Cavity filling with foam product
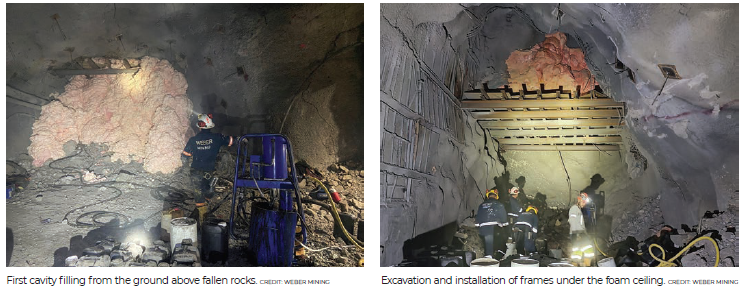
The geological conditions and mine-related impacts can cause rock bursts or large-scale cave-ins, challenging each mine operator. These cavities can lead to production stoppages and hindered extraction. To prevent more severe problems, continue production with the minimum delay, and restore workplace safety, those cavities must be filled as soon as possible.
Phenolic and silicate foam products with different technical characteristics are available for individual solutions in mining and tunneling.
Phenolic foams: Rocsil foam
Phenolic foams are high-expanding, two-component foams designed to rapidly fill large voids and cavities. The benefits of this technology are timesaving and safety increases compared to classic filling. Designed in the 1980s, especially for cavity filling when the roof collapses in the longwall, the technology has been improved by various expansion ratios, safer chemistry, and longer shelf life of the components. There are ten different variants available for each specific requirement.
Rocsil is one of the phenolic products that reduce transportation times to working areas due to reduced quantities of Rocsil required to fill large volumes compared to conventional cementitious options. Other advantages include the following:
> Because of the high expansion rates, complete cavity filling is assured. This allows for the containment of the surrounding strata in exposed cavities, thus containing further self-mining or falls of ground.
> Containment of the excavation is ensured due to the active filling support of the foam.
> Increased work safety.
> No shrinkage.
> Fire resistant.
The foam is pumped into the cavity by a pneumatic pump with a preset mix ratio of the two components: resin and catalyst. A mixing gun merges the components shortly before the product emerges from the pipe and is placed.
The foaming starts immediately, which enables a quick cavity filling with minimum product input. The expansion ratio varies depending on the desired compressive strength of the final product. Cavity-filling foams enable a cost-effective, time-saving, and safe cavity-filling solution.
Case Study
A mine needed to connect two galleries (access A and access B) to improve traffic. This new roadway is critical, as on access A, the mine has underground offices and mechanical shops. Direct access to this area would accommodate the newly developed area in access B.
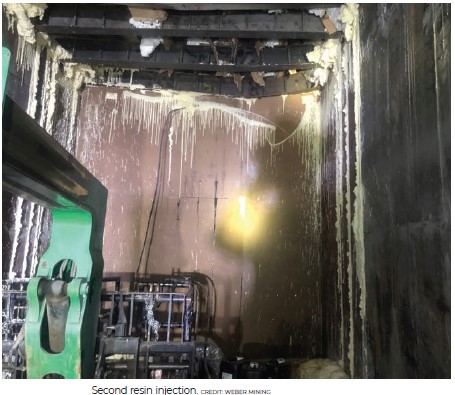
The first collapse
The mine started its gallery development from access A toward access B; however, 30 metres before connecting, they had a rock burst, generating a 600 m3 cavity. Since the rockfall was ongoing, removing the fallen rock from the ground was impossible to facilitate the installation of sets. Therefore, an alternative method had to be considered to stabilize the cavity while minimizing personal exposure, thereby improving operator safety.
Phenolic foam was chosen and injected from afar of the cavity. This technique has been used to profound effect worldwide in hard rock mines and was brought to Mexico in 2017. To ensure nothing was left to chance and guarantee the project’s success, Weber Mining’s standard procedure was employed, with its own hardware and technical team.
Immediately after the beginning of the collapse, the area was evacuated safely and promptly without incident or injury. The team initiated the injection from a safe location, 10 metres from the rock burst, installing a set of four injection tubes with different lengths inside the cavity to guarantee a complete filling. The injection started from the roadway floor, with a first injection lance of four metres. Because of the pump pressure, the injection lance has a four-to-five-metre flush, enabling the technicians to steer the foam where needed. As the filling continues and the foam goes up inside the cavity, the previously installed injection lances are used, with a better reach higher up inside the hole. The pumps are equipped with manometers that indicate any increase in pressure, indicative of voids getting filled. The expansion of the Rocsil foam between the surrounding strata and the containment backing attached to the confined area allows for the pressurization of the cavity filling. This pressurization exerts a resultant force on the surrounding strata and provides an active support function. Load distribution of a foamed product like Rocsil typically allows for a better load transfer under the weight of collapsing rock.
