Demolition robots in underground mining: Q&A
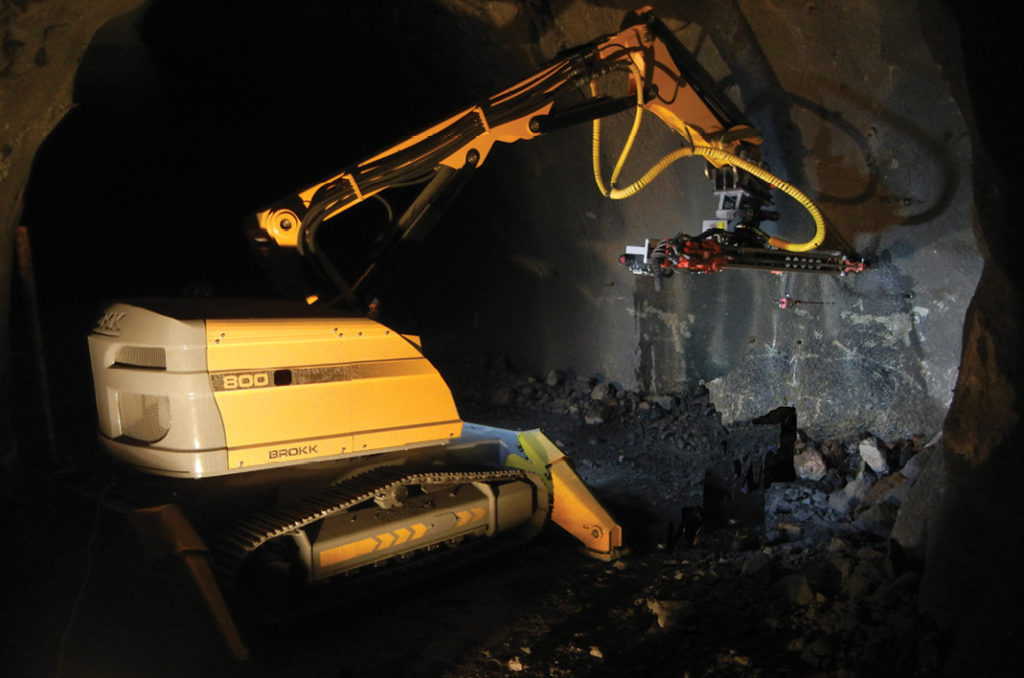
Demolition robots excel at underground mining due to compact, emission-free power, and remote-operation. Designed for demanding demolition applications, these machines easily stand up to the heat and pressure of ultra-deep mining.
Why are demolition robots used in mining?
Demolition robots are used for a variety of tasks, including scaling, drilling, blasting, bolting, breaking, shaft maintenance, and stope retrievals. After a rock fall, for example, a demolition robot can be used to retrieve equipment like a loader. They tend to travel the uneven ground more quickly than traditional retrieval equipment, and they can break up oversize and other obstacles to make extraction easier.
There are also models that are set on a pedestal rather than tracks. These stationary breaker boom systems are used for primary breaking tasks that feed mobile crushers, jaw crushers, gyratory crushers, and grizzlies. The power source and arm are integrated for a compact breaking solution that has just a single power cable.
What are the main features of a demolition robot?
Demolition robots offer exceptional power-to-weight ratios – often on par with machines three times their size – and significantly outclass even the most advanced jackleg drills. An advanced three-part arm provides unrivaled range of motion for drilling, scaling, breaking, and bolting in any direction. The use of hydraulics also eliminates the need for supplying compressed air, which in turn, minimizes the utility requirement at the face, while electric running guarantees zero-emission operation.
What is SmartConcept technology?
SmartConcept is a set of technological features, developed by Brokk, that offer improvements in power management, reliability, maintainability, and ergonomics. The SmartConcept technology is split into three parts: SmartPower, SmartDesign, and SmartRemote.
How do SmartPower and SmartDesign technologies apply in the case of demolition robots?
The revolutionary SmartPower system was designed to withstand extremely tough day-to-day demolition forces. It helps the operator start the robot on a poor power supply while, at the same time, protecting it from harmful faulty power. The system senses when the power supply is poor or faulty and compensates as much as possible to protect internal components. The technology has unparalleled reliability.
SmartDesign extends machine life and provides unprecedented ease of maintenance. With 70% fewer cables and the addition of hardened exterior components, Brokk robots are better equipped to withstand the rigors of machine vibrations and heat generated during operation. The line features several elements to ease maintenance, including strategic, easy-to-access grease points and hydraulic hoses; LED headlights with built-in protections; and steel machine covers. Through the technology, operators not only get 360° rotation abilities, but they can operate “over the back,” which offers heightened flexibility in confined spaces.
What are the main reasons to choose underground demolition robot technology in the mining industry?
Everyone is aware of the dangers of underground mining, so safety is a major reason to choose a robot. With remote-operation, workers can strategically position themselves to avoid the most dangerous situations. We know that 80% of underground mining accidents and fatalities occur at the face, so allowing workers to perform drilling, blasting, bolting, and breaking remotely can make a huge difference.

Versatility and efficiency are other reasons. With the right attachment, operators can move from scaling to drilling for bolting and then drilling for blasting with one tool change – that includes cleaning the lifters with a spade tool in the hammer. These machines can also handle much larger attachments than similar sized equipment, allowing mines to bring powerful tools to new applications without increasing tunnel size. It even opens the possibility of 100% remote drilling and bolting since there are several compact demolition robots with ample power to operate carousel attachments. While the operator stands a safe distance away, the robot can drill, load a rock bolt, then torque it without any wasted movement for fast, efficient, safe bolting of the back.
Are the demolition robots battery-powered?
Currently, demolition robots are offered in electric and diesel models. The first remote-controlled demolition machine, introduced in 1976, was electric, and the technology has continued to evolve ever since. The electric models feature zero emissions, which means they are ideal for underground mining. The SmartPower design ensures that faulty electricity or power surges will not damage the machine while preserving unparalleled power consistency. Brokk (the demolition robot manufacturer) continues to monitor the development of battery-powered machines as technology continues to advance. It is conceivable that battery-powered models will be available in the future. CMJ
Comments