Decarbonizing mining operations
Is the “electrification of everything” the best solution?
The latest Intergovernmental Panel on Climate Change (IPCC) report (2021) cannot make it any clearer: mitigating the adverse effects of climate change relies on our unrelenting and unified global efforts to accelerate the lowering of greenhouse gas (GHG) emissions caused by human activity. In response, many mining companies across the globe have stepped up their efforts in recent years to commit to significant reductions in their GHG emissions. Most corporate plans ultimately aim for a net-zero carbon footprint by 2050 with many also defining interim targets for 2030. While setting ambitious goals, corporate plans must translate into real-world actions. How will the global mining sector respond to this challenge and make these commitments a reality in the coming decades?
A multi-faceted strategic approach is essential to lowering emissions, mitigating climate change, managing the associated business risks, and saving money. Yes, you can reduce cost and reduce GHG emissions within the same plan!
Cutting costs and emissions also requires ongoing monitoring and fine-tuning to factor in changing market forces. In this article, we look at a few ways of achieving significant GHG emissions reductions for mining operations, working towards a net-zero goal, while bearing in mind there is no single “silver bullet” solution to mitigating adverse climate change.
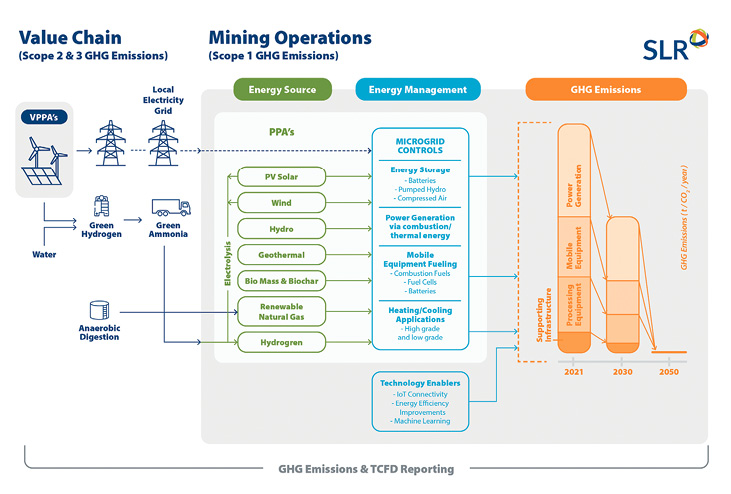
Using less energy
Assessing ways to use less energy is a fundamental component of a holistic GHG mitigation strategy. We see that embracing a “lean” culture of continuous improvement through the elimination of energy waste is an essential strategic and operational planning component. Here are a few questions to ask:
> Energy and/or process audits lead to energy efficiency improvements. When was the last time a detailed audit was done that considers “energy flow” and have our mining production processes been optimized to the point of leveraging the best of the current energy efficient technologies available?
> Capture and re-use waste heat. Where are we letting heat energy go to waste in our processes, and how can we capture and utilize in another process area not thought of before?
> Adopting next-level plant automation. This means we need to embrace machine learning and advanced IoT concepts. Are we taking advantage of the game-changing recent developments?
While a focus on using less energy through efficiency improvements will move the needle in the right direction, it cannot be the only solution to achieving net-zero. Once we have exhausted all the possible efficiency improvements, the use of some energy is still fundamental to doing business. Therefore, other carbon neutral energy solutions are needed to help formulate the overall clean energy mix for mining operations.
Electrification
The electrification of everything within all mining operations and processes is not a practical option. In many cases the energy efficiency losses and the costs of overcoming the process engineering constraints, especially in heating applications, outweigh the benefits. This means it is not the “silver bullet” solution, but it does have a big place in building out the pathway to full decarbonization – by virtue of the significant amount of electricity mines do need to sustain their operations. The GHG emissions contribution from power generation alone can represent more than 75% of the total emissions of a mining operation today. Therefore, looking at where your mine’s electricity comes from is critical to achieving net-zero. It is often the single largest contributing factor.
Renewable energy power generation
Where does your electricity come from and how clean is it?
While remote mining operations are reliant on sourcing their own electricity, many mines closer to populated areas are connected to the electricity grid, which means that electricity comes with a built-in GHG emissions intensity (i.e., your mine’s Scope 2 emissions). If you were to fully electrify everything in your mining operation, it does not mean you will also achieve net-zero. Assessing the strategic plans of your local electricity operator is needed in these situations. Upon close inspection of the strategic plans for some electricity operating regions, the GHG emissions intensity is projected to increase, not decrease in the coming decade. In Ontario for example, the system operator’s current plan includes a tripling of GHG emissions factor for grid-connected power generation due to the retirement of nuclear units and substitution with natural gas.
Utilize the renewable energy resources available on your doorstep
Mining operations not connected to the electricity grid (i.e., off-grid or “islanded” systems) represent the greatest decarbonization challenge, because the traditional use of diesel or natural gas power generation is no longer an acceptable path forward. Lower carbon solutions are needed to achieve decarbonization goals. Water, solar, wind, bioenergy, geothermal, and tidal are all renewable energy options that can and should be considered for integration within a mining operation today. There is not one single alternative that will work in all locations, as the variable characteristics of some renewable energy sources need to be carefully evaluated against the steady state electricity demand of typical mining operations. The question is: Have all the renewable energy resource options been assessed for their feasibility within your mining lease and its surrounding areas?
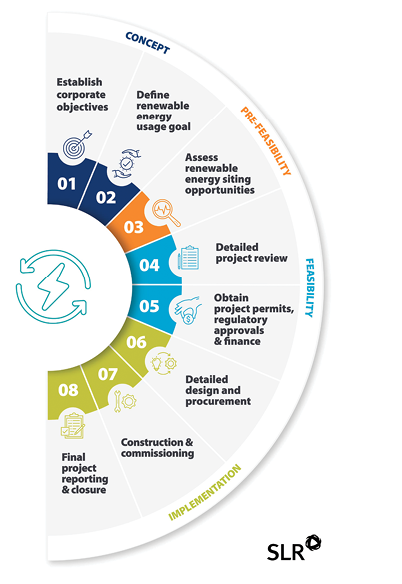
The other significant incentive for considering the renewable energy options is cost. On a levelized cost of energy (LCOE) basis, onshore wind and solar installations are more competitive than the cheapest fossil fuel-fired options. Over the past 10 years, the global cost of photovoltaic (PV) solar has fallen 85%; the cost of onshore wind has fallen 56%. Couple this with the projected capital cost reduction of ~50% for battery storage (to level out the supply-demand disparity) in 2030, compared to 2019 rates, and the economics of a hybrid microgrid system start to become very attractive. These are game-changing cost reductions.
Green (renewable) hydrogen – for those hard-to-decarbonize sources
Green hydrogen – the production of hydrogen from renewable energy – represents the single most promising development for the hard-to-decarbonize areas of our mining operations. We have the necessary momentum now to make this energy solution a reality, rather than it being a “pie-in-the-sky” idea. There are many advantages of integrating hydrogen into a mining operation:
> Mature technologies are available to produce it from electricity.
> It can act as a renewable energy storage resource, thereby enabling steady-state baseload power.
> It can be used to power mobile equipment (either combustion firing or hydrogen-electric fuel cell).
> It can be effectively stored and transported.
> It may be blended with natural gas in various concentrations to create a staged energy transition pathway away from 100% natural gas.
> It can be used for both heat (e.g., HVAC, boilers, kilns, etc.) and base load power applications – both reciprocating engines (e.g., GE Jenbacher JGC series) and gas turbines (e.g., Siemens SGT-A65).
We believe that all mining company strategic decarbonization plans should consider the inclusion of green hydrogen as part of the mix of options on the table, as there is too much momentum in the market to ignore it. In some instances, where renewable energy is abundant, like Chile, Australia, and many African countries, it will logically form a greater part of the renewable energy mix. The main challenge in the coming decade will be bringing down the capital costs to widen its market viability. London-based market research company IHS Markit predicts the current costs will fall by 40% in 2025 compared to today’s prices.
Electrification of mobile equipment
Very significant gains have been made in the past few years in the development of electric-powered mining equipment. Advancements in battery and fuel cell technology is driving this change. Underground mining applications have gained strong momentum in recent years, due in part to the added benefits of significantly improved underground air quality and safety for workers.
Electric vehicle (EV) options for all sorts of mining equipment are now available, from an ever-increasing range of manufacturers. Improving power-to-weight ratios, operational range and reducing capital cost are three of the key market drivers creating a zero-emissions equipment supply market that becomes increasingly more competitive.
Carbon capture
In some situations, offsetting the difficult-to-decarbonize sources with a carbon capture solution may be an option, although this needs careful evaluation to verify and validate the GHG emissions reduction claims. One promising area of development is the use of mine tailings for carbon capture via a carbon mineralization process (e.g., magnesium carbonate). However, this will not work everywhere. Different types of tailings have different reactivity potential. Understanding the labile magnesium fraction is important to understand the reactivity potential, and therefore the total carbon sequestration potential.
The big advantage to using tailings is its application across the full mining lifecycle – in closed mines, operating mines, and mines under development. While it is early days for this technology, this is one area to watch closely.
What are the roadblocks?
Boardroom-led ESG goals and objectives linked to decarbonization are fundamental to leading the way for all company management and employees to follow. The very top of an organization must be fully committed for a net-zero plan to be successful. The board might not have all the detailed answers for how to decarbonize their company’s mining operations; there will undoubtedly be roadblocks that are getting in the way, whether they are perceived or quantified. Reviewing the roadblocks through the lens of the “PESTEL” (political, economic, social, technological, environmental, legal) strategic framework can identify opportunities to work around the barriers to implementation.
Your pathway to net-zero
There is no single pathway to net-zero that fits with every mining operation’s extraction, processing, and transportation methods. Every net-zero pathway needs to be defined on a site-by-site basis.
How you can achieve net-zero
Achieving net-zero GHG emissions status in a mining operation is a big, hairy audacious goal. Breaking it down into more manageable chunks is very much needed. It also requires a strategy of not trying to do it alone. Scope 3 emissions mean you need resilient supply chain partners who have net-zero goals of their own. They need to be an integral part of your journey to net-zero.
How to accelerate efforts in the present day will be critical to achieving 2030 decarbonization targets and net-zero goals by 2050. Market demand for base and rare metals is surging because of strong growth in electrification and clean energy technology application. This requires mining operations to increase their production rates, which can create even more GHG emissions in the process if not managed effectively. Achieving your targets and goals will also rely on the further blurring of traditional market sector lines and greater collaboration between mining, power, energy, and industrial companies throughout the supply chain. While this can seem challenging on face value, it also presents many untapped opportunities to explore. Is your company taking advantage of these opportunities and is it on track to achieve net-zero?
Ashley Gibson, PEng, is a technical director and regional renewable energy sector lead for SLR Consulting.
Comments
Dr. Gus Van Weert.
The reduction of iron oxides with green H2 to a steel precursor is burdened by its inherent inefficiency of not monetizing the O2 coproduction. Or simply, half the green electrical energy is immediately wasted by venting electrowon O2. This inefficiency does not occur by using pyrrhotite (FeS) instead of Fe-oxides in a chloride electrolyte. Metallic iron and elemental sulphur (not SO2!) will be the products of this process, which has already been practiced for nearly fifty years for Sudbury nickel by Falconbridge / Glencore..