Finally, the 600 m3 cavity was filled in only 8 hours, from a single place of injection, without exposing any of the mining personnel to an unsafe area. From there, the mine had to follow a strict excavation process consisting of excavating one metre of gallery with fallen rocks and foams, installing sets and shotcrete before excavating again. This process allows the mine to recover the gallery quickly without ever being exposed to further rock bursts, as the roof is now composed of foam.
The second collapse
As the roadway recovery on access A was pursued, the mine continued development from access B. Unfortunately, the roof of access B collapsed as well. This time, the collapse was so big that the rock burst reached the cavity previously filled on access A, leading to a completely collapsed area between the two accesses to be connected. Again, the gallery had to be evacuated by the mining personnel, and the team was commissioned for the roadway recovery. At this point, there was no way for the mine operators to provide an indication of the size of the void, except that it was more than twice the first one, the recorded height was 25 metres, and it had propagated to the right. Therefore, because of the voids’ sheer size and difficult access, an iterative process of cavity fills and excavation had to be implemented instead of a one-event cavity filling.
Usually, a cavity can quickly be filled with foam, even with a sole injection tube. This is because the foam sets and expands in two minutes, giving it time to migrate inside the cavity and fill any existing voids as the cavity is getting filled. However, because of the shape and size of this cavity, two sets of injection tubes were placed at various locations. Each injection tube was intentionally placed to ensure the optimum foam distribution inside the cavity.
The first set of tubes was placed at the center of the cavity, close to the top, while the second set was placed on the right side. Once placed, the first tube was connected to the hoses and the mixing gun. The mixing gun was then connected to the pump, and pumping started. This system allowed for a safe and simple transfer from one injection tube to the next.
Foam calculations
Because of the cavity’s size and the ongoing rock fall, it was impossible to calculate the exact volume of foam required to ensure stabilization. Given the availability of local stock, the team first came to the mine with an initial conservative quantity of resins. As it was clear that the cavity was bigger than assumed, more resin was supplied to the mine in less than 12 hours. With a 40 times expansion rate, the required resin quantity is reduced, as is the logistic requirement, easing the completion of the work.
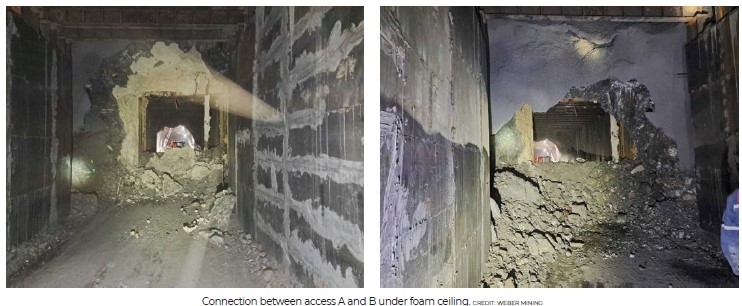
Roadway recovery: First eight sets
Once the first part of the cavity was filled, the excavation process began, following the same method used in access A. The mine excavated through the fallen rocks and foam, placing sets every metre with shotcrete before pursuing. After 8 metres of excavation, the teams continued filling the remaining void using the same strategy. Given the resin consumption, a void volume of 1,500 m3 was estimated at the finish. The first injection lasted 5 hours, while the second had to take place over two shifts for 11 hours.
Initial evidence of the effectiveness of the stabilization came from direct observation and measurements underground by the mine operation teams when the mine started excavating the fallen rock above which the foam was injected and could place sets without difficulty under a stable “foam” roof. Another aspect is the cavity filling secures the new sets in place by absorbing the energy of falling rock in case of further collapse from the top of the cavity. That means even if the cavity is not filled completely, the support of the gallery built by the sets is secured by the above foam canopy.
In conclusion, the two galleries could be connected in approximately two months without incident, accident, or injury of any kind. A foam roof now protects the 30-metre length collapsed area between the two galleries. It provides a safe and long-term roadway for heavy traffic between the mine’s underground offices and its newly developed mining area.
Ultimately, it serves as the most fitting testament and legacy of the efficacy of the foam as an alternative to traditional cavity-
filling products. Success was achieved in the face of technical adversity. Even though the rock fall was ongoing, and the size of the cavity could have blocked the access for months and delayed the mining operation, adherence to the procedure and the hardware successfully used not only worked but also did so better than expected. CMJ
Anthony Ferrenbach is the general manager at Weber Mining Mexico.
Comments