Building the EV infrastructure backwards
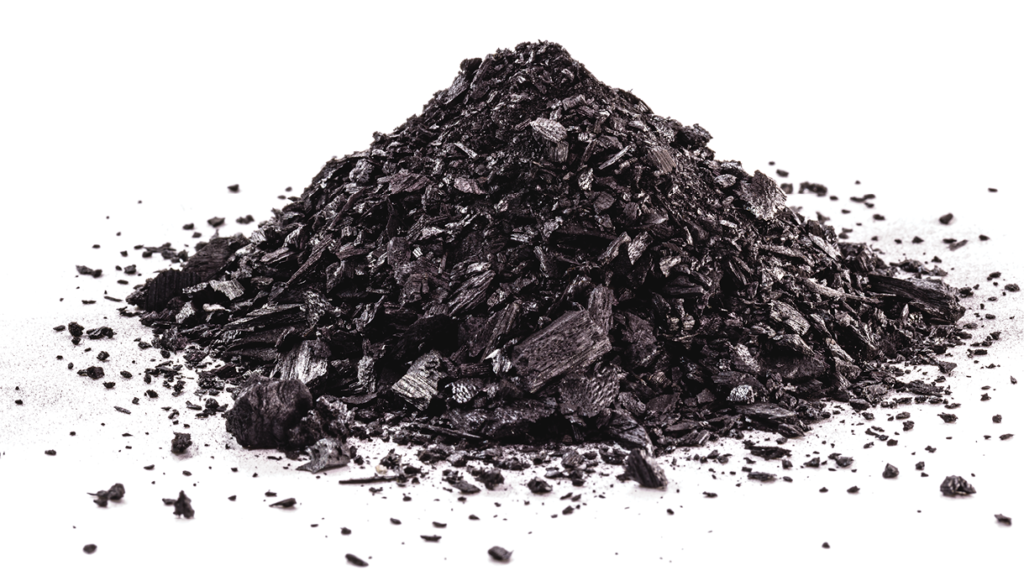
Lithium, cobalt, and nickel dominate the battery scene, as they get a lot of coverage, as cathode material. However, found in every EV battery anode, graphite is a crystalline carbon allotrope that is often forgotten. Producing graphite in the forms needed to build high-performance battery cells is a complex process.
Graphex is a major global producer and distributor of graphite in its various forms, with its principal offices in Hong Kong and regional offices in Shanghai and Royal Oak, Michigan. The company is focused on the development of technologies and products to enhance renewable energy, particularly the production of spherical graphite and graphene, key components in EVs/lithium-ion batteries, as well as in other uses.
Graphex has extensive commercial experience in the deep processing of graphite and producing battery grade purified spherical graphite. It also provides technology for producing coated spherical graphite (CSG) and distributes synthetic graphite. Battery makers use a blend of CSG and synthetic graphite to form Li-ion battery anodes.
John DeMaio (JD) is the president of the graphene division of Graphex Group and the CEO of Graphex Technologies LLC, with over 35 years of experience in executive leadership and operational management in the energy and infrastructure sectors. He is responsible for the expansion of the graphite business into the U.S. and Europe. Recently, I caught up with DeMaio, and he talked to the Canadian Mining Journal about Graphex, battery minerals, supply chains, and more.
CMJ: Can you please talk to us about your background and how you became the CEO?
JD: On a certain level, my background looks very diverse, but one thread that permeates all the way through is energy-focus, sustainability, and I always refer to it as I was involved in the energy transition long before that term was coined. I started my career basically at Procter and Gamble, which is a manufacturing company, but my focus was on onsite sustainability. We worked on optimization programs for energy consumption within the manufacturing environment. I ultimately wound up working on a waste to energy plant that was onsite, where we offset the energy consumption for the plant by installing a wood burning to steam plant.
After that, I got into mechanical contracting, which again was focused on energy conservation, energy retrofits, and waste to energy plants. In the city of Los Angeles, I worked on a waste to energy recapture kind of facility for the water pollution control plant where we took the digester gas, used it to fire combined cycle power generation, and then heat recovery to capture the waste heat and create energy. Then, I worked on one of the early solar energy generation stations, the SEGS one and two in the Mojave Desert.
So, these are early precursors to the modern movement. From there, I worked for a company that is now part of Stantec. Many people do not know that the highest energy consumption for municipalities is for the movement of water: potable water, wastewater, etc., and we focused on optimization programs for that.
Then, I joined Siemens where I led the smart infrastructure group for western U.S. We focused primarily on energy transformations for citywide municipalities, large scale users like universities, and major corporate campuses, where we would take a holistic view of their energy consumption and attack it with a combination of energy reduction measures; onsite generation measures.
So, we got into solar again, waste-to-energy, wind power, other renewables, even fuel cells. It is an all-of-the-above approach to addressing energy conservation and energy transition. Then, I was looking for the next opportunity. The energy transition to this point has been a little bit of an uphill battle to reduce, reuse, replace, and protect. Even though it makes sense from a sustainability standpoint and from an economic standpoint, there has been historic resistance to energy transition initiatives with the electric vehicle and electrification movement more broadly.
