Case study: Waterproofing high-temperature water flows in mining operations
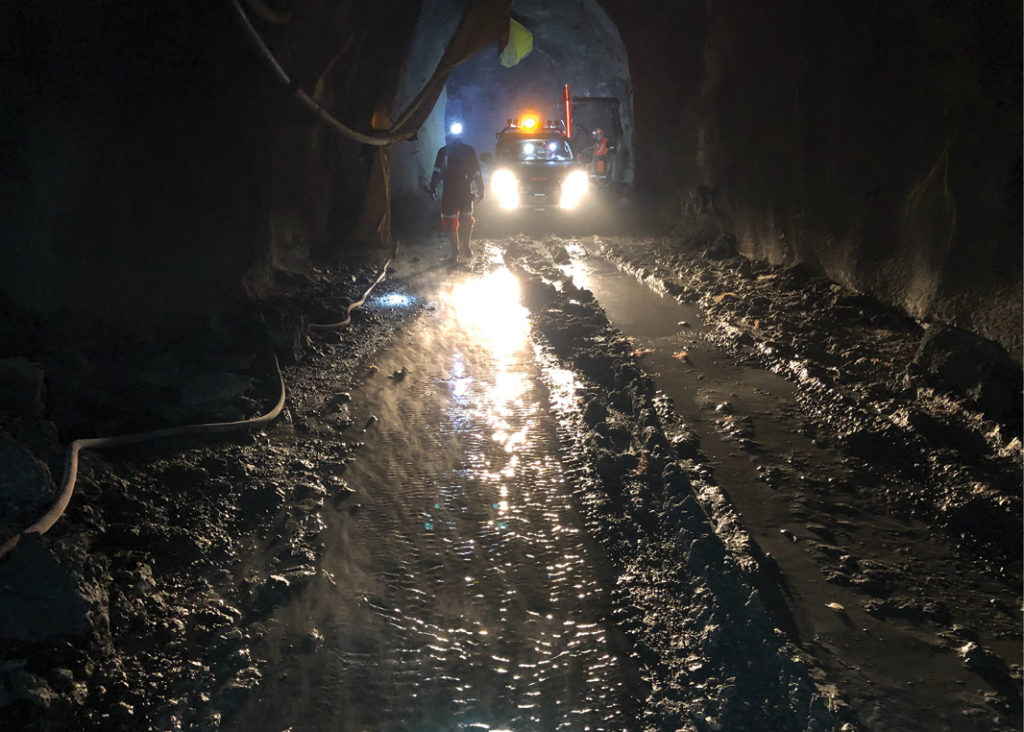
In this study, the mine was in the process of tunnel excavation. Initially, the mining advanced under dry conditions. However, as the excavation cycle continued, water ingress started to appear. With further development, the volume of water inflows increased, and the internal temperature of the tunnel began to rise, reaching around 35°C. This combination of water ingress and elevated temperature levels started to adversely affect the well-being and performance of the mining staff.
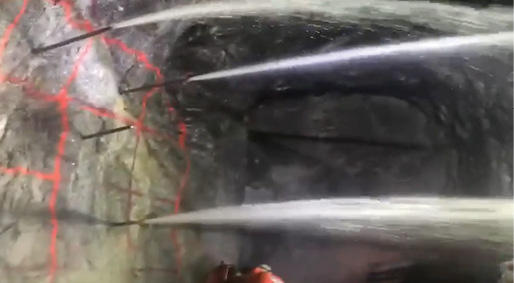
By the time the mine reached its final development phase, the water inflow had intensified to a degree that it was hindering blasting activities.
Traditional methods, which involved controlling the water flow using cement injections, proved ineffective. The persistent water flow, coupled with a significant pressure of 1200 kPa, resulted in the cement being washed away before it could solidify and set within the ground.
Given this challenging situation, the decision was made to turn to a polymeric resin as a potential solution to divert and manage the water inflows and allow continued tunnel development.
In usual scenarios, fast-setting resins with a setting time of 1.25 minutes are the go-to choice. However, because of the excessive water pressure experienced in this mine, a two-phase plan was proposed to achieve effective waterproofing.
Phase 1: Superficial waterproofing
The first phase entailed the use of an ultra-fast setting resin with a curing time of 30 seconds. This resin was injected into drillings that were two-metre deep, mainly focusing on the tunnel’s face. The primary objective of this stage was to establish superficial waterproofing, approximately one metre deep, to manage and curtail the water inflows and set the stage for a subsequent, deeper resin injection.
