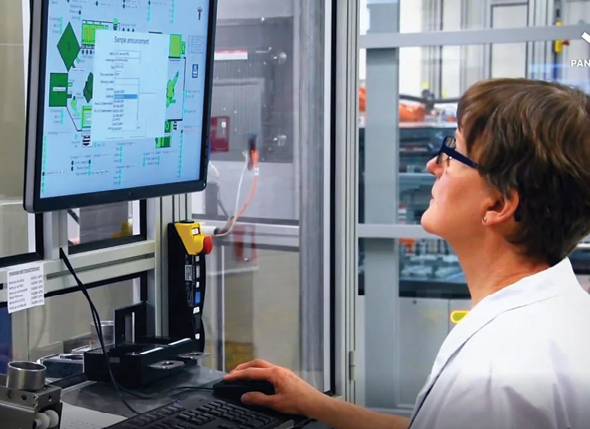
As the energy transition ramps up, there is an increasing demand for more, greener metal. In fact, to open a new mine today, environmental impact is already a non-negotiable consideration. The question is “What exactly is net-zero, and can we achieve it?”
Benefits across the mining process
To make an impact, there are three main areas of the mining process we can target: what we are mining for, how we mine, and what comes after operations finish.
Net-zero mining means no environmental impact – in the air, water, or on land. While it is a challenge, there are already many tools that can help. Technological innovations, such as automation, real-time environmental monitoring, ore sorting, and optimized furnace performance, can significantly reduce carbon footprint across the mining value chain. When applied systematically across all three areas, they create great value like savings in energy, resources, and costs.
Extracting sustainable mining methods
Combination mining is a radical shift that could make a massive difference in the industry. By extracting every element that could be useful from the mined rock instead of only one, less waste is generated, profits are scaled more easily, and the industry is supported with valuable extra resources, such as rare earth elements. This approach relies on great elemental analysis to characterize exactly what is in the rock – which is very achievable today with technology like pulsed fast thermal neutron activation (PFTNA) analyzers.
Processing, or how we mine, is the best target for producers looking to go green. If ores are sorted in the mine or at the stockpile, they can be put into the right place the first time to avoid the heavy and energy-intensive work of moving them around later. Energy spent on crushing and grinding waste rock can also be cut out because only ore-bearing material will make it to the mill.
The benefits of ore sorting and analysis keep compounding further along the chain. Metal yield can be maximized while minimizing wasted material and energy if it is known exactly what is entering the furnace or smelter. Receiving this data in real-time also prevents potential tonnes of wasted material due to issues and downtime.
Wastewater: Taking the waste out
Online analysis could easily reduce huge piles of waste, but less visible wastewater is also critical for mining’s environmental impact. The water used for processing can be recycled, but it takes precise monitoring to pick up potentially toxic elements and remove them safely. Luckily, instruments like the Epsilon Xflow make this kind of technology more accessible than ever.
Aim high!
There is a lot of support available, so mining companies should aim high and not be discouraged by how big the task seems. Technology is filling in the gaps, but there are also a lot of people working on helping the mining industry over the hurdles to net-zero. It is our responsibility to help the mining industry become as sustainable as possible.
Dr. Uwe König, PhD, has over 17 years of experience working with rocks, ores, and minerals, and he is focusing also on new real-time, digital, and automated solutions. In 2005, Dr. König joined Malvern Panalytical from the Martin-Luther University where he received his Ph.D. in mineralogy and geology. He has particular interest and expertise in X-ray diffraction (XRD) and the Rietveld method.
Comments