So, I was contacted by Graphex with their intention to expand into the North American marketplace, and my first response was, thank you for the outreach, but I have no experience in graphite. And to their credit, they said, “really nobody has, there is not many people with that kind of experience.” What they were looking for is someone who has been in the energy transition space and is familiar with technologies and how to roll out programs, how to navigate environmental, regulatory, and financial kind of environments, and to move not only the company, but the whole electrification initiative forward. All the experiences that I accumulated to this point have bearing on how to move this initiative forward, so I was a perfect fit.
There is a lot of navigation that needs to happen to establish Graphex in North America as part of an ecosystem or an industry efficiently and effectively, and I have been in those kinds of environments.
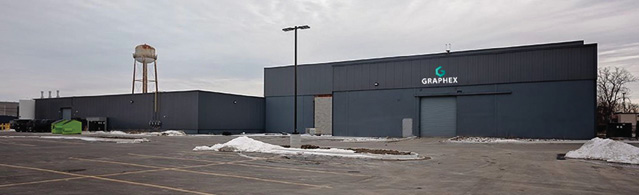
CMJ: Can you talk to us about the history of Graphex?
JD: Graphex has been in the natural graphite refining business for over a decade. It was established in China where the whole lithium-ion battery technology and ecosystem is the most advanced in the world currently. As a result, Graphex started to produce graphite (i.e., refine from the raw material) on a commercial scale in 2013. We had spent a couple of years before that perfecting our methodologies and our technology to get to commercial relevance. We do not do mining. We take the output from the mines and shape it, purify it, and put special coating on it to make it perform in the manner that is required for electric vehicles manufacturing and/or other uses like consumer electronics, power tools, et cetera.
In 2020, the company made the conscious decision to expand outside of Asia and North America and ultimately target Europe and beyond. Currently, we are ranked in the top 10 as far as volume production, as we produce 10,000 metric tonnes of finished product.
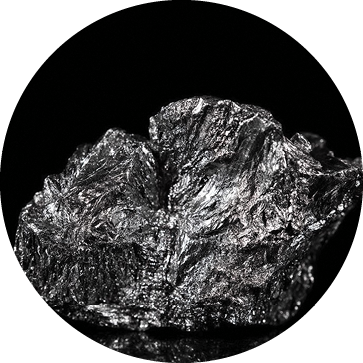
CMJ: What is the role of graphite in batteries? Why is it ideal for that role? And what are the forms and functions of graphite in the anode?
JD: Graphite has been the predominant anode material since lithium-ion batteries were invented, and its properties make it relatively ideal. It is an abundant natural product, but it is inert. It holds the charge very well. It performs its function, which is to store the charge and then to allow that charge to flow for use. There really has been no viable substitute for graphite over the last 50 years. For the foreseeable future, graphite will continue to play a role. The anode is 95% to 99% comprised of graphite. Factors to be considered are particle sizes, coating methodology, and synthetic graphite. So, some battery configurations will include a percentage of synthetic and natural graphite.
Synthetic is similar, but it is almost a completely different animal. So natural graphite, as we know, is almost 100% carbon. Synthetic graphite is produced from petroleum coke, which is a byproduct of oil and gas production methodologies. It is a petroleum-based feedstock that is then processed via an energy intensive process into synthetic graphite, which has a high density, and its swelling characteristics are a bit better than natural graphite. One of the operating limitations of lithium-ion batteries is that charging and discharging can create swelling during that process. So, the more you can limit that swelling, the longer battery life you will have, but it comes at not only a dollar cost, but an ESG footprint.
CMJ: What is the role of graphite in future battery technologies in your opinion? Do you see the emerging technology still using graphite in the anode?
JD: When you think that the overall goal of electrification is to move away from fossil fuels, it does not make intuitive sense to introduce a petroleum-based product as part of that solution. When you look at the current landscape of anode materials, it is about almost 50/50 between natural and synthetic graphite and synthetic, including a small percentage (about 6%) for the additives, silicon oxide, lithium, titanium oxide, et cetera, which may play a larger role moving forward. The forecast moving forward is that natural graphite will occupy a larger and larger percentage. Some of the additives will occupy a larger percentage, albeit still in the single digits. And the element that will get squeezed out a bit is synthetic for the reasons I mentioned, and that is likely the current thinking over the next 15 or 20 years.
CMJ: You have several products ranging from spherical to synthetic graphite and more; which type is planned for the North American facility and why?
JD: We focus on natural graphite. We have the capability to produce synthetic, but as we look at the expansion into North America and the prospect of building out domestic infrastructure, we see a clearer path to quicker productivity on the natural graphite front. The facilities required to refine natural graphite are still significant industrial facilities but not as significant as synthetic graphite facilities. Synthetic graphite facilities look like oil refinery facilities because we are dealing with petrochemical products. As far as Graphex is concerned, and for the foreseeable future, our focus is going to be on natural graphite unless we really have a strong demand and a willing partner to get into synthetic production domestically.
