Cat brings partnerships to the fore
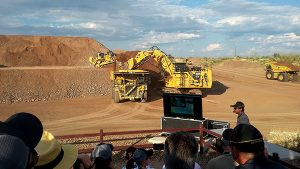
Jag Samaraweera leads a demonstration of Cat’s autonomous haul technology. CREDIT: ALISHA HIYATE
Every year, Caterpillar hosts a group of mining journalists at its Tinaja Hills Demonstration and Learning Center in Tucson, Ariz., to hear about its latest advancements in mining technology and to see first-hand how they work.
This year, however, one of the biggest takeaways from the two-day program in September was not Caterpillar’s new products, but the company’s strategy. Over the past few years, that strategy has shifted from a focus on product offerings to one of partnerships and the “ecosystem” of solution providers that Caterpillar can offer its customers.
“A collaborative approach yields so much value for the customer as opposed to a transactional approach just selling Cat-branded technology,” said Craig Watkins, mining technology sales support, one of more than 10 Cat representatives to present during the program.
One obvious advantage is that Cat can access the expertise of its technology partners in specialized areas and combine that knowledge with its own expertise to bring new technologies to market.
“Partners enhance speed and agility to get things to customers,” said Bill Dears, mining technology commercial manager.
In fact, the world’s largest construction and mining equipment manufacturer even brought in some of its partners – Torc Robotics, Trimble, and Alight to name a few – to demonstrate the depth and advantages of its ecosystem approach.
Torc has expertise in autonomous vehicle technology and Cat has adopted some of Torc’s technology in mining applications. The companies are also working together on a retrofit program that will allow Cat technology to control Komatsu 930E mining trucks. (Command for Hauling, Cat’s autonomous hauling application within its MineStar system, will be available for use with the 930E trucks in the first quarter of 2019.)
Michael Fleming, CEO of Torc said that while self-driving trucks are already a mature technology, further advances and disruptions will happen in the space and a partnership model is needed as no one company has all the skill sets needed to adapt.
Cat’s Watkins added that the partnership model allows Cat to focus on core capabilities so it doesn’t get bogged down in details that Torc or other partners are better able to address.
Network services provider FTP Solution is helping Cat address the communications piece at mine sites, preventing hiccups in communication that can have a big financial impact. Building redundancies into communication systems has been one way to manage that, but Watkins said FTP is now evolving toward identifying breakdowns before they happen.
Trimble, which is a leader in industrial GPS and in hardware development, is working with Cat on making data more consistent at mine sites, where mismatched data often exists in various formats, originating from multiple sources.
Financial forecasting company, meanwhile, Alight can help mining companies gain better insight into their businesses to make better decisions.
Tough market
One could argue Cat had no choice but to change its strategy to deliver more to customers: the mining business hasn’t been booming in recent years.
“In 2014, when the decision was made at Cat to execute this strategy, it was a dark time in mining,” acknowledged Sean McGinnis, mining technology product manager.
For example, after a peak in the sale of large mining trucks (150-400 ton capacity) in 2012, there was a dramatic drop in demand. In 2016, the company’s truck sales were down 95% from the peak numbers achieved in 2012.
The company has adjusted in the last three years by focusing on mine production systems rather than machines and on delivering autonomous solutions to its customers that are brand agnostic to accommodate mixed fleets.
Since big purchases are unlikely for a while as mining companies continue to watch their spending, the retrofit market is still the biggest for autonomy. So interoperability – giving customers the ability to use Cat Command with equipment made by other OEMs – will be key.
First up is the Komatsu 930E truck, but Cat is also working to get Command for Drilling to work with P&H drills (Komatsu).
Autonomous mining
Cat reports a surge in interest in autonomous systems since MineExpo in late 2016, with an increasing recognition among customers of the safety and productivity that autonomous systems offer.
“This year, we thought we’d do a couple of demos, but we’ve done 13,” said Bill Dears.
Cat only started offering autonomous vehicles less than five years ago. The industry is still in the early stages of automation with autonomous trucks only accounting for a couple hundred of the 8-9,000 mining trucks operating around the world.
About 90 of the company’s 793F autonomous trucks are in operation at three different mine sites, said Jag Samaraweera, sales support consultant, mining technology at a live demonstration in Tucson. Before the end of the year, that number will reach 100.
“They’ve moved about 550 million tonnes autonomously in five years’ time and they’ve done that, most proudly, safely,” Samaraweera said.
The trucks have operated alongside manned trucks without a single lost-time accident.
“Being able to run manned and autonomous trucks together in the same site is a key differentiator that we’ve got with MineStar,” Samaraweera said at the demo, as the visitors watched autonomous trucks in operation: waiting their turns to get into position to be loaded, and detecting and avoiding other vehicles or hazards in their paths.
Caterpillar’s MineStar technology platform, which consists of a suite of applications including fleet management, safety, equipment health monitoring and other applications, can be used to optimize an entire mine site, whether it’s manned or unmanned.
At the MineStar Command Centre next to the demonstration area, visitors got a glimpse at how autonomous vehicles work so seamlessly. It starts with a “Builder” at the mine site office, who builds a virtual mine plan that the trucks follow. The builder can customize truck operations according to conditions and act as a trouble shooter – for example, accounting for weather conditions or telling the trucks to avoid a developing pothole in its path. The trucks can also “see” what around them and avoid obstacles with the help of LiDAR (light detecting and ranging) technology and Cat Detect.
In addition, when manned vehicles are working side by side with autonomous vehicles, the operator of the manned vehicle can take control of the autonomous vehicle – telling it when it can enter an area and when to leave and go to the next point.
Cascading benefits
While only the 793F truck is fully autonomous now, soon all large Cat mining trucks will be available with autonomous operation.
Semi-autonomous operation of drills and LHDs has been available from Caterpillar for some time, and an autonomous solution for drills will be available in first quarter 2018. Semi-autonomous operation of dozers is in trials at four mine sites now.
Autonomy itself, however, is not really the goal – consistency is.
Eliminating variability has cascading benefits: For example, in drilling and blasting, when all holes are drilled to the exact same level, you will end up with a level surface to drive on right away, McGinnis noted.
Overall, there’s about a 34% productivity and value improvement possible in drilling and blasting through automation, he said, including savings in capex, the cost of explosives, faster cycles and reduced maintenance, and increased and consistent crusher throughout.
In loading and hauling, the productivity improvement is even greater, up to 40%, through improved throughput, shortened dump times, and increased payload capacity.
Cat is also working on extending the benefits of automation to smaller mines, with the launch of NextGen MineStar in 2018. The platform will allow smaller mines to leverage digital information and intelligence.
Comments