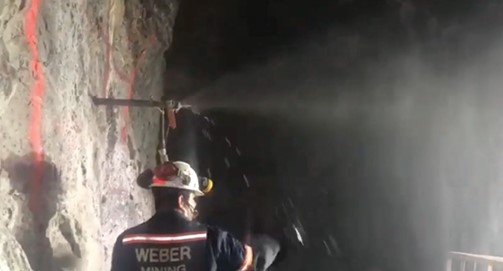
The resin’s innate characteristics played a vital role during this phase. Not containing water in its composition, it does not dissolve when in contact with water. More importantly, when the resin interacts with water, it expands, increasing up to five times its original volume. This is particularly advantageous in situations with high water flow, as the rapid expansion allows the resin to seal cracks swiftly and effectively.
Phase 2: Deeper waterproofing
After achieving initial control over the water flow, the next phase commenced. This involved a more profound application of the resin, focused primarily on the tunnel’s periphery. The main aim was to redirect water away from the central tunnel areas, thus facilitating drier conditions for further development. This approach was also instrumental in helping with ground consolidation during blasting operations.
A planned drilling pattern for injection of the resin was instituted for this phase. Each injection point was two metres apart and extended six metres in depth.
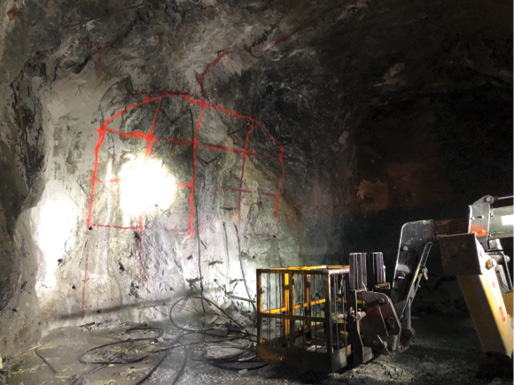
A 1.25-minute setting resin was employed. This resin, once injected, moved into the ground’s fissures, expanded, set, and then carried on its migration to effectively seal the ground across the injected length. The application of the resin showcases the perfect blend of these two aspects of migration and expansion. The resin’s strength is contingent upon its expansion degree, with a compressive strength that varies between 8 MPa and 40 MPa. The robustness of the resin ensures ground consolidation, and concurrently, achieves waterproofing — a pivotal factor in ensuring mine safety and effectiveness.
During the preliminary injection phase, especially in the vicinity of the primary leakage point, there was a notable rise in ground water pressure when obstructing the water flow. Without the right measures, this surge in pressure could have led to ground fractures. But, with the strategic positioning of resin injection along the tunnel’s face, not only was waterproofing accomplished, but it also served as a buffer against potential fractures from increased water pressure. This strategy effectively stopped the emergence of new leaks within the tunnel while sealing the primary ones. With the successful primarily waterproofing, the water influx was significantly reduced, paving the way for the subsequent waterproofing phase. This phase was characterized by a more in-depth application of the resin, enabling the mine to push forward on
a ground that was both dry and consolidated.
Given the mine’s dynamic situation where water influx intensified with every advance, this deeper treatment was critical. It prevented a regression to potentially dangerous situations like flooding and elevated temperatures that could adversely affect the crew’s productivity and safety.
Thanks to the groundwork laid in the initial phase, the second phase of injection proceeded without any hindrance from water pressure flushing the resin. The resin seamlessly migrated into the ground. Occasionally, certain pressure spikes were noticed, signifying the resin’s saturation and the filling of the cracks. Whenever this was observed, the injection process was halted before moving to the subsequent holes.
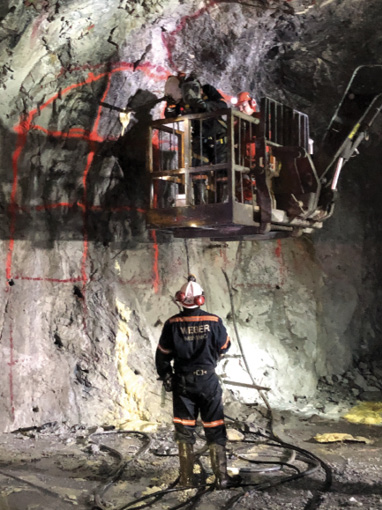
A noteworthy feature of the resin was its rapid setting time, coupled with its expansive nature upon interacting with water. This meant that the amount of resin required was substantially reduced, translating to a solution that was both cost-effective and logistically efficient.
Conclusion
Upon completion of the injection process, the mine progressed its initial five metres on completely dry ground, leaving a waterproofed barrier of one metre. In this case, after drilling holes to check for water presence, two more six-metre advances with resin injection were made past the water-bearing area. Resin injection allowed for safe advancement without the risk of gallery flooding, enabling personnel to work at acceptable temperatures. At the same time, consolidating the periphery ensured no over-excavation, facilitating overall progress.
Anthony Ferrenbach is the general manager at Weber Mining Mexico.
Comments