In fact, there is no large commercial market for that right now. Currently, there is no commercial scale graphite refining capability in North America. There are some pilot plants, and there are some other plants that are under construction, but no one with the same experience that we have is currently operating in North America. We feel that we have responsibility and an opportunity to really hit the ground running and to meet this demand that those of us in the industry know is there.
CMJ: How badly was the EV batteries industry affected by the supply chain problems?
JD: There are multiple risks. A globally diverse supply chain has pros and cons. It is better to have a diverse supply chain when you can. If there is a disruption in one stream, then you can make up for it. Where that becomes challenging in the critical mineral supply chain is that not all supply chains are created equal, and there can be multiple ways for those supply chains to be disrupted. For example, geopolitical tensions or a mine shut down because of terrorist activity. Many things can be outside your control. So, as much as you can bring that end-to-end supply chain local.
Other benefits that come with that include job creation and the economic stimulation that happens with that. Ultimately, there are limitations with respect to the raw materials. You can only extract those where they exist in space and time. In case of graphite, there is not a lot of graphite in North America or in the U.S. There is some up in Canada. And as a result, we are aligning ourselves with those resources. We had a recent announcement about our relationship with Northern Graphite, the only producing mine currently in North America, and a recent announcement with the Syrah for their production out of Mozambique. We are also looking for resources in Tanzania, South Star Battery Metals, and Groton in Brazil to diversify our access to the raw material that we need, and as a result, we believe that will provide resiliency to our ability to supply the domestic end user OEMs and battery makers.
Nobody can predict where the next disruption is going to come from. During covid, one of the biggest disruptions was that there were no container ships available, and as a result, shipping costs went up. Recently, here in North America, Graphex Technologies, LLC, a wholly owned subsidiary of Graphex Group Limited, is developing a processing facility in Warren, Michigan, creating a stable domestic supply chain to meet unprecedented national demand for graphite, bringing technology from Asia versus shipping it out to Asia, and bringing jobs to the U.S. instead of shipping jobs out.
CMJ: What do governments, automakers, and battery makers need to do to accelerate the plan to reach net-zero?
JD: As a society, we are trying to replace internal combustion in the case of mobility, thus trying to replace over a hundred years of internal combustion technology and infrastructure completely with electrified mobility. At the same time, we are trying to domesticate all that. So, the paradigm must shift. In the current situation, we are focused on the manufacturing of the vehicles first. Then, the batteries, and now we are focusing on the supply chain. So, when the automakers design these electric vehicles, then they go to the industry to ask to provide the raw materials or the finished materials, there is no industry there to respond. That industry must be created, which is part of what we are doing. So, when you ask what the governments can do, it is also what OEMs can do. What can the whole ecosystem do to support what the industry players, like Graphex, are trying to do? The answer is to build out the infrastructure. For example, there is no capacity right now for graphite refining.
I refer to it as aggressive collaboration. We need to get some federal and provincial government subsidies, funding, and incentive programs. We also need to get some forward commitments from OEMs to companies like Graphex to support us to build these facilities so we can produce the material that is needed. Finally, we do need some regulations from the governments. It is taking about 10 to 15 years and hundreds of millions of dollars to build mining operations. Similarly, we are not going to build a hundred million dollars or $200 million plant without some assurance that our product is going to be accepted and purchased by the end users. We hope to see some outreach by the government to say that they are on board with this. We want electrification, and we want sustainability to bring jobs back.
CMJ: So, is there a need for a more dynamic regulatory system?
JD: Definitely. More dynamic is a good way to put it to avoid using the word “aggressive,” but also more collaborative.
CMJ: VW’s plant in Canada will not start producing batteries until 2027, and Stellantis’ plant is also on the way; how fast do we need to build more EV battery plants in North America?
JD: I think battery plants are coming online in North America at a decent pace. More critically are the plants we need to build to feed them with the materials they need to make the batteries. Otherwise, we are only partly addressing this domestication effort, and we are still going to be, as a society and an industry, dependent on foreign sources of materials. I think the focus really needs to be on these midstream refining capabilities like the ones that we represent, not just for graphite, but for all the other critical minerals as well. We are building it out backwards: auto manufacturing first, then batteries, and then the materials that go into those batteries. So, the next piece of the puzzle is the refining capabilities that we represent.
CMJ: Graphex recently announced the formation of its
U.S. strategic advisory committee; can you please talk to us about it?
JD: We announced the formation of the strategic advisory committee around the same time we announced that we are looking at ways to create an effective standalone U.S. entity for Graphex. It makes sense to do it since we have already established a standalone U.S. presence, called Graphex Technologies, for geopolitical reasons and operational efficiency. The strategic advisory committee is being formed to assist, give us some guidance around the formation of the U.S. entity, and then of course in the implementation of our strategy, our expansion, and diversification strategy going forward in the U.S. For those reasons, we brought on two very qualified members, and we are actively seeking to add two or three more on that advisory committee. And again, it is all part of domesticating the supply chain and creating an efficient ecosystem for Graphex to be a foundational player in this build-out of domestic supply chain. We need to achieve commercial success, and we want to make sure that graphite production stays there.
Comments