Clean water at what cost?
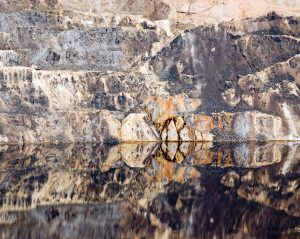
The former Berkeley Pit copper mine, now an environmental clean-up site, in Butte,
Mont. Credit: IStock/Phil Augustavo
While many challenges exist as operators try to return a depleted mine site to nearly pre-development conditions, one aspect that continues to perplex is water quality management. While earthwork, revegetation, structure demolition and removal, and other similar tasks can be defined within a moderate range of reliability and certainty, the job of predicting, defining, and subsequently managing the quality of project site effluent continues to challenge operators. Containment, chemical treatment, filtration, or dilution are often the first line of defense, but to determine the proper approach without the benefit of predictive modelling can lead those charged with estimating anticipated costs at a loss. When evaluators attempt to estimate these costs, they soon realize the requirements can vary wildly from one site to the next and a catch-all approach probably will result in a significant under or overvaluation.
The key to a reliable cost estimate lies in the details. Representative characterization of potential site discharge flow rates (based upon the maximum anticipated, not the average) and quality (pH along with any suspended particulates, dissolved deleterious elements, and a host of other properties) are needed to design the methods of treatment, the magnitude of the required facilities, and extent of the consumables.
Three of the more common, least expensive approaches that operators specify for treatment are land application discharge systems, anoxic limestone drains, and pulsed bed limestone reactors. But as should be apparent, each approach is used for different treatment requirements. Land application discharge methods are specified when there are no deleterious materials in the effluent and the problem is simply a matter of disposing of a fluid with non-toxic (but perhaps still detrimental to active surface flow) characteristics, such as turbidity. Anoxic limestone drains are used to control effluent pH, as are pulsed bed limestone reactors. The latter, however, works to increase the solubility of the limestone to handle highly acidic effluent.
Land application discharge
To estimate the construction costs of a land application discharge system is not so difficult. In essence, an evaluator needs to (based on the flow rate) determine the size and length of the pipeline (trunk line) through which the effluent flows to the discharge area, the sizes and lengths of the series of pipes used to distribute the effluent, the number of pressure regulators and diffusion nozzles or sprinklers, and the horsepower of the primary distribution pump. The calculations needed to establish the sizes and quantities of all these are well understood, so no special algorithms are required. For our work, the only slightly subjective assumption is the flow rate of the effluent through the conduits, which we set at 4 ft. per second.
As we estimate the costs of this approach, we include a mechanic to install the pump, construction workers to install the pipelines and associated dispersal equipment, and labourers to assist the mechanic and the construction workers.
A mechanic is also provided to maintain the pump and to periodically monitor the installation over the specified period of operation. In addition to the time that mechanics spend installing the pump, we also assume that they spend about two hours per day monitoring and maintaining the system.
Anoxic limestone drains
The process of estimating the capital and operating costs for this system is more complex, but still manageable. With this approach, acid mine drainage is channelled through a trench filled with a bed of limestone and then is openly exposed to oxygen. As it flows through this bed, the fluid’s level of alkalinity is transformed to somewhere between 275 and 300 mg CaCO3/litre. The volume of the limestone required to achieve the target alkalinity can be estimated by the following (Hedin & Watzlaf 1994):
M = ((Q × P × T) ÷ V) + ((Q × C × L) ÷ R)
Where:
M = Metric tons of limestone
Q = Volume of flow in terms of cubic metres per day
P = Bulk density of limestone in terms of tons per cubic metre
T = Retention time in terms of days
V = bulk void volume (limestone bed) – roughly 0.412
C = Alkalinity concentration in terms of tons CaCO3 per cubic metre
L = Life of drain in days
R = CaCO3 content of the limestone
A retention period of 15 hours and an initial effluent CaCO3 concentration of 50 mg/L are considered reasonable, and a limestone CaCO3 content of 82% is standard. The trench that must be excavated for this drain should be 1.25 times the volume of the limestone. Excess trench volume, which represents the layer above the emplaced limestone, is filled with a mixture of soils and bentonite.
Costs for this approach all centre around system construction. Once it is commissioned, the system is considered passive, so operating costs are theoretically non-existent.
Pulsed bed limestone
Here, the calculations needed to estimate costs become much more complex. With this approach, effluent is pumped under pressure through a bed of finely crushed limestone in a carbon dioxide rich environment. In one of its more common configurations, the reactor consists of four limestone-bed pressure tanks in which the beds are alternately fluidized during the treatment process. In addition to the limestone tanks, a single carbonator pressure tank serves to facilitate absorption of carbon dioxide into the acidic drainage. Two additional tanks are then used to recharge and rinse limestone as the effluent either enters or exits the system.
Estimators must gauge the volume of each of these tanks, the horsepower of at least one transfer pump, and the capacity of a blower. To estimate the operating costs, evaluators need to provide a mechanic to maintain the pump and the blower, and to periodically monitor the plant. Evaluators must also determine the consumption rates of both the limestone and the carbon dioxide.
How much will all this cost?
While a comparison of the relative expenses associated with these three approaches is by necessity ignorant of much of the detail tied to the chemistry of the individual flows and to the system design parameters, the table above does provide some insight.
Values above are courtesy of Costmine’s Reclamation Cost Estimator. Of note is the relatively flat cost increases of the land application discharge system from one flow rate to the next. This is attributable to the fact that construction cost increases (due to increases in pipe diameters and pump capacities) are minor and that the driving cost factor is the labour required to maintain the system over the five years of operation, which is similar for each capacity. Also of note is the proportionality of the increases in costs of the anoxic limestone drain system. This system is passive, so there are no operating costs included in the above totals. Consequently, the construction cost is the only consideration and is proportional to the size of the system, which is in turn proportional to the anticipated flow rate. The only variable in the overall algorithm is the size (and subsequent productivity) of the excavation machinery.
While the above provides a very cursory glimpse into the costs of some water treatment options and into the task of estimating those costs, please be aware that the design of the treatment system is critical to the success of closure, and both the complexity and the associated costs of these systems can vary greatly. Here, we have examined only three of the simplest, least expensive approaches.
Scott Stebbins, P.E., is president of Aventurine Mine Cost Engineering. He can be reached at aventsherp@aol.com.
Data used in this article is available through Costmine at www.costmine.com. For a free trial of Costmine’s Reclamation Cost Estimator, contact info@costmine.com.
Comments