Custom screen solution improves plant performance at Bell Creek
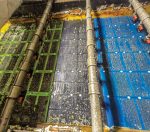
Polydeck’s custom solution (blue and lack panels on right) showing little to no blinding. CREDIT: POLYDECK .
Tahoe Resources’ (now part of Pan American Silver) Bell Creek gold mine and processing facility in Ontario was looking for help. They were experiencing severe blinding on trash circuit screens and needed a solution.
The plant was experiencing an inordinate amount of downtime because of fibrous blasting material residue left on the screens, which the crews had to clean was reducing throughput and increasing energy consumption.
Polydeck screening experts John Griffith and Perry Miller visited the plant several times in order to understand the problem and gather the information they would need to formulate a solution.
Upon investigation they discovered the following operating conditions: Feed: ~75% feed rate of 225 tonnes per hour of solids; Feed Rate: At full flow the total slurry to dewater: – 2862.1 gallons per minute.
Polydeck began testing some panels that were modified to add flexibility and installed them on the carbon safety screen. The modified panels had some success; however, even more flexibility was needed.
Ultimately, Griffith and Miller decided to create a custom solution for Bell Creek.
The new panels would need to meet a wide range of demanding criteria. The would need to be durable enough to remain effective for a six-month life-cycle, and still be flexible enough to impart some secondary motion. The secondary motion would be needed to resist particles of trash from plugging the aperture, while simultaneously preventing the build-up of calcium carbonate on the underside of the panel, which had been observed on virtually every trash and carbon safety screen in use at this site.
Typically, panels in this application would require almost daily cleaning, which is inefficient and expensive. Removing this maintenance requirement or greatly reducing its frequency would be paramount.
Another criteria would be compatibility of fastening — necessary in order to allow the panels to be used on existing machines with other manufacturers’ modular panels.
Above all else, the panel would need to provide adequate dewatering. An ambitious target of 60 GPM per sq. ft. was set.
Griffith and Miller decided to commission two custom Polydex panel designs to ad-dress the issues specific to Bell Creek. Polydex modular polyurethane screen panel solutions have proven to be a good choice for a variety of screening circuits and are especially well suited for wet applications.
Polyurethane offers the most options, not only in terms of screen openings, but also in the integration of performance enhancing features like dams, restricted flow bars, skid bars, and deflectors. Polydex is especially customizable, because options are numerous, and are available for issues like high wear zones, pegging, bed depth creation, drainage rates and high open area. New features and changes can be made quickly, and polyurethane can reduce perceptible noise levels by as much as 50% versus competitive steel options. Another significant benefit for maintenance crews is the ease of use of Polydex products and the availability of fastening options, either in pin fastening or snap fastening. This greatly reduces the time required for installation or removal.
In October of last year, new custom Polydex 1 by 1-ft. slotted panels with pin fastening were installed at Bell Creek in rows one through four, and new Polydex 1 x 1-ft. VR screen panels were installed in rows five and six.
The remaining six rows of the screen contained panels manufactured by competitors of Polydeck in order to draw a comparison in performance. After three months, the results – and the comparison between competing products – were nothing short of astounding.
“The panel’s performance exceeded our best expectations, both in drainage rate and durability. This innovation provides a cost-effective alternative solution to more costly vibrating screen machines and specialty media solutions.” Griffith say The custom-made Polydex slotted and VR screen panels exhibited excellent dewatering results with little water proceeding past the last row of Polydeck panels. They allowed for more efficient rinsing of material and increased throughput by 32%. The drain rate (GPM) increased by more than 2.5 times and the screen capacity more than doubled. Last but not least, the panels eliminated the need for a secondary screen al-together.
While competitor panels still exhibited problematic blinding, the custom Polydex panels demonstrated remarkable results. The panels utilized in this test effectively resisted blinding, which greatly reduced the labour costs associated with cleaning the panels frequently and increased the availability of the unit for its intended purpose: screening.
To say the screens have been very well received is an understatement. As Nick Muskovac, Tahoe Resources Metallurgical Technician explained that eliminating secondary bypass screens helps Bell Creek gold mine operate more efficient on several fronts.
“Increased drainage with Polydeck panels has allowed the bypass of the secondary trash screen. This provides savings in maintenance time, energy consumption, and process water,” Muskovac says. “This is a critical path for our operations.
Polydeck has provided excellent customer service and has worked closely with us to solve our screening issues.”
The successful testing of the Polydex panels at Bell Creek and their reliability for de-watering and resistance to plugging promises to have a far-reaching impact on the gold mining industry.
Polydeck is looking forward to working with other gold producers that are interested in the opportunity to screen their trash product utilizing Polydex with conventional screening machines.
This article was provided by Polydeck. Polydeck is the leading provider of the most dependable synthetic screen media in the aggregate, coal, and mining sectors in North and South America.